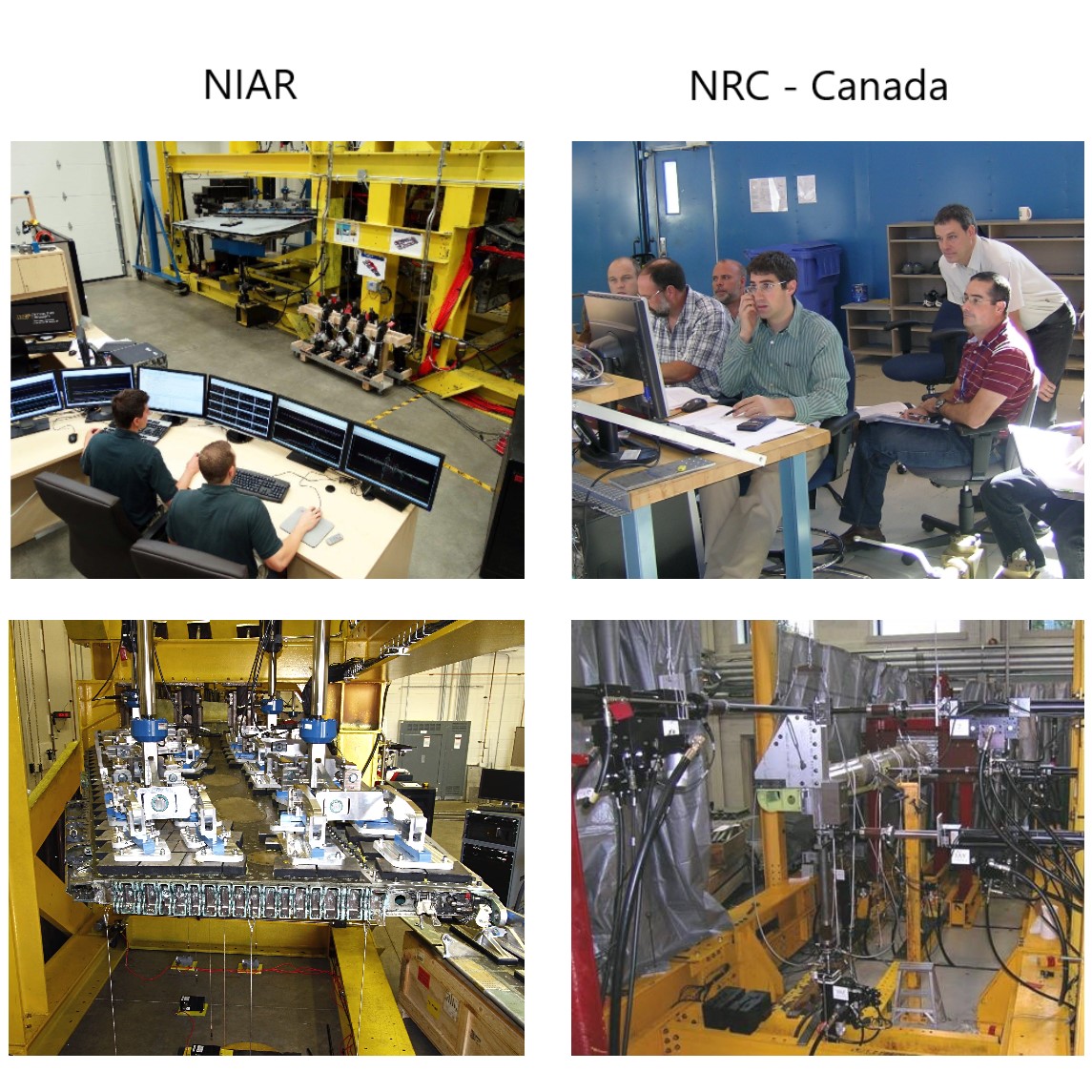
Los bancos de pruebas estructurales a escala real que cuentan con esquemas de actuación altamente acoplados presentan desafíos únicos para los ingenieros de pruebas aeroespaciales. En estas configuraciones complejas, varios actuadores ejercen diferentes fuerzas sobre la misma parte de un artículo de prueba de forma simultánea, lo que aumenta la posibilidad de que se produzcan errores que pueden poner en peligro los cronogramas de las pruebas y retrasar los programas de desarrollo.
Una herramienta para reducir estos errores, mejorando de esta manera la velocidad y la eficiencia de la prueba, es C3Performance, una funcionalidad del software de adquisición de datos y control MTS AeroPro™. Conocido también como C-cubed, C3 Performance permite a los equipos de prueba administrar esquemas de actuación altamente acoplados de manera eficaz, sin tener que dedicar tiempo adicional a los programas de prueba para resolver numerosas paradas y bloqueos recurrentes.
La técnicade compensación de acoplamiento cruzado C3 Performance, se desarrolló conjuntamente por expertos del Consejo Nacional de Investigación de Canadá (NRC) y MTS Systems Corporation. Hoy en día, es una parte estándar del protocolo de pruebas de la NRC, el laboratorio de pruebas estructurales a gran escala de Canadá, donde André Beltempo trabaja como ingeniero de pruebas estructurales.
“Por lo general, usamos C-cubed en todas las pruebas”, afirma Beltempo. “En las pruebas de fatiga a escala real, se observa una interacción muy compleja entre los actuadores. Precisamente por eso lo necesitamos”.
El equipo de Beltempo recientemente utilizó C3Performance durante una demostración de tecnología para un importante fabricante de helicópteros. El programa de pruebas de fatiga y estáticas se centró en una pluma de cola compuesta, fabricada con técnicas avanzadas de fabricación. Las pruebas eran idénticas a las que se utilizarían para certificar que la pieza cumple las exigencias de la FAA en materia de seguridad.
“Si se observa el accesorio de interfaz de la caja de engranajes del rotor de cola, los dos actuadores traseros se cargan en el mismo accesorio", señala Beltempo. "La compensación del acoplamiento cruzado ayuda a minimizar la lucha [entre los actuadores]”
La prueba incluyó seis actuadores y cuatro millones de puntos finales, que funcionaron durante la noche durante alrededor de 125 días, con una frecuencia media de 0,5 Hz. Esta velocidad de prueba hubiera sido imposible sin C3Performance, según Beltempo.
“No podríamos haberlo hecho tan rápido sin la compensación de acoplamiento cruzado”, agregó. “Para una prueba de la noche a la mañana, habríamos tenido que ejecutar los niveles finales a la mitad de la velocidad para no tener que preocuparnos por paradas involuntarias. Nuestro enfoque estándar para cualquier prueba de fatiga es ajustar la prueba, aplicar C-cubed y volver a ajustarla de inmediato. Nunca he visto un aumento de velocidad inferior a un factor de dos para un artículo rígido”.
Otro aspecto que Beltempo aprecia sobre C3Performance es su facilidad de uso general. Gracias a que los operadores de prueba pueden configurarlo por sí mismos, C3Performance ayuda a los laboratorios a ganar aún más tiempo.
“El hecho de que sea un dispositivo de manos libres me permite centrarme en tareas más importantes", afirma Beltempo. “Si tuviera que sentarse y calcular todos los coeficientes por su cuenta, sería diferente. Sin embargo, simplemente haces clic en un botón y sucede. Es una mejora real en la productividad”.
Si bien es natural que la organización que ayudó a desarrollar el C3 Performance lo aplique a cada prueba de fatiga como una cuestión de protocolo, otros laboratorios también están descubriendo el potencial para resolver problemas de esta poderosa utilidad.
Para el Dr. Waruna Seneviratne, director técnico del laboratorio de materiales compuestos y avanzados del Instituto Nacional de Investigación de Aviación (NIAR) de la Universidad Estatal de Wichita, el problema era la falta de sueño.
“Estábamos realizando una prueba de fatiga con una combinación muy particular de sujeciones y actuadores personalizados, y teníamos un programa de pruebas muy agresivo”, afirma Seneviratne. "La prueba se realizó durante la noche y tuvimos un número elevado de activaciones de límites de error molestos. Nuestro equipo tuvo que bajar al laboratorio en mitad de la noche para ver qué era lo que provocaba las paradas de las pruebas y reiniciarlas. Nos estábamos quedando atrás”.
La prueba se centró en la evaluación de la vida útil a la fatiga de las estructuras de material compuesto de los aviones F/A-18 Hornet, muchos de los cuales se acercan a su retiro. Debido a que el reemplazo de la aeronave no estará listo hasta 2019, la Marina de los EE. UU. necesita prolongar de manera segura la vida útil de las estructuras compuestas envejecidas de la aeronave.
La investigación de Seneviratne determinó con éxito que a las juntas encoladas de material compuesto y titanio en la raíz del ala les quedaba mucha vida. La nueva prueba amplió el estudio para incluir toda el ala interior, que tiene una capa de material compuesto. El artículo de prueba incluye el ala interior, el flap de arrastre y el cañón central, así como el flap de arrastre simulado y el ala exterior. El equipo de investigación de NIAR tuvo que construir una plataforma de acero de alta resistencia con accesorios de diseño personalizado y aplicar cargas importantes para recrear maniobras agresivas.
“Había diferencias significativas entre la carrera y las cargas de los actuadores, lo que era una fuente probable de los errores”, expresó. “Necesitábamos una forma de minimizar las paradas falsas, así que empezamos a investigarlo”.
El ingeniero de investigación Travis Cravens, miembro del equipo de Seneviratne, se encargó de instalar y configurar el C3Performance. Los ingenieros de sistemas y aplicaciones de MTS realizaron la instalación y la capacitación en menos de un día y el laboratorio vio los resultados casi de inmediato.
“Al final del primer día ya funcionábamos un 20 % más rápido sin necesidad de realizar modificaciones mecánicas en el banco de pruebas”, señala Cravens. “C3 Performance fue muy fácil de aprender y configurar; todo ocurre dentro del software. Simplemente se crea una matriz de acoplamiento cruzado aplicando una carga unitaria en cada canal de carga, lo que representa solo un paso adicional para cada actuador”.
Para agilizar la configuración de las pruebas, C3 Performance elimina la tarea, que requiere mucho tiempo, de ingresar manualmente los datos de acoplamiento cruzado, al utilizar casos de cargas unitarias para generar coeficientes de compensación de acoplamiento cruzado automatizados. Seneviratne describió este proceso con una analogía acertada.
“Es como tener un equipo de 20 personas que no se conocen trabajando en el mismo proyecto”, afirma. “Las cargas unitarias no son más que una forma de presentar a todas esas personas para que colaboren y trabajen de forma más eficiente”.
Con algunos ajustes adicionales, Seneviratne y Cravens fueron capaces de aumentar la tasa de pruebas en un 24 % y reducir el número de paradas considerablemente.
“Mejoró enormemente el rendimiento de nuestra prueba”, expresó Cravens. “Con la mejora del seguimiento de la carga, es mucho menos probable que las pequeñas perturbaciones en la retroalimentación activen los límites de error, lo que resulta en menos paradas de prueba. La reducción del error también nos ha permitido ejecutar más segmentos por hora”.
Antes de utilizar elC3 Performance, NIAR solo era capaz de alcanzar un máximo de 375 segmentos por hora, con una media de 97 paradas y 55 bloqueos por bloque de pruebas. Con C3 Performance, esto mejoró a 480 segmentos por hora con un promedio de 51 paradas y 15 bloqueos.
“El número de paradas fue un tercio de lo que eran antes, lo que supuso una gran ganancia para nosotros”, menciona Seneviratne. “Eso nos permitió realizar la prueba durante la noche, algunas noches sin una sola interrupción. Son hasta 10 horas de pruebas que no teníamos antes, lo que nos ayudó enormemente con nuestra agenda”.El
C3 Performance ahorró semanas, lo que permitió al equipo de Seneviratne proporcionar los resultados de las pruebas a tiempo. Además, se mejoró la productividad del laboratorio: el equipo pudo funcionar con un cronograma más predecible y tuvo más tiempo para dedicarlo a otros proyectos. En cualquier laboratorio con recursos limitados, esa es una ventaja importante.
“Saber que podíamos realizar la prueba durante la noche y estar seguros de que podíamos realizar inspecciones y reparaciones durante el día nos permitió aumentar la eficiencia de nuestra ruta de prueba”, señala Seneviratne. “Pudimos planificar mejor y coordinar nuestras actividades sabiendo que la prueba se realizó durante la noche sin supervisión y con interrupciones mínimas”.
Una herramienta para reducir estos errores, mejorando de esta manera la velocidad y la eficiencia de la prueba, es C3Performance, una funcionalidad del software de adquisición de datos y control MTS AeroPro™. Conocido también como C-cubed, C3 Performance permite a los equipos de prueba administrar esquemas de actuación altamente acoplados de manera eficaz, sin tener que dedicar tiempo adicional a los programas de prueba para resolver numerosas paradas y bloqueos recurrentes.
La técnicade compensación de acoplamiento cruzado C3 Performance, se desarrolló conjuntamente por expertos del Consejo Nacional de Investigación de Canadá (NRC) y MTS Systems Corporation. Hoy en día, es una parte estándar del protocolo de pruebas de la NRC, el laboratorio de pruebas estructurales a gran escala de Canadá, donde André Beltempo trabaja como ingeniero de pruebas estructurales.
“Por lo general, usamos C-cubed en todas las pruebas”, afirma Beltempo. “En las pruebas de fatiga a escala real, se observa una interacción muy compleja entre los actuadores. Precisamente por eso lo necesitamos”.
El equipo de Beltempo recientemente utilizó C3Performance durante una demostración de tecnología para un importante fabricante de helicópteros. El programa de pruebas de fatiga y estáticas se centró en una pluma de cola compuesta, fabricada con técnicas avanzadas de fabricación. Las pruebas eran idénticas a las que se utilizarían para certificar que la pieza cumple las exigencias de la FAA en materia de seguridad.
“Si se observa el accesorio de interfaz de la caja de engranajes del rotor de cola, los dos actuadores traseros se cargan en el mismo accesorio", señala Beltempo. "La compensación del acoplamiento cruzado ayuda a minimizar la lucha [entre los actuadores]”
La prueba incluyó seis actuadores y cuatro millones de puntos finales, que funcionaron durante la noche durante alrededor de 125 días, con una frecuencia media de 0,5 Hz. Esta velocidad de prueba hubiera sido imposible sin C3Performance, según Beltempo.
“No podríamos haberlo hecho tan rápido sin la compensación de acoplamiento cruzado”, agregó. “Para una prueba de la noche a la mañana, habríamos tenido que ejecutar los niveles finales a la mitad de la velocidad para no tener que preocuparnos por paradas involuntarias. Nuestro enfoque estándar para cualquier prueba de fatiga es ajustar la prueba, aplicar C-cubed y volver a ajustarla de inmediato. Nunca he visto un aumento de velocidad inferior a un factor de dos para un artículo rígido”.
Otro aspecto que Beltempo aprecia sobre C3Performance es su facilidad de uso general. Gracias a que los operadores de prueba pueden configurarlo por sí mismos, C3Performance ayuda a los laboratorios a ganar aún más tiempo.
“El hecho de que sea un dispositivo de manos libres me permite centrarme en tareas más importantes", afirma Beltempo. “Si tuviera que sentarse y calcular todos los coeficientes por su cuenta, sería diferente. Sin embargo, simplemente haces clic en un botón y sucede. Es una mejora real en la productividad”.
Si bien es natural que la organización que ayudó a desarrollar el C3 Performance lo aplique a cada prueba de fatiga como una cuestión de protocolo, otros laboratorios también están descubriendo el potencial para resolver problemas de esta poderosa utilidad.
Para el Dr. Waruna Seneviratne, director técnico del laboratorio de materiales compuestos y avanzados del Instituto Nacional de Investigación de Aviación (NIAR) de la Universidad Estatal de Wichita, el problema era la falta de sueño.
“Estábamos realizando una prueba de fatiga con una combinación muy particular de sujeciones y actuadores personalizados, y teníamos un programa de pruebas muy agresivo”, afirma Seneviratne. "La prueba se realizó durante la noche y tuvimos un número elevado de activaciones de límites de error molestos. Nuestro equipo tuvo que bajar al laboratorio en mitad de la noche para ver qué era lo que provocaba las paradas de las pruebas y reiniciarlas. Nos estábamos quedando atrás”.
La prueba se centró en la evaluación de la vida útil a la fatiga de las estructuras de material compuesto de los aviones F/A-18 Hornet, muchos de los cuales se acercan a su retiro. Debido a que el reemplazo de la aeronave no estará listo hasta 2019, la Marina de los EE. UU. necesita prolongar de manera segura la vida útil de las estructuras compuestas envejecidas de la aeronave.
La investigación de Seneviratne determinó con éxito que a las juntas encoladas de material compuesto y titanio en la raíz del ala les quedaba mucha vida. La nueva prueba amplió el estudio para incluir toda el ala interior, que tiene una capa de material compuesto. El artículo de prueba incluye el ala interior, el flap de arrastre y el cañón central, así como el flap de arrastre simulado y el ala exterior. El equipo de investigación de NIAR tuvo que construir una plataforma de acero de alta resistencia con accesorios de diseño personalizado y aplicar cargas importantes para recrear maniobras agresivas.
“Había diferencias significativas entre la carrera y las cargas de los actuadores, lo que era una fuente probable de los errores”, expresó. “Necesitábamos una forma de minimizar las paradas falsas, así que empezamos a investigarlo”.
El ingeniero de investigación Travis Cravens, miembro del equipo de Seneviratne, se encargó de instalar y configurar el C3Performance. Los ingenieros de sistemas y aplicaciones de MTS realizaron la instalación y la capacitación en menos de un día y el laboratorio vio los resultados casi de inmediato.
“Al final del primer día ya funcionábamos un 20 % más rápido sin necesidad de realizar modificaciones mecánicas en el banco de pruebas”, señala Cravens. “C3 Performance fue muy fácil de aprender y configurar; todo ocurre dentro del software. Simplemente se crea una matriz de acoplamiento cruzado aplicando una carga unitaria en cada canal de carga, lo que representa solo un paso adicional para cada actuador”.
Para agilizar la configuración de las pruebas, C3 Performance elimina la tarea, que requiere mucho tiempo, de ingresar manualmente los datos de acoplamiento cruzado, al utilizar casos de cargas unitarias para generar coeficientes de compensación de acoplamiento cruzado automatizados. Seneviratne describió este proceso con una analogía acertada.
“Es como tener un equipo de 20 personas que no se conocen trabajando en el mismo proyecto”, afirma. “Las cargas unitarias no son más que una forma de presentar a todas esas personas para que colaboren y trabajen de forma más eficiente”.
Con algunos ajustes adicionales, Seneviratne y Cravens fueron capaces de aumentar la tasa de pruebas en un 24 % y reducir el número de paradas considerablemente.
“Mejoró enormemente el rendimiento de nuestra prueba”, expresó Cravens. “Con la mejora del seguimiento de la carga, es mucho menos probable que las pequeñas perturbaciones en la retroalimentación activen los límites de error, lo que resulta en menos paradas de prueba. La reducción del error también nos ha permitido ejecutar más segmentos por hora”.
Antes de utilizar elC3 Performance, NIAR solo era capaz de alcanzar un máximo de 375 segmentos por hora, con una media de 97 paradas y 55 bloqueos por bloque de pruebas. Con C3 Performance, esto mejoró a 480 segmentos por hora con un promedio de 51 paradas y 15 bloqueos.
“El número de paradas fue un tercio de lo que eran antes, lo que supuso una gran ganancia para nosotros”, menciona Seneviratne. “Eso nos permitió realizar la prueba durante la noche, algunas noches sin una sola interrupción. Son hasta 10 horas de pruebas que no teníamos antes, lo que nos ayudó enormemente con nuestra agenda”.El
C3 Performance ahorró semanas, lo que permitió al equipo de Seneviratne proporcionar los resultados de las pruebas a tiempo. Además, se mejoró la productividad del laboratorio: el equipo pudo funcionar con un cronograma más predecible y tuvo más tiempo para dedicarlo a otros proyectos. En cualquier laboratorio con recursos limitados, esa es una ventaja importante.
“Saber que podíamos realizar la prueba durante la noche y estar seguros de que podíamos realizar inspecciones y reparaciones durante el día nos permitió aumentar la eficiencia de nuestra ruta de prueba”, señala Seneviratne. “Pudimos planificar mejor y coordinar nuestras actividades sabiendo que la prueba se realizó durante la noche sin supervisión y con interrupciones mínimas”.