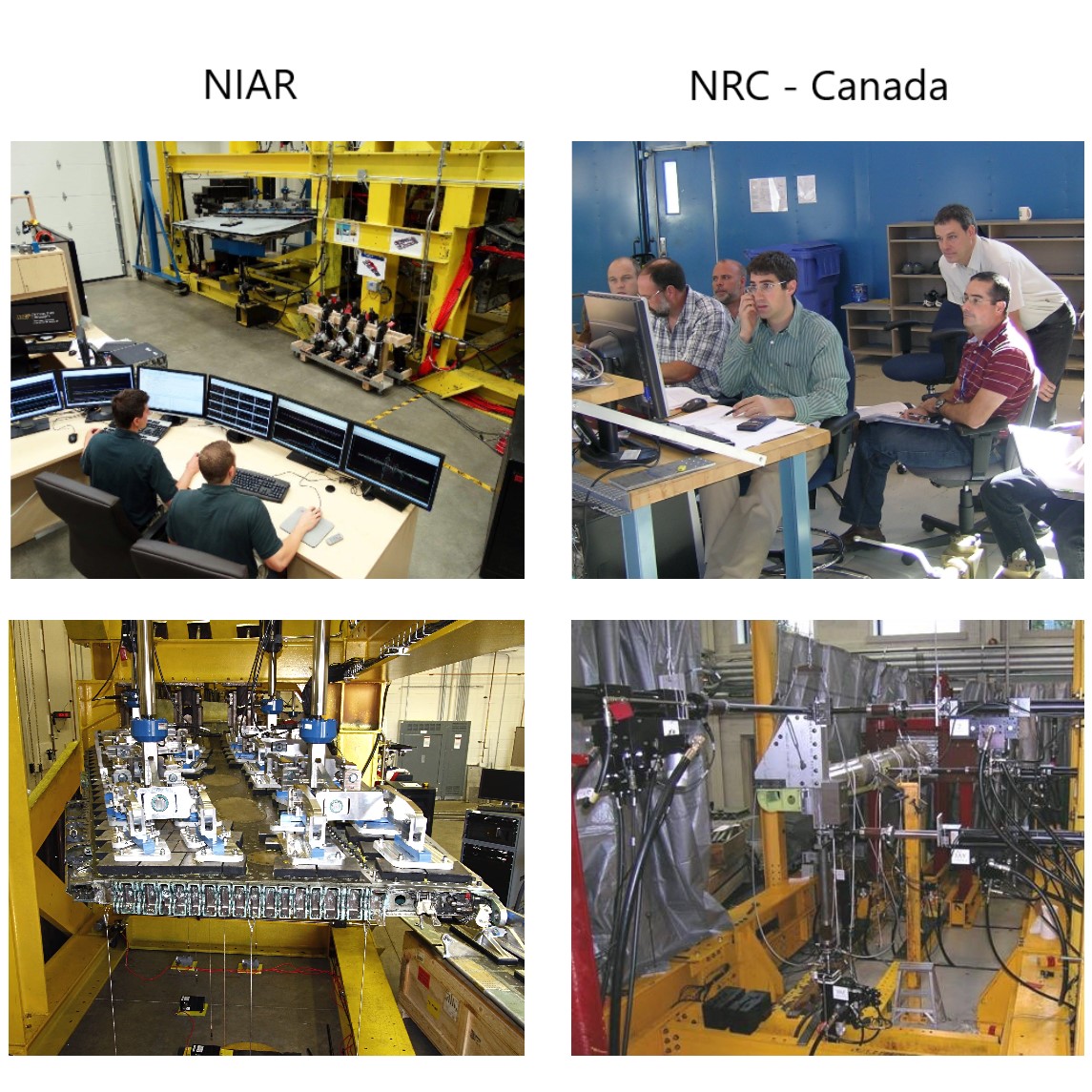
Strukturprüfstände im Maßstab 1:1, die hochgradig kreuzgekoppelte Betätigungsschemata aufweisen, stellen die Prüfingenieure in der Luft- und Raumfahrt vor besondere Herausforderungen. In diesen komplexen Konfigurationen üben mehrere Zylinder gleichzeitig unterschiedliche Kräfte auf denselben Teil eines Prüflings aus, was die Gefahr von Fehlern erhöht, die Prüfzeitpläne gefährden und Entwicklungsprogramme verzögern können.
Ein Tool zur Reduzierung solcher Fehler – und damit zur Verbesserung der Testgeschwindigkeit und -effizienz – ist C3 Performance, ein Dienstprogramm der MTS AeroPro™ Regel- und Datenerfassungssoftware. C3 Performance, auch bekannt als C hoch 3, ermöglicht es Testteams, hochgradig kreuzgekoppelte Betätigungsschemata effektiv zu verwalten, ohne zusätzliche Zeit in die Testpläne einplanen zu müssen, um zahlreiche, wiederkehrende Stopps und Verriegelungen zu lösen.
Die C3 Performance-Querkopplungs-Kompensationstechnik wurde gemeinsam von Experten des National Research Council of Canada (NRC) und der MTS Systems Corporation entwickelt. Heute ist es ein Standardbestandteil des Testprotokolls im Strukturtestlabor für den großen Maßstab des NRC of Canada, wo Andre Beltempo als Strukturtestingenieur arbeitet.
„Normalerweise verwenden wir C hoch 3 für alle Tests“, sagt Beltempo. „Bei Ermüdungstests im Originalmaßstab sieht man sehr komplexe Wechselwirkungen zwischen den Zylindern. Genau deshalb brauchen wir es.“
Das Team von Beltempo hat kürzlich C3 Performance bei einer Technologievorführung für einen großen Hubschrauberhersteller eingesetzt. Das Ermüdungs- und statische Testprogramm konzentrierte sich auf einen Heckausleger aus Verbundwerkstoff, der mit fortschrittlichen Fertigungstechniken hergestellt wurde. Die Tests waren identisch mit denen, die für die Zertifizierung des Teils für die sichere Lebensdauertoleranz nach FAA-Anforderungen verwendet wurden.
„Wenn man sich den Schnittstellenbeschlag des Heckrotorgetriebes ansieht, werden die beiden hinteren Zylinder auf denselben Beschlag geladen“, sagte Beltempo. „Die Kreuzkopplungskompensation minimiert Konflikte zwischen den Zylindern.“
Der Test umfasste sechs Zylinder und vier Millionen Endpunkte, die über Nacht für etwa 125 Tage mit einer durchschnittlichen Frequenz von 0,5 Hz liefen. Diese Testgeschwindigkeit wäre laut Beltempo ohne C3 Performance nicht möglich gewesen
„Wir hätten es ohne eine kreuzgekoppelte Kompensation nicht so schnell geschafft“, sagte er. „Für einen Test über Nacht hätten wir die Endstufen mit halber Geschwindigkeit laufen lassen müssen, um uns keine Sorgen um unbeaufsichtigte Abschaltungen machen zu müssen. Unsere Standardvorgehensweise für jeden Ermüdungstest ist es, den Test abzustimmen, C hoch 3 anzuwenden und ihn sofort wieder abzustimmen. Ich habe noch nie eine Geschwindigkeitssteigerung von weniger als einem Faktor 2 bei einem starren Prüfling gesehen.“
Ein weiterer Aspekt, den Beltempo an C3 Performance schätzt, ist die allgemeine Benutzerfreundlichkeit. Da die Prüfer es selbst einrichten können, hilft C3 Performance den Laboren, noch mehr Zeit zu gewinnen.
„Da ich nicht ständig eingreifen muss, kann ich mich auf wichtigere Aufgaben konzentrieren“, erklärte Beltempo. „Wenn Sie alle Koeffizienten selbst ermitteln müssten, wäre das etwas anderes. Aber Sie klicken einfach auf eine Schaltfläche und die Werte werden berechnet. Das ist eine echte Produktivitätssteigerung.“
Während es für die Organisation, die an der Entwicklung von C3 Performance mitgewirkt hat, selbstverständlich ist, das Programm bei jedem Ermüdungstest im Rahmen des Protokolls anzuwenden, entdecken auch andere Labore das Problemlösungspotenzial dieses leistungsstarken Programms.
Für Dr. Waruna Seneviratne, technischer Leiter im Labor für Verbundwerkstoffe und fortschrittliche Materialien am National Institute for Aviation Research (NIAR) der Wichita State University, war das Problem der Schlafmangel.
„Wir führten einen Ermüdungstest mit einer sehr ausgeprägten Kombination aus kundenspezifischer Befestigung und Betätigung durch und hatten einen sehr aggressiven Testplan“, so Seneviratne. „Der Test lief über Nacht und wir erlebten eine große Anzahl von störenden fehlerhaften Grenzwertauslösungen. Unser Team musste mitten in der Nacht ins Labor kommen, um zu sehen, was die Ursache für die Testabschaltungen war, und um den Test neu zu starten. Wir sind in Rückstand geraten.“
Der Test konzentrierte sich auf die Bewertung der Ermüdungslebensdauer von Verbundwerkstoffstrukturen der F/A-18 Hornet Flugzeuge, von denen viele kurz vor der Ausmusterung stehen. Da der Ersatz für das Flugzeug nicht vor 2019 fertiggestellt sein wird, muss die US-Marine die Lebensdauer der alternden Verbundwerkstoffstrukturen des Flugzeugs sicher verlängern.
Senevirates Forschung stellte erfolgreich fest, dass die Verbundwerkstoff-Titan-Verbindungen an der Flügelwurzel noch einsatzfähig waren. Der neue Test erweiterte die Studie auf den gesamten inneren Flügel, der eine Haut aus Verbundwerkstoff hat. Der Prüfling umfasst den Innenflügel, die Hinterkantenklappe und das Mittelrohr sowie die simulierte Vorderkantenklappe und den Außenflügel. Das NIAR-Forschungsteam musste einen aufwändigen Prüfstand aus hochfestem Stahl mit speziell angefertigten Vorrichtungen konstruieren und erhebliche Lasten aufbringen, um aggressive Manöver nachzustellen.
„Es gab signifikante Unterschiede zwischen den Hüben und Lasten der Zylinder, was eine wahrscheinliche Fehlerquelle war“, sagte er. „Wir mussten die Fehlabschaltungen minimieren und setzten uns mit dieser Aufgabe auseinander.“
Forschungsingenieur Travis Cravens, ein Mitglied des Teams von Seneviratne, kümmerte sich um die Einrichtung und Konfiguration von C3 Performance. Die System- und Applikationsingenieure von MTS haben die Installation und Schulung in weniger als einem Tag abgeschlossen, und das Labor sah fast sofort Ergebnisse.
„Am Ende des ersten Tages waren wir ohne mechanische Änderungen am Prüfstand bereits 20 Prozent schneller“, so Cravens. „C3 Performance war sehr einfach zu erlernen und einzurichten; es geschieht alles innerhalb der Software. Sie erstellen einfach eine Kreuzkopplungsmatrix, indem Sie eine Einheitslast auf jeden Lastkanal aufbringen, was nur einen zusätzlichen Schritt für jeden Zylinder darstellt.“
Um den Prüfaufbau zu rationalisieren, eliminiert C3 Performance die zeitintensive Aufgabe der manuellen Eingabe von Kreuzkopplungsdaten durch die Verwendung von Einheitslastfällen zur automatischen Generierung von Kreuzkopplungskompensationskoeffizienten. Seneviratne charakterisierte diesen Prozess mit einer treffenden Analogie.
„Es ist, als würde ein Team von 20 Leuten, die sich nicht kennen, am selben Projekt arbeiten“, sagte er. „Die Einheitslasten sind einfach eine Möglichkeit, all diese Leute miteinander bekannt zu machen, damit sie zusammenarbeiten und effizienter arbeiten können.“
Mit einer zusätzlichen Feineinstellung konnten Seneviratne und Cravens die Testrate um 24 Prozent erhöhen und die Anzahl der Stopps deutlich reduzieren.
„So konnte die Leistung unseres Tests deutlich verbessert werden“, sagte Cravens. „Mit der verbesserten Lastnachführung ist es viel unwahrscheinlicher, dass kleine Störungen in der Rückkopplung Fehlergrenzen auslösen, was zu weniger Testabbrüchen führt. Dank der Fehlerreduzierung können wir auch mehr Segmente pro Stunde ausführen.“
Vor der Verwendung von C3 Performance konnte NIAR nur maximal 375 Segmente pro Stunde erreichen, mit einem Durchschnitt von 97 Stopps und 55 Verriegelungen pro Testblock. Mit C3 Performance hat sich dies auf 480 Segmente pro Stunde mit durchschnittlich 51 Stopps und 15 Verriegelungen verbessert.
„Die Anzahl der Stopps war nur noch ein Drittel, was ein großer Gewinn für uns ist“, sagte Seneviratne. „So konnten wir den Test über Nacht laufen lassen, einige Nächte ohne eine einzige Unterbrechung. Das sind bis zu 10 Stunden Testzeit, die wir vorher nicht hatten, was uns bei unserem Zeitplan sehr geholfen hat.“Dank
C3 Performance konnte Seneviratnes Team Wochen an Arbeitszeit einsparen und die Testergebnisse rechtzeitig liefern. Darüber hinaus wurde die Produktivität des Labors erhöht: Das Team konnte nach einem besser vorhersehbaren Zeitplan arbeiten und hatte mehr Zeit, sich anderen Projekten zu widmen. In jedem Labor mit endlichen Ressourcen ist das ein wichtiger Vorteil.
„Da wir wussten, dass wir den Test über Nacht durchführen konnten und uns darauf verlassen konnten, dass die Inspektion und Reparatur tagsüber durchführbar waren, konnten wir die Effizienz unseres Testpfades erhöhen“, so Seneviratne. „Wir konnten besser planen und unsere Aktivitäten koordinieren, da wir wussten, dass der Test über Nacht unbeaufsichtigt mit minimalen Unterbrechungen lief.“
Ein Tool zur Reduzierung solcher Fehler – und damit zur Verbesserung der Testgeschwindigkeit und -effizienz – ist C3 Performance, ein Dienstprogramm der MTS AeroPro™ Regel- und Datenerfassungssoftware. C3 Performance, auch bekannt als C hoch 3, ermöglicht es Testteams, hochgradig kreuzgekoppelte Betätigungsschemata effektiv zu verwalten, ohne zusätzliche Zeit in die Testpläne einplanen zu müssen, um zahlreiche, wiederkehrende Stopps und Verriegelungen zu lösen.
Die C3 Performance-Querkopplungs-Kompensationstechnik wurde gemeinsam von Experten des National Research Council of Canada (NRC) und der MTS Systems Corporation entwickelt. Heute ist es ein Standardbestandteil des Testprotokolls im Strukturtestlabor für den großen Maßstab des NRC of Canada, wo Andre Beltempo als Strukturtestingenieur arbeitet.
„Normalerweise verwenden wir C hoch 3 für alle Tests“, sagt Beltempo. „Bei Ermüdungstests im Originalmaßstab sieht man sehr komplexe Wechselwirkungen zwischen den Zylindern. Genau deshalb brauchen wir es.“
Das Team von Beltempo hat kürzlich C3 Performance bei einer Technologievorführung für einen großen Hubschrauberhersteller eingesetzt. Das Ermüdungs- und statische Testprogramm konzentrierte sich auf einen Heckausleger aus Verbundwerkstoff, der mit fortschrittlichen Fertigungstechniken hergestellt wurde. Die Tests waren identisch mit denen, die für die Zertifizierung des Teils für die sichere Lebensdauertoleranz nach FAA-Anforderungen verwendet wurden.
„Wenn man sich den Schnittstellenbeschlag des Heckrotorgetriebes ansieht, werden die beiden hinteren Zylinder auf denselben Beschlag geladen“, sagte Beltempo. „Die Kreuzkopplungskompensation minimiert Konflikte zwischen den Zylindern.“
Der Test umfasste sechs Zylinder und vier Millionen Endpunkte, die über Nacht für etwa 125 Tage mit einer durchschnittlichen Frequenz von 0,5 Hz liefen. Diese Testgeschwindigkeit wäre laut Beltempo ohne C3 Performance nicht möglich gewesen
„Wir hätten es ohne eine kreuzgekoppelte Kompensation nicht so schnell geschafft“, sagte er. „Für einen Test über Nacht hätten wir die Endstufen mit halber Geschwindigkeit laufen lassen müssen, um uns keine Sorgen um unbeaufsichtigte Abschaltungen machen zu müssen. Unsere Standardvorgehensweise für jeden Ermüdungstest ist es, den Test abzustimmen, C hoch 3 anzuwenden und ihn sofort wieder abzustimmen. Ich habe noch nie eine Geschwindigkeitssteigerung von weniger als einem Faktor 2 bei einem starren Prüfling gesehen.“
Ein weiterer Aspekt, den Beltempo an C3 Performance schätzt, ist die allgemeine Benutzerfreundlichkeit. Da die Prüfer es selbst einrichten können, hilft C3 Performance den Laboren, noch mehr Zeit zu gewinnen.
„Da ich nicht ständig eingreifen muss, kann ich mich auf wichtigere Aufgaben konzentrieren“, erklärte Beltempo. „Wenn Sie alle Koeffizienten selbst ermitteln müssten, wäre das etwas anderes. Aber Sie klicken einfach auf eine Schaltfläche und die Werte werden berechnet. Das ist eine echte Produktivitätssteigerung.“
Während es für die Organisation, die an der Entwicklung von C3 Performance mitgewirkt hat, selbstverständlich ist, das Programm bei jedem Ermüdungstest im Rahmen des Protokolls anzuwenden, entdecken auch andere Labore das Problemlösungspotenzial dieses leistungsstarken Programms.
Für Dr. Waruna Seneviratne, technischer Leiter im Labor für Verbundwerkstoffe und fortschrittliche Materialien am National Institute for Aviation Research (NIAR) der Wichita State University, war das Problem der Schlafmangel.
„Wir führten einen Ermüdungstest mit einer sehr ausgeprägten Kombination aus kundenspezifischer Befestigung und Betätigung durch und hatten einen sehr aggressiven Testplan“, so Seneviratne. „Der Test lief über Nacht und wir erlebten eine große Anzahl von störenden fehlerhaften Grenzwertauslösungen. Unser Team musste mitten in der Nacht ins Labor kommen, um zu sehen, was die Ursache für die Testabschaltungen war, und um den Test neu zu starten. Wir sind in Rückstand geraten.“
Der Test konzentrierte sich auf die Bewertung der Ermüdungslebensdauer von Verbundwerkstoffstrukturen der F/A-18 Hornet Flugzeuge, von denen viele kurz vor der Ausmusterung stehen. Da der Ersatz für das Flugzeug nicht vor 2019 fertiggestellt sein wird, muss die US-Marine die Lebensdauer der alternden Verbundwerkstoffstrukturen des Flugzeugs sicher verlängern.
Senevirates Forschung stellte erfolgreich fest, dass die Verbundwerkstoff-Titan-Verbindungen an der Flügelwurzel noch einsatzfähig waren. Der neue Test erweiterte die Studie auf den gesamten inneren Flügel, der eine Haut aus Verbundwerkstoff hat. Der Prüfling umfasst den Innenflügel, die Hinterkantenklappe und das Mittelrohr sowie die simulierte Vorderkantenklappe und den Außenflügel. Das NIAR-Forschungsteam musste einen aufwändigen Prüfstand aus hochfestem Stahl mit speziell angefertigten Vorrichtungen konstruieren und erhebliche Lasten aufbringen, um aggressive Manöver nachzustellen.
„Es gab signifikante Unterschiede zwischen den Hüben und Lasten der Zylinder, was eine wahrscheinliche Fehlerquelle war“, sagte er. „Wir mussten die Fehlabschaltungen minimieren und setzten uns mit dieser Aufgabe auseinander.“
Forschungsingenieur Travis Cravens, ein Mitglied des Teams von Seneviratne, kümmerte sich um die Einrichtung und Konfiguration von C3 Performance. Die System- und Applikationsingenieure von MTS haben die Installation und Schulung in weniger als einem Tag abgeschlossen, und das Labor sah fast sofort Ergebnisse.
„Am Ende des ersten Tages waren wir ohne mechanische Änderungen am Prüfstand bereits 20 Prozent schneller“, so Cravens. „C3 Performance war sehr einfach zu erlernen und einzurichten; es geschieht alles innerhalb der Software. Sie erstellen einfach eine Kreuzkopplungsmatrix, indem Sie eine Einheitslast auf jeden Lastkanal aufbringen, was nur einen zusätzlichen Schritt für jeden Zylinder darstellt.“
Um den Prüfaufbau zu rationalisieren, eliminiert C3 Performance die zeitintensive Aufgabe der manuellen Eingabe von Kreuzkopplungsdaten durch die Verwendung von Einheitslastfällen zur automatischen Generierung von Kreuzkopplungskompensationskoeffizienten. Seneviratne charakterisierte diesen Prozess mit einer treffenden Analogie.
„Es ist, als würde ein Team von 20 Leuten, die sich nicht kennen, am selben Projekt arbeiten“, sagte er. „Die Einheitslasten sind einfach eine Möglichkeit, all diese Leute miteinander bekannt zu machen, damit sie zusammenarbeiten und effizienter arbeiten können.“
Mit einer zusätzlichen Feineinstellung konnten Seneviratne und Cravens die Testrate um 24 Prozent erhöhen und die Anzahl der Stopps deutlich reduzieren.
„So konnte die Leistung unseres Tests deutlich verbessert werden“, sagte Cravens. „Mit der verbesserten Lastnachführung ist es viel unwahrscheinlicher, dass kleine Störungen in der Rückkopplung Fehlergrenzen auslösen, was zu weniger Testabbrüchen führt. Dank der Fehlerreduzierung können wir auch mehr Segmente pro Stunde ausführen.“
Vor der Verwendung von C3 Performance konnte NIAR nur maximal 375 Segmente pro Stunde erreichen, mit einem Durchschnitt von 97 Stopps und 55 Verriegelungen pro Testblock. Mit C3 Performance hat sich dies auf 480 Segmente pro Stunde mit durchschnittlich 51 Stopps und 15 Verriegelungen verbessert.
„Die Anzahl der Stopps war nur noch ein Drittel, was ein großer Gewinn für uns ist“, sagte Seneviratne. „So konnten wir den Test über Nacht laufen lassen, einige Nächte ohne eine einzige Unterbrechung. Das sind bis zu 10 Stunden Testzeit, die wir vorher nicht hatten, was uns bei unserem Zeitplan sehr geholfen hat.“Dank
C3 Performance konnte Seneviratnes Team Wochen an Arbeitszeit einsparen und die Testergebnisse rechtzeitig liefern. Darüber hinaus wurde die Produktivität des Labors erhöht: Das Team konnte nach einem besser vorhersehbaren Zeitplan arbeiten und hatte mehr Zeit, sich anderen Projekten zu widmen. In jedem Labor mit endlichen Ressourcen ist das ein wichtiger Vorteil.
„Da wir wussten, dass wir den Test über Nacht durchführen konnten und uns darauf verlassen konnten, dass die Inspektion und Reparatur tagsüber durchführbar waren, konnten wir die Effizienz unseres Testpfades erhöhen“, so Seneviratne. „Wir konnten besser planen und unsere Aktivitäten koordinieren, da wir wussten, dass der Test über Nacht unbeaufsichtigt mit minimalen Unterbrechungen lief.“