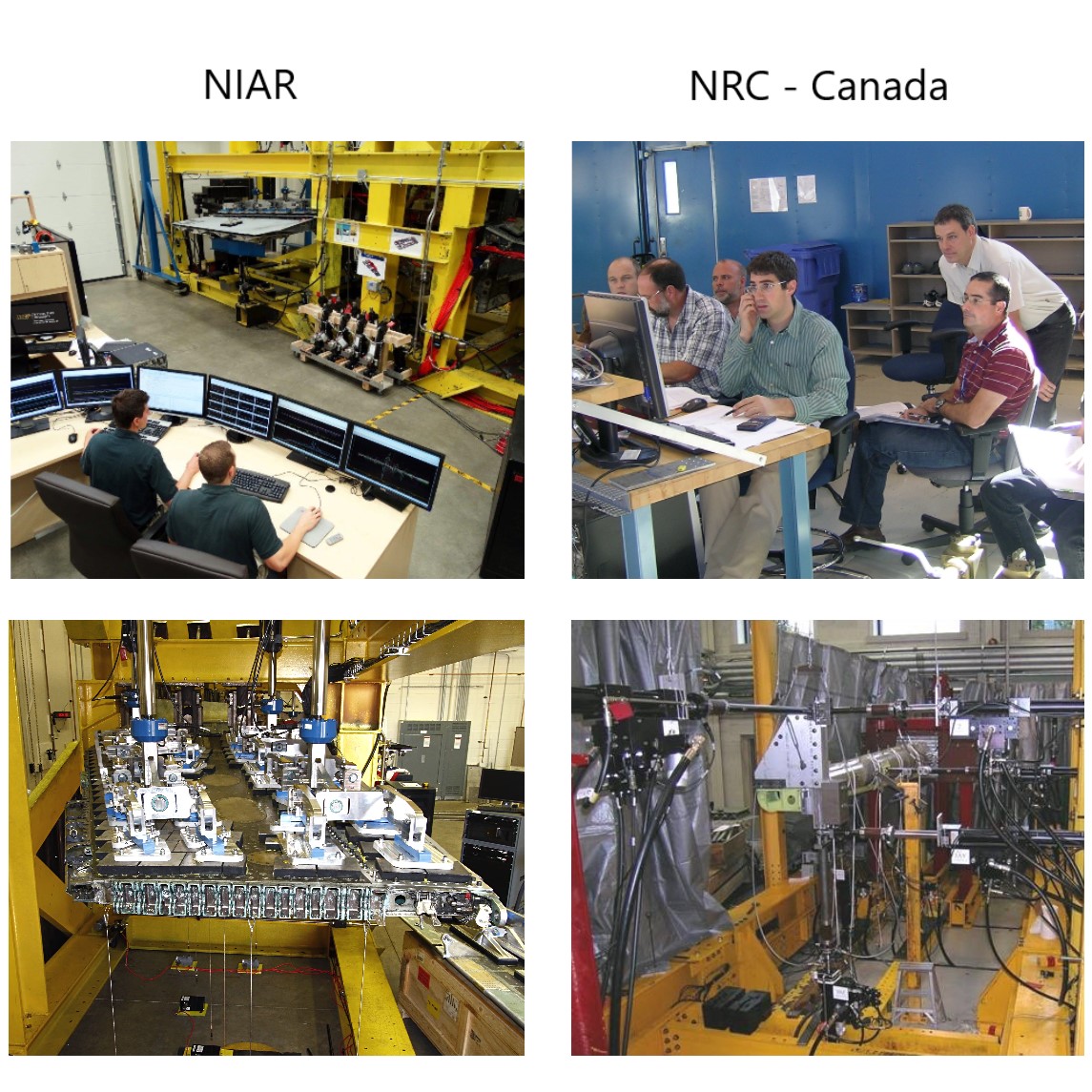
고도의 교차 결합 액추에이션 스키마가 포함된 실물 크기 구조 테스트 기기를 다루는 항공 우주 테스트 엔지니어는 독특한 난관에 부딪힙니다. 이렇게 복잡한 구성에서 다중 액추에이터는 테스트 대상의 같은 부분에 동시에 다른 힘을 가하여 테스트 일정을 위협하고 개발 프로그램을 지연시키는 오류가 발생할 확률을 높입니다.
이러한 오류를 줄여 테스트 속도와 효율성을 향상시키는 한 가지 도구는 MTS AeroPro™ 제어 및 데이터 수집 소프트웨어의 유틸리티인 C3 Performance입니다. C-cubed라고도 하는 C3 Performance를 사용하면 테스트 팀이 반복되는 수많은 중지 및 인터락을 해결하기 위해 테스트 일정에 추가 시간을 할애하지 않고도 고도로 교차 결합된 작동 체계를 효과적으로 관리할 수 있습니다.
C3 Performance 교차 결합 보상 기술은 NRC(National Research Council of Canada)와 MTS Systems Corporation의 전문가가 공동 개발했습니다. 이는 Andre Beltempo가 구조 테스트 엔지니어로 근무하는 캐나다의 실물 크기 구조 테스트 실험실이 위치한 NRC의 테스트 프로토콜에서 표준으로 사용됩니다.
"저희는 보통 모든 테스트에서 C 큐브를 사용합니다." Beltempo의 말입니다. "실물 크기 피로 테스트에는 액추에이터가 매우 복잡한 방식으로 상호작용합니다. 이것이 바로 우리에게 필요한 이유입니다.”라고 말합니다.
Beltempo 씨의 팀은 최근 주요 헬리콥터 제조업체의 기술 시연 중에 C3 Performance를 사용했습니다. 피로 및 정적 테스트 프로그램은 복합 테일붐에 집중했으며 고급 제조 기술을 사용해 제작되었습니다. 테스트는 안전 수명 허용 오차 FAA 요구 사항에 대한 부품을 인증하는 데 사용되는 테스트와 동일했습니다.
“테일 로터 기어 박스 인터페이스 피팅을 보면 두 개의 후면 액추에이터가 모두 동일한 피팅에 하중을 가하고 있습니다." "교차 결합 보상은 [액추에이터 간의] 충돌을 최소화하는 데 도움이 됩니다.”
테스트에는 평균 주파수 0.5Hz로 약 125일 동안 밤새 실행되는 6개의 액추에이터와 400만 개의 엔드포인트가 포함되었습니다. Beltempo에 따르면 이 테스트 속도는 C3 Performance가 없었다면 불가능했을 것입니다.
그는 “교차 결합 보상이 없었다면 이렇게 빨리 할 수 없었을 것”이라고 말했습니다. “야간 테스트의 경우 무인 종료에 대해 걱정할 필요가 없도록 최종 레벨을 절반 속도로 실행해야 했습니다. 모든 피로 측정 테스트에 대한 우리의 표준 접근 방식은 테스트를 조정하고 C-cubed를 적용한 후에 즉시 다시 조정하는 것입니다. 단단한 제품에 대해 2배 미만의 속도 증가를 본 적이 없습니다."
Beltempo 씨가 C3 Performance에 대해 감사하는 바는 전반적으로 사용하기 쉽다는 것입니다. 테스트 운영자가 자체적으로 설정할 수 있기 때문에 C3 Performance를 사용하면 실험실에서 더 많은 시간을 확보할 수 있습니다.
“핸즈프리라는 점 덕분에 더 중요한 작업에 집중할 수 있습니다.”라고 Beltempo 씨는 말했습니다. “앉아서 모든 계수를 스스로 계산해야 한다면 상황이 달라질 것입니다. 하지만 버튼을 클릭하기만 하면 됩니다. 진정한 생산성 향상이라고 할 수 입니다.”
C3 Performance 개발을 도운 조직이 프로토콜의 문제로 모든 피로 측정 테스트에 C3 Performance를 적용하는 것은 당연한 일이지만, 다른 실험실에서도 이 강력한 유틸리티의 문제 해결 잠재력을 발견하고 있습니다.
위치타 주립 대학교 NIAR(국립항공연구소) 복합재료 및 첨단재료 실험실의 기술 이사인 Waruna Seneviratne 박사에게 문제는 수면 부족이었습니다.
“우리는 맞춤형 고정 장치와 작동의 매우 독특한 조합으로 피로 측정 테스트를 실행하고 있었고 매우 빡빡한 테스트 일정을 가지고 있었습니다.”라고 Seneviratne 박사가 말했습니다. “테스트는 밤새 실행되었으며 많은 수의 성가신 오류 제한 트리거가 발생했습니다. 팀은 테스트 종료의 원인을 확인하고 테스트를 다시 시작하기 위해 한밤중에 연구소로 와야 했습니다. 우리는 점점 뒤처지고 있었습니다.”
이 테스트는 F/A-18 Hornet 항공기 복합 구조의 피로 수명을 평가하는 데 중점을 두었으며 항공기 대부분은 퇴역을 앞두고 있습니다. 항공기 교체가 2019년까지 준비되지는 않기 때문에 미 해군은 항공기의 노후된 복합 구조의 서비스 수명을 안전하게 연장해야 합니다.
Seneviratne 박사의 연구는 날개 루트의 합성물-티타늄 접합 조인트에 상당한 수명이 남아 있음을 성공적으로 확인했습니다. 새로운 테스트는 복합재 외피가 있는 전체 내부 날개를 포함하도록 연구를 확장했습니다. 테스트 제품에는 내부 날개, 뒷전 플실험실 및 중앙 배럴과 시뮬레이션된 앞전 플실험실 및 외부 날개가 포함됩니다. NIAR의 연구팀은 공격적인 기동을 재현하기 위해 맞춤 설계된 고정 장치가 있는 정교한 고강도 강철 장비를 만들고 상당한 하중을 가해야 했습니다.
“액추에이터 전체에서 스트로크와 하중 사이에 상당한 차이가 있었는데, 이것이 오류의 원인이 될 수 있었습니다.”라고 그는 말했습니다. "잘못된 종료를 최소화할 방법이 필요했기 때문에 조사를 시작했습니다."
Seneviratne 팀의 연구원인 Travis Cravens 씨는 C3 Performance의 설정 및 구성을 다루었습니다. MTS의 시스템 및 응용 분야 엔지니어는 설치 및 교육을 하루도 채 되지 않아 완료했으며 실험실에서는 거의 즉시 결과를 확인할 수 있었습니다.
"우리는 테스트 장비에 대한 기계적 수정 없이 첫날이 끝날 때까지 20% 더 빠르게 실행하고 있었습니다.”라고 Cravens 씨가 말했습니다. “C3 Performance는 배우고 설정하기가 매우 쉬웠습니다. 그것은 모두 소프트웨어 내에서 발생합니다. 각 액추에이터에 대해 단 하나의 추가 단계를 나타내는 각 하중 부하 채널에 단위 하중을 적용하여 교차 결합 매트릭스를 생성하기만 하면 됩니다.”
테스트 설정을 간소화하기 위해 C3 3 Performance는 자동화된 교차 결합 보상 계수를 생성하기 위해 단위 하중 케이스를 사용하여 교차 결합 데이터를 수동으로 입력하는 시간 집약적인 작업을 제거합니다. Seneviratne 씨는 이 과정을 적절한 비유로 나타내며
“서로 모르는 20명이 같은 프로젝트를 하는 것과 같다"고 말했습니다. "단위 하중은 단순히 모든 사람들을 서로 소개하여 그들이 더욱 효율적으로 협업하고 작업할 수 있도록 하는 방법입니다."
약간의 추가 튜닝을 통해 Seneviratne 씨와 Cravens 씨는 테스트 비율을 24% 높이고 중지 횟수를 크게 줄일 수 있었습니다.
"테스트 성능이 크게 향상되었습니다."라고 Cravens 씨는 말했습니다. “개선된 하중 추적 덕분에 피드백의 작은 변화가 오류 제한을 트리거할 가능성이 훨씬 줄어들어 테스트 중단이 줄어듭니다. 오류가 감소되어 시간당 더 많은 세그먼트를 실행할 수 있었습니다."
C3 Performance를 사용하기 전에 NIAR은 테스트 블록당 평균 97개의 중지와 55개의 인터락으로 시간당 최대 375개의 세그먼트만 달성할 수 있었습니다. C3 Performance를 통해 평균 51번의 정지와 15번의 인터락으로 시간당 480개 구간으로 개선되었습니다.
“정지 횟수는 기존의 3분의 1에 불과했으며 이는 큰 이점이었습니다.”라고 Seneviratne 씨가 말했습니다. “그래서 우리는 밤새 테스트를 실행할 수 있었고 어느 날은 중단 없이 실행할 수 있었습니다. 이전에는 없었던 최대 10시간의 테스트로 일정에 큰 도움이 되었습니다."
C3 Performance는 몇 주를 절약하여 Seneviratne의 팀이 제 시간에 테스트 결과를 제공할 수 있도록 했습니다. 또한 실험실 생산성이 향상되었습니다. 팀은 더 예측 가능한 일정으로 작업할 수 있었고 다른 프로젝트에 더 많은 시간을 할애할 수 있었습니다. 한정된 리소스가 있는 실험실에서 이는 중요한 이점입니다.
“밤새 테스트를 실행할 수 있고 낮에는 검사와 수리를 할 수 있다는 확신이 있었기 때문에 테스트 경로의 효율성을 높일 수 있었습니다.”라고 Seneviratne 씨가 말했습니다. "테스트가 최소 수준으로 중단하여 밤새 무인 상태로 실행되었다는 사실을 알고 더욱 효율적으로 계획하고 활동을 조정할 수 있었습니다."
이러한 오류를 줄여 테스트 속도와 효율성을 향상시키는 한 가지 도구는 MTS AeroPro™ 제어 및 데이터 수집 소프트웨어의 유틸리티인 C3 Performance입니다. C-cubed라고도 하는 C3 Performance를 사용하면 테스트 팀이 반복되는 수많은 중지 및 인터락을 해결하기 위해 테스트 일정에 추가 시간을 할애하지 않고도 고도로 교차 결합된 작동 체계를 효과적으로 관리할 수 있습니다.
C3 Performance 교차 결합 보상 기술은 NRC(National Research Council of Canada)와 MTS Systems Corporation의 전문가가 공동 개발했습니다. 이는 Andre Beltempo가 구조 테스트 엔지니어로 근무하는 캐나다의 실물 크기 구조 테스트 실험실이 위치한 NRC의 테스트 프로토콜에서 표준으로 사용됩니다.
"저희는 보통 모든 테스트에서 C 큐브를 사용합니다." Beltempo의 말입니다. "실물 크기 피로 테스트에는 액추에이터가 매우 복잡한 방식으로 상호작용합니다. 이것이 바로 우리에게 필요한 이유입니다.”라고 말합니다.
Beltempo 씨의 팀은 최근 주요 헬리콥터 제조업체의 기술 시연 중에 C3 Performance를 사용했습니다. 피로 및 정적 테스트 프로그램은 복합 테일붐에 집중했으며 고급 제조 기술을 사용해 제작되었습니다. 테스트는 안전 수명 허용 오차 FAA 요구 사항에 대한 부품을 인증하는 데 사용되는 테스트와 동일했습니다.
“테일 로터 기어 박스 인터페이스 피팅을 보면 두 개의 후면 액추에이터가 모두 동일한 피팅에 하중을 가하고 있습니다." "교차 결합 보상은 [액추에이터 간의] 충돌을 최소화하는 데 도움이 됩니다.”
테스트에는 평균 주파수 0.5Hz로 약 125일 동안 밤새 실행되는 6개의 액추에이터와 400만 개의 엔드포인트가 포함되었습니다. Beltempo에 따르면 이 테스트 속도는 C3 Performance가 없었다면 불가능했을 것입니다.
그는 “교차 결합 보상이 없었다면 이렇게 빨리 할 수 없었을 것”이라고 말했습니다. “야간 테스트의 경우 무인 종료에 대해 걱정할 필요가 없도록 최종 레벨을 절반 속도로 실행해야 했습니다. 모든 피로 측정 테스트에 대한 우리의 표준 접근 방식은 테스트를 조정하고 C-cubed를 적용한 후에 즉시 다시 조정하는 것입니다. 단단한 제품에 대해 2배 미만의 속도 증가를 본 적이 없습니다."
Beltempo 씨가 C3 Performance에 대해 감사하는 바는 전반적으로 사용하기 쉽다는 것입니다. 테스트 운영자가 자체적으로 설정할 수 있기 때문에 C3 Performance를 사용하면 실험실에서 더 많은 시간을 확보할 수 있습니다.
“핸즈프리라는 점 덕분에 더 중요한 작업에 집중할 수 있습니다.”라고 Beltempo 씨는 말했습니다. “앉아서 모든 계수를 스스로 계산해야 한다면 상황이 달라질 것입니다. 하지만 버튼을 클릭하기만 하면 됩니다. 진정한 생산성 향상이라고 할 수 입니다.”
C3 Performance 개발을 도운 조직이 프로토콜의 문제로 모든 피로 측정 테스트에 C3 Performance를 적용하는 것은 당연한 일이지만, 다른 실험실에서도 이 강력한 유틸리티의 문제 해결 잠재력을 발견하고 있습니다.
위치타 주립 대학교 NIAR(국립항공연구소) 복합재료 및 첨단재료 실험실의 기술 이사인 Waruna Seneviratne 박사에게 문제는 수면 부족이었습니다.
“우리는 맞춤형 고정 장치와 작동의 매우 독특한 조합으로 피로 측정 테스트를 실행하고 있었고 매우 빡빡한 테스트 일정을 가지고 있었습니다.”라고 Seneviratne 박사가 말했습니다. “테스트는 밤새 실행되었으며 많은 수의 성가신 오류 제한 트리거가 발생했습니다. 팀은 테스트 종료의 원인을 확인하고 테스트를 다시 시작하기 위해 한밤중에 연구소로 와야 했습니다. 우리는 점점 뒤처지고 있었습니다.”
이 테스트는 F/A-18 Hornet 항공기 복합 구조의 피로 수명을 평가하는 데 중점을 두었으며 항공기 대부분은 퇴역을 앞두고 있습니다. 항공기 교체가 2019년까지 준비되지는 않기 때문에 미 해군은 항공기의 노후된 복합 구조의 서비스 수명을 안전하게 연장해야 합니다.
Seneviratne 박사의 연구는 날개 루트의 합성물-티타늄 접합 조인트에 상당한 수명이 남아 있음을 성공적으로 확인했습니다. 새로운 테스트는 복합재 외피가 있는 전체 내부 날개를 포함하도록 연구를 확장했습니다. 테스트 제품에는 내부 날개, 뒷전 플실험실 및 중앙 배럴과 시뮬레이션된 앞전 플실험실 및 외부 날개가 포함됩니다. NIAR의 연구팀은 공격적인 기동을 재현하기 위해 맞춤 설계된 고정 장치가 있는 정교한 고강도 강철 장비를 만들고 상당한 하중을 가해야 했습니다.
“액추에이터 전체에서 스트로크와 하중 사이에 상당한 차이가 있었는데, 이것이 오류의 원인이 될 수 있었습니다.”라고 그는 말했습니다. "잘못된 종료를 최소화할 방법이 필요했기 때문에 조사를 시작했습니다."
Seneviratne 팀의 연구원인 Travis Cravens 씨는 C3 Performance의 설정 및 구성을 다루었습니다. MTS의 시스템 및 응용 분야 엔지니어는 설치 및 교육을 하루도 채 되지 않아 완료했으며 실험실에서는 거의 즉시 결과를 확인할 수 있었습니다.
"우리는 테스트 장비에 대한 기계적 수정 없이 첫날이 끝날 때까지 20% 더 빠르게 실행하고 있었습니다.”라고 Cravens 씨가 말했습니다. “C3 Performance는 배우고 설정하기가 매우 쉬웠습니다. 그것은 모두 소프트웨어 내에서 발생합니다. 각 액추에이터에 대해 단 하나의 추가 단계를 나타내는 각 하중 부하 채널에 단위 하중을 적용하여 교차 결합 매트릭스를 생성하기만 하면 됩니다.”
테스트 설정을 간소화하기 위해 C3 3 Performance는 자동화된 교차 결합 보상 계수를 생성하기 위해 단위 하중 케이스를 사용하여 교차 결합 데이터를 수동으로 입력하는 시간 집약적인 작업을 제거합니다. Seneviratne 씨는 이 과정을 적절한 비유로 나타내며
“서로 모르는 20명이 같은 프로젝트를 하는 것과 같다"고 말했습니다. "단위 하중은 단순히 모든 사람들을 서로 소개하여 그들이 더욱 효율적으로 협업하고 작업할 수 있도록 하는 방법입니다."
약간의 추가 튜닝을 통해 Seneviratne 씨와 Cravens 씨는 테스트 비율을 24% 높이고 중지 횟수를 크게 줄일 수 있었습니다.
"테스트 성능이 크게 향상되었습니다."라고 Cravens 씨는 말했습니다. “개선된 하중 추적 덕분에 피드백의 작은 변화가 오류 제한을 트리거할 가능성이 훨씬 줄어들어 테스트 중단이 줄어듭니다. 오류가 감소되어 시간당 더 많은 세그먼트를 실행할 수 있었습니다."
C3 Performance를 사용하기 전에 NIAR은 테스트 블록당 평균 97개의 중지와 55개의 인터락으로 시간당 최대 375개의 세그먼트만 달성할 수 있었습니다. C3 Performance를 통해 평균 51번의 정지와 15번의 인터락으로 시간당 480개 구간으로 개선되었습니다.
“정지 횟수는 기존의 3분의 1에 불과했으며 이는 큰 이점이었습니다.”라고 Seneviratne 씨가 말했습니다. “그래서 우리는 밤새 테스트를 실행할 수 있었고 어느 날은 중단 없이 실행할 수 있었습니다. 이전에는 없었던 최대 10시간의 테스트로 일정에 큰 도움이 되었습니다."
C3 Performance는 몇 주를 절약하여 Seneviratne의 팀이 제 시간에 테스트 결과를 제공할 수 있도록 했습니다. 또한 실험실 생산성이 향상되었습니다. 팀은 더 예측 가능한 일정으로 작업할 수 있었고 다른 프로젝트에 더 많은 시간을 할애할 수 있었습니다. 한정된 리소스가 있는 실험실에서 이는 중요한 이점입니다.
“밤새 테스트를 실행할 수 있고 낮에는 검사와 수리를 할 수 있다는 확신이 있었기 때문에 테스트 경로의 효율성을 높일 수 있었습니다.”라고 Seneviratne 씨가 말했습니다. "테스트가 최소 수준으로 중단하여 밤새 무인 상태로 실행되었다는 사실을 알고 더욱 효율적으로 계획하고 활동을 조정할 수 있었습니다."