Model 329 Spindle-Coupled Road Simulators
Apply force and motion in six degrees of freedom through vehicle spindles to replicate the effects of real-world road loads on vehicle and subsystem durability. The latest iteration of this industry standard test system, the new Model 329i, combines a refined kinematic design, versatile FlexTest controls and renowned RPC software to achieve new levels of test productivity and accuracy.
Applications
- Durability
Test Specimens
- Passenger Cars and SUVs
- Light Trucks
- Heavy Trucks
- Motorcycles
- All-Terrain Vehicles
Key Product Features
Accurate / Repeatable Results
Refined kinematic design supports higher dynamic inputs (up to 80 Hz) and delivers superior closed loop control with minimal latency (0.35 ms)
Integrated / Synchronized
FlexTest digital controls enable reliable and seamless connectivity between the test rig and the specimen, including specimens with active systems
Accelerated Testing
Combining the test rig with market-leading RPC software allows engineers to replicate real damage from road events up to 10x faster than on the proving ground
Unmatched Expertise
Global experts on road simulation support users to design tests and methods, including implementation of MTS’ ground-breaking HSRC technology that reduces reliance on traditional RLDA
Model Comparison
Full Vehicle (4-corner)
- Test full vehicles
- Used for body and chassis applications and final design validation
- 6DOF forces generated from the inertia of the vehicle reacting to the motion of the system
- Wide range of payload and performance options
Axle/Steer (2-corner)
- Test front or rear axle assemblies
- Used for axle applications and early design qualification
- 6DOF forcesgenerated from the motion of the system against a reaction base
- Wide range of payload and performance options
Suspension/Steer (1-corner)
- Test single vehicle corner assemblies
- Used for for suspension development and early design qualification
- 6DOF forces generated from the motion of the system against a reaction base
Custom Variants
- Heavy Truck
- Long Stroke
- Steer
- Motorcycle/ATV
Technical Overview
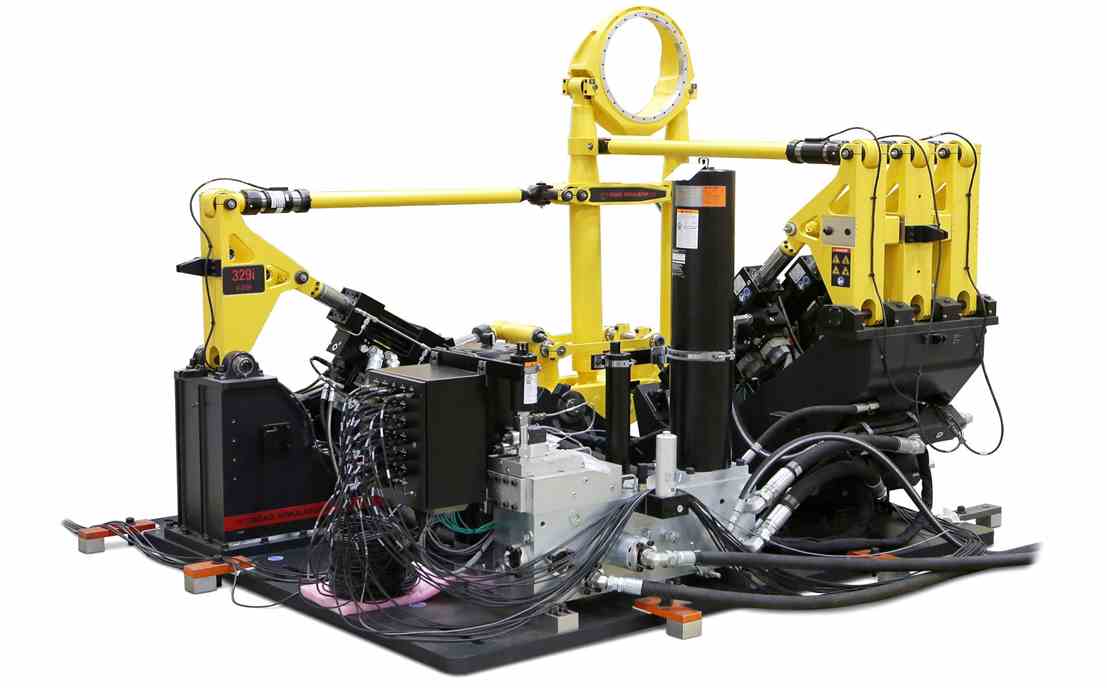
The new Model 329i Spindle-couple Road Simulator integrates a diverse array of MTS mechanical, controls and software innovations to meet evolving requirements for connectivity, accuracy, productivity and efficiency.
- Integrate seamlessly with active vehicle systems and CAE models
- FlexTest Elite Performance Controllers
- Digital interfaces via EtherCAT, CANbus and more
- Real-time and iterative MTS Hybrid Simulation
- Achieve optimal test accuracy
- Refined, patented kinematic design
- Up to 80 Hz road input
- Superior closed loop control with minimal latency
- Next-generation RPC Connect Software
- Maximize test system reliability and operational efficiency
- MTS DuraGlide Actuators
- Stronger, updated wrist joint design
- MTS Echo Intelligent Lab health and performance monitoring
- Unrivaled Global Service & Support
- Expert systems integration and test consulting
- Remanufacture/Upgrade programs
- Available configurations
- Passenger Car, Light Truck
329i 6DOF Passenger Car (PC)
Vertical |
Longitudinal |
Lateral |
Steer |
Brake/Drive |
Camber |
|
Max. Operating Frequency |
80 Hz |
80 Hz |
80 Hz |
80 Hz |
80 Hz |
80 Hz |
Spindle Force/Moment |
63 kN |
22 kN |
20 kN |
6.9 kN-m |
4.0 kN-m |
9.6 kN-m |
(14,100 lbf) |
(4,950 lbf) |
(4,500 lbf) |
(61,000 in-lbf) |
(35,400 in-lbf) |
(85,000 in-lbf) |
|
Spindle Displacement |
± 190 mm |
± 196 mm |
± 129 mm |
± 8 deg |
± 17 deg |
± 8 deg |
(± 7.5 in) |
(± 7.7 in) |
(± 5.1 in) |
- |
- |
- |
|
Spindle Velocity |
7 m/sec |
2.2 m/sec |
2.4 m/sec |
750 deg/sec |
700 deg/sec |
400 deg/sec |
(276 in/sec) |
(86 in/sec) |
(94 in/sec) |
- |
- |
- |
- Total maximum recommended vehicle mass 3000 kg (6,600 lb).
- All performance estimates are subject to change.
- Dynamic specification is based on single axis only, sinusoidal input, non-continuous events.
- Performance values are nominal at mid position – not simultaneous, nor corrected for linkage.
- Maximum brake clearance diameter is 450 mm for above performance predictions.
- All displacements are expressed in terms of double amplitude values.
- Typical required oil-flow for random loading is approximately 284 lpm (75 gpm) per corner. This rating is highly dependent on actual operating conditions and should be discussed further with an MTS Application Engineer.
329i 6DOF Light Truck (LT)
Vertical |
Longitudinal |
Lateral |
Steer |
Brake/Drive |
Camber |
|
Max. Operating Frequency |
80 Hz |
80 Hz |
80 Hz |
80 Hz |
80 Hz |
80 Hz |
Spindle Force/Moment |
77 kN |
29.5 kN |
33.5 kN |
6.9 kN-m |
6.2 kN-m |
14.1 kN-m |
(17,300 lbf) |
(6,600 lbf) |
(7,500 lbf) |
(61,000 in-lbf) |
(54,800 in-lbf) |
(125,000 in-lbf) |
|
Spindle Displacement |
± 190 mm |
± 196 mm |
± 129 mm |
± 8 deg |
± 17 deg |
± 8 deg |
(± 7.5 in) |
(± 7.7 in) |
(± 5.1 in) |
- |
- |
- |
|
Spindle Velocity |
5.0 m/sec |
3.0 m/sec |
2.6 m/sec |
750 deg/sec |
450 deg/sec |
450 deg/sec |
(197 in/sec) |
(118 in/sec) |
(102 in/sec) |
- |
- |
- |
- Total maximum recommended vehicle mass 6000 kg (13,200 lb).
- All performance estimates are subject to change.
- Dynamic specification is based on single axis only, sinusoidal input, non-continuous events.
- Performance values are nominal at mid position – not simultaneous, nor corrected for linkage.
- Maximum brake clearance diameter is 450 mm for above performance predictions.
- Minimum required oil-flow for random loading is approximately 386 lpm (102 gpm) per corner. This rating is highly dependent on actual operating conditions and should be discussed further with an MTS Application Engineer.
- Optional static support can provide up to 23 kN (5000 lbf) of additional vertical upforce per corner to offset vehicle weight.
329 6DOF Passenger Car (PC)
Vertical |
Longitudinal |
Lateral |
Steer |
Brake/Drive |
Camber |
|
Max. Operating Frequency |
50 Hz |
50 Hz |
50 Hz |
50 Hz |
50 Hz |
50 Hz |
Spindle Force/Moment |
63 kN |
22 kN |
20 kN |
6.9 kN-m |
4.0 kN-m |
9.6 kN-m |
(14,100 lbf) |
(4,950 lbf) |
(4,500 lbf) |
(61,000 in-lbf) |
(35,400 in-lbf) |
(85,000 in-lbf) |
|
Spindle Displacement |
± 190 mm |
± 196 mm |
± 129 mm |
± 8 deg |
± 16 deg |
± 8 deg |
(± 7.5 in) |
(± 7.7 in) |
(± 5.1 in) |
- |
- |
- |
|
Spindle Velocity |
7 m/sec |
2.2 m/sec |
2.4 m/sec |
700 deg/sec |
700 deg/sec |
400 deg/sec |
(276 in/sec) |
(86 in/sec) |
(94 in/sec) |
- |
- |
- |
- Total maximum recommended vehicle mass 3000 kg (6,600 lb).
- All performance estimates are subject to change.
- Dynamic specification is based on single axis only, sinusoidal input, non-continuous events.
- Performance values are nominal at mid position – not simultaneous, nor corrected for linkage.
- Maximum brake clearance diameter is 430 mm for above performance predictions.
- Typical required oil-flow for random loading is approximately 284 lpm (75 gpm) per corner. This rating is highly dependent on actual operating conditions and should be discussed further with an MTS application engineer.
329 6DOF Light Truck (LT)
Vertical |
Longitudinal |
Lateral |
Steer |
Brake/Drive |
Camber |
|
Max. Operating Frequency |
50 Hz |
50 Hz |
50 Hz |
50 Hz |
50 Hz |
50 Hz |
Spindle Force/Moment |
77 kN |
29.5 kN |
33.5 kN |
6.9 kN-m |
6.2 kN-m |
11.3 kN-m |
(17,300 lbf) |
(6,600 lbf) |
(7,500 lbf) |
(61,000 in-lbf) |
(54,800 in-lbf) |
(100,000 in-lbf) |
|
Spindle Displacement |
± 190 mm |
± 196 mm |
± 129 mm |
± 8 deg |
± 17 deg |
± 8 deg |
(± 7.5 in) |
(± 7.7 in) |
(± 5.1 in) |
- |
- |
- |
|
Spindle Velocity |
5.0 m/sec |
3.0 m/sec |
2.6 m/sec |
750 deg/sec |
450 deg/sec |
450 deg/sec |
(197 in/sec) |
(118 in/sec) |
(102 in/sec) |
- |
- |
- |
- Total maximum recommended vehicle mass 6000 kg (13,200 lb).
- All performance estimates are subject to change.
- Dynamic specification is based on single axis only, sinusoidal input, non-continuous events.
- Performance values are nominal at mid position – not simultaneous, nor corrected for linkage.
- Maximum brake clearance diameter is 430 mm for above performance predictions.
- Typical required oil-flow for random loading is approximately 386 lpm (102 gpm) per corner. This rating is highly dependent on actual operating conditions and should be discussed further with an MTS application engineer.
- Optional static support is capable of providing up to 23 kN (5,000 lbf) of additional vertical upforce per corner to offset vehicle weight.
329 6DOF Medium Steer (MS)
Vertical |
Longitudinal |
Lateral |
Steer |
Brake/Drive |
Camber |
|
Max. Operating Frequency |
50 Hz |
50 Hz |
50 Hz |
50 Hz |
50 Hz |
50 Hz |
Spindle Force/Moment |
77 kN |
25.8 kN |
33.2 kN |
8.3 kN-m |
6.0 kN-m |
7.2 kN-m |
(17,300 lbf) |
(5,800 lbf) |
(7,450 lbf) |
(73,400 in-lbf) |
(53,000 in-lbf) |
(63,700 in-lbf) |
|
Spindle Displacement |
300 mm |
200 mm |
200 mm |
50 deg |
30 deg |
20 deg |
(11.8 in) |
(7.8 in) |
(7.8 in) |
- |
- |
- |
|
Spindle Velocity |
6.1 m/sec |
2.2 m/sec |
2.5 m/sec |
700 deg/sec |
880 deg/sec |
700 deg/sec |
(240 in/sec) |
(85 in/sec) |
(100 in/sec) |
- |
- |
- |
- Total maximum recommended vehicle mass 6000 kg (13,200 lb).
- All performance estimates are subject to change.
- Dynamic specification is based on single axis only, sinusoidal input, non-continuous events.
- Performance values are nominal at mid position – not simultaneous, nor corrected for linkage.
- Maximum brake clearance diameter is 420 mm.
- Typical required oil-flow for random loading is approximately 386 lpm (102 gpm) per corner. This rating is highly dependent on actual operating conditions and should be discussed further with an MTS application engineer.
Optional Features |
Passenger Car |
Light Truck |
Heavy Truck |
Steer |
Custom |
Longitudinal body restraint fixture |
x |
x |
|
|
x |
Torque input fixture |
x |
x |
|
|
x |
Specimen installation and removal (manual or powered) |
x |
x |
|
x |
x |
Yaw /Twist fixture |
x |
x |
|
|
x |
Dynamic brake intensifier |
x |
x |
|
x |
x |
Shock cooling |
x |
x |
x |
x |
x |
DAFA reaction fixture (axle testing) |
x |
x |
|
x |
x |
Vertical static support |
x |
x |
x |
|
x |
X-Y positioning (manual, semi- and fully automated) |
x |
x |
|
x |
x |
Wide range of spindle housing sizes |
x |
x |
|
x |
x |
Wide range of wheel force transducers |
x |
x |
x |
x |
x |
Steer input |
x |
x |
|
x |
x |
Vehicle lift |
x |
x |
x |
x |
x |
Wide range of hydraulic power units |
x |
x |
x |
x |
x |
Multi-Pump Control Manager |
x |
x |
x |
x |
x |
Hydraulic distribution system design and implementation |
x |
x |
x |
x |
x |
On-site service and engineering consulting |
x |
x |
x |
x |
x |
Equipment health monitoring |
x |
x |
x |
x |
x |
Factory training |
x |
x |
x |
x |
x |
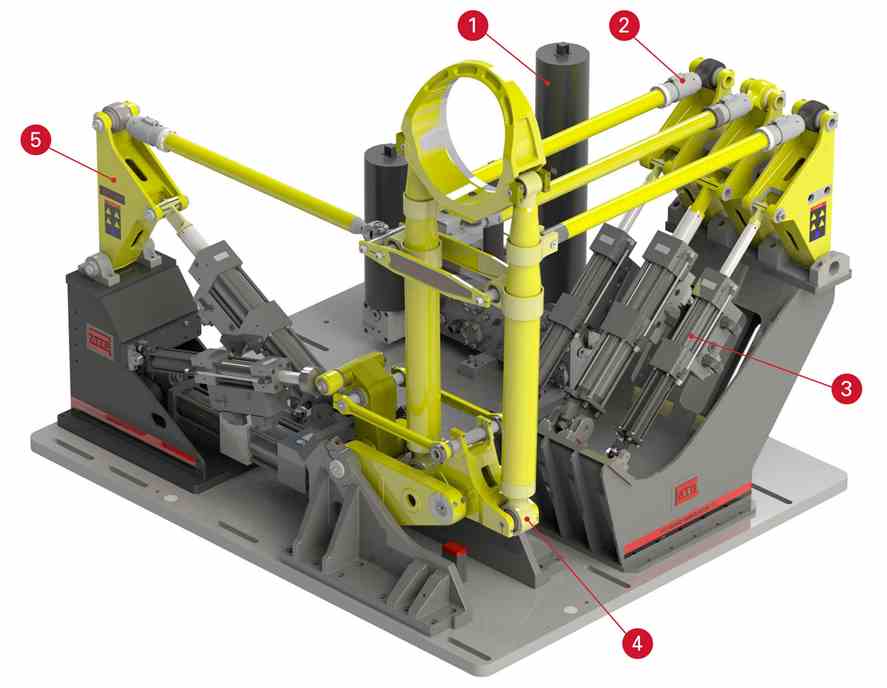
- Hydraulic Service Manifold & Accumulator
- Wrist Joint
- MTS DuraGlide Actuators with MTS SureCoat Rod Finishing Technology
- J-Crank
- Bell Crank
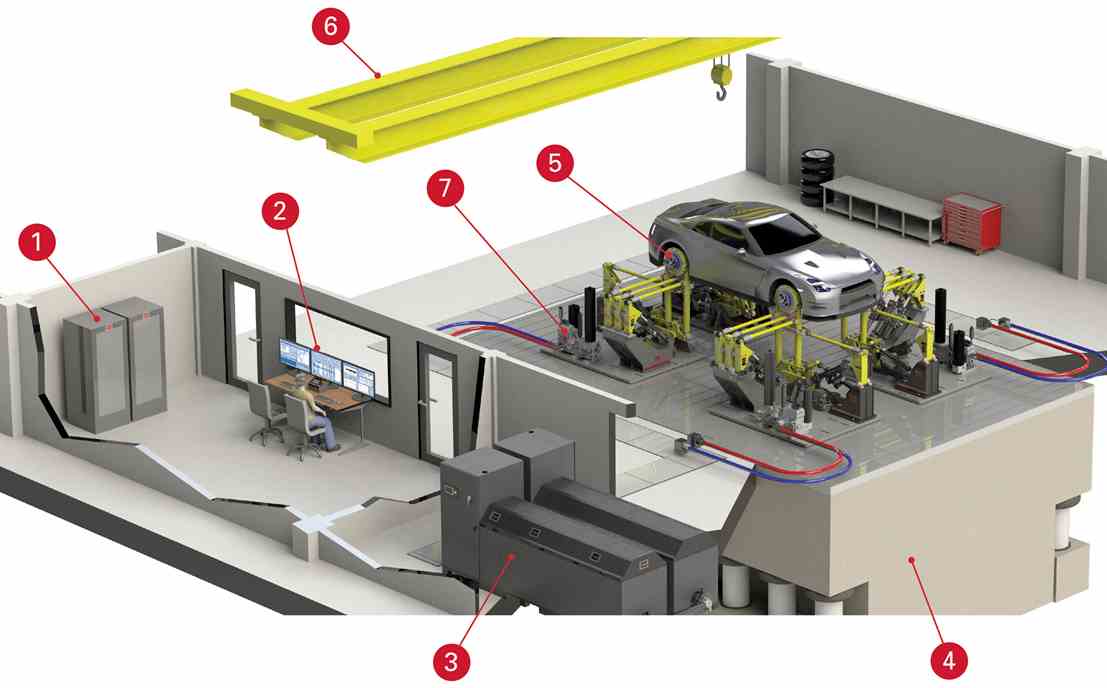
- FlexTest Controller
- RPC Pro Software
- SilentFlo Hydraulic Power Units (HPU)
- Seismic Mass
- SWIFT Evo Wheel Force Transducer
- Overhead Crane
- Hydraulic Service Manifold (HSM) & Accumulation
Service & Support
Our experts are here to help keep you up and running.
Related Products, Parts or Accessories
RPC® Connect Software
FlexTest® Controllers
SWIFT® Evo Wheel Force Transducers
Hybrid Simulation: Full Vehicle HSRC
Model 320 Tire-coupled Road Simulators
Looking for more products?
Go to Solution FinderContact An MTS Rep Today
Ready for a quote or need more information? We're here to help. Request a quoteResources
Model 329i Road Simulator
Achieve new levels of durability test fidelity and productiv…
Next-generation RPC Connect Software Now Available!
Josh Hernandez marks the beginning of the RPC Connect era in…
Introducing FlexTest Elite Performance Controllers
Increase channel count, system rate and computational cap…
The Origins of RPC with Dr. Glen Grenier
Q&A with the durability testing pioneer on the rise of R…
The Road to RPC Connect
Cody Johnson explores RPC software - past, present and futur…
RPC Connect Software Preview: Webinar 1
Safa Mogharebi explores the new Graphical User Interface
RPC Connect Software Preview: Webinar 2
Safa Mogharebi explores the new Setup & Analyze Stages
RPC Connect Software Preview: Webinar 3
Safa Mogharebi explores the new Model & Simulate Stages
RPC Connect Software Preview: Webinar 4
Safa Mogharebi explores the new Test Stage
Introducing an all-electric, durability capable Model 320 Tire-coupled Road Simulator
Featuring MTS Iron-core Linear Electric Actuation
European Off-Highway Seminar
Explore the technologies and methods used to evaluate agricu…
Test Rig Design
Build your own high-quality, reconfigurable component and su…
New Generation Flat-Trac Systems
MTS permanent magnet motors enhance torque capacity, resp…
Optimum Sample Rate for Servohydraulic Systems
Brad Thoen explores how system sample rate affects control f…
Pushing Tire Testing into Uncharted Territory
NTRC equips world's most capable tire testing facility
Testing High-performance Bike Suspensions
Tour the testing lab at Fox Factory, Inc. to see how they co…
National Tire Research Center (NTRC): Transforming Tire Design
High-powered MTS tire test system enables manufacturers t…
The Promise of Virtual Testing
Using analysis tools to derive accurate loads, motion and da…
Factors to Weigh When Considering Electric or Hydraulic Test Systems
Guidance on damper test systems and road simulators