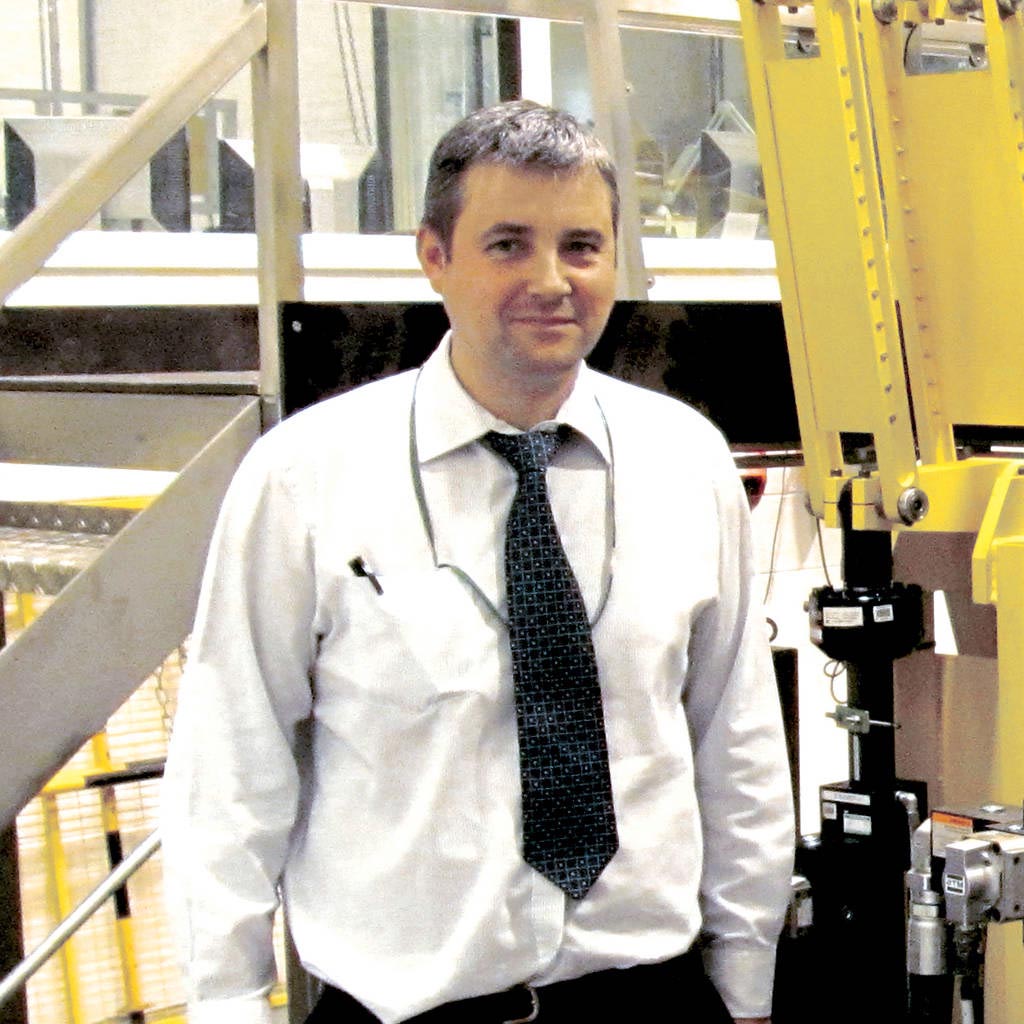
RETO DEL CLIENTE
Jaguar Land Rover (JLR) ofrece una variada cartera de vehículos y fabrica algunos de los vehículos de lujo y 4x4 más conocidos del mundo. Para respaldar el desarrollo continuo de esta cartera, los ingenieros de pruebas estructurales en dos instalaciones en el Reino Unido se mantienen ocupados realizando baterías de pruebas de durabilidad en numerosos componentes, subsistemas y prototipos de vehículos. Entre los que lideran este esfuerzo se encuentra Ian Payne, líder del grupo de análisis y verificación de productos. El equipo de Payne es responsable de los equipos de prueba que se utilizan para evaluar la fuerza y la resistencia de todos los productos JLR desde el nivel de los componentes hasta la simulación completa del vehículo.
“Diseñamos, fabricamos y operamos equipos que van desde plataformas de un solo eje hasta simuladores de carretera de vehículos completos de última generación en todos nuestros laboratorios”, señala Payne. “Somos la base de la verificación de la durabilidad del vehículo. Los datos que recopilamos respaldan el desarrollo de productos en todo el negocio".
Uno de los mayores retos que enfrenta Payne es la presión constante para producir mejores resultados más rápido, acelerando la velocidad de comercialización de productos nuevos. Como resultado, Payne y su equipo buscan todas las oportunidades para mejorar la precisión y eficiencia de las pruebas. Una forma en que abordan el problema es a través de la integración de pruebas, combinando múltiples pruebas concretos en una sola simulación rica en datos.
“La máxima prioridad para nosotros es optimizar el tiempo de prueba”, afirma Payne. “La desventaja es que estamos recibiendo pruebas más complejos. Es muy difícil simular todos los sistemas activos de nuestros vehículos, como la amortiguación variable, el balanceo activo y los diferenciales activos, e incorporar toda esa complejidad en un prueba en tiempo real”.
SOLUCIÓN DE MTS
Hoy, JLR está resolviendo este reto con un par de sistemas MAST (Mesa de simulación multiaxial) de MTS. El equipo de Payne utiliza los sistemas MAST para verificar la resistencia estructural de los sistemas completos de montaje del motor, incluido el tren de fuerza y la transmisión, con entradas de la carrocería, cargas de montaje del motor estructural y par en tiempo real suministrado a través de los accesorios de entrada de par (TIF).
"Realizamos simulaciones en tiempo real para establecer la resistencia estructural a lo largo de la vida útil prevista del vehículo", indica Payne. “Con los sistemas MAST de MTS, podemos ver todo el sistema de montaje del motor a la vez. También nos permite observar el embalaje del vehículo, incluido el embalaje debajo del capó y los arneses de cableado. Es una gran herramienta para nosotros".
Disponibles en configuraciones ortogonales y hexapodales, los sistemas MTS MAST están diseñados para reproducir con precisión los fenómenos de vibración de los entornos de servicio reales en entornos de laboratorio controlados. Los sistemas ortogonales que utiliza el equipo de Payne cuentan con mesas cuadradas de 2 x 3 metros sin resonancias y son capaces de proporcionar simulaciones de seis grados de libertad (6DOF): tres actuadores verticales aplican movimientos verticales, de cabeceo y de balanceo, mientras que tres actuadores horizontales aplican movimientos laterales, de guiñada y longitudinales.
"Ponemos cargas de control directas en el tren de potencia, normalmente longitudinales y laterales, y ocasionalmente verticales, para asegurar las cargas medias correctas en los soportes del motor durante las pruebas", explicó Payne. “Es una mesa bastante grande. Nos permite empaquetar un sistema completo de tren de fuerza delantero 4x4 con el motor V8. Hacemos funcionar la mesa a frecuencias de hasta 30 Hz, y el par motor hasta 20 Hz".
BENEFICIOS PARA EL CLIENTE
Según Payne, los sistemas MTS MAST son esenciales para combinar en un solo prueba muchos que antes estaban separados. En concreto, el diseño robusto del sistema MAST y su elevada carga útil permiten al equipo de Payne maximizar la masa de la probeta, mientras que el control de movimiento 6DOF de precisión proporciona todas las capacidades de prueba necesarias para un espectro completo de verificación de prototipos.
Intentamos hacer todos las pruebas que podamos en un solo prototipo físico", explicó Payne. “Es más complejo, pero en realidad estamos ahorrando una gran cantidad de tiempo durante el desarrollo. la prueba también es más sólido porque las interacciones del sistema funcionan todas juntas, lo que es mucho más real".
Un mayor realismo significa que un solo prueba MAST puede arrojar luz sobre muchas de las fallas del mundo real que los equipos de JLR esperan ver una vez que los prototipos lleguen a la pista de pruebas. Entender y solucionar estas fallas antes del campo de pruebas mejora la eficiencia y acorta el tiempo de comercialización.
“Con una prueba de 6DOF, obtenemos una gran comprensión de la resistencia estructural completa del vehículo”, menciona Payne. “El sistema MAST es fantástico para este trabajo. Con respecto a la combinación de pruebas y la creación de simulaciones de vehículos completos más complejas, nuestro enfoque se mantendrá en el sistema MAST y las pruebas 6DOF por el momento".
Los sistemas de prueba, por supuesto, son solo una parte de la solución completa. MTS también proporciona un software de prueba líder en el sector, así como servicio y asistencia especializados, en los que el equipo de Payne ha llegado a confiar.
“Recibimos gran apoyo de MTS”, afirma Payne. “Tenemos relaciones sólidas con todos los miembros del equipo de MTS y tenemos un gran respeto por la experiencia que aportan los ingenieros de servicio de campo. Su conocimiento técnico es muy apreciado y será muy valioso a medida que seguimos avanzando”.