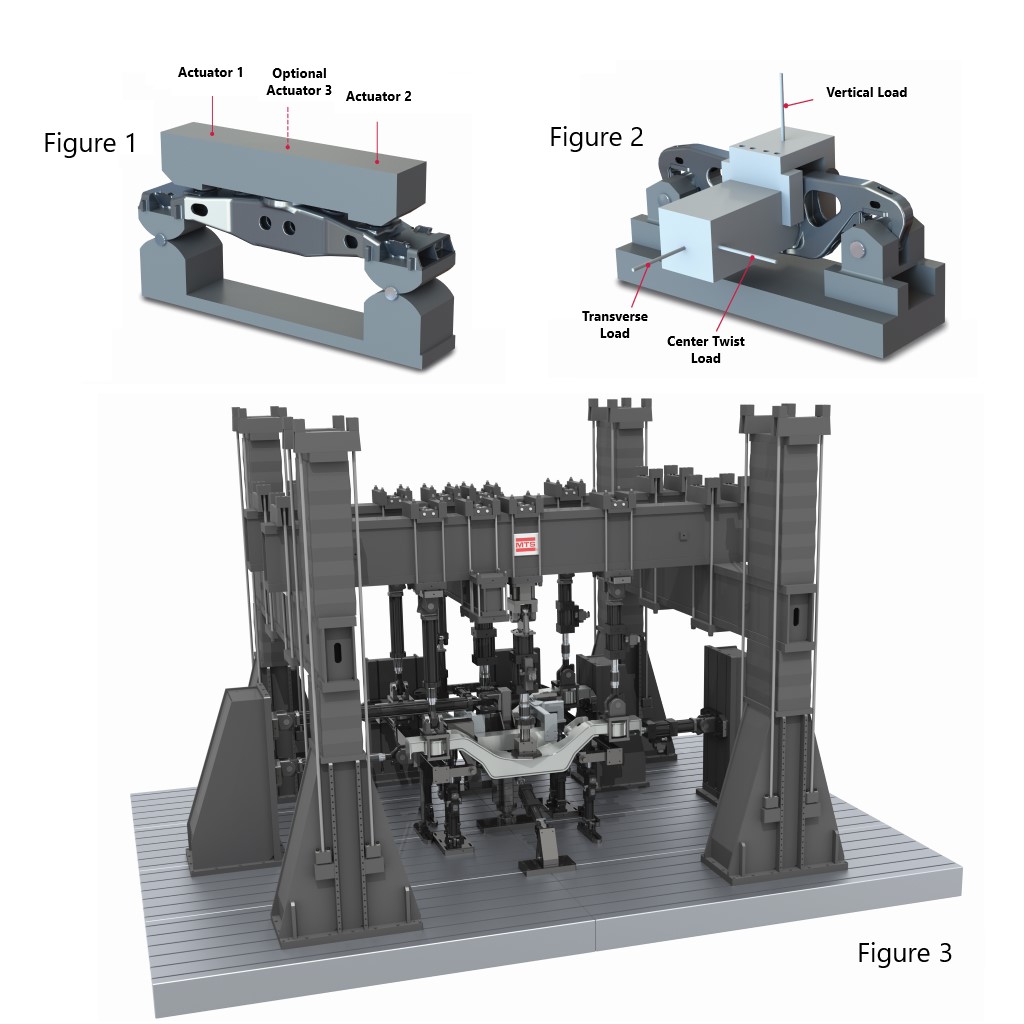
Quando si considerano tutti i componenti e i sottoinsiemi che compongono un sistema di materiale rotabile e l'ambiente circostante, è utile tracciare una linea immaginaria lungo la parte superiore della rotaia. Questa linea divide il sistema in due grandi gruppi. Il primo gruppo, situato sopra la linea, è il "materiale rotabile", rappresentato da un telaio del carrello (o una combinazione di due telai laterali e un sostegno) insieme alla sospensione primaria e secondaria e al vagone. Il secondo gruppo, situato al di sotto della linea, è "la via", rappresentata da binari, elementi di fissaggio, traversine, zavorra e altri componenti. L'interfaccia tra i due gruppi è l'asse con un set di ruote.
Mentre molti degli elementi più semplici di questo sistema possono essere affrontati attraverso il test delle componenti di base, la valutazione di un componente o sottogruppo all'interno del materiale rotabile richiede la considerazione di tre fattori ugualmente importanti: fatica, prestazioni e comfort.
Sebbene la resistenza alla fatica possa non essere ciò che il passeggero apprezza (o addirittura a cui pensa) durante il viaggio, rappresenta comunque una parte molto importante nella progettazione e nel servizio del materiale rotabile. Durante il secolo scorso, l'industria ferroviaria ha compreso e riconosciuto l'importanza dei test di resistenza nella progettazione e produzione di componenti ferroviari. Al fine di garantire una resistenza costante e la sicurezza dei passeggeri, sono stati sviluppati numerosi standard di certificazione.
SODDISFARE GLI STANDARD DI CERTIFICAZIONE
I produttori di componenti e sottosistemi ferroviari devono testare componenti e sottosistemi per soddisfare gli standard di certificazione appropriati, compresi gli standard internazionali come M-202-97 per i sostegni, M-203-05 per i telai laterali e UIC 615 per i carrelli. Questi standard aiutano a definire i test utilizzati per stabilire la resistenza e la durata dei nuovi componenti, e sono essenziali per garantire il funzionamento sicuro e a lungo termine delle linee passeggeri, merci e ferroviarie leggere.
I test di certificazione del carrello, del sostegno e del telaio laterale richiedono ai produttori di condurre test di sicurezza e affidabilità su strutture e componenti del carrello in configurazioni specifiche. Vengono applicati carichi statici e dinamici per valutare prestazioni, forza e resistenza. I risultati dei test includono i livelli di carico di rottura e di snervamento, nonché i dati sulla resistenza.
Sono necessari tre carichi per testare correttamente i sostegni: carico del fondo, rimbalzo centrale e rimbalzo sul bordo (vedi Figura 1). Questi carichi rappresentano le forze a cui è soggetto il sostegno nel suo ambiente di servizio effettivo. Anche per il telaio laterale sono richiesti tre carichi: torsione verticale, trasversale e centrale (vedi Figura 2). Tutti questi vettori di forza separati sono importanti per porre i carichi e la distribuzione delle sollecitazioni corretti sul campione e aiutano a garantire un'adeguata resistenza.
Per testare i sostegni e i telai laterali, un telaio di carico verticale adeguatamente valutato è l'ideale ed è relativamente semplice da fissare. I test di fatica del telaio del carrello, tuttavia, sono più sofisticati e complessi. I test di certificazione del carrello sono definiti da standard internazionali e locali e richiedono un numero maggiore di canali e fissaggi molto più complicati. Le configurazioni di carico per il test si basano sulla configurazione del carrello. Il numero di assi per carrello, il numero di carrelli per vagone ferroviario e il peso combinato del carrello e del vagone sono alcuni dei parametri che determinano i carichi necessari per il test. I test di certificazione richiedono un sistema di carico multicanale ad alta forza e in genere eseguono milioni di cicli. Durante un test, la deformazione e altri segnali vengono raccolti e analizzati per aiutare i progettisti a comprendere le dinamiche di carico dell'ambiente di servizio, identificare le aree di forte stress e migliorare di conseguenza i progetti. Confrontando le risposte alla deformazione con i modelli di analisi degli elementi finiti (FEA), gli ingegneri possono convalidare i modelli, migliorando i progetti futuri.
PROVE DI FATICA AVANZATE
Gli standard di certificazione sono rigorosi e coinvolgono milioni di cicli di carico, ma si concentrano esclusivamente sull'insieme minimo di carichi (verticale, trasversale e deformazione) necessari per verificare resistenza e fattore di sicurezza adeguati. Questi carichi sono notevolmente superiori a quelli previsti durante il normale funzionamento. Le cronologie di carico sono volutamente conservative, per garantire un tasso di guasto il più vicino possibile allo zero in tutte le possibili combinazioni di utilizzo. Questo approccio si è dimostrato adeguato per i comuni carrelli merci ed è stato adottato (in una forma o nell'altra) in tutto il mondo.
Nel moderno materiale rotabile passeggeri, tuttavia, i carrelli, le sospensioni e l'interfaccia della vettura sono molto più complessi rispetto al trasporto merci. I carrelli passeggeri ad alta velocità sono saldature complesse. Elementi come ammortizzatori, collegamenti delle sospensioni e componenti ausiliari (compressori, pinze dei freni) presentano tutti carichi aggiuntivi al carrello. Questi carichi sono spesso costituiti da vettori e posizioni di carico molto diversi da quelli descritti dallo standard di certificazione. Le posizioni, le grandezze, i vettori e le fasi di questi carichi sono importanti da considerare per gli ingegneri di test interessati a replicare l'effettivo ambiente operativo del carrello nel modo più realistico possibile.
La complessità diventa rapidamente un problema in queste circostanze. Sebbene i test di certificazione in genere utilizzino meno di 10 canali (nella maggior parte dei casi, meno di sei), i test di sviluppo più avanzati potrebbero richiedere più di 20 (e in alcuni casi più di 30) canali di controllo. La combinazione di carichi aggiuntivi con i carichi prescritti dagli standard di certificazione rappresenta una grande sfida in termini di fissaggio.
Affrontare questa complessità è essenziale. Negli ultimi 10-15 anni, è cresciuta notevolmente tra gli utenti finali una domanda di materiale rotabile che offra maggiore affidabilità, migliori prestazioni e maggiore comfort. Per soddisfare queste esigenze, i produttori stanno sviluppando materiali e metodi di fabbricazione che non erano disponibili quando sono stati stabiliti gli standard di certificazione. Nuovi materiali, e soprattutto nuovi metodi di riduzione del peso, utilizzati nella progettazione e produzione di praticamente ogni componente del sistema ferroviario hanno creato la necessità di nuove procedure di test di sviluppo che esulano dall'ambito dei test di certificazione tradizionali.
Per queste applicazioni strutturali più grandi, sono necessari telai a portale a due o quattro colonne con configurazioni di attuatori personalizzate (vedi Figura 3). Poiché molte delle forze su un carrello sono elevate, gli attuatori utilizzati per replicare questi carichi sono grandi. L'applicazione diretta degli attuatori ai punti di carico può richiedere che più attuatori occupino lo stesso spazio fisico contemporaneamente. Questo è un problema la cui soluzione richiede una notevole esperienza nei fissaggi e nei meccanismi cinematici. Le combinazioni di attuatori, leve, montanti (colonne portanti) e cuscinetti vengono utilizzate per applicare i vettori di carico alle posizioni corrette. I sensori di carico possono essere installati su attuatori, montanti di carico e/o dispositivi di reazione. I cuscinetti girevoli su entrambe le estremità dei montanti e degli attuatori eliminano i carichi laterali e di flessione. In alcuni casi, il campione può essere capovolto per consentire un migliore accesso ai punti di carico.
L'accoppiamento incrociato – quando l'azione di un attuatore ne influenza un altro – presenta seri problemi di controllo che devono essere superati. Il controller digitale e il software devono collaborare per coordinare l'ampiezza e la fase dei canali interessati, per eliminare il rischio di interferenze e garantire un caricamento accurato. In genere, sono coinvolte tecniche di controllo avanzate. L'intero sistema, compreso il sottosistema campione, telaio e attuatore, potrebbe contenere alcune non linearità naturali. Tenere conto di queste non linearità può richiedere la modifica dei segnali di azionamento, per ottenere la cronologia di carico desiderata sul campione.
Le regolazioni vengono in genere effettuate con un software di elaborazione del segnale avanzato, come MTS Remote Parameter Control (RPC®), che si basa sulla matrice della funzione di risposta in frequenza (FRF) dell'intero sistema. Il software misura il comando del controller e lo confronta con l'ampiezza e la fase delle risposte del campione nell'intervallo di frequenza desiderato. Viene generata una matrice di accoppiamento incrociato, che include tutti gli accoppiamenti incrociati e altre differenze lineari tra comando e risposta. Questa FRF viene quindi invertita e moltiplicata per la risposta desiderata. Il risultato è un file di azionamento dell'attuatore che compensa l'accoppiamento incrociato e i problemi correlati. I contributi non lineari vengono corretti calcolando l'errore, creando un file di correzione corrispondente e quindi applicando la correzione al file di unità precedente. Questo processo iterativo viene ripetuto fino a raggiungere la precisione desiderata. L'applicazione di tali tecniche di compensazione del controllo consente al test di essere eseguito con precisione a una frequenza molto più elevata, il che riduce il tempo di test e ne aumenta la qualità.
Mentre ciò avviene, gli ingegneri devono essere in grado di raccogliere e gestire grandi quantità di dati. Il sistema di test potrebbe dover ospitare, ad esempio, fino a 250 estensimetri e canali di spostamento per trovare potenziali vulnerabilità nel progetto. Alcuni di questi dati devono essere raccolti in tempo reale per l'uso nel sistema di controllo, mentre quantità ancora maggiori di dati devono essere raccolte per l'analisi offline e il confronto con i modelli di ingegneria assistita da computer (CAE).
Superare tutte queste sfide è difficile, ma vale l'investimento. I risultati consentono ai produttori di componenti di ottimizzare i progetti, differenziare le nuove offerte di prodotti e fornire la fiducia nella qualità e affidabilità dei nuovi componenti di cui i clienti hanno bisogno.
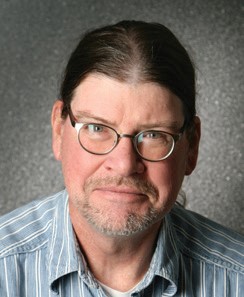