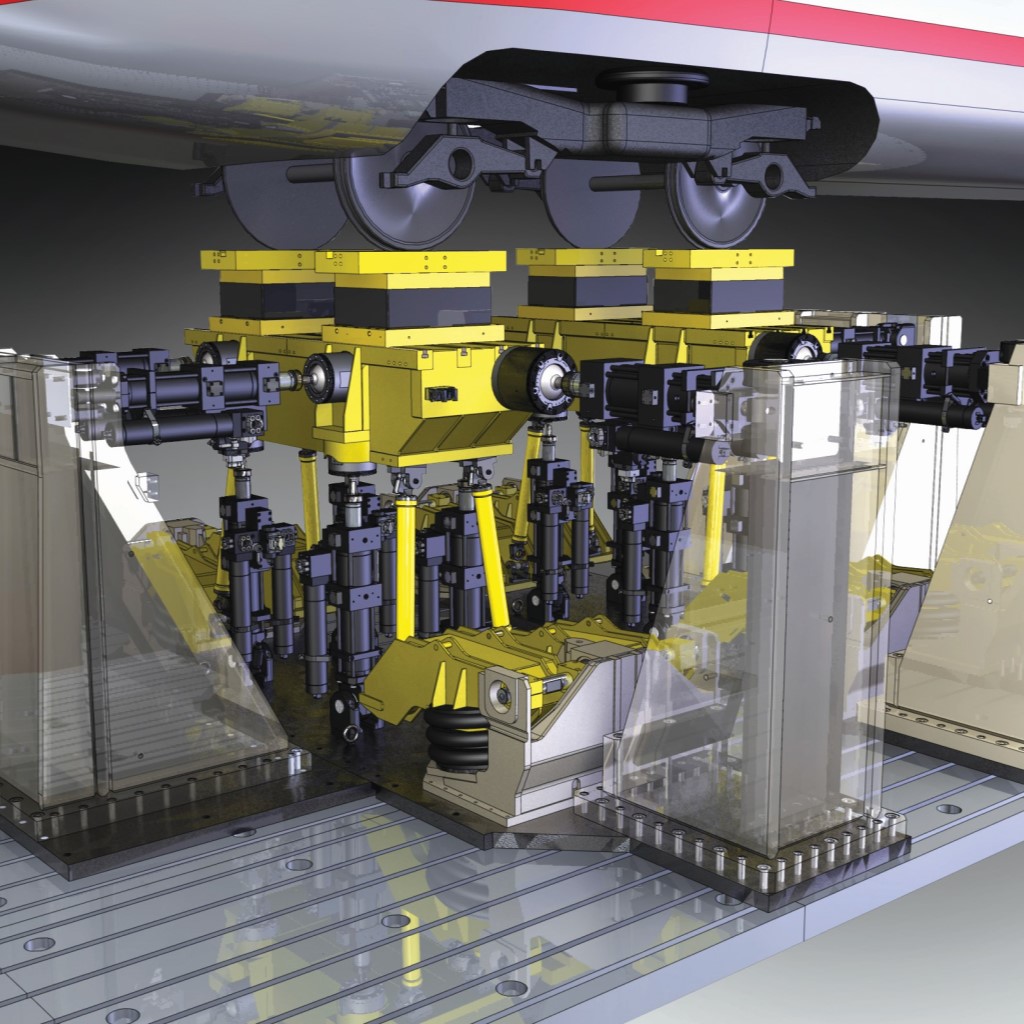
El crecimiento global de los viajes en tren está aumentando la demanda de nuevos vagones de pasajeros, lo cual es una buena noticia para los fabricantes de todo el mundo. Al mismo tiempo, estos nuevos vehículos deben responder a expectativas más altas. Los vagones de pasajeros modernos deben viajar a mayor velocidad, ofrecer un viaje cómodo, maximizar la eficiencia energética y, por supuesto, cumplir plenamente la normativa.
Satisfacer estas necesidades al mismo tiempo presenta un difícil conjunto de retos de diseño. La eficiencia depende de la eliminación del peso, pero esto no puede afectar la estabilidad. La estabilidad se hace más difícil a altas velocidades, y los vagones más rápidos del mundo llegan a circular a 350 kilómetros por hora. La comodidad de conducción también es más difícil de conseguir a altas velocidades.
Como estos factores están relacionados, los fabricantes deben ser capaces de optimizar los nuevos diseños para administrar las compensaciones efectivas Por ejemplo, un bogie más rígido puede ofrecer más estabilidad pero menos comodidad para el conductor. La rigidez de la barra antivuelco puede modificarse para mejorar la maniobrabilidad o la comodidad de los pasajeros, pero no ambas cosas a la vez.
Los equipos de desarrollo de productos están sometidos a una intensa presión de tiempo debido a la alta demanda del mercado y los diseñadores deben trabajar con rapidez. Aquí es donde las pruebas mecánicas se vuelven muy útiles.
RETOS EN EL LABORATORIO
En el laboratorio de pruebas, los diseñadores de componentes pueden estudiar muchas iteraciones de un nuevo diseño con relativa rapidez, de una manera altamente controlada y repetible. Los resultados de las pruebas revelan coeficientes y otros factores que pueden retroalimentarse en modelos virtuales de componentes y subsistemas para hacerlos más precisos. Esto ayuda a acelerar el proceso de análisis y de mejora de nuevos diseños.
El laboratorio plantea sus propios retos. La lista de pruebas pertinentes es larga y cada una de ellas suele requerir un tipo diferente de sistema de pruebas con una configuración única. Adquirir los sistemas necesarios para optimizar los nuevos diseños de bogies puede resultar caro. La configuración y la ejecución de las pruebas pueden resultar ineficaces cuando se utilizan varios sistemas.
El mayor desafío de todos es la necesidad de probar todo el mecanismo, no solo un componente. Esto puede parecer contrario a la lógica pero los ingenieros de diseño avanzado entienden que las pruebas de piezas individuales no proporcionan la misma precisión o conocimiento que las pruebas de un bogie completo.
Aunque las pruebas de componentes discretos son más fáciles de administrar y pueden realizarse con rapidez, no proporcionan la misma precisión que las pruebas de todos los componentes como sistema. Las interacciones de los componentes producen comportamientos inesperados debido a la fricción y al movimiento fuera del eje. Estas interacciones no se pueden replicar evaluando cada componente por separado. Los ingenieros han sospechado durante mucho tiempo que este era el caso, pero solo en la última década se ha vuelto obvio. Los modelos virtuales son cada vez más sofisticados, pero los ingenieros no han podido predecir con exactitud el rendimiento del sistema en el carril basándose en las características de los componentes individuales.
Recientemente, se ha puesto en servicio un innovador sistema de prueba de vagones ferroviarios que se puede utilizar para medir la cinemática y la conformidad de un mecanismo de bogie completo. El sistema, suministrado por MTS Systems Corp., también se puede utilizar para proporcionar caracterización, durabilidad básica y pruebas de vibración, todo en un solo sistema.
PRUEBAS DE SUSPENSIÓN PRIMARIA Y SECUNDARIA
Actualmente instalado en un fabricante de vagones de pasajeros de alta velocidad en Asia, el nuevo sistema de medición de bogies proporciona el tamaño y la fuerza necesarios para cargar un bogie completo y un vagón de ferrocarril completo. El sistema de prueba incorpora una considerable instrumentación diseñada para mediciones extremadamente precisas de estos mecanismos complejos.
La complejidad proviene de las muchas formas en que se pueden distorsionar los datos de prueba. Para garantizar resultados precisos, los sistemas de prueba deben poder prevenir (o compensar) todos los siguientes fenómenos: cambio de fase causado por latigazo o amortiguación; distorsión de la señal y ruido causado por resonancias del sistema y de la muestra; y errores de medición de fuerza que surgen de diafonía, compensación de temperatura de los transductores, expansión y contracción térmica de accesorios y probetas, errores de calibración, deslizamiento, desviación o daño a los transductores, montajes, cables o acondicionadores. En muchos casos, se combinan varias señales para calcular el resultado deseado, lo que agrava el error total.
Algunas de las pruebas más importantes que realiza el sistema son las de la suspensión primaria, que incluye todos los componentes entre el bogie y el eje (muelle, muelle helicoidal, barra de torsión, galleta de goma, etc.). Si bien la suspensión primaria afecta la dirección, el manejo y, hasta cierto punto, la comodidad del conductor, los ingenieros deben comprender el sistema completo de montaje y suspensión del juego de ruedas con gran detalle para optimizar los nuevos diseños. La rigidez de la suspensión primaria está en el mismo rango que la rigidez del bastidor del bogie, y la interacción entre las dos determina la respuesta general de manejo del bogie. Por esta razón, el nuevo sistema de prueba está diseñado exclusivamente para medir las contribuciones de los componentes individuales o las características del ensamblaje completo como un sistema integrado.
La prueba de rigidez de la suspensión primaria consiste en fijar la suspensión secundaria, montar transformadores diferenciales variables lineales (LVDT) en los puntos de respuesta del alojamiento del cojinete del eje y del bogie, y aplicar una fuerza o un desplazamiento programado en cada uno de los grados de libertad (DOF) deseados. Para lograr un resultado útil, los ingenieros deben garantizar la precisión y resolución de las celdas de carga y los LVDT, mantener una temperatura constante en el laboratorio y tomar medidas a diferentes velocidades para evaluar las características de amortiguación. Es importante medir la rigidez del bogie en cada dirección, no solo en la vertical, porque la estabilidad es una función de los desplazamientos multiaxiales combinados, no solo de la vertical. Por ejemplo, durante las curvas el bogie se tuerce (se deforma en el eje de guiñada) y la rigidez de la deformación es fundamental para una dirección estable.
Esta misma configuración se puede utilizar para realizar una prueba de amortiguación de la suspensión primaria y evaluar la amortiguación en relación con la rigidez del resorte. Los datos de las pruebas de la suspensión primaria son muy útiles para alimentar los modelos virtuales del bogie, tanto para la generación de modelos como para su validación.
Otro conjunto importante de pruebas son las que se realizan en la suspensión secundaria, que se encuentra entre la parte superior del bogie y la parte inferior del vagón. Para estas pruebas, la suspensión primaria es fija y la suspensión secundaria, generalmente un par de bolsas de aire, se monta en celdas de carga multiaxiales. Un accesorio de vagón de ferrocarril simulado se limita en 3DOF y se controla en el 3DOF restante para presentar la suspensión secundaria con las mismas cargas y deformaciones que ve en servicio. Esto permite evaluar las características de rigidez y amortiguación. Debido a la forma inclinada del “sombrero” de la bolsa de aire, predecir la rigidez lateral y de balanceo es particularmente desafiante. El material elastomérico se deforma de forma imprevisible, y estos movimientos afectan en gran medida al confort de la conducción.
PRUEBAS DE RENDIMIENTO ADICIONALES
Otro tipo de prueba que puede realizar este sistema es la medición del par de resistencia de la dirección, en la que el bogie gira bajo el vagón simulado y se mide su rigidez. Para realizar esta prueba, se aplican cargas o desplazamientos laterales iguales y opuestos a cada eje. Las fuerzas de tensión/compresión y longitudinales se ponen a cero y se ordena a los actuadores verticales que mantengan la fuerza deseada o el movimiento plano fijo en las ruedas.
Además, el sistema de prueba se puede configurar para probar el coeficiente de suspensión para vías rectas o curvas. En esta prueba, la probeta es un vagón de ferrocarril completo (o simulado) con giroscopios de medición de ángulos en las mesas, los bogies y la carrocería. La prueba consiste en elevar las ruedas de un lado del bogie a la superelevación deseada y medir el ángulo del bogie y del automóvil en relación con el ángulo de la mesa. Estas relaciones pueden ser difíciles de predecir debido a los numerosos elementos de la suspensión completa. Los fabricantes pueden utilizar una prueba similar para conocer el coeficiente de vuelco, que es vital para garantizar la comodidad y la seguridad de la conducción.
También se pueden evaluar vagones completos. Si los ingenieros quieren comprender la respuesta dinámica para las pruebas de coeficientes, el sistema puede controlarse con ruido en forma de banda ancha o formas de onda específicas, como una onda sinusoidal. La respuesta de la carrocería del vagón se mide y su frecuencia natural puede estimarse a partir de los datos resultantes utilizando un software de pruebas.
Otras pruebas que el sistema puede realizar incluyen la ubicación del centro de gravedad, la prueba de momento de inercia y la reproducción en tiempo real de los datos operativos en el carril.
Si bien es cierto que un sistema de pruebas de rendimiento polivalente representa una importante inversión de capital para el laboratorio, proporciona un retorno de la inversión igualmente importante gracias a su capacidad para acelerar el calendario de pruebas, reducir los costos y mejorar la precisión de los datos de las pruebas y la caracterización de las probetas. En última instancia, estas capacidades permitirán a los fabricantes de vagones y bogies mejorar la precisión de los modelos, lograr innovaciones más rápido, fabricar vehículos de mayor calidad y generar una ventaja competitiva duradera.
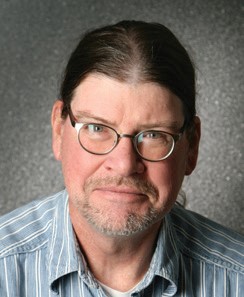