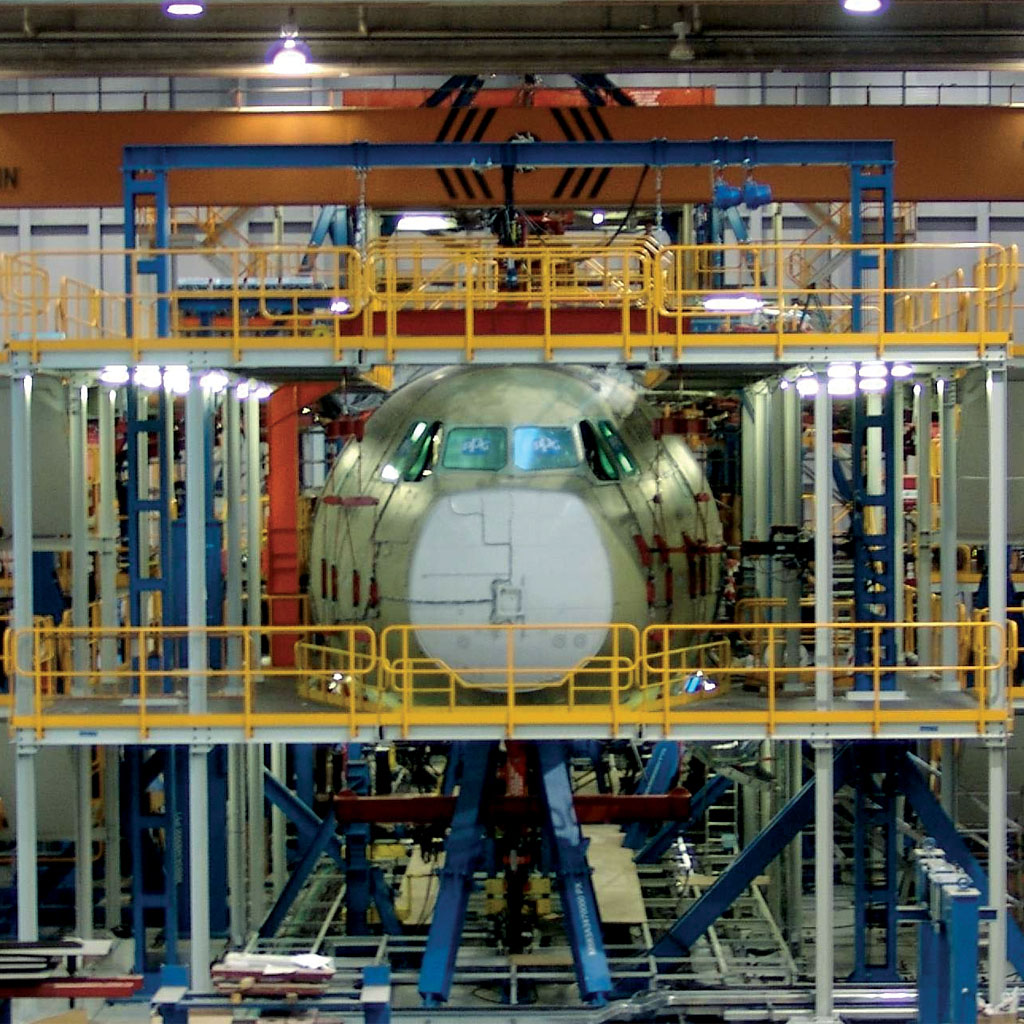
RETO DEL CLIENTE
Con sede en Getafe, España, Airbus Military (antes EADS CASA-MTAD) ha sido responsable del diseño, la producción y las pruebas de aviones militares emblemáticos durante las últimas décadas. Después de la aprobación del programa en 2003, Airbus comenzó a trabajar en el próximo proyecto de alto perfil: el desarrollo del avión de transporte militar Airbus A400M de servicio mediano.
El avión turbohélice de cuatro motores es único por su tamaño relativamente grande y su capacidad para reabastecerse de combustible en el aire. Ya están programados pedidos de 180 aviones A400M para Alemania, Francia, España, Reino Unido, Turquía, Bélgica, Luxemburgo y Malasia. Durante el proceso de desarrollo, el primer artículo de prueba a gran escala se ensambló en Getafe, mientras que al mismo tiempo el banco de pruebas crecía alrededor y dentro del avión. El objetivo era montar la prueba completa en seis meses después de la llegada del ala a Getafe procedente de Sevilla.
“El cronograma de esta aeronave no nos dejó tiempo para retrasos”, indica Angel Gago, jefe del Laboratorio de Pruebas Estructurales de Airbus Military. “Durante las pruebas, nuestro reto sería lograr los niveles más altos de eficiencia y, al mismo tiempo, preservar la integridad estructural del artículo de prueba durante todo el proceso”.
Las pruebas estructurales del Airbus A400M requieren 120 canales de control y más de 9000 calibres extensiométricos, con la capacidad de leer 6000 calibres a la vez. Además, se deben aplicar cargas masivas a los artículos de prueba para simular las condiciones operativas de la aeronave en el mundo real. Gago sabía que con una configuración que implicaba tanta complejidad y fuerzas, mantener la integridad del artículo de prueba requeriría la capacidad de cargar y descargar el sistema de prueba con absoluta precisión.
“Un mal funcionamiento del sistema podría hacernos retroceder meses de tiempo de ingeniería valioso si el artículo de prueba sufría algún daño”, explica Gago. “Esas fallas son raras, pero era un riesgo que no podíamos correr. Para nosotros era fundamental poder eliminar la energía de forma inmediata y uniforme del banco de pruebas en cualquier momento y de forma controlada”.
SOLUCIÓN DE MTS
La relación de Airbus Military con MTS comenzó hace más de 20 años. “Comenzamos a trabajar con MTS en 1978, y cinco años después, MTS nos ayudó a trasladar con éxito nuestras pruebas dentro de un circuito de servocontrol cerrado por primera vez”, comenta Gago. “Ahora utilizamos el software AeroPro™ para todas nuestras pruebas de aeronaves y lascapacidades integradas de control y adquisición de datos nos facilitan la gestión de toda nuestra actividad de pruebas en tiempo real”.
“Nos complació descubrir que MTS no solo ofrece tecnología avanzada en esta área, sino que la tecnología se puede administrar desde la misma interfaz del software AeroPro que ya estábamos usando”, agregó Gago. “La capacidad de MTS para ofrecer la solución de prueba completa, incluidos todos los actuadores, controles y software, nos permitió avanzar más rápido”.
MTS ayudó a Airbus Military a agregar los sistemas Active Load Abort (ALA) a cada uno de sus equipos de prueba para que los utilicer el avión Airbus A400M. La tecnología ALA ayuda a proteger los artículos de prueba al ofrecer un control estricto sobre la descarga del sistema de prueba estructural en caso de una pérdida de energía o bloqueo del sistema.
Durante dicho evento, el sistema ALA utiliza medidas, tanto a nivel de software como de hardware, para reducir todas las cargas de los actuadores a un estado neutral exactamente al mismo tiempo, independientemente de las presiones variables y las posiciones individuales de los actuadores. Un sistema de control separado funciona en paralelo al sistema de control de carga, teniendo en cuenta el estado de toda la prueba al eliminar la presión hidráulica del artículo de prueba. El sistema detecta una falla en el lado del control y luego trabaja para eliminar de manera instantánea y uniforme la carga de todo el artículo de prueba.
“MTS trabajó de cerca con nosotros en cada paso del camino hasta que nuestro sistema ALA estuvo completamente integrado y operativo”, agregó Gago. “Ahora, este sistema funciona de manera uniforme en todo nuestro laboratorio de pruebas, que administramos junto con nuestro servocontrol y adquisición de datos en el entorno AeroPro”.
BENEFICIOS PARA EL CLIENTE
Gago explica que el principal beneficio de la tecnología MTS ALA es que ha permitido a Airbus Military ofrecer una nueva forma de pensar sobre cómo proteger los artículos de prueba que se utilizan durante las pruebas estructurales ante cualquier mal funcionamiento del sistema o comportamientos inesperados.
“Ahora tenemos la confianza de saber que nuestros artículos de prueba están bien protegidos contra daños durante las pruebas”, afirma Gago. “Nuestros ingenieros de pruebas pueden concentrarse en la prueba en sí, sin tener que preocuparse por cómo una falla inesperada en el banco de pruebas podría arruinar su arduo trabajo”.
Según Jesús Posada, jefe de Pruebas Estructurales de Airbus Military, MTS también participará cuando el laboratorio de pruebas ingrese a la siguiente fase de pruebas de fatiga. “Pronto tenemos previsto mejorar la velocidad de nuestras pruebas de fatiga, y pensamos apoyarnos en la experiencia de MTS para que nos ayude a mejorar este tipo de pruebas”, afirma Posada. “Hemos escuchado mucho sobre las herramientas del software AeroPro para acelerar las pruebas dinámicas y esperamos aprovecharlas al máximo en un futuro próximo”.
C