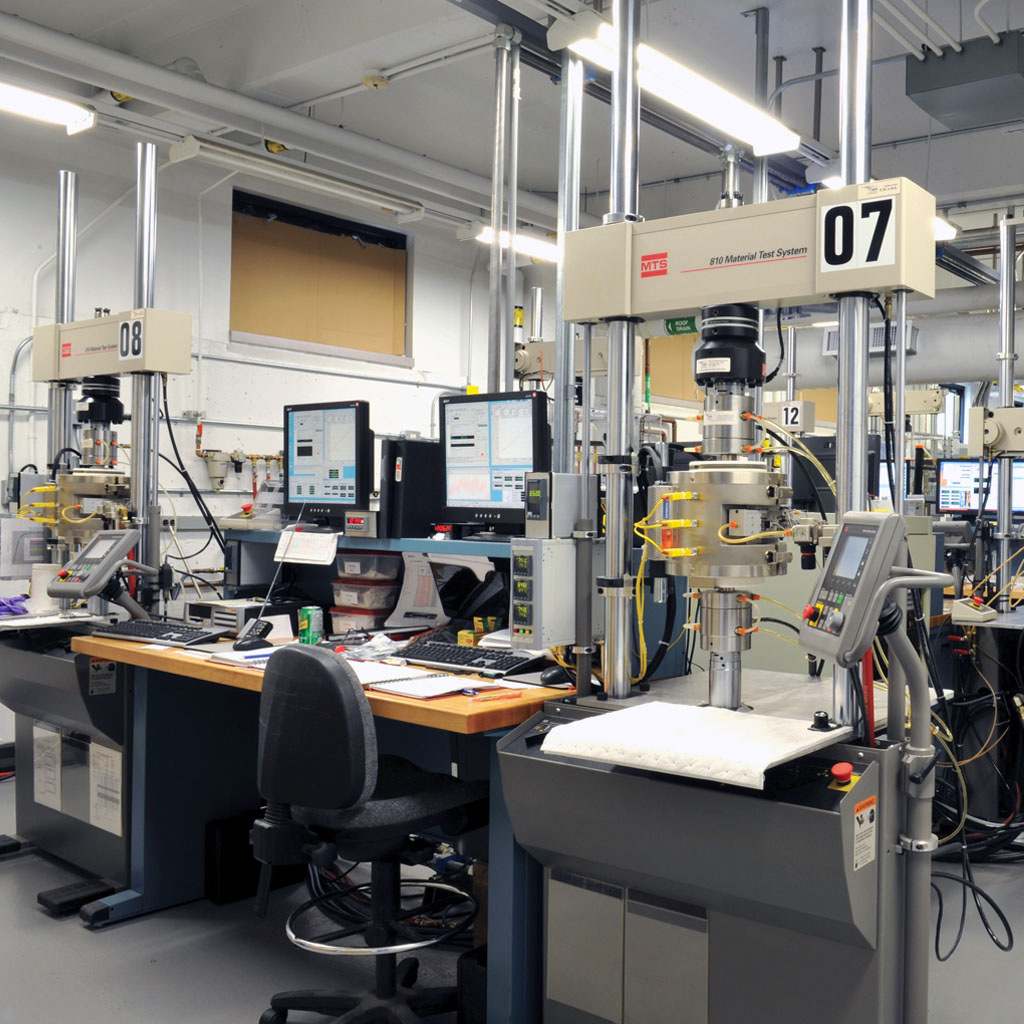
SFIDA DEL CLIENTE
Lo sviluppo di materiali a temperatura elevata, quelli che possono funzionare a temperature estreme per lunghi periodi, sta ponendo le basi per la prossima generazione di motori a reazione e turbine a gas, i quali ridefiniranno le aspettative per l'efficienza nei consumi di carburante. Alcune delle ricerche più avanzate in questo campo si svolgono nel Laboratorio di prestazioni di strutture e materiali, parte dell'Istituto per la ricerca aerospaziale del National Research Council of Canada, situato a Ottawa, in Ontario.
Qui il Gruppo di tecnologia di materiali e componenti, un team di 15 ricercatori, è specializzato in progettazione, sviluppo e test di nuovi materiali per turbine a gas, comprese leghe per temperature elevate e compositi a matrice ceramica. Il gruppo continua con la ricerca interna e collabora anche con produttori di motori commerciali come Pratt & Whitney, Rolls-Royce, General Electric e fornitori di materiali come ATI Allvac e Carpenter Technologies. Per determinare esattamente le prestazioni dei nuovi materiali e la loro durata se esposti a temperature sempre più elevate, occorre eseguire un'ampia gamma di test meccanici di precisione.
"Facciamo di tutto, dai test di tensione, di scorrimento e di tenacità alla frattura fino a test più specializzati, come di fatica da sfregamento, di fatica termomeccanica, di propagazione delle cricche da fatica e del tasso di propagazione delle cricche da scorrimento", ha affermato il dott. Kearsey, direttore del gruppo Struttura delle meccaniche di fatica e frattura a temperatura elevata. "Stiamo sviluppando i materiali, li testiamo e poi sviluppiamo metodi di test standard per caratterizzare questi materiali, che includono la determinazione della geometria del campione e la duplicazione dell'ambiente di servizio del motore in laboratorio".
In questo momento, la più grande sfida del dott. Kearsey è semplice: il calore. Nei decenni precedenti, le temperature per testare acciaio inossidabile, titanio e leghe di alluminio erano relativamente moderate. I test sui materiali più avanzati di oggi richiedono temperature fino al 25% più calde.
"Le temperature sono così elevate che testare i materiali diventa un problema più complesso", ha affermato. "Come si misurano i materiali a 1000 °C quando la pratica standard si basa su apparecchiature classificate per 800 °C? Come si aggiunge la strumentazione adeguata a misurare il tasso di propagazione delle cricche? Non è impossibile, ma è molto complicato. Dobbiamo essere assolutamente certi che le temperature e i carichi siano tracciabili al 100%, perché i nostri risultati vengono utilizzati per realizzare componenti cruciali del motore".
SOLUZIONE MTS
Il Gruppo di tecnologia di materiali e componenti implementa 18 diverse soluzioni MTS per i test a temperatura elevata, una gamma che include tutto dai tradizionali telai di carico MTS 810 ai sistemi di test servoidraulici all'avanguardia MTS Landmark® .
"Il motivo per cui usiamo i telai di carico soltanto di MTS è la stabilità", ha affermato il dott. Kearsey. "Quando abbiamo quattro o cinque telai in esecuzione fianco a fianco, il laboratorio trema. I telai MTS sono molto stabili, non c'è piegatura o torsione che potrebbe disallineare il campione.
A completare l'attrezzatura di test della struttura ci sono due centraline idrauliche MTS, i controlli digitali FlexTest® e il software MultiPurpose TestWare®. Il laboratorio utilizza anche una serie completa di accessori per test MTS, inclusi pinze e dispositivi di fissaggio, estensimetri e sensori di sforzo, forni e unità di riscaldamento a induzione. Tutti elementi che hanno bisogno di essere facili da combinare e integrare nelle configurazioni, spesso complesse, richieste per specifici test a temperatura elevata.
"L'hardware deve funzionare correttamente a diverse temperature e condizioni di test", ha affermato il dott. Kearsey. "Ci piace poter prendere un forno MTS e applicarlo a qualsiasi telaio di carico. L'intercambiabilità è importante, soprattutto per la ripetibilità. Quando dobbiamo fare 100 test su una geometria simile, non vogliamo perdere tempo a reimpostare la calibrazione per ogni singolo test".
VANTAGGI PER IL CLIENTE
Per il dott. Kearsey, niente è più importante dell'affidabilità di hardware e software di test. L'affidabilità è essenziale per l'accuratezza dei risultati, per la produttività del laboratorio e per la soddisfazione dei clienti esterni.
"Acquistiamo l'attrezzatura di MTS perché non si guasta quasi mai", ha affermato. "Non ha bisogno di essere sostituita, è affidabile e tracciabile. In quanto laboratorio di ricerca, la tracciabilità è un requisito fondamentale. Se eseguiamo un allineamento su un sistema, dobbiamo essere sicuri che sia esattamente lo stesso per il test successivo. Non ha importanza se stiamo testando una lega avanzata a cristallo singolo o valutando leghe vecchie di 50 anni per la modellazione di previsione della vita. Con i sistemi di test MTS, possiamo generare i dati necessari per prendere decisioni sicure".
L'affidabilità degli estensimetri è particolarmente cruciale nei test sui materiali a temperatura elevata, specialmente a frequenze fino a 10 Hz o con materiali più rigidi in cui le riflessioni misurate sono minori. Il dott. Kearsey cita anche l'affidabilità del software come un fattore significativo.
"Quando si eseguono test di fatica termomeccanici, ad esempio, i test possono durare tre mesi", ha affermato. "È molto costoso per i nostri clienti. Non si vorrebbe mai dire loro che il software è andato in crash durante il test e che i loro risultati non sono validi. Il software MTS è fondamentale in questo senso perché non ci dà grattacapi del genere. È molto affidabile e molti dei moduli sono pre-programmati per la fatica a basso numero di cicli, per la fatica termomeccanica e per altri tipi di test".
Persino adesso ci si aspetta che il limite maggiore aumenti, mentre il dott. Kearsey lavora per superare le sfide associate ai test a 1000 °C. In effetti sta lavorando con MTS per progettare sistemi di test in grado di funzionare a queste temperature molto più elevate.
"Dato che le leghe più recenti vengono sostituite con compositi a matrice ceramica, dovremo eseguire test fino a 1300 °C o 1400 °C", ha affermato. "Con MTS stiamo già discutendo sul come realizzarlo. Di che dimensione dovrà essere il forno? Quale sarà la zona calda? Di quale estensimetria avremo bisogno? MTS sembra sempre arrivare da noi al momento giusto. Questo tipo di supporto è il motivo per cui continuiamo a tornare da MTS".