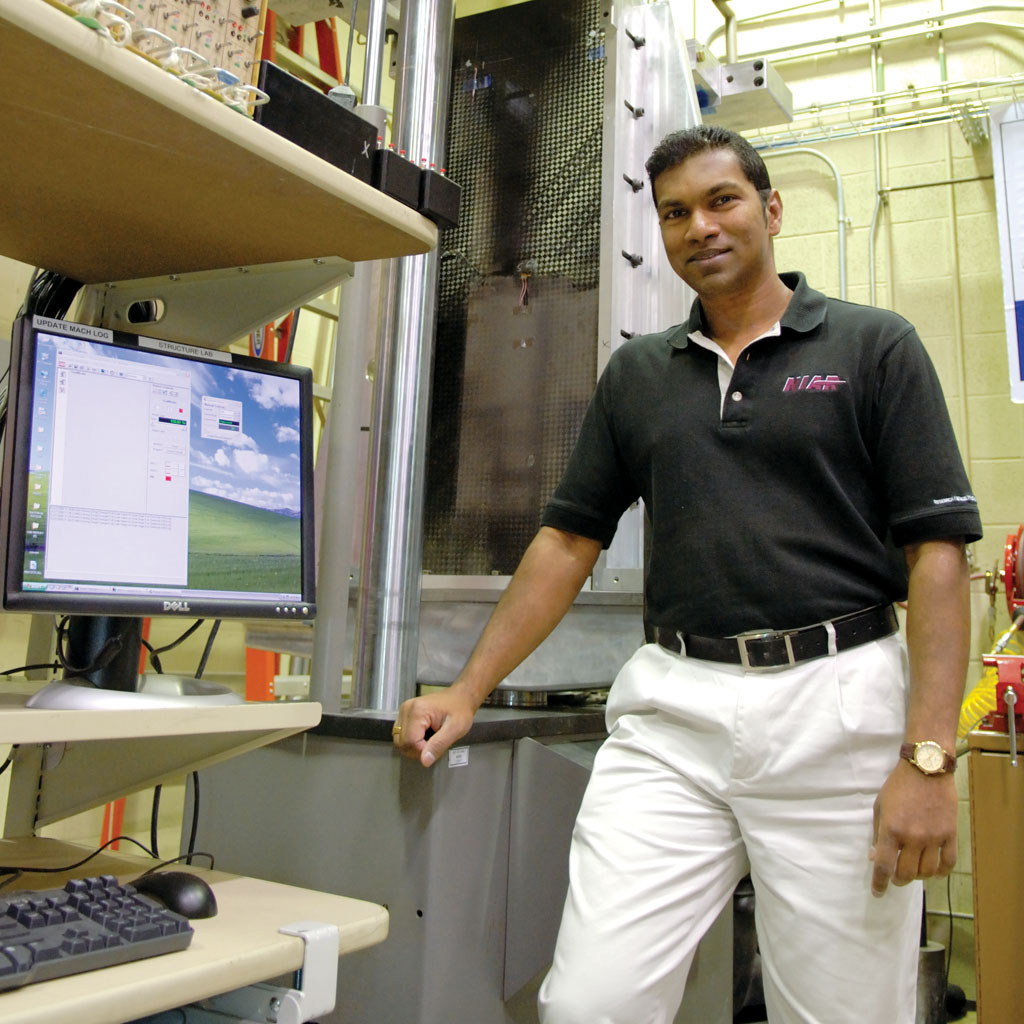
RETO DEL CLIENTE
Desde 1985, el Instituto Nacional de Investigación Aeronáutica (NIAR) de la Universidad Estatal de Wichita ha respondido a las necesidades del sector en materia de investigación, diseño, pruebas y certificación, proporcionando soluciones competitivas e innovadoras que cumplen con altos estándares tecnológicos. NIAR, ubicado en Wichita, Kansas, reúne a la universidad, el gobierno y la industria para promover tecnologías para la aviación y las industrias relacionadas. Las instalaciones de 120.000 pies cuadrados del NIAR albergan 15 laboratorios, con investigación en juntas avanzadas, aerodinámica, envejecimiento de aeronaves, dinámica de choques, materiales compuestos y avanzados, componentes estructurales, realidad virtual, mecánica computacional y muchos más.
El Laboratorio de Estructuras de NIAR proporciona capacidades de investigación y pruebas para artículos de prueba que van desde muestras de materiales hasta estructuras de aeronaves a gran escala. La investigación realizada por el Laboratorio de Estructuras permite a las organizaciones comerciales, de aviación general y militares comprender mejor cómo reducir los costos de fabricación y, al mismo tiempo, aumentar la eficiencia operativa. Los proyectos de investigación relacionados con la tolerancia al daño, los efectos de los defectos y las pruebas de elementos para el diseño y la certificación de aeronaves y vehículos aéreos no tripulados hacen del Laboratorio de estructuras de NIAR una de las instalaciones más concurridas y buscadas de su tipo.
El laboratorio respalda las necesidades de prueba del Centro de Excelencia de Materiales Compuestos y Avanzados (CECAM) de la Administración Federal de Aviación (FAA) y del Centro Nacional de Desempeño de Materiales Avanzados (NCAMP) de la NASA, ambos con sede en NIAR. A través de estas organizaciones, NIAR está desarrollando métodos rentables para calificar material compuesto al compartir bases de datos centrales para la calificación de materiales. En el futuro, utilizando estas bases de datos compartidas, un fabricante podrá seleccionar un sistema de material compuesto aprobado a partir del cual fabricar piezas y realizar un subconjunto más pequeño de pruebas, en comparación con las pruebas de materiales ya realizados por el NCAMP, para una aplicación específica.
"Para que los materiales sean aceptados en nuestras bases de datos compartidas, las materias primas deben fabricarse de acuerdo con las especificaciones de los materiales, que imponen un control riguroso de las propiedades físicas, químicas y mecánicas clave", explica Waruna Seneviratne, director del Laboratorio de Estructuras. "Podemos realizar esta investigación y cumplir con nuestros objetivos de prueba, en gran parte, debido a nuestro uso de equipos avanzados de prueba de materiales de MTS Systems".
SOLUCIÓN DE MTS
El Laboratorio de Estructuras está equipado con una amplia variedad de extensómetros y accesorios de prueba de MTS estándar y personalizados, incluido un extensómetro láser y extensómetros tipo KGR para pruebas de adhesivos. El laboratorio también utiliza cámaras ambientales MTS, lo que le permite realizar pruebas de fatiga estática y de espectro en temperaturas que oscilan entre –200 °F y 2500 °F, así como en ambientes con humedad controlada y niebla salina. Las soluciones de prueba de MTS están equipadas con el avanzado software FlexTest, tecnología de control líder en el sector y capacidades de adquisición de datos multicanal, lo que proporciona al laboratorio la flexibilidad necesaria para realizar prácticamente cualquier investigación de prueba de materiales.
BENEFICIOS DEL CLIENTE
En coordinación con la FAA y el NCAMP, el laboratorio llevó a cabo varios programas importantes de investigación y pruebas durante el año pasado utilizando sus sofisticadas soluciones MTS. Gran parte de la investigación se llevó a cabo para acelerar el desarrollo de estructuras avanzadas de aviones, como el Boeing 787 y el Airbus A380, y contribuirá a impulsar el desarrollo de vehículos aéreos durante la próxima década, a medida que las nuevas tecnologías emergentes se apliquen al diseño y se pongan en producción en toda la industria aeronáutica.
Utilizando equipos MTS, el laboratorio realiza la caracterización de adhesivos y pruebas de elementos de juntas adheridas fatigadas y dañadas. El laboratorio identifica las respuestas características de las estructuras unidas a los defectos de fabricación y reparación del mundo real. La investigación incluye los efectos de los defectos de fabricación, los rayos y los impactos de baja velocidad en la resistencia residual de las uniones adheridas. Este trabajo ayudará a establecer pautas para los controles de procesos y adhesivos para estructuras adheridas.
El equipo también investiga la complejidad asociada con el uso de materiales compuestos avanzados no convencionales en estructuras de aeronaves mediante el análisis de elementos finitos y pruebas de subcomponentes. A partir de sus hallazgos, el laboratorio desarrolló una metodología simplificada para el cálculo de propiedades mecánicas de compuestos trenzados no ortogonales para estructuras cónicas utilizando una base de datos de materiales existente.
“Estamos muy familiarizados con los equipos MTS, ya que el NIAR utiliza la tecnología de la compañía ampliamente a través de sus numerosos laboratorios para realizar investigaciones avanzadas”, dijo Seneviratne. "Aún no encontramos algo que el software y el equipo de MTS no puedan hacer".