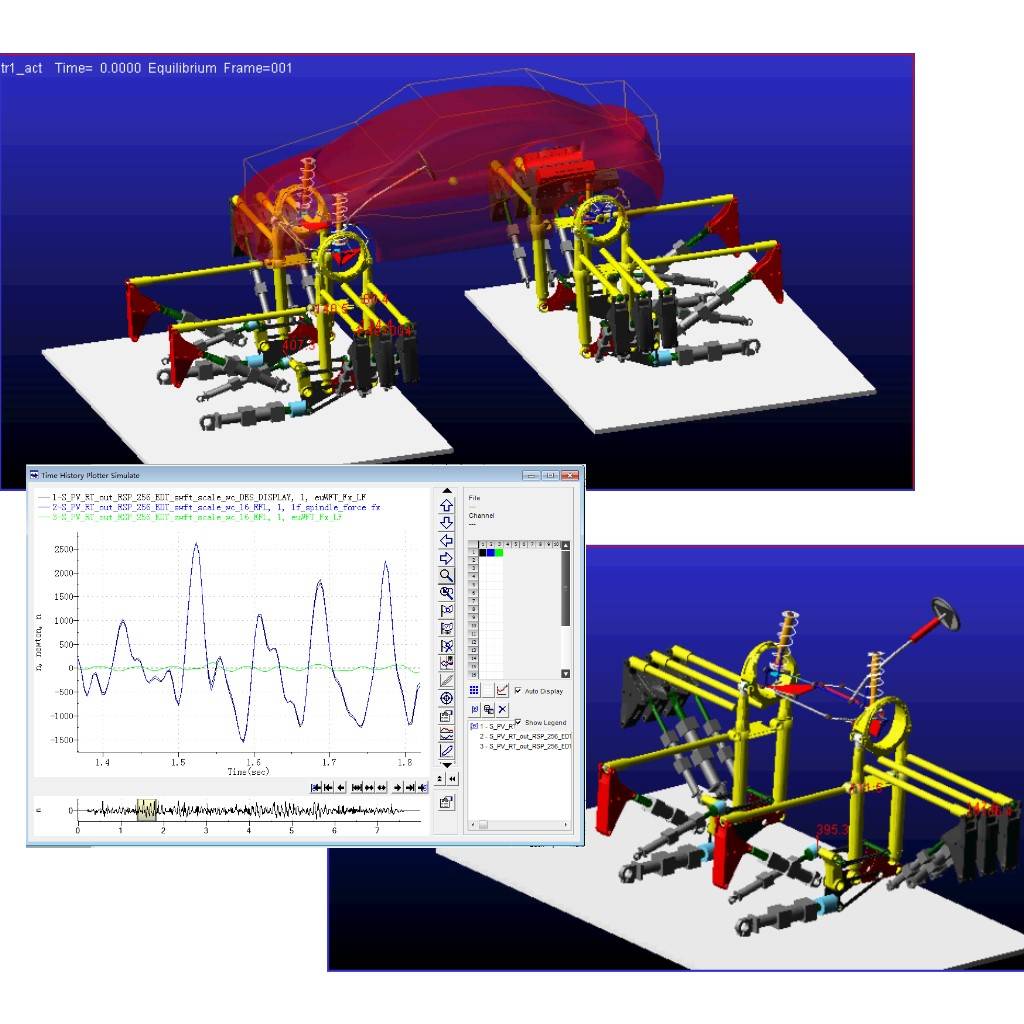
개발 주기를 단축하고 비용을 절감해야 한다는 지속적인 압박 속에서 자동차 제조업체는 분석 도구를 사용하여 물리적 프로토타입이 나오기 훨씬 전에 차량 설계에 대한 의미 있는 가상 평가를 미리 수행하는 방법을 점점 더 모색하고 있습니다. 이러한 방식으로 정확히 예측되거나 계산된 하중을 얻을 수 있는 기능을 통해 구성요소 물리적 테스트의 효율성을 높이고 설계 결함을 초기에 파악 및 제거할 수 있으며 재작업 및 프로토타입에 대한 의존도를 줄이고 설계 검증을 간소화할 수 있습니다.
차량 개발 프로세스 초기에 정확히 계산된 하중을 얻기 위해 다양한 시뮬레이션 접근 방식이 고안되었습니다. 한 가지 방법인 가상 시험장은 디지털화된 도로에서 차량 모델을 "운전"하는 것입니다. 이 접근 방식은 전적으로 가상 모델에 의존하는 장점이 있지만 물리적 테스트를 통해 검증하기 어려운 부정확한 하중을 발생시킵니다. 반면에 세미 분석 방법은 기존 차량에서 얻은 스핀들 하중을 사용하여 차량 모델을 활성화시킵니다. 이 방법은 가상 시험장보다 더 나은 결과를 제공하지만 차량 모델에 완전히 적합하지는 않은 경계 조건을 설정하므로 계산된 하중은 여전히 부정확하고 검증하기 어렵습니다. 세 번째 방법인 가상 테스트는 실제 물리적 테스트 시스템의 모델을 시뮬레이션에 통합하여 차량 모델을 활성화함으로써 이러한 문제를 해결합니다.
가상 테스트는 유한 요소 분석 도구, 다물체 동역학 분석 도구 및 RPC 반복 기술을 사용하여 개발 프로세스 초기에 차량 시스템의 정확한 하중, 동작 및 손상 정보를 도출하는 물리적 테스트 시뮬레이션입니다. 이 방식의 장점은 매우 많습니다. 첫째, 지면이나 타이어를 증명하는 것보다 물리적 테스트 시스템의 제약 조건을 모델링하는 것이 더 쉽기 때문에 가상 테스트가 다른 방법보다 훨씬 더 효과적인 경계 조건을 설정합니다. 둘째, 가상 테스트는 분석 영역에서 유용성을 증명한 입증되고 잘 정립된 물리적 테스트 도구 및 기술을 다수 활용합니다. 셋째, 모델링된 물리적 테스트 시스템의 통합은 후속 물리적 테스트를 통해 결과 검증을 크게 간소화하고, 물리적 테스트 설정 및 고정 장치 설계를 개선할 수 있는 기회를 제공합니다. 분석 및 물리적 테스트 분야에 걸쳐 가상 테스트에는 CAE 도구와 물리적 테스트에 대한 고급 지식, RPC Pro 소프트웨어와 분석 모델을 연결하는 프로세스 개발, 가능하면 어느 정도의 가상 테스트 노출 및 경험이 필요합니다.
MTS는 수년 동안 다양한 방법론을 평가하기 위해 현대 자동차(HMC), Thermo King과 같은 주요 고객과 함께 다양한 데모 프로젝트를 수행하여 가상 테스트 접근 방식을 개선하는 데 주력해 왔습니다. 해당 프로젝트에는 전체 차량 및 하위 시스템에 대한 가상 테스트가 포함되었으며, 모두 측정된 RLD(도로 하중 데이터) 또는 실제 물리적 테스트와 만족스러운 상관관계를 보여주었습니다. 이러한 경험을 통해 얻은 기본 방법론은 다음 단계로 구성됩니다. 1) 테스트 장비 모델을 시편 모델과 연결 2) 모델을 RPC Pro와 연결 3) 가상 테스트 장비에서 도로 하중 데이터 재현 4) 계산된 하중 추출 5) 물리적 구성요소/하위 시스템 테스트 생성
SAIC(State Automotive Institute of China)와의 최근 데모 프로젝트는 실제로 이 방법론의 우수한 예시를 제공합니다.
- 테스트 장비 모델을 시편 모델과 연결
MTS는 프로젝트 초기에 ADAMS, Simulink 및 ADAMS-Simulink 공동 시뮬레이션 형식으로 테스트 장비 모델 모음을 구축했습니다. 모델링된 MTS 테스트 장비에는 다양한 모델 329 스핀들 결합 로드 시뮬레이터, 모델 353.20 MAST(다축 시뮬레이션 테이블) 시스템 및 TestLine 구성요소 테스트 시스템이 포함되었습니다. FlexTest 디지털 컨트롤러, MTS 액추에이터 및 서보 밸브, 액추에이터 변위, 가속도 및 하중을 DOF 변위, 가속도 및 하중으로 변환하는 액추에이터 변환을 포함한 일부 테스트 장비 구성요소도 모델링되었습니다. 프로젝트 시간 제약과 복잡한 공동 시뮬레이션 모델의 상대적으로 느린 시뮬레이션 속도로 인해 ADAMS/Car 329 모델은 SAIC 전체 차량, 전면 서스펜션 및 후면 서스펜션 모델과 결합되어 결국에는 대부분의 가상 테스트에 사용되었습니다.
- RPC Pro와 모델 결합
가상 테스트 서버는 RPC Pro 소프트웨어와 ADAMS/Car 329 모델을 연결하기 위해 개발되었습니다. 테스트 중에 RPC Pro는 이 가상 서버를 사용하여 드라이브 파일을 ADAMS 모델로 보내고, ADAMS 시뮬레이션을 시작하고, 응답 파일을 ADAMS 폴더에서 RPC Pro 작업 디렉터리로 복사합니다. 또한 RPC Pro에 이미 있는 Matlab 인터페이스 도구를 사용하여 RPC Pro를 공동 시뮬레이션 모델과 결합했습니다.
- 가상 테스트 장비에서 도로 하중 데이터 재현
그런 다음 RPC 반복 기술을 사용하여 다양한 선별 이벤트 및 조작에 대해 시험장에서 수집한 도로 하중(스핀들 하중) 데이터를 재현했습니다. 흥미롭게도 가상 329 장비에 대한 초기 RPC 반복은 수렴을 나타내지 않아 SAIC 차량 모델에 결함이 있음을 시사합니다. 모델에 대한 후속 분석에서 실제로 결함이 나타났으며 이는 단기간에 수정되었습니다. 모델이 개선됨에 따라 RPC 반복이 마침내 집약되어, 전체 및 부분 차량 가상 시뮬레이션 둘 다에 대해 모든 채널에서 원하는 신호와 달성된 신호 간의 우수한 상관관계와 낮은 RMS 오류를 보여줍니다.
- 계산된 하중 추출
RPC 반복 수렴 시 모든 기계적 구성요소 또는 하위 시스템에 대해 계산된 하중을 시간의 함수로 차량 모델에서 쉽게 얻을 수 있습니다.
- 물리적 테스트 생성
그런 다음, 차량 모델에서 추출한 하중 시간 기록을 사용하여 후속 물리적 구성요소 테스트를 정의했습니다. 부품이 단일 축이나 다중 축 하중을 받는지 여부가 결정되면 RPC Pro의 테스트 방법 및 도구를 사용하여 상당히 가속화된 구성요소 테스트를 정의할 수 있습니다. 단일 축 하중을 받는 구성요소의 경우 Block Cycle 방법 또는 PSD(Power Spectrum Density) 방법을 사용할 수 있습니다. 다축 하중을 받는 구성요소의 피크 밸리 슬라이싱 방법을 사용할 수 있습니다. 구성요소의 하중 빈도를 보존해야 하는 상황에서는 시간 이력 재생 방법이 가장 적합합니다. 이러한 테스트 유형을 위해 RPC Pro는 잠재적인 가속 내구성 테스트를 2배에서 10배까지 가속화할 수 있는 피로 민감 편집 기능을 제공합니다. 각 구성요소에 대한 하중 신호가 결정되면 가상 테스트 장비의 기반이 된 동일한 물리적 테스트 시스템을 사용하여 구성요소 테스트를 수행할 수 있습니다. 또한 Peak-Valley Compensation, Adaptive Inverse Compensation, RPC iteration과 같은 RPC Pro의 다양한 보상 기술을 사용하여 물리적 테스트 중에 원하는 하중 조건이 정확하게 달성되었는지 확인할 수 있습니다.
가상 테스트에 대한 MTS의 지속적인 탐색은 물리적 부품이나 프로토타입을 개발하기 전에 구성요소 하중을 정확하게 예측하기 위한 효과적인 수단임을 보여줍니다. 이러한 계산된 하중을 얻은 후에는 이를 얻는 데 사용된 동일한 RPC Pro 도구 및 기술을 사용하여 정확도와 차량 모델의 정확도를 검증하는 데 필요한 물리적 테스트를 생성하고 수행할 수 있습니다. 효과적인 가상 테스트가 차량 개발에 미치는 잠재적 영향은 상당합니다. 정확한 예측 하중 및 차후 조기 물리적 테스트의 가용성은 구성요소 및 하위 시스템 재작업을 최소화하고, 여러 프로토타입의 필요성을 줄이며 설계 검증을 가속화합니다. 또한 물리적 테스트의 역할은 다음과 같이 발전합니다. 테스트는 차량 설계의 최종 검증을 달성하기 위해 계속 필요하지만 차량 모델의 정확성을 검증하기 위해 갈수록 맞춤화될 것입니다. 마지막으로 가상 테스트는 분석과 물리적 테스트 분야 및 문화의 통합을 촉진하여 도구, 프로세스 및 경험의 공유를 통해 새로운 효율성을 극대화할 것입니다.
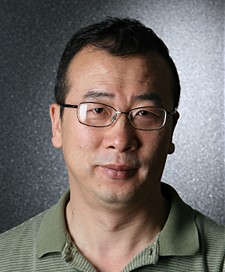