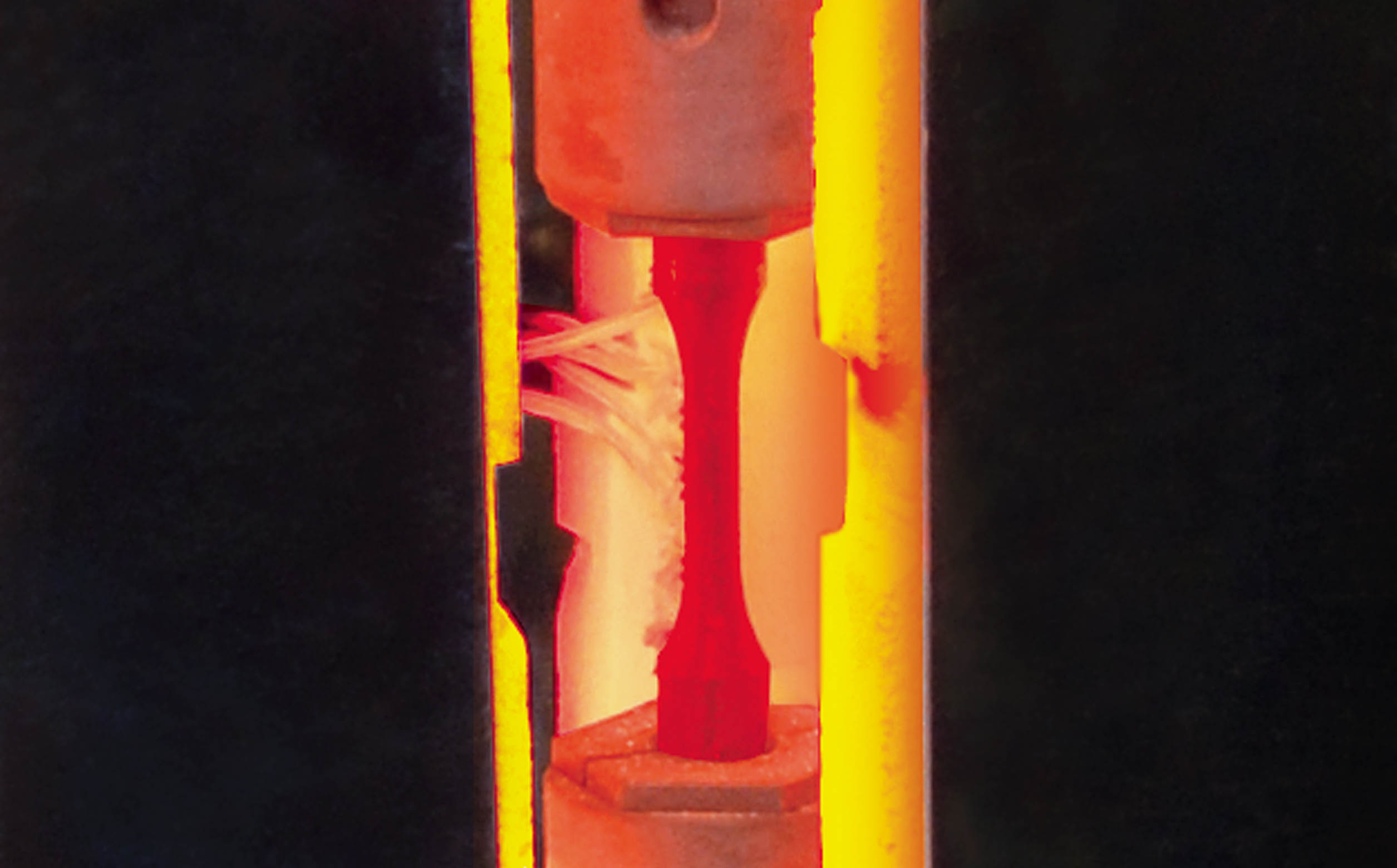
Con el respaldo de un doctorado en metalurgia mecánica y varias décadas de experiencia en pruebas de alta temperatura, el ingeniero y científico de planta de I+D de MTS, Erik Schwarzkopf, analiza los retos de mantener un control preciso de las temperaturas de prueba.
P: ¿Por qué es tan importante la temperatura en las pruebas de materiales, en particular en las pruebas isotérmicas de LCF o HCF?
R: Los ingenieros necesitan comprender cómo cambian las propiedades de los materiales a diferentes temperaturas con el fin de diseñar productos y componentes con un rendimiento confiable a las temperaturas que tienen lugar en los entornos reales de funcionamiento. Las pruebas de fatiga de ciclo bajo (LCF) y fatiga de ciclo alto (HCF) duran muchas horas, por lo cual la estabilidad de la temperatura es crucial. A lo largo de la prueba, una desviación de cinco o diez grados puede añadir una incertidumbre significativa en los resultados.
P: ¿Cómo se mide la temperatura en una configuración de prueba típica?
R: El método más común es un termopar con dos conductores metálicos (cables). El flujo de la corriente en la unión de los cables es proporcional a la temperatura en la unión. Los cables se suelen fijar a la probeta para que la temperatura en la unión sea la misma que la temperatura de la probeta. Para las pruebas a alta temperatura, los investigadores utilizan termopares de tipo R con cables de platino y rodio, a pesar de que los termopares de tipo K con cables de cromel y alumel son una opción menos costosa. Las aplicaciones a temperaturas más bajas y de alta sensibilidad requieren termopares tipo J de hierro y constantán.
P: ¿Cómo se controla la temperatura durante una prueba?
R: La salida de un controlador de proporcional-integral-derivado (PID) se puede utilizar para energizar un sistema de calentamiento que rodea la probeta. Dentro de la cámara o el horno, se puede usar uno o más controladores para manejar diferentes zonas del espacio interior. La idea es controlar la temperatura para que la temperatura en la probeta se mantenga uniforme, incluso si hay espacios de temperatura variable en otras partes.
P: ¿La temperatura realmente es tan distinta en todo el horno?
R: Sí. Si el controlador de temperatura envía las mismas instrucciones a los tres elementos de calentamiento en el horno, el gradiente en la probeta será lo suficientemente amplio como para poner en cuestionamiento los resultados de la prueba. Esto, claro está, es inaceptable. También es innecesario. Es posible controlar la temperatura con eficacia, pero se deben comprender los mecanismos termodinámicos en juego. Los gradientes ocurren porque el tren de carga se extiende por fuera del horno hacia la celda de carga y el actuador, que están a temperatura ambiente. El calor en el horno se transfiere a esas zonas a temperatura ambiente por conducción mientras que los elementos de calentamiento siguen agregando calor, pero estas acciones no ocurren a la misma velocidad. Cuando hay múltiples zonas para controlar, creamos “amortiguadores” que alejan los gradientes más altos de la longitud del calibre de la probeta y hacia los fustes o incluso las varillas de empuje. De esta manera, el gradiente en la sección reducida de la probeta será aceptablemente bajo.
P: ¿Qué tan bajo debería ser el gradiente en la probeta?
R: Depende de la norma. Las diferentes especificaciones de prueba nacionales e internacionales para LCF y HCF no llegan a un acuerdo con respecto a los gradientes. Por lo general, el gradiente máximo en la longitud del calibre es un pequeño porcentaje de la temperatura nominal de la prueba. En consecuencia, si la temperatura nominal de la prueba es 500 °C, la sección reducida debería tener un gradiente de no más de 5 °C a 10 °C, o el uno o dos por ciento. En un sistema de pruebas bien diseñado, el gradiente en la sección reducida se puede mantener dentro del 1 % de la temperatura deseada. El horno de tres zonas de MTS modelo 653.04, por ejemplo, puede mantener el gradiente a ±2 °C a lo largo de una longitud del calibre de 25 mm a una temperatura nominal de prueba de 800 °C, lo cual se encuentra dentro de las especificaciones ASTM e ISO.
P: ¿Cuánto tarda en alcanzar la temperatura de prueba deseada?
R: Puede tardar una hora en subir, sumergir la probeta y alcanzar el equilibrio en la probeta y el tren de carga. Si se sube demasiado rápido, se puede sobrepasar y dañar la probeta, o agregar un tiempo mayor para el enfriamiento y recalentamiento. Muchos laboratorios han intentado minimizar el tiempo de subida a lo largo de los años, porque puede afectar la productividad. Para algunas pruebas de tensión, se pueden precalentar las probetas y los trenes de carga en hornos de repuesto y luego instalarlos en el sistema de pruebas cuando sea oportuno. Otros laboratorios han experimentado con las tasas variables de calentamiento en cada zona del horno, lo cual puede ayudar a reducir los tiempos de inmersión. Las plantillas de LCF y HCF a alta temperatura para el software TestSuite™ MP Elite de MTS, por ejemplo, utilizan perfiles complejos para elevar rápidamente la temperatura de las zonas exteriores, y luego elevar cuidadosamente la zona interna que contiene la probeta. Sin embargo, en muchos casos la especificación de la prueba dicta el tiempo de inmersión.
P: ¿El horno más grande y mejor es siempre la opción correcta?
R: Depende de lo que se entienda por “más grande” y “mejor”. Un horno puede tener una temperatura máxima mayor, más aislamiento, un interior más grande, zonas de calentamiento más grandes o más zonas de control. Lo que debemos preguntarnos es: ¿cuáles son los resultados? Más zonas de control ofrecen gradientes más bajos en la probeta, pero son más costosas. Las zonas de calentamiento más grandes también reducen los gradientes, pero requieren varillas de empuje de alta temperatura. Más aislamiento ofrece estabilidad, pero dificulta la recuperación después de un rebasamiento. El uso de un horno de 1000 °C para una prueba a 150 °C pondrá en riesgo el control de la temperatura. Y la lista sigue.
P: ¿Qué más es importante tener en cuenta para un control preciso de la temperatura?
R: Antes de elegir accesorios, como un horno o mordazas, se debe pensar en la aplicación en su totalidad: temperatura deseada de prueba, geometría de la probeta, gradiente y tiempo de prueba. También se debe pensar en el modo en que se calentará una probeta y se manejará la temperatura durante la prueba. El método más común en una prueba isotérmica es el uso de un horno de resistencia con termopares en contacto con la probeta. Los termopares se sueldan por puntos a los fustes de la probeta, no en la sección reducida, porque pueden provocar grietas. Lo más importante es que los investigadores deberían aprovechar por completo los conocimientos existentes para las pruebas a alta temperatura. Hace no mucho tiempo, el enfoque normal era el de prueba y error. Hoy se puede elegir un camino más astuto y obtener resultados más precisos.