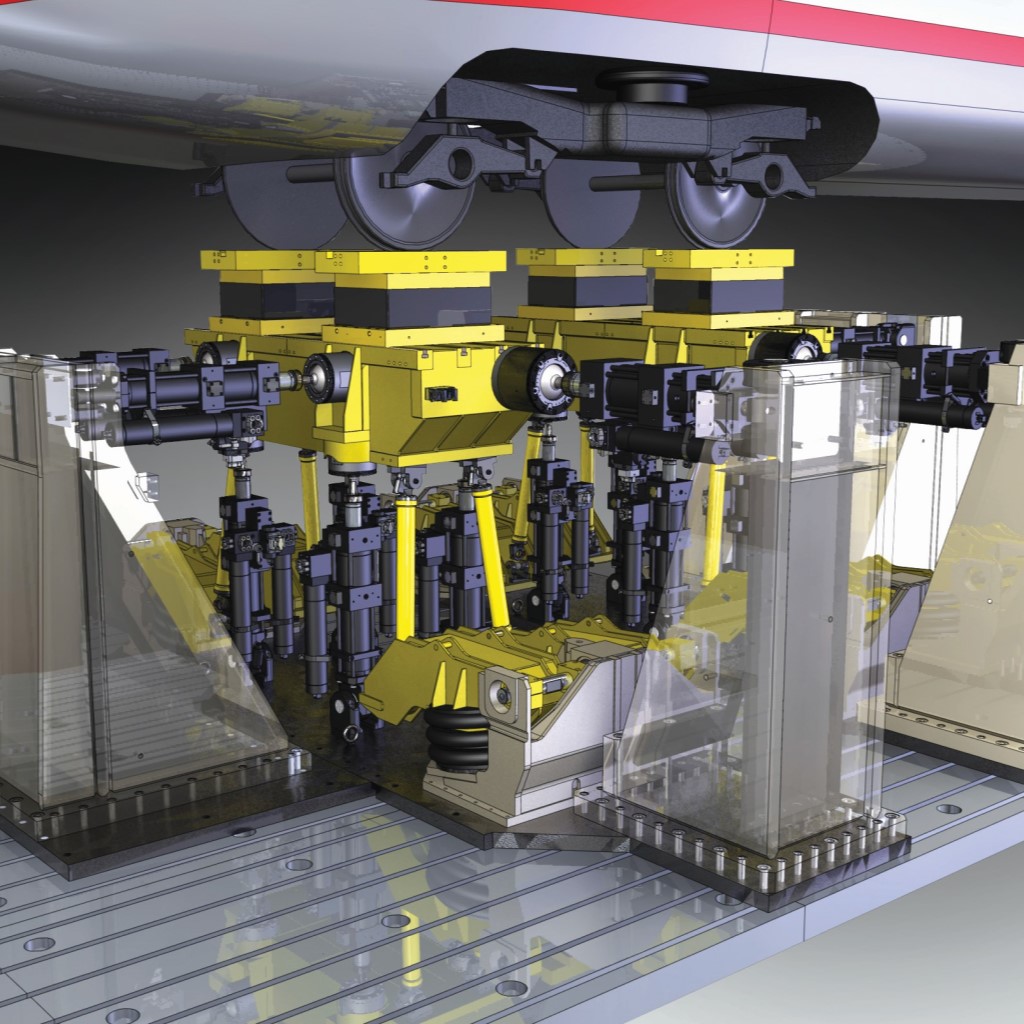
La crescita globale dei viaggi in treno sta aumentando la domanda di nuovi vagoni ferroviari per passeggeri, il che è una buona notizia per i produttori di tutto il mondo. Allo stesso tempo, questi nuovi vagoni devono soddisfare aspettative più elevate. I moderni vagoni ferroviari devono viaggiare a velocità più elevate, offrire un viaggio confortevole, massimizzare l'efficienza energetica e, naturalmente, raggiungere la piena conformità normativa.
Affrontare queste esigenze presenta una serie impegnativa di sfide progettuali nello stesso momento. L'efficienza dipende dalla rimozione del peso, ma ciò non può influire sulla stabilità. La stabilità diventa più difficile alle alte velocità e i vagoni ferroviari più veloci al mondo ora corrono fino a 350 chilometri all'ora. Il comfort di viaggio è anche più difficile da ottenere alle alte velocità.
Poiché questi fattori sono correlati, i produttori devono essere in grado di ottimizzare i nuovi progetti per gestire efficacemente i compromessi. Ad esempio, un carrello più rigido potrebbe fornire una maggiore stabilità ma un minor comfort. La rigidità del telaio può essere modificata per offrire una migliore maneggevolezza o un'esperienza più confortevole per il passeggero, ma non entrambe le cose allo stesso tempo.
I team di sviluppo del prodotto sono sottoposti a un'intensa pressione a causa dell'elevata domanda del mercato, quindi i progettisti devono lavorare rapidamente. È qui che i test meccanici diventano molto utili.
SFIDE IN LABORATORIO
Nel laboratorio di test, i progettisti di componenti possono esaminare molte iterazioni di un nuovo progetto in tempi relativamente brevi e in modo altamente controllato e ripetibile. I risultati dei test rivelano coefficienti e altri fattori che possono essere reimmessi nei modelli virtuali di componenti e sottosistemi per renderli più accurati. Questo aiuta ad accelerare il processo di analisi e miglioramento di nuovi progetti.
Il laboratorio offre sfide tutte sue. L'elenco dei test rilevanti è lungo e ognuno richiede in genere un diverso tipo di sistema di test con una configurazione univoca. L'acquisizione dei sistemi necessari per ottimizzare i nuovi progetti di carrelli può essere costosa. La configurazione e l'esecuzione dei test può diventare inefficiente quando sono in uso più sistemi.
La sfida più grande di tutte è la necessità di testare l'intero meccanismo, non solo un singolo componente. Questo può sembrare controintuitivo, ma i progettisti avanzati comprendono che il test di singole parti non fornisce la stessa accuratezza o comprensione del test di un carrello completo.
Sebbene i test discreti dei componenti siano più facili da gestire e possano essere eseguiti rapidamente, non forniscono la stessa precisione del test di tutti i componenti di un sistema. Le interazioni dei componenti producono comportamenti imprevisti a causa dell'attrito e del movimento fuori asse. Queste interazioni non possono essere replicate valutando ogni componente separatamente. Gli ingegneri sospettavano da tempo che fosse così, ma solo nell'ultimo decennio è diventato evidente. I modelli virtuali sono diventati più sofisticati, ma gli ingegneri non sono stati in grado di prevedere con precisione le prestazioni del sistema su rotaia in base alle caratteristiche dei singoli componenti.
Recentemente è stato messo in servizio un innovativo sistema di test per vagoni ferroviari, che può essere utilizzato per misurare la cinematica e la conformità di un meccanismo completo del carrello. Il sistema, fornito da MTS Systems Corp., può essere utilizzato anche per fornire caratterizzazione, durabilità di base e test di vibrazione, il tutto in un unico sistema.
TEST DI SOSPENSIONE PRIMARIA E SECONDARIA
Attualmente installato presso un produttore in Asia di vagoni ferroviari ad alta velocità per passeggeri, il nuovo sistema di misurazione del carrello fornisce le dimensioni e la forza necessarie per caricare un carrello completo e un vagone ferroviario completo. Il sistema di test incorpora una notevole strumentazione progettata per misurazioni estremamente precise di questi complessi meccanismi.
La complessità deriva dai molti modi in cui i dati dei test possono essere distorti. Per garantire risultati accurati, i sistemi di test devono essere in grado di prevenire (o compensare) tutti i seguenti fenomeni: sfasamento causato da sferza o smorzamento; distorsione del segnale e rumore causati dalle risonanze del sistema e del campione; ed errori di misurazione della forza derivanti da diafonia, compensazione della temperatura dei trasduttori, espansione e contrazione termica di dispositivi e campioni, errori di calibrazione, slittamento, deriva o danneggiamento di trasduttori, supporti, cavi o condizionatori. In molti casi, più segnali vengono combinati per calcolare il risultato desiderato, aggravando l'errore totale.
Alcuni dei test più importanti che il sistema esegue sono quelli della sospensione primaria, che comprende tutti i componenti tra il carrello e l'assale (molla, molla elicoidale, barra di torsione, pastiglia in gomma eccetera). Mentre la sospensione primaria influisce sullo sterzo, sulla manovrabilità e in una certa misura sul comfort del pilota, gli ingegneri devono comprendere in modo molto dettagliato il montaggio completo delle ruote e il sistema di sospensione per ottimizzare i nuovi progetti. La rigidità della sospensione primaria è nella stessa gamma della rigidità del telaio del carrello e l'interazione tra le due determina la risposta complessiva alla manovrabilità del carrello. Per questo motivo, il nuovo sistema di test è progettato in modo univoco per misurare i contributi dei singoli componenti o le caratteristiche dell'intero assemblaggio come sistema integrato.
Il test di rigidità della sospensione primaria prevede il fissaggio della sospensione secondaria, il montaggio di trasformatori differenziali variabili lineari (LVDT) nell'alloggiamento del cuscinetto dell'assale e nei punti di risposta del carrello e l'applicazione di forza o spostamento programmati in ciascuno dei gradi di libertà (DOF) desiderati. Per ottenere un risultato utile, gli ingegneri devono garantire l'accuratezza e la risoluzione delle celle di carico e degli LVDT, mantenere una temperatura costante in laboratorio ed eseguire misurazioni a velocità diverse per valutare le caratteristiche di ammortizzazione. È importante misurare la rigidità del carrello in ogni direzione, non solo in verticale, perché la stabilità è una funzione degli spostamenti multiassiali combinati, non solo verticali. Durante le curve, ad esempio, il carrello si deforma (deformandosi nell'asse di imbardata) e la rigidità di curvatura è fondamentale per una sterzata stabile.
Questa stessa configurazione può essere utilizzata per eseguire un test di ammortizzazione della sospensione primaria e valutare l'ammortizzazione in relazione alla rigidità della molla. I dati dei test delle sospensioni primarie sono molto utili per alimentare i modelli virtuali del carrello sia per la generazione che per la convalida del modello.
Un'altra importante serie di test comprende quelli effettuati sulla sospensione secondaria, che si trova tra la parte superiore del carrello e la parte inferiore del vagone. Per questi test la sospensione primaria è fissa e la sospensione secondaria – tipicamente una coppia di airbag – è montata su celle di carico multiassiali. Un infisso simulato di un vagone ferroviario è vincolato in 3DOF e controllato nei restanti 3DOF per sottoporre la sospensione secondaria agli stessi carichi e deformazioni che subisce in servizio. Ciò consente di valutare le caratteristiche di rigidità e ammortizzazione. A causa della forma inclinata del "cappello" dell'airbag, è particolarmente difficile prevedere la rigidità laterale e al rollio. Il materiale elastomerico si deforma in modi imprevedibili e questi movimenti influiscono notevolmente sul comfort di viaggio.
ULTERIORI TEST DI PRESTAZIONE
Un altro tipo di test che questo sistema può eseguire è la misurazione della coppia di resistenza allo sterzo, in cui il carrello viene ruotato sotto il vagone simulato e viene misurata la sua rigidità. Per eseguire questo test, a ciascun asse vengono applicati carichi o spostamenti laterali uguali e opposti. La tensione/compressione e le forze longitudinali sono impostate a zero e gli attuatori verticali hanno l'ordine di mantenere la forza desiderata o il movimento planare fisso alle ruote.
Inoltre, il sistema di test può essere configurato per testare il coefficiente di sospensione per binario rettilineo o curvo. In questo test, il campione è un vagone ferroviario completo (o simulato) con giroscopi che misurano l'angolo sulle tavole, sui carrelli e sulla carrozzeria. Il test prevede il sollevamento delle ruote su un lato del carrello fino alla sopraelevazione desiderata e la misurazione dell'angolo del carrello e del vagone rispetto all'angolo della tavola. Queste relazioni possono essere difficili da prevedere, a causa dei molti elementi nella sospensione completa. I produttori possono utilizzare un test simile per comprendere il coefficiente di ribaltamento, fondamentale per garantire comfort e sicurezza di viaggio.
Possono essere valutati anche vagoni ferroviari completi. Se gli ingegneri desiderano comprendere la risposta dinamica per i test sui coefficienti, il sistema può essere comandato con rumore a banda larga o forme d'onda specifiche, come un'onda sinusoidale. La risposta della carrozzeria del vagone viene misurata e si può stimare la sua frequenza naturale dai dati risultanti utilizzando un software di test.
Altri test che il sistema può eseguire includono la posizione del centro di gravità, il test del momento di inerzia e la riproduzione in tempo reale dei dati operativi su rotaia.
Sebbene sia vero che un sistema di test delle prestazioni multiuso rappresenta un investimento di capitale significativo per il laboratorio, fornisce un ritorno sull'investimento altrettanto significativo, grazie alla sua capacità di accelerare il programma di test, ridurre i costi e migliorare l'accuratezza dei dati e la caratterizzazione dei campioni. In definitiva, queste capacità consentiranno ai produttori di vagoni ferroviari e carrelli di migliorare la precisione dei modelli, raggiungere l'innovazione più rapidamente, realizzare veicoli di qualità superiore e creare un vantaggio competitivo duraturo.
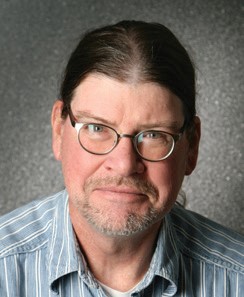