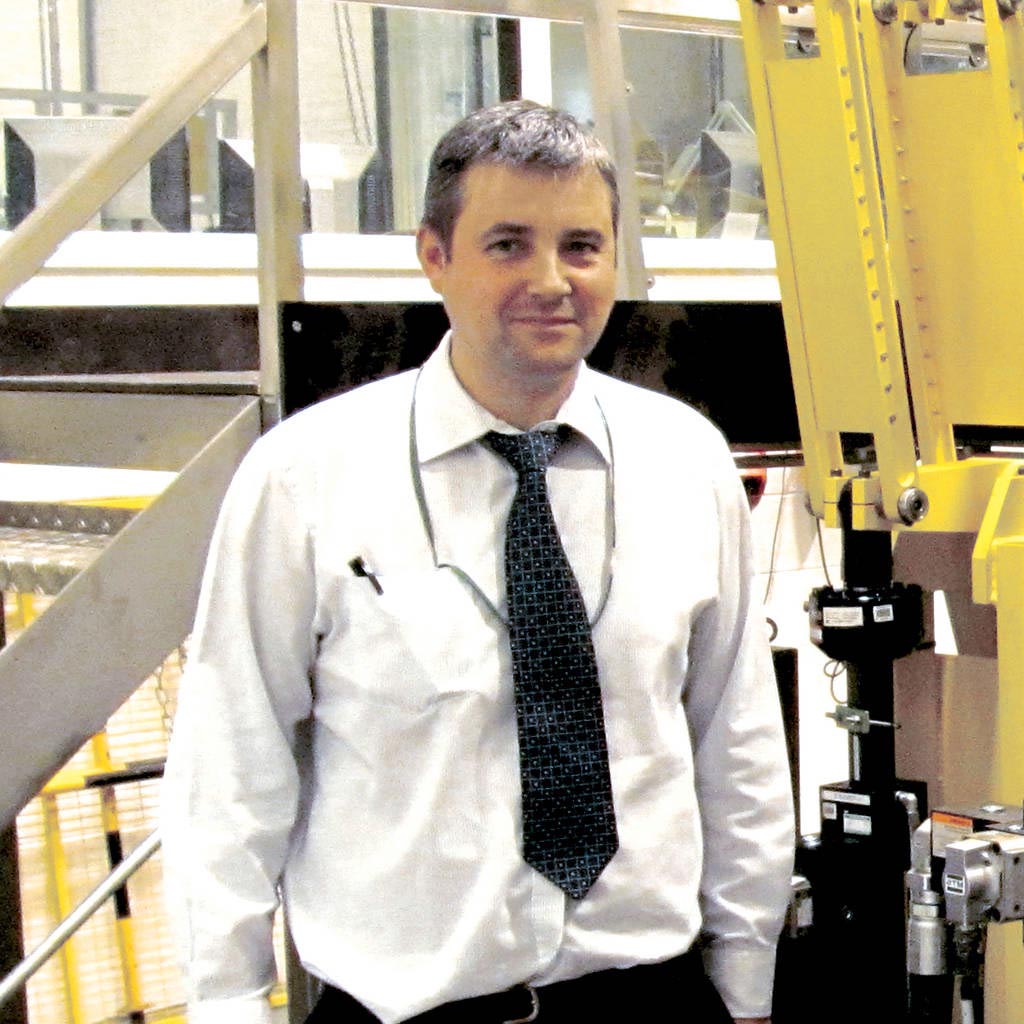
KUNDENHERAUSFORDERUNG
Jaguar Land Rover (JLR) bietet ein vielfältiges Fahrzeugportfolio und stellt einige der weltweit bekanntesten Luxusautos und Geländewagen her. Um die kontinuierliche Entwicklung dieses Portfolios zu unterstützen, sind die Strukturtestingenieure an zwei Standorten in Großbritannien damit beschäftigt, Batterien von Haltbarkeitstests an zahlreichen Komponenten, Subsystemen und Fahrzeugprototypen durchzuführen. Zu denjenigen, die diese Bemühungen leiten, gehört Ian Payne, Gruppenleiter für Produktanalyse und -verifizierung. Paynes Team ist für die Prüfstände verantwortlich, mit denen die Festigkeit und Ausdauer aller JLR-Produkte von der Komponentenebene bis zur vollständigen Fahrzeugsimulation bewertet wird.
„Wir konstruieren, fertigen und betreiben in allen unseren Laboren Geräte, die von einachsigen Prüfständen bis hin zu hochmodernen Vollfahrzeug-Straßensimulatoren reichen“, so Payne. „Wir liefern die Grundlage für die Überprüfung der Haltbarkeit von Fahrzeugen. Die Daten, die wir sammeln, unterstützen die Produktentwicklung im gesamten Unternehmen.“
Eine der größten Herausforderungen für Payne ist der ständige Druck, bessere Ergebnisse in kürzerer Zeit zu erzielen und die Markteinführung von neuen Produkten zu beschleunigen. Daher suchen Payne und sein Team nach jeder Möglichkeit zur Verbesserung der Genauigkeit und Effizienz der Tests. Eine Möglichkeit, das Problem anzugehen, ist die Testintegration – die Kombination mehrerer diskreter Tests in einer einzigen, datenreichen Simulation.
„Die oberste Priorität für uns ist die Optimierung der Testzeit“, sagte Payne. „Der Nachteil ist, dass die Tests immer komplexer werden. Es ist sehr schwierig, all die aktiven Systeme unserer Fahrzeuge - wie variable Dämpfung, aktives Wanken und aktive Differenziale – zu simulieren und all diese Komplexität in einen Echtzeittest einzubauen.“
MTS-LÖSUNG
Heute löst JLR diese Herausforderung mit zwei MAST-Systemen (Multi-axial Simulation Table) von MTS. Paynes Team nutzt die MAST-Systeme, um die strukturelle Belastbarkeit kompletter Motoraufhängungssysteme, einschließlich des Antriebsstrangs und des Antriebsstrangs, mit Karosserieeingaben, strukturellen Motoraufhängungslasten und Echtzeit-Drehmomenten zu verifizieren, die durch Drehmoment-Eingabevorrichtungen geliefert werden.
„Wir führen Echtzeitsimulationen durch, um die strukturelle Belastbarkeit über die korrelierte voraussichtliche Lebensdauer des Fahrzeugs zu ermitteln“, so Payne. „Mit den MAST-Systemen von MTS können wir das gesamte Motorlagerungssystem auf einmal betrachten. So können wir auch die Fahrzeuggehäuse betrachten, einschließlich der Gehäuse unter der Motorhaube und des Kabelbaums. Es ist ein großartiges Werkzeug für uns.“
Die MTS MAST-Systeme sind sowohl in orthogonaler als auch in Hexapod-Konfiguration erhältlich und wurden entwickelt, um die Schwingungsphänomene realer Betriebsumgebungen in kontrollierten Laborumgebungen genau nachzubilden. Die orthogonalen Systeme, die von Paynes Team eingesetzt werden, verfügen über quadratische, resonanzfreie 2 x 3 Meter große Tische und sind in der Lage, sechs Freiheitsgrade (6DOF) zu simulieren – drei vertikale Zylinder führen vertikale, Nick- und Rollbewegungen aus, während drei horizontale Zylinder laterale, Gier- und Längsbewegungen ausführen.
„Wir belasten den Antriebsstrang direkt, typischerweise in Längs- und Querrichtung und gelegentlich auch in der Vertikalen, um die korrekte mittlere Belastung der Motorlager während der Tests zu gewährleisten“, so Payne. „Es ist ein ziemlich großer Tisch. So können wir ein komplettes 4x4-Frontantriebsystem mit dem V8-Motor kombinieren. Wir betreiben den Tisch mit Frequenzen bis zu 30 Hz und das Antriebsmoment bis zu 20 Hz.“
KUNDENVORTEILE
Laut Payne sind die MTS MAST-Systeme unerlässlich, um viele ehemals getrennte Tests zu einem einzigen zusammenzufassen. Insbesondere das robuste Design und die hohe Nutzlast des MAST-Systems ermöglichen es dem Team von Payne, die Prüflingsmasse zu maximieren, während die präzise 6DOF-Bewegungssteuerung alle Testmöglichkeiten bietet, die für das gesamte Spektrum der Prototypenverifizierung erforderlich sind.
„Wir versuchen, so viele Tests wie möglich in einen einzigen physischen Prototyp zu packen“, sagte Payne. „Es ist zwar komplexer, aber wir sparen tatsächlich sehr viel Zeit bei der Entwicklung. Der Test ist auch robuster, weil die Systeminteraktionen alle zusammenarbeiten, was viel realistischer ist.“
Mehr Realismus bedeutet, dass ein einziger MAST-Test Licht auf viele der Fehler werfen kann, die die JLR-Teams in der realen Welt erwarten, sobald die Prototypen auf der Teststrecke sind. Das Verstehen und Beheben dieser Fehler vor der Erprobung verbessert die Effizienz und verkürzt die Zeit bis zur Marktreife.
„Mit einem 6DOF-Test erhalten wir einen großartigen Einblick in die strukturelle Belastbarkeit des gesamten Fahrzeugs“, so Payne. „Das MAST-System ist fantastisch für diese Arbeit. Im Hinblick auf die Kombination von Tests und die Erstellung komplexerer Vollfahrzeugsimulationen wird unser Fokus vorerst auf dem MAST-System und 6DOF-Tests liegen.“
Testsysteme sind natürlich nur ein Teil der Gesamtlösung. MTS bietet außerdem branchenführende Prüfsoftware sowie fachkundigen Service und Support, auf den sich das Team von Payne verlassen kann.
„Wir bekommen großartige Unterstützung von MTS“, sagte Payne. „Wir haben gute Beziehungen zu jedem im MTS-Team und wir haben großen Respekt vor dem Fachwissen, das die Außendiensttechniker mitbringen. Ihr technisches Wissen wird sehr geschätzt und wird sehr wertvoll sein, wenn wir weiter voranschreiten.“