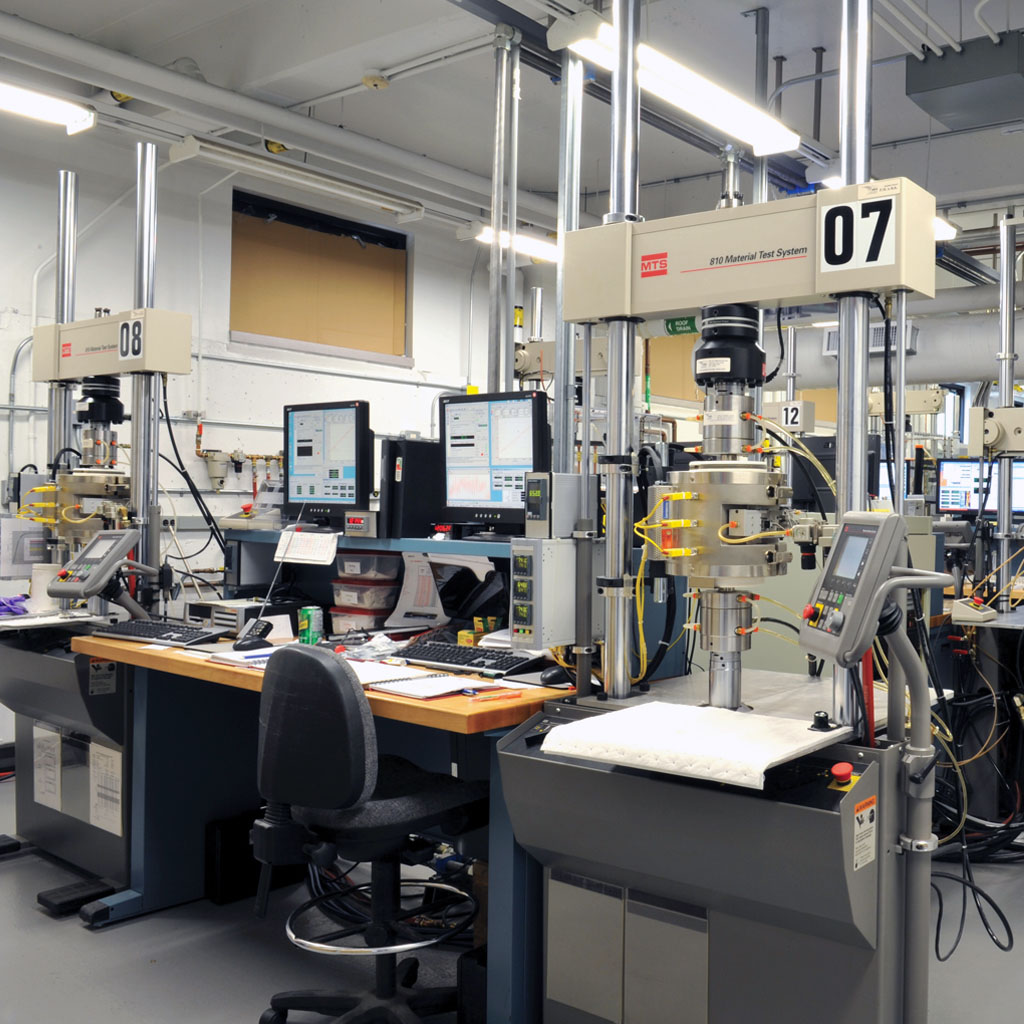
고객이 직면한 과제
극한의 온도에서 장기간 성능을 발휘할 수 있는 고온 재료의 개발은 연료 효율성에 대한 기대치를 재정의할 차세대 제트 엔진 및 가스 터빈의 토대를 마련하고 있습니다. 이 분야에서 가장 진보된 연구 중 일부는 온타리오주 오타와에 있는 캐나다 항공우주연구소 국립연구위원회의 소속된 구조 및 재료 성능 실험실에서 수행됩니다.
15명의 연구 과학자로 구성된 팀인 Materials and Component Technologies Group은 고온 합금 및 세라믹 매트릭스 복합 재료를 포함하여 새로운 가스 터빈 재료의 설계, 개발 및 테스트를 전문적으로 다룹니다. 이 그룹은 사내 연구를 추진하며 Pratt & Whitney, Rolls-Royce 및 General Electric과 같은 상용 엔진 제조업체와 ATI Allvac 및 Carpenter Technologies와 같은 재료 공급업체와도 협력합니다. 점점 더 높은 온도에 노출될 때 새로운 재료가 어떻게 성능을 발휘하고 얼마나 오래 지속되는지를 정확히 판단하려면 광범위한 정밀 기계 테스트를 수행해야 합니다.
"우리는 인장, 크리프 및 파괴 인성 테스트에서 프레팅 피로, 열기계 피로, 피로 균열 성장 및 크리프 균열 성장 속도와 같은 더욱 전문화된 테스트에 이르기까지 모든 작업을 수행합니다."라며 그룹의 고온 피로 및 파괴 역학 시설 관리자인 Kearsey 박사가 말했습니다. "재료를 개발하고 테스트한 다음 이러한 재료를 특성화하기 위한 표준 테스트 방법을 개발하고 있습니다. 여기에는 시편 형상을 파악하고 실험실에서 엔진의 서비스 환경을 복제하는 것이 포함됩니다."
현재 Kearsey 박사의 가장 큰 과제는 간단합니다. 바로 열입니다. 지난 수십 년 동안 스테인리스 스틸, 티타늄, 알루미늄 합금을 테스트하기 위한 온도는 비교적 적당했습니다. 오늘날 가장 진보된 재료를 테스트하려면 최대 25% 더 높은 온도가 필요합니다.
"온도가 너무 높아서 재료를 테스트하는 것이 더 복잡한 문제가 됩니다."라고 그는 말했습니다. “표준 관행이 800°C 등급의 장비를 사용할 때 1,000°C에서 재료를 어떻게 측정하는가? 균열 성장 속도를 측정하기 위해 적절한 기기를 어떻게 추가하는가? 이러한 의문 사항은 불가능하지는 않지만 매우 복잡합니다. 테스트 결과는 중요한 엔진 구성요소을 만드는 데 사용되기 때문에 온도와 하중이 100% 추적 가능하다는 것을 반드시 확인해야 합니다.”
MTS 솔루션
Materials and Component Technologies Group은 기존 MTS 810 하중 프레임에서 최첨단 MTS Landmark® 서보 유압식 테스트 시스템에 이르기까지 모든 것을 포함하는 구성인 고온 테스트를 위해 18개의 서로 다른 MTS 솔루션을 배포합니다.
"MTS 하중 프레임만 사용하는 이유는 안정성 때문입니다."라고 Kearsey 박사는 말했습니다. “4~5개의 프레임을 나란히 실행하면 실험실이 흔들립니다. MTS 프레임은 매우 안정적입니다. 시편을 잘못 정렬할 수 있는 비틀림이나 비틀림이 없습니다."
시설의 테스트 장비를 완성하는 것은 두 개의 MTS 유압 동력 장치인 FlexTest® 디지털 제어 및 다목적 TestWare® 소프트웨어입니다 또한 실험실은 그립 및 고정 장치, 신율계 및 스트레인 게이지, 용광로, 유도 가열 장치를 포함하여 MTS 테스트 액세서리를 완벽하게 보완합니다. 이러한 모든 액세서리는 특정 고온 테스트에 필요한 복잡한 구성에 쉽게 결합하고 통합할 수 있어야 합니다.
Kearsey 박사는 “하드웨어는 다양한 테스트 온도와 조건에서 제대로 작동해야 합니다. “MTS 퍼니스를 어떤 하중 프레임에도 부착할 수 있다는 점이 만족스럽습니다. 호환성은 특히 반복성을 위해 중요합니다. 유사한 형상에 대해 100번의 테스트를 수행해야 할 때 각각의 단일 항목에 대해 보정을 다시 수행하는 데 시간을 소비하고 싶지 않습니다."
고객 혜택
Kearsey 박사에게 테스트 하드웨어 및 소프트웨어의 신뢰성보다 더 중요한 것은 없습니다. 결과의 정확성, 실험실의 생산성 및 외부 클라이언트의 만족을 위해서는 신뢰성이 필수적입니다.
"거의 고장이 나지 않기 때문에 MTS 장비를 구매합니다."라고 그는 말했습니다. “교체할 필요가 없고 신뢰할 수 있으며 추적 가능합니다. 연구 실험실에서 추적성은 핵심 요구 사항입니다. 시스템에서 정렬을 수행하는 경우 정확히 다음 테스트에서 발생하는지 확인해야 합니다. 고급 단결정 합금을 테스트하든 수명 예측 모델링을 위해 50년 된 합금을 평가하든 관계없습니다. MTS 테스트 시스템을 사용하여 확신을 가지고 결정을 내리는 데 필요한 데이터를 생성할 수 있습니다.”
신율계의 신뢰성은 최대 10Hz의 주파수에서 또는 측정된 반사가 더 작은 더 단단한 재료의 고온 재료 테스트에서 특히 중요합니다. 또한 Kearsey 박사는 소프트웨어의 신뢰성을 중요한 요소로 언급했습니다.
"예를 들어, 열기계 피로 테스트를 수행할 때 테스트는 3개월 동안 지속될 수 있습니다."라고 그는 말했습니다. “클라이언트에게는 테스트 비용이 매우 비싸기 때문에 테스트 중에 소프트웨어가 충돌했고 결과가 유효하지 않다고 말하고 싶지 않을 수 있습니다. MTS 소프트웨어는 이러한 골칫거리를 주지 않기 때문에 이 점에서 매우 중요합니다. 매우 안정적이며 많은 모듈이 저주기 피로, 열기계 피로 및 기타 유형의 테스트를 위해 사전 프로그래밍되어 있습니다."
지금도 Kearsey 박사는 1,000°C에서 테스트와 관련된 과제를 극복하기 위해 노력하고 있으며 상한 온도가 상승할 것으로 예상하고 있습니다. 실제로 그는 MTS와 협력하여 훨씬 더 높은 온도에서 수행할 수 있는 테스트 시스템을 설계하고 있습니다.
“새로운 합금이 세라믹 매트릭스 복합재로 대체됨에 따라 최대 1,300°C 또는 1,400°C의 테스트를 실행해야 합니다." “우리는 이미 MTS를 통해 이를 실현하는 방법에 대해 논의하고 있습니다. 어떤 크기의 퍼니스가 필요한가? 핫존은 어떻게 되는가? 어떤 신율계가 필요한가? MTS는 항상 적시에 우리에게 오는 것 같습니다. 이러한 지원은 우리가 계속 MTS를 이용하는 이유입니다.”라고 그는 말했습니다.