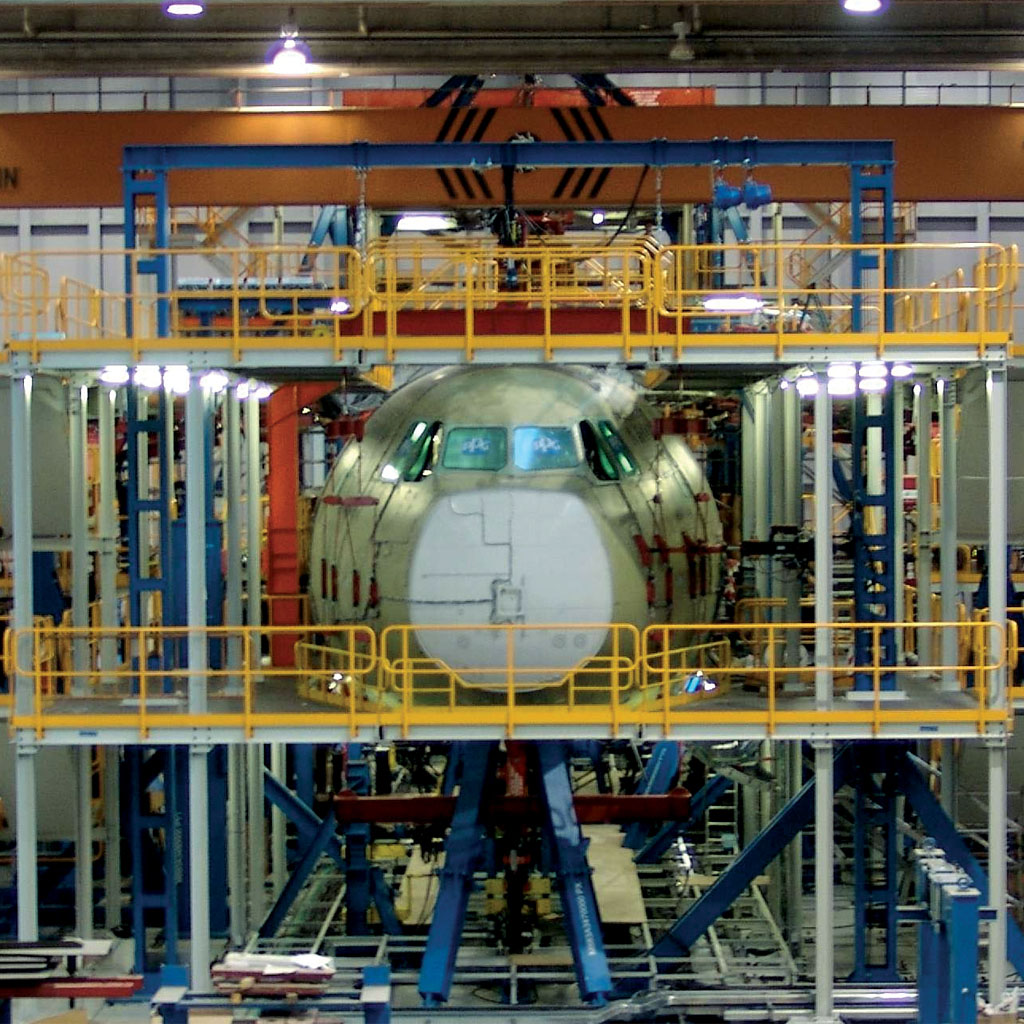
KUNDENHERAUSFORDERUNG
Airbus Military (ehemals EADS CASA-MTAD) mit Hauptsitz im spanischen Getafe war in den letzten Jahrzehnten für die Entwicklung, Produktion und Erprobung von bedeutenden Militärflugzeugen verantwortlich. Nach der Programmgenehmigung im Jahr 2003 begann Airbus mit der Arbeit am nächsten hochkarätigen Projekt: Die Entwicklung des mittelschweren militärischen Transportflugzeugs Airbus A400M.
Das viermotorige Turboprop-Flugzeug ist durch seine relativ große Größe und seine Fähigkeit, während des Fluges aufgetankt zu werden, einzigartig. Aufträge über 180 A400M-Flugzeuge sind bereits für Deutschland, Frankreich, Spanien, Großbritannien, die Türkei, Belgien, Luxemburg und Malaysia vorgesehen. Während des Entwicklungsprozesses wurde der erste maßstabsgetreue Testkörper in Getafe zusammengebaut, während gleichzeitig der Prüfstand um und im Flugzeug wuchs. Ziel war es, den kompletten Test in sechs Monaten nach der Ankunft des Flügels in Getafe von Sevilla aus aufzusetzen.
„Der Zeitplan für dieses Flugzeug ließ uns keine Zeit für Verzögerungen“, sagt Angel Gago, Leiter des Strukturtestlabors bei Airbus Military. „Während der Tests besteht unsere Herausforderung darin, ein Höchstmaß an Effizienz zu erreichen und gleichzeitig die strukturelle Integrität des Testobjekts während des gesamten Prozesses zu erhalten.“
Die Strukturtests für den Airbus A400M erfordern 120 Kontrollkanäle und mehr als 9000 Dehnungsmessstreifen, wobei 6000 Dehnungsmessstreifen gleichzeitig gelesen werden können. Außerdem müssen massive Lasten auf die Prüfkörper aufgebracht werden, um die realen Betriebsbedingungen des Flugzeugs zu simulieren. Gago wusste, dass die Aufrechterhaltung der Integrität des Prüfkörpers bei einem Aufbau mit solch hoher Komplexität und Kräften die Fähigkeit erfordern würde, das Prüfsystem mit absoluter Präzision zu be- und entlasten.
„Eine Fehlfunktion des Systems könnte uns Monate an wertvoller Entwicklungszeit zurückwerfen, wenn der Testgegenstand einen Schaden erleiden würde“, so Gago. „Solche Ausfälle sind selten, aber es war ein Risiko, das wir nicht eingehen konnten. Für uns war es wichtig, dass wir jederzeit sofort und gleichmäßig Energie kontrolliert aus dem Prüfstand abführen können.“
MTS-LÖSUNG
Die Beziehung zwischen Airbus Military und MTS begann vor mehr als 20 Jahren. „Wir haben bereits 1978 begonnen, mit MTS zusammenzuarbeiten, und fünf Jahre später hat MTS uns geholfen, unsere Tests zum ersten Mal erfolgreich in einen geschlossenen Servoregelkreis zu verlegen“, erzählt Gago. „Wir verwenden jetzt die AeroPro™-Software für alle unsere Flugzeugtests. Die integrierte Steuerung und die Datenerfassungsfunktionen von machen es uns leicht, alle unsere Testaktivitäten in Echtzeit zu verwalten.
Wir waren erfreut zu entdecken, dass MTS nicht nur eine fortschrittliche Technologie in diesem Bereich bietet, sondern dass die Technologie über dieselbe AeroPro-Softwareoberfläche verwaltet werden kann, die wir bereits verwendeten“, fügt Gago hinzu. „Die Fähigkeit von MTS, die komplette Testlösung einschließlich aller Aktuatoren, Steuerungen und Software zu liefern, ermöglichte es uns, schneller voranzukommen.“
MTS unterstützte Airbus Military bei der Ausstattung der Prüfstände für den Airbus A400M mit aktiven Lastabbruchsystemen (Active Load Abort bzw. ALA). Die ALA-Technologie trägt zur Sicherung von Prüfgegenständen bei, indem sie eine strenge Kontrolle über die Entlastung des strukturellen Prüfsystems im Fall eines Stromausfalls oder einer Systemverriegelung bietet.
Während eines solchen Ereignisses setzt das ALA-System sowohl auf Software- als auch auf Hardware-Ebene Maßnahmen ein, um alle Aktuatorlasten zum exakt gleichen Zeitpunkt in einen neutralen Zustand zu reduzieren, unabhängig von unterschiedlichen Drücken und einzelnen Aktuatorpositionen. Parallel zur Laststeuerung läuft eine separate Steuerung, die den Zustand der gesamten Prüfung bei der hydraulischen Druckentlastung des Prüfkörpers berücksichtigt. Das System erkennt einen Fehler auf der Steuerseite und arbeitet dann daran, die Last sofort und gleichmäßig vom gesamten Prüfgegenstand zu entfernen.
„MTS hat bei jedem Schritt eng mit uns zusammengearbeitet, bis unser ALA-System vollständig integriert und betriebsbereit war“, erklärt Gago. „Jetzt arbeitet dieses System durchgängig in unserem Prüflabor, das wir zusammen mit unserer Servosteuerung und Datenerfassung in der AeroPro-Umgebung verwalten.“
KUNDENVORTEILE
Laut Gago liegt der Hauptvorteil der ALA-Technologie von MTS darin, dass sie Airbus Military eine neue Denkweise darüber ermöglicht hat, wie man Prüfkörper, die bei Strukturtests verwendet werden, vor Systemfehlfunktionen oder unerwartetem Verhalten schützen kann.
„Wir haben jetzt die Gewissheit, dass unsere Prüfkörper während des Tests gut vor Schäden geschützt sind“, so Gago. „Unsere Prüfingenieure können sich auf den Test selbst konzentrieren, ohne sich Gedanken darüber machen zu müssen, wie ein unerwarteter Fehler auf dem Prüfstand ihre harte Arbeit zunichte machen könnte.“
Laut Jesus Posada, Leiter der Strukturtests bei Airbus Military, wird MTS auch beteiligt sein, wenn das Prüflabor in die nächste Phase der Ermüdungsprüfung eintritt. „Wir planen in Kürze, die Geschwindigkeit unserer Ermüdungstests zu verbessern, und wir planen, uns auf das Prüfwissen von MTS zu verlassen, um uns bei der Verbesserung dieser Art von Tests zu helfen“, sagt Posada. „Wir haben schon viel über die AeroPro-Softwaretools zur Beschleunigung der dynamischen Tests gehört und freuen uns darauf, sie in naher Zukunft in vollem Umfang nutzen zu können.“
C