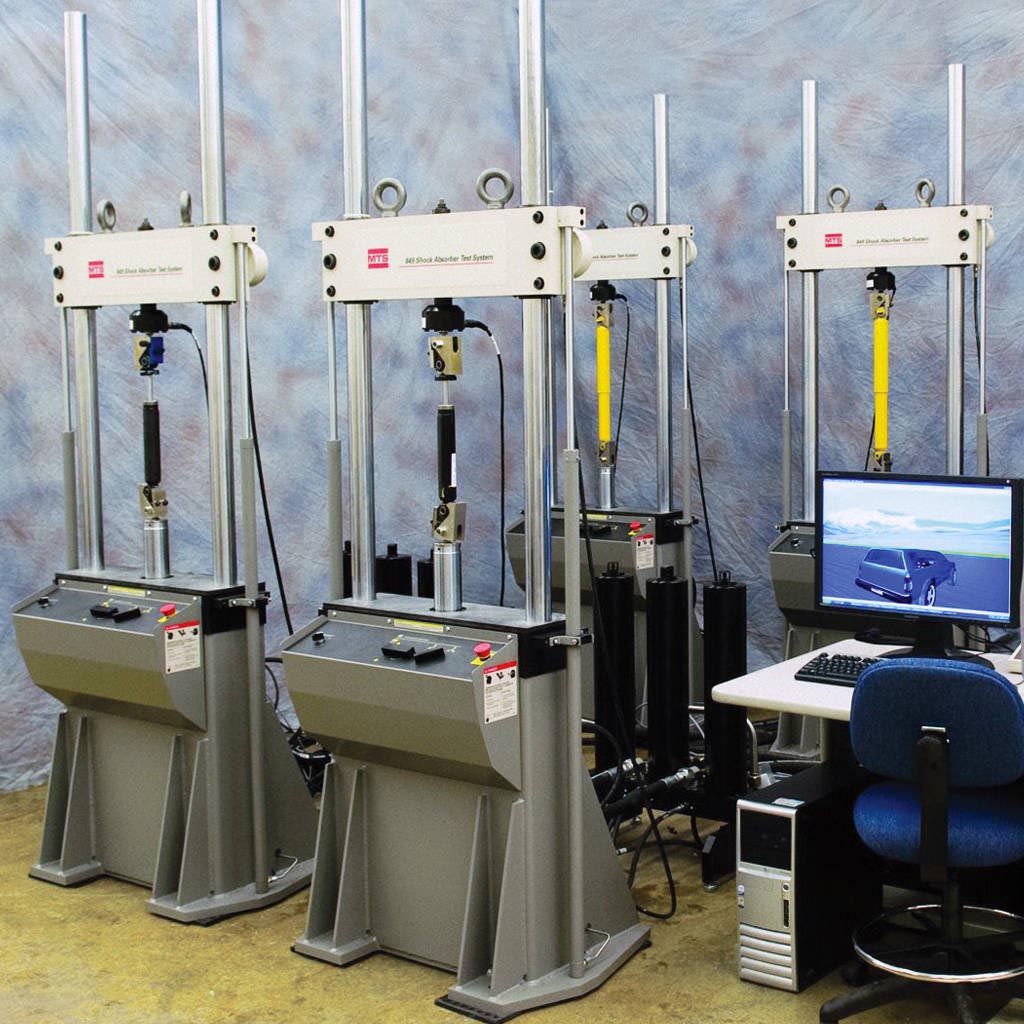
RETO DEL CLIENTE
Nissan® se esfuerza por satisfacer la demanda de los consumidores de productos de alta calidad y alto rendimiento. Satisfacer estas demandas de manera oportuna requiere no solo un desarrollo efectivo, sino también una validación eficiente para evitar iteraciones costosas y lentas entre las dos actividades. La mejora continua de herramientas y métodos es especialmente importante en el contexto de la consecución de los objetivos de la dinámica de los vehículos, en la que los ingenieros buscan constantemente la posibilidad de obtener una visión más profunda del rendimiento de los subsistemas que se utilizan en los vehículos en una fase más temprana del desarrollo.
Aunque las herramientas de ingeniería asistida por computadora (CAE) proporcionan una predicción oportuna del rendimiento, lo que permite reducir el tiempo y los costos de desarrollo, ciertas limitaciones impiden que estas herramientas revelen fenómenos inesperados o desconocidos durante el desarrollo. Aplazar el descubrimiento de los fenómenos inesperados hasta la pista supone un riesgo para los presupuestos y los calendarios. Una forma de evitar los riesgos asociados con el descubrimiento tardío es complementar el CAE con pruebas físicos durante el desarrollo. Hacerlo promete mejorar la evaluación del desempeño y disminuir la necesidad general de prototipos, lo que se traduce en costos reducidos.
Los ingenieros automotrices de Nissan Motor Co., Ltd. querían poder pasar de la paralización del diseño al inicio de la producción en un año natural. Para alcanzar este objetivo sería necesario mejorar las fortalezas complementarias del CAE y de los procedimientos de prueba, lo que incluye comprender a fondo cómo los subsistemas del vehículo funcionarán e influirán en el rendimiento de cada uno de ellos. Para cumplir plazos de desarrollo tan agresivos, este conocimiento tendría que obtenerse mucho antes de que el prototipo del vehículo esté disponible.
En ese momento, la empresa estaba desarrollando un nuevo sistema de amortiguación y tenía previsto analizar cómo probar este subsistema con mayor precisión y en una fase más temprana del desarrollo. Después de un breve período de descubrimiento, Nissan decidió asociarse con MTS, debido en parte al liderazgo global de 40 años de la compañía en tecnología y experiencia en pruebas de vehículos.
SOLUCIÓN DE MTS
MTS trabajó en estrecha colaboración con Nissan para implementar la tecnología mecánica Hardware-in-the-loop™ (mHIL), que permite realizar evaluaciones del rendimiento del vehículo antes de que el prototipo completo esté disponible.
La tecnología MTS mHIL amplía la tecnología Hardware-in-the-Loop (HIL) ampliamente utilizada para validar unidades de controlador electrónico (ECU), colocando sistemas o componentes mecánicos en el ciclo de un modelo de vehículo en tiempo real. Debido a que la tecnología mHIL usa piezas reales, es más sensible que el CAE solo, lo que lleva a decisiones de desarrollo más efectivas. Además, la tecnología mHIL permite a los ingenieros manejar estas piezas en un entorno virtual que permite resolver problemas y evitar problemas en una etapa mucho más temprana del desarrollo del vehículo. Esta capacidad produce prototipos más robustos y, en última instancia, una validación y un trabajo de seguimiento más eficientes.
MTS y Nissan lanzaron un programa piloto que utiliza la tecnología mHIL para validar el rendimiento de los nuevos sistemas de amortiguación que se están desarrollando en Nissan. Este sistema de pruebas piloto acabaría convirtiéndose en el Sistema de pruebas de amortiguación de cuatro esquinas MTS que actualmente utilizan los ingenieros de Nissan. Los resultados del piloto mostraron una correlación superior entre los datos de las pruebas y las pruebas reales en pista para analizar tanto la comodidad de conducción como el manejo. Utilizando el Sistema de pruebas de amortiguación de cuatro esquinas MTS, Nissan redujo en un 40 % los cambios retroactivos en sus vehículos en desarrollo.
BENEFICIOS PARA EL CLIENTE
El Sistema de pruebas de amortiguación de cuatro esquinas MTS con tecnología mHIL permite a Nissan identificar y resolver problemas derivados de comportamientos inesperados del subsistema en una etapa temprana del desarrollo del vehículo. La tecnología le ahorra a Nissan mucho tiempo y dinero al exponer fenómenos inesperados que anteriormente solo surgían cuando se conducía un prototipo en una pista de prueba.
"La tecnología MTS mHIL nos permite descubrir y resolver elementos desconocidos del desarrollo de funciones de calidad (QFD) durante la etapa de preparación, reduciendo el tiempo de prueba de nuestro vehículo en al menos un mes", manisfestó Yoichi Sakai, representante principal del desarrollo experimental de sistemas de Nissan. “En un momento en el que muchos fabricantes están reduciendo el desarrollo de vehículos experimentales, la tecnología mHIL nos brinda un medio rápido, preciso y asequible para continuar con esas iniciativas.
“Además, la eficiencia lograda a través de la tecnología mHIL también nos permite ofrecer vehículos de mayor calidad a los consumidores a un precio más asequible”, agregó el Sr. Sakai.
En 2008, MTS y Nissan Motor Co., Ltd. recibieron el premio Herramienta de desarrollo del año de la revista Vehicle Dynamics International, por su trabajo colaborativo en el desarrollo del sistema de amortiguación de cuatro esquinas utilizando tecnología mHIL.
“La tecnología mHIL representa una auténtica revolución en la velocidad y la rentabilidad del desarrollo de vehículos", afirma Sakai. "Ha sido extremadamente beneficioso para Nissan, y seguramente será igualmente ventajoso para los proveedores".