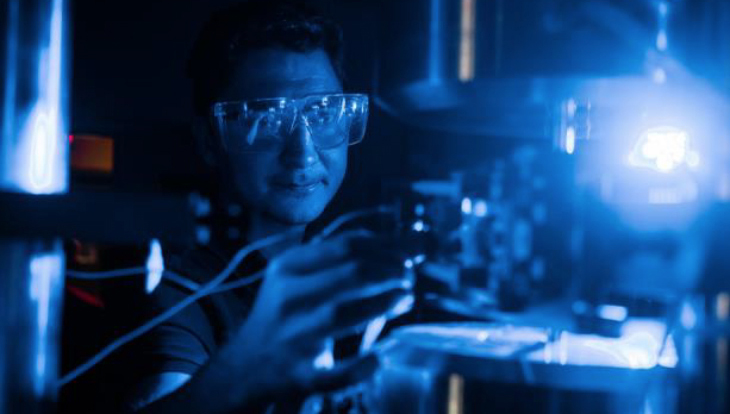
부하를 견뎌야 하는 거의 모든 기계 부품은 시스템의 수명 동안 두 번 이상 로드됩니다. 많은 산업에서 구조 재료는 반복적이고 가변적인 단축 또는 다축 비례 또는 비 비례 부하 조건을 견디도록 설계되었습니다. 이러한 종류의 금속 구조를 설계할 때 종종 재료의 내부하 여분을 활용하지 못하는 탄성(수율 제한) 분석을 기반으로 하기 때문에 구조 중량과 내구성이 비효율적입니다. 반대로 안전한 순환 탄성 특성을 보여주는 성능 시험 설계는 구성요소의 수명을 연장하거나 경량화의 이점을 늘릴 수 있습니다.
Lehigh University, 시운전 디자인을 위한 문을 개방하다
시운전은 소성 축적의 정지와 순수한 탄성 거동의 회복으로 이어지는 주기적 하중 시 적절한 잔류 응력을 설정함으로써 달성됩니다. 성능 시험의 개념과 설계 규칙은 1920년대에 개발되었지만 원자력 산업 외부에는 거의 알려지지 않았으며 많은 엔지니어링 설계 커뮤니티에서 많이 활용되지 않고 있습니다. 성능 시험 분석의 광범위한 응용 분야에서 주요 장애물은 최신 전체 필드 측정을 사용하는 까다로운 열역학적 부하 조건에 대한 실험 평가가 부족하다는 것입니다. 성능 시험 설계 및 최적화에서 보다 광범위한 응용을 가능하게 하기 위해 이 실험적 특성화를 제공하는 것은 Lehigh University의 Natasha Vermaak 박사가 지휘하는 팀의 주요 목표 중 하나입니다.
Lehigh 팀은 실험 데이터를 통해 구성 모델을 보정할 수 있습니다. 이러한 모델은 주기적 비탄성 동작을 더 잘 이해하고 모델링하기 위해 접촉식 신장계와 비접촉식 디지털 이미지 상관 관계(DIC) 시스템이 제공하는 정보를 결합합니다.
데이터 동기화
테스트 시스템 컨트롤러에는 DIC 측정을 위해 열기계 테스트를 DIC 컨트롤러와 동기화하는 여러 디지털 및 아날로그 입력 및 출력이 있습니다. 실험 데이터는 두 시스템 모두에 저장됩니다. DIC 결과(DIC 필드, 구성요소, 프로젝트)는 DIC 시스템에 저장되고 테스트 시스템 데이터는 그곳에 저장됩니다. 그러나 테스트 시스템 컨트롤러 아날로그 출력을 사용하면 열 화상 보정과 함께 두 개의 채널을 DIC 시스템으로 보내고 해당 DIC 프로젝트에 저장할 수도 있습니다. 이를 통해 DIC 필드와 적용된 부하 간의 시간 동기화가 개선됩니다. 또한 전체 필드 측정을 지점 기반 데이터와 더 쉽게 비교할 수 있습니다.
데이터 분석 및 감소
테스트 시스템 소프트웨어의 중요한 기능은 중간 측정을 기반으로 동작을 변경하는 실험을 프로그래밍하는 기능입니다. 시편 응답 측정은 조건부 프로그래밍을 사용하여 다른 기준을 생성하고, 추가 측정을 시작하고, 하중 조건을 조정합니다. 성능 시험 테스트의 경우 하중이 주기적으로 적용되는 동안 플라스틱 축적이 안정화되는지를 결정하는 것이 목표입니다. 소프트웨어는 이 조건을 자동으로 확인하는 사용자 정의 프로그램을 생성할 수 있습니다. DIC 컨트롤러를 트리거하는데 사용하면 관련 데이터만 기록되고 데이터가 감소합니다. DIC 시스템은 데이터 동기화 및 수집을 위한 보완 기능도 제공합니다.
보완적인 스트레인 측정 솔루션
테스트 실험실은 더 포괄적인 재료 특성화를 제공하기 때문에 접촉 및 비접촉 스트레인 측정 솔루션을 모두 사용합니다. DIC는 샘플의 모든 가시 지점에서 스트레인 및 변형과 같은 신장계보다 훨씬 더 많은 정보를 제공합니다. 그리고 비접촉식 측정 솔루션은 샘플 크기, 실험 설정 및 재사용과 관련하여 추가적인 자유를 제공합니다. 반면 접촉식 신장계는 견고하고 신뢰할 수 있는 변형 측정 기술로 잘 알려져 있습니다. 신장계는 또한 이미지를 처리하는 데 상당한 데이터 저장 공간과 시간이 필요할 수 있는 DIC 시스템보다 더 높은 데이터 수집 속도를 자랑합니다.
Vermaak Lab에서는 테스트 시스템 및 DIC 시스템 파트너로부터 받은 엔지니어링, 응용 분야 및 통합 지원의 이점을 활용하여 이러한 시스템과의 데이터 수집, 동기화 및 분석을 정확하고 효율적으로 만듭니다.
Lehigh University, 시운전 디자인을 위한 문을 개방하다
시운전은 소성 축적의 정지와 순수한 탄성 거동의 회복으로 이어지는 주기적 하중 시 적절한 잔류 응력을 설정함으로써 달성됩니다. 성능 시험의 개념과 설계 규칙은 1920년대에 개발되었지만 원자력 산업 외부에는 거의 알려지지 않았으며 많은 엔지니어링 설계 커뮤니티에서 많이 활용되지 않고 있습니다. 성능 시험 분석의 광범위한 응용 분야에서 주요 장애물은 최신 전체 필드 측정을 사용하는 까다로운 열역학적 부하 조건에 대한 실험 평가가 부족하다는 것입니다. 성능 시험 설계 및 최적화에서 보다 광범위한 응용을 가능하게 하기 위해 이 실험적 특성화를 제공하는 것은 Lehigh University의 Natasha Vermaak 박사가 지휘하는 팀의 주요 목표 중 하나입니다.
Lehigh 팀은 실험 데이터를 통해 구성 모델을 보정할 수 있습니다. 이러한 모델은 주기적 비탄성 동작을 더 잘 이해하고 모델링하기 위해 접촉식 신장계와 비접촉식 디지털 이미지 상관 관계(DIC) 시스템이 제공하는 정보를 결합합니다.
데이터 동기화
테스트 시스템 컨트롤러에는 DIC 측정을 위해 열기계 테스트를 DIC 컨트롤러와 동기화하는 여러 디지털 및 아날로그 입력 및 출력이 있습니다. 실험 데이터는 두 시스템 모두에 저장됩니다. DIC 결과(DIC 필드, 구성요소, 프로젝트)는 DIC 시스템에 저장되고 테스트 시스템 데이터는 그곳에 저장됩니다. 그러나 테스트 시스템 컨트롤러 아날로그 출력을 사용하면 열 화상 보정과 함께 두 개의 채널을 DIC 시스템으로 보내고 해당 DIC 프로젝트에 저장할 수도 있습니다. 이를 통해 DIC 필드와 적용된 부하 간의 시간 동기화가 개선됩니다. 또한 전체 필드 측정을 지점 기반 데이터와 더 쉽게 비교할 수 있습니다.
데이터 분석 및 감소
테스트 시스템 소프트웨어의 중요한 기능은 중간 측정을 기반으로 동작을 변경하는 실험을 프로그래밍하는 기능입니다. 시편 응답 측정은 조건부 프로그래밍을 사용하여 다른 기준을 생성하고, 추가 측정을 시작하고, 하중 조건을 조정합니다. 성능 시험 테스트의 경우 하중이 주기적으로 적용되는 동안 플라스틱 축적이 안정화되는지를 결정하는 것이 목표입니다. 소프트웨어는 이 조건을 자동으로 확인하는 사용자 정의 프로그램을 생성할 수 있습니다. DIC 컨트롤러를 트리거하는데 사용하면 관련 데이터만 기록되고 데이터가 감소합니다. DIC 시스템은 데이터 동기화 및 수집을 위한 보완 기능도 제공합니다.
보완적인 스트레인 측정 솔루션
테스트 실험실은 더 포괄적인 재료 특성화를 제공하기 때문에 접촉 및 비접촉 스트레인 측정 솔루션을 모두 사용합니다. DIC는 샘플의 모든 가시 지점에서 스트레인 및 변형과 같은 신장계보다 훨씬 더 많은 정보를 제공합니다. 그리고 비접촉식 측정 솔루션은 샘플 크기, 실험 설정 및 재사용과 관련하여 추가적인 자유를 제공합니다. 반면 접촉식 신장계는 견고하고 신뢰할 수 있는 변형 측정 기술로 잘 알려져 있습니다. 신장계는 또한 이미지를 처리하는 데 상당한 데이터 저장 공간과 시간이 필요할 수 있는 DIC 시스템보다 더 높은 데이터 수집 속도를 자랑합니다.
Vermaak Lab에서는 테스트 시스템 및 DIC 시스템 파트너로부터 받은 엔지니어링, 응용 분야 및 통합 지원의 이점을 활용하여 이러한 시스템과의 데이터 수집, 동기화 및 분석을 정확하고 효율적으로 만듭니다.