Subjecting full-scale structures to real-world loading poses enormous challenges for civil engineering test labs. Working with MTS, the University of Minnesota built and maintains one of the world's highest capacity seismic test systems, capable of applying massive forces to very large specimens in six degrees of freedom.
Professor Catherine French, PhD, PE - Laboratory Director explores the unique capabilities of the University of Minnesota Multi-Axial Subassemblage Test (MAST) Lab, used by researchers worldwide for applying realistic loads to large-scale specimens, such as core walls, beam-column frame systems, wind turbine tower bases, and more. Results from these test are used to verify design codes, analyze new materials and systems, and optimize civil project safety and cost-effectiveness.
One of ten original NEES (Network for Earthquake Engineering Simulation) sites, the University of Minnesota MAST Lab integrates state-of-the-art MTS testing technologies, including 6 Degree-of-Freedom (6DOF) Control, ultra-low friction hydrostatic bearings, and advanced quasi-static and real-time hybrid simulation. |
|
|
|

High-bandwidth transducers and accelerometers - typically used in elastomer testing - perform damper NVH measurements with fidelity and accuracy up to 800 Hz. A highly stiff elastomer system load frame with larger diameter columns, a thicker crosshead, and more robust base prevents the resonant modes that can corrupt test data. Linear electric actuation technology provides the clean sinusoidal input and low total harmonic distortion (THD) required for meaningful chuckle testing.
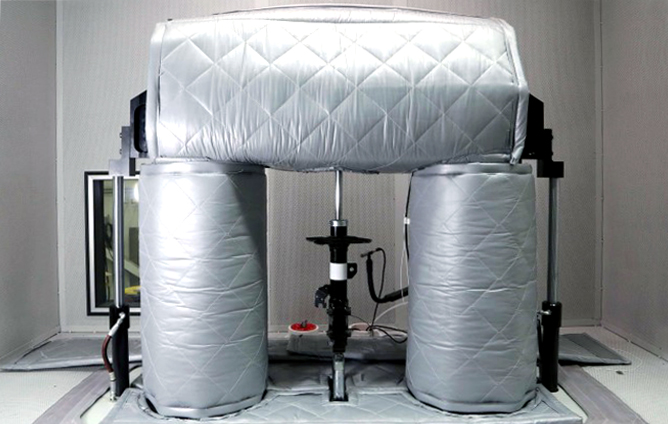
The inherent low audible noise of the Model 853 system combined with the available integrated acoustic chamber enables air-borne "swish" testing with background noise less than 40 decibels.

The multi-functional Model 853 can also perform elastomer testing with an optional elastomer test fixture, MTS Elastomer Testing software, and a versatile FlexTest controller capable of reproducing any signal.