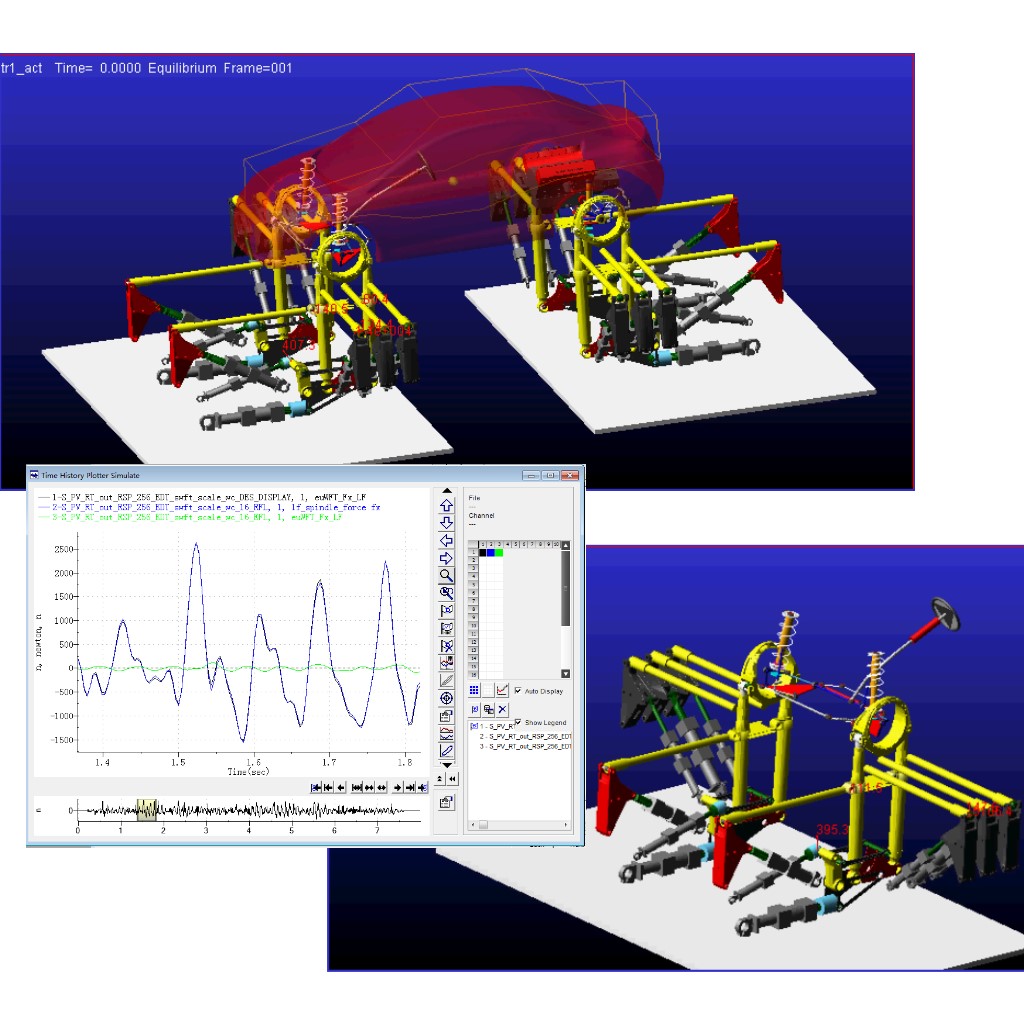
Bajo la incesante presión de acortar los ciclos de desarrollo y reducir los costos, los fabricantes de automóviles exploran cada vez más formas de utilizar herramientas de análisis para realizar evaluaciones virtuales importantes de los diseños de los vehículos desde el principio, mucho antes de que estén disponibles los prototipos físicos. La capacidad de obtener cargas precisas predichas o calculadas de esta manera, aumenta la eficacia de las pruebas físicos de los componentes, permite identificar y eliminar con antelación los defectos de diseño, reduce la necesidad de reelaboración y la dependencia de los prototipos, y agiliza la validación del diseño.
Se han ideado diversos enfoques de simulación para obtener cargas calculadas con precisión en las primeras fases del proceso de desarrollo del vehículo. Un método, el Campo de pruebas virtual, implica "conducir" un modelo de vehículo sobre una carretera digitalizada. Si bien tiene la ventaja de depender completamente de modelos virtuales, este enfoque produce cargas inexactas que son difíciles de validar mediante pruebas físicas. Por otro lado, un método semianalítico utiliza las cargas de los ejes adquiridas de un vehículo existente para excitar el modelo del vehículo. Esto ofrece mejores resultados que el campo de pruebas virtual, pero establece condiciones de límite que no son del todo apropiadas para el modelo del vehículo, por lo que las cargas calculadas siguen siendo incorrectas y difíciles de validar. Un tercer método, la prueba Virtual, supera estos problemas integrando un modelo de un sistema de prueba físico real en la simulación para estimular el modelo del vehículo.
La prueba virtual es la simulación de una prueba física, utilizando herramientas de análisis de elementos finitos, herramientas de análisis dinámico de múltiples cuerpos y técnicas de iteración RPC para derivar cargas precisas, información de movimiento y daños de un sistema de vehículo muy temprano en el proceso de desarrollo. Las ventajas de este enfoque son numerosas. En primer lugar, porque es más fácil modelar las limitaciones de un sistema de prueba físico que probar las superficies del suelo o los neumáticos, las pruebas virtuales establecen condiciones de contorno mucho más eficaces que los otros métodos. En segundo lugar, las pruebas virtualesaprovechan unconjunto de herramientas y técnicas de prueba físico probadas y bien establecidas, que han demostrado su utilidad en el ámbito del análisis. Y tercero, la incorporación de un sistema de prueba físico modelado agiliza en gran medida la validación de los resultados a través de pruebas físicos posteriores y brinda la oportunidad de mejorar las configuraciones de la prueba físico y los diseños de accesorios. Al abarcar las disciplinas de prueba analítico y físico, las pruebas virtuales requieren conocimientos avanzados tanto de las herramientas CAE como de las pruebas físicos, el desarrollo de un proceso para vincular el software RPC Pro y los modelos de análisis y, preferiblemente, cierto grado de exposición y experiencia en pruebas virtuales.
Durante años, MTS se ha centrado en perfeccionar el enfoque de las pruebas virtuales, realizando diversos proyectos de demostración con clientes clave como Hyundai Motor Company (HMC) y Thermo King para evaluar diversas metodologías. Estos proyectos incluyeron pruebas virtuales de vehículos completos y subsistemas, y todos arrojaron una correlación satisfactoria con los datos de carga en carretera (RLD) medidos o con las pruebas físicos reales. La metodología básica extraída de estas experiencias comprende los siguientes pasos: 1) Conecte los modelos de banco de pruebas con modelos de probetas; 2) Acople los modelos con RPC Pro; 3) Reproduzca datos de carga en carretera en el banco de pruebas virtual; 4) Extraiga las cargas calculadas; 5) Cree la prueba del componente físico/subsistema.
Un reciente proyecto de demostración con el State Automotive Institute of China (SAIC) ofrece un excelente ejemplo de esta metodología en la práctica:
- Conectar los modelos de banco de pruebas con modelos de probetas
Al comienzo del proyecto, MTS construyó una colección de modelos de banco de pruebas en formatos de co-simulación ADAMS, Simulink y ADAMS-Simulink. Los bancos de prueba de MTS que se modelaron incluían una variedad de Simuladores de Carretera con eje acoplado modelo 329, un sistema de mesa de simulación multiaxial (MAST) modelo 353.20 y un sistema de prueba de componentes TestLine. Asimismo, se modelaron determinados componentes del banco de pruebas, incluido un controlador digital FlexTest, actuadores y servoválvulas MTS, y un transformador de actuadores que convierte el desplazamiento, la aceleración y la fuerza del actuador en desplazamiento, aceleración y fuerza DOF. Debido a las limitaciones de tiempo del proyecto y a las velocidades de simulación relativamente lentas de los modelos de co-simulación más complejos, el modelo ADAMS/Car 329 se acopló con los modelos de vehículo completo, suspensión delantera y suspensión trasera de SAIC y finalmente se utilizó para la mayor parte de las pruebas virtuales.
- Acoplar los modelos con RPC Pro
Se desarrolló un servidor virtual de pruebas para conectar el software RPC Pro y el modelo ADAMS/Car 329. Durante las pruebas, RPC Pro utiliza este servidor virtual para enviar los archivos de accionamiento al modelo ADAMS, iniciar la simulación ADAMS y copiar el archivo de respuesta de la carpeta ADAMS al directorio de trabajo de RPC Pro. Además, se utilizó una herramienta de interfaz de Matlab ya existente en RPC Pro para acoplar RPC Pro con los modelos de co-simulación.
- Reproducir datos de carga en carretera en el banco de pruebas virtual
Luego se utilizó la técnica de iteración RPC para reproducir los datos de carga de la carretera (fuerza de los ejes) recogidos en el campo de pruebas para una variedad de eventos y maniobras seleccionadas. Curiosamente, las iteraciones iniciales de RPC en las plataformas virtuales 329 no mostraron ninguna convergencia, lo que sugiere fallas en el modelo de vehículo de SAIC. El análisis posterior del modelo sí reveló deficiencias, que se corrigieron en poco tiempo. Con la mejora del modelo, las iteraciones de RPC finalmente convergieron, mostrando una excelente correlación entre las señales deseadas y las logradas y bajos errores RMS en todos los canales para las simulaciones virtuales de vehículos completos y parciales.
- Extraer las cargas calculadas
Después de la convergencia de la iteración RPC, las cargas calculadas para cualquier componente mecánico o subsistema pueden obtenerse fácilmente a partir del modelo del vehículo como funciones del tiempo.
- Crear pruebas físicos
Luego, se utilizaron los historiales de tiempo de carga extraídos del modelo del vehículo para definir las pruebas de componentes físicos posteriores. Una vez que se determina si una pieza está sometida a una carga de un solo eje o de varios ejes, se puede utilizar el conjunto de métodos y herramientas de prueba de RPC Pro para definir pruebas de componentes significativamente acelerados. Para los componentes sometidos a una carga de un solo eje, se puede utilizar el método del ciclo de bloques o el de la densidad espectral de potencia (PSD). Para los componentes sometidos a cargas multieje, puede utilizarse el método Peak Valley Slicing. Para situaciones en las que es necesario preservar la frecuencia de carga de un componente, el método de reproducción del historial temporal es el más apropiado; para este tipo de pruebas, RPC Pro cuenta con la edición sensible a la fatiga, que tiene el potencial de acelerar las pruebas de durabilidad por un factor de 2 a 10. Una vez que se han determinado las señales de carga para cada componente, se puede utilizar el mismo sistema de pruebas físico en el que se basaron los bancos de pruebas virtuales para realizar la prueba de los componentes. Además, se pueden utilizar diversas técnicas de compensación en RPC Pro, como la compensación pico-valle, la compensación inversa adaptativa y la iteración RPC, para asegurarse de que las condiciones de carga deseadas se alcanzan con precisión durante las pruebas físicos.
La exploración continua de MTS de las pruebas virtuales demuestra que es un medio eficaz para predecir con precisión las cargas de los componentes antes del desarrollo de piezas físicas o prototipos. Una vez que se obtienen estas cargas calculadas, las mismas herramientas y técnicas de RPC Pro utilizadas para obtenerlas se pueden utilizar para crear y realizar las pruebas físicos necesarios para validar su precisión, así como la precisión del modelo del vehículo. Las posibles repercusiones de las pruebas virtuales eficaces en el desarrollo del vehículo son considerables. La disponibilidad de cargas exactas previstas y los subsiguientes pruebas físicos anticipados minimizarán la reelaboración de componentes y subsistemas, reducirán la necesidad de múltiples prototipos y acelerarán la validación del diseño. Además, el papel de las pruebas físicos evolucionará: Si bien las pruebas seguirán siendo necesarios para lograr la validación final del diseño de un vehículo, se adaptarán cada vez más a la validación de la precisión del modelo del vehículo. Y, por último, las pruebas virtuales impulsarán la integración de las disciplinas y culturas de análisis y pruebas físicos, propiciando la aparición de nuevas eficiencias a través del intercambio de herramientas, procesos y experiencias.
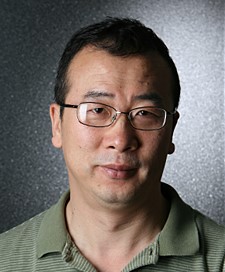