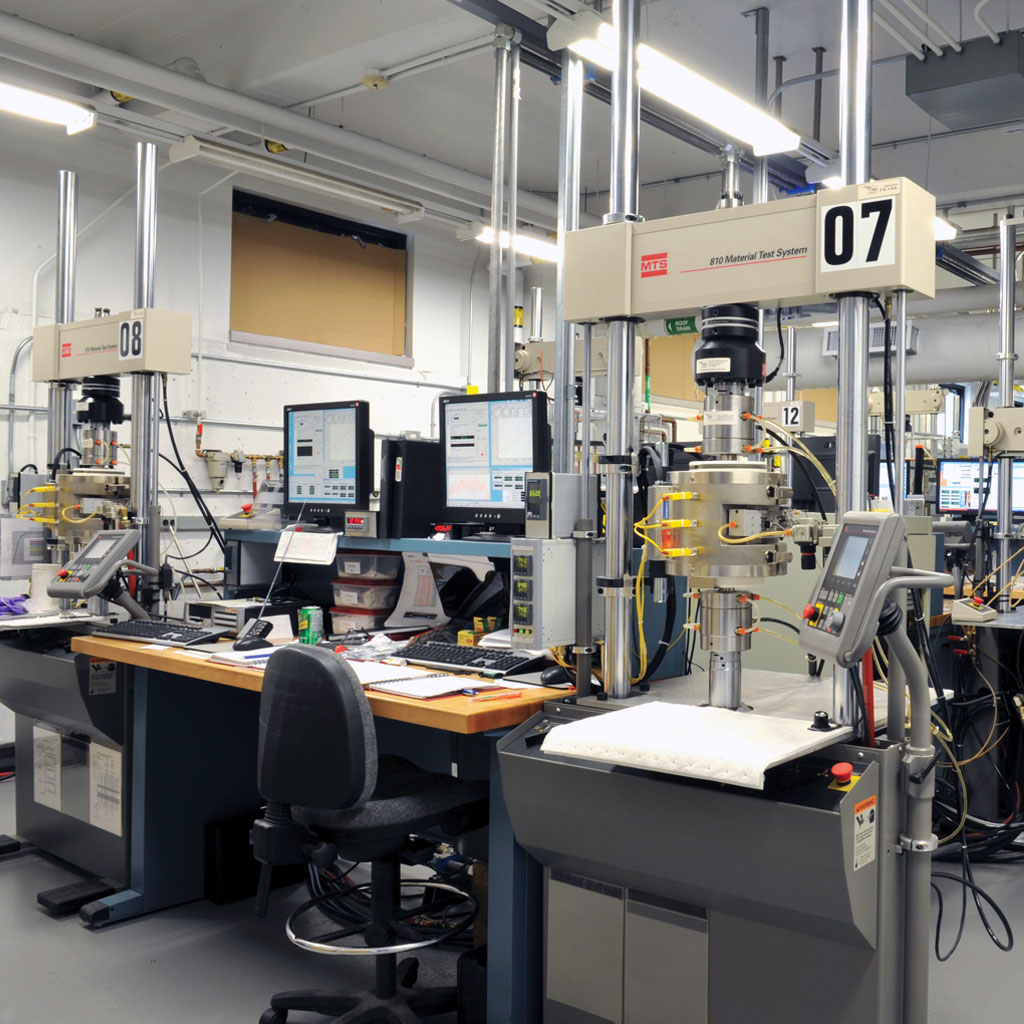
RETO DEL CLIENTE
El desarrollo de materiales de alta temperatura, aquellos que pueden funcionar a temperaturas extremas durante períodos prolongados, está preparando el escenario para la próxima generación de motores a reacción y turbinas de gas que redefinirán las expectativas de eficiencia de combustible. Algunas de las investigaciones más avanzadas en este campo se llevan a cabo en el Laboratorio de Rendimiento de Estructuras y Materiales, que forma parte del Instituto de Investigación Aeroespacial del Consejo Nacional de Investigación de Canadá ubicado en Ottawa, Ontario.
Aquí, el Grupo de Tecnologías de Materiales y Componentes, un equipo de 15 científicos de investigación, se especializa en el diseño, desarrollo y en sayode nuevos materiales para turbinas de gas, incluidas aleaciones de alta temperatura y compuestos de matriz cerámica. El grupo realiza investigaciones internas y también colabora con fabricantes de motores comerciales como Pratt & Whitney, Rolls-Royce y General Electric, y proveedores de materiales como ATI Allvac y Carpenter Technologies. Para determinar exactamente cómo se comportarán los nuevos materiales y cuánto durarán cuando se expongan a temperaturas cada vez más altas, deben realizar una amplia gama de pruebas mecánicos de precisión.
“Hacemos cualquier cosa, desde pruebas de resistencia a la tracción, fluencia y rotura hasta pruebas más especializados, como fatiga por fricción, fatiga termomecánica, crecimiento de grietas por fatiga y tasa de crecimiento de grietas por fluencia”, explica el Dr. Kearsey, director de la Instalación de Mecánica de Fractura y Fatiga a Alta Temperatura del grupo. "Estamos desarrollando los materiales, probándolos y luego desarrollando métodos de prueba estándar para caracterizar estos materiales, lo que incluye averiguar la geometría de la probeta y duplicar el entorno de servicio del motor en el laboratorio".
En este momento, el mayor reto del Dr. Kearsey es simple: el calor. En décadas anteriores, las temperaturas para las pruebas de acero inoxidable, titanio y aleaciones de aluminio eran relativamente moderadas. Las pruebas de los materiales más avanzados de hoy en día requieren temperaturas hasta un 25 % más altas.
“Las temperaturas son tan altas que probar los materiales se convierte en un problema más complejo”, dijo. “¿Cómo se miden materiales a 1000 °C cuando la práctica estándar se basa en equipos clasificados para 800 °C? ¿Cómo se agrega la instrumentación adecuada para medir la tasa de crecimiento de grietas? No es imposible, pero es muy complicado. Tenemos que estar absolutamente seguros de que las temperaturas y las cargas sean 100 % rastreables, porque nuestros resultados se están utilizando para fabricar componentes críticos del motor”.
SOLUCIÓN DE MTS
El grupo de tecnologías de materiales y componentes implementa 18 soluciones MTS diferentes para pruebas de alta temperatura, una línea que incluye todo, desde bastidores de carga MTS 810 heredados hasta sistemas de prueba servohidráulicos MTS Landmark® de última generación.
“La razón por la que solo usamos bastidores de carga MTS es la estabilidad”, indica el Dr. Kearsey. “Cuando tenemos cuatro o cinco fotogramas corriendo uno al lado del otro, el laboratorio está temblando. Los bastidores de MTS son muy estables; no hay torsión o giro que pueda desalinear la muestra".
Completan el equipo de prueba de la instalación dos unidades de potencia hidráulica MTS,controles digitales FlexTest® y el software Multipurpose TestWare®. El laboratorio también utiliza un conjunto completo de accesorios de prueba MTS, como mordazas y accesorios, extensómetros y bandas extensométricas, hornos y unidades de calentamiento por inducción, que deben ser fáciles de combinar e integrar en las configuraciones, a menudo complejas, que requieren las pruebas específicas de alta temperatura.
“El hardware debe funcionar correctamente a diferentes temperaturas y condiciones de prueba", indica el Dr. Kearsey. Nos gusta que podamos tomar un horno MTS y adherirlo a cualquier bastidor de carga. La intercambiabilidad es importante, especialmente para la repetibilidad. Cuando tenemos que hacer 100 pruebas en una geometría similar, no queremos perder tiempo rehaciendo la calibración para cada una".
BENEFICIOS PARA EL CLIENTE
Para el Dr. Kearsey, nada es más importante que la confiabilidad del hardware y del software de prueba. La fiabilidad es fundamental para la precisión de los resultados, la productividad del laboratorio y la satisfacción de los clientes externos.
“Compramos equipo MTS porque casi nunca falla”, comenta. “No tiene que ser reemplazado. Es confiable y rastreable. Como laboratorio de investigación, la trazabilidad es un requisito clave. Si hacemos una alineación en un sistema, tenemos que estar seguros de que eso es exactamente lo que sucede en el siguiente prueba. No importa si estamos probando una aleación de monocristal avanzada o evaluando aleaciones de 50 años para el modelo de predicción de vida. Con los sistemas de prueba MTS, podemos generar los datos necesarios para tomar decisiones confiables".
La confiabilidad de los extensómetros es particularmente crítica en las pruebas de materiales a alta temperatura, especialmente a frecuencias de hasta 10 Hz o con materiales más rígidos donde las reflexiones medidas son más pequeñas. El Dr. Kearsey también cita la confiabilidad del software como un factor importante.
"Por ejemplo, cuando se realiza una prueba de fatiga termomecánica, las pruebas pueden durar tres meses", afirma. “Es muy costoso para nuestros clientes. Nunca querrá decirles que el software se bloqueó durante la prueba y que sus resultados no son válidos. El software MTS es fundamental en este sentido porque no nos da ese dolor de cabeza. Es muy confiable y muchos de los módulos están preprogramados para fatiga de ciclo bajo, fatiga termomecánica y otros tipos de pruebas".
Incluso ahora, mientras el Dr. Kearsey trabaja para superar los retos asociados con las pruebas a 1000 °C, espera que el límite superior aumente. De hecho, está trabajando con MTS para diseñar sistemas de prueba que puedan funcionar a estas temperaturas mucho más altas.
"A medida que las aleaciones más nuevas se reemplacen con compuestos de matriz cerámica, necesitaremos realizar pruebas de hasta 1300 °C o 1400 °C”, indica. “Ya estamos conversando cómo hacer que esto suceda con MTS. ¿Qué tamaño de horno necesitaremos? ¿Cuál será la zona caliente? ¿Qué extensometría necesitaremos? Parece que MTS siempre llega a nosotros en el momento adecuado. Ese tipo de apoyo es la razón por la que seguimos volviendo a MTS".