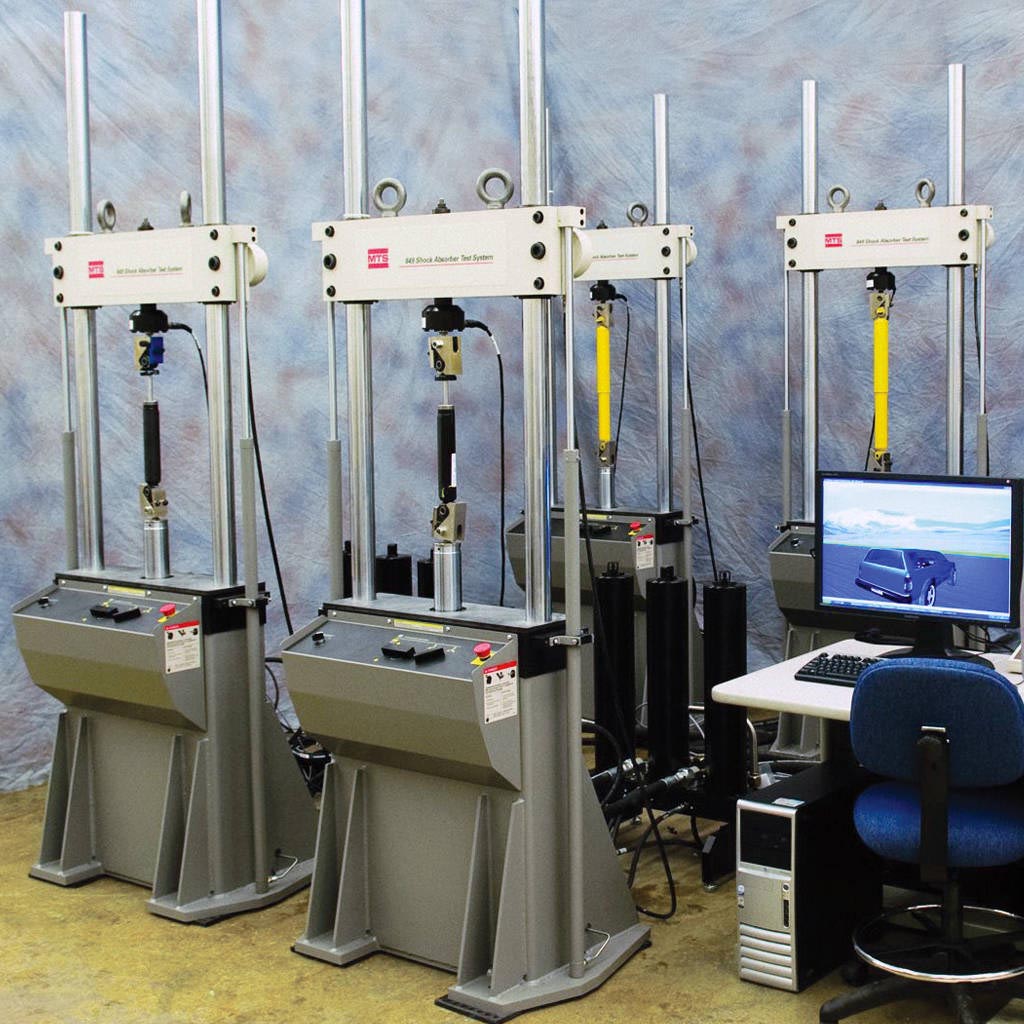
KUNDENHERAUSFORDERUNG
Nissan® strebt danach, die Nachfrage der Verbraucher nach Produkten mit hoher Qualität und hoher Leistung zu erfüllen. Um diese Anforderungen zeitnah zu erfüllen, ist nicht nur eine effektive Entwicklung, sondern auch eine effiziente Validierung erforderlich, um kostspielige und zeitraubende Iterationen zwischen den beiden Aktivitäten zu vermeiden. Die kontinuierliche Verbesserung von Werkzeugen und Methoden ist besonders wichtig im Zusammenhang mit der Erreichung der Vorgaben bezüglich der Fahrzeugdynamik, bei der die Ingenieure laufend versuchen, in einem früheren Stadium der Entwicklung einen tieferen Einblick in die Leistung der in den Fahrzeugen verwendeten Subsysteme zu erhalten.
Während computergestützte Konstruktionswerkzeuge (CAE) eine rechtzeitige Leistungsvorhersage ermöglichen, was zu einer Reduzierung der Entwicklungszeit und -kosten führt, verhindern bestimmte Einschränkungen, dass diese Werkzeuge unerwartete oder unbekannte Phänomene während der Entwicklung aufdecken. Das Aufschieben der Entdeckung von unerwarteten Phänomenen auf die Strecke birgt die Gefahr, dass Budgets und Zeitpläne beeinträchtigt werden. Eine Möglichkeit, die mit der späten Entdeckung verbundenen Risiken zu vermeiden, ist die Ergänzung von CAE durch physikalische Tests während der Entwicklung. Dies verspricht eine bessere Leistungsbewertung und einen geringeren Bedarf an Prototypen, was zu geringeren Kosten führt.
Die Automobilingenieure von Nissan Motor Co., Ltd. wollten innerhalb eines Kalenderjahres vom Design Freeze zum Produktionsstart übergehen können. Um dieses Ziel zu erreichen, müssten die komplementären Stärken von CAE und Testverfahren ausgebaut werden, einschließlich eines gründlichen Verständnisses, wie die Teilsysteme des Fahrzeugs funktionieren und sich gegenseitig beeinflussen. Um solch aggressive Entwicklungszeiträume einhalten zu können, müsste dieses Verständnis lange vor der Verfügbarkeit des Fahrzeugprototyps erlangt werden.
Zu dieser Zeit war das Unternehmen gerade dabei, ein neues Dämpfersystem zu entwickeln und wollte untersuchen, wie dieses Teilsystem genauer und in einem früheren Entwicklungsstadium getestet werden könnte. Nach einer kurzen Erkundungsphase entschied sich Nissan für eine Partnerschaft mit MTS, unter anderem aufgrund der 40-jährigen weltweiten Marktführerschaft des Unternehmens im Bereich der Fahrzeugprüftechnologie und -expertise.
MTS-LÖSUNG
MTS arbeitete eng mit Nissan zusammen, um die Mechanical-Hardware-in-the-Loop™ (mHIL)-Technologie einzusetzen, die Leistungsbewertungen des Fahrzeugs ermöglicht, bevor der vollständige Fahrzeugprototyp verfügbar ist.
Die mHIL-Technologie von MTS erweitert die weit verbreitete Hardware-in-the-Loop (HIL)-Technologie, die für die Validierung von elektronischen Steuergeräten (ECUs) verwendet wird, indem sie mechanische Systeme oder Komponenten in die Schleife eines Echtzeit-Fahrzeugmodells platziert. Da die mHIL-Technologie reale Teile verwendet, ist sie sensibler als CAE allein, was zu effektiveren Entwicklungsentscheidungen führt. Darüber hinaus können die Ingenieure dank der mHIL-Technologie diese Teile in einer virtuellen Umgebung fahren, was die Fehlersuche und die Vermeidung von Problemen in einem viel früheren Stadium der Fahrzeugentwicklung ermöglicht. Diese Fähigkeit führt zu robusteren Prototypen – und letztlich zu effizienteren Validierungs- und Nachverfolgungsarbeiten.
MTS und Nissan starteten ein Pilotprogramm mit der mHIL-Technologie zur Validierung der Leistung der neuen Dämpfersysteme, die bei Nissan entwickelt werden. Aus diesem Pilottestsystem wurde schließlich das MTS Vier-Ecken-Dämpfertestsystem, das derzeit von den Nissan-Ingenieuren verwendet wird. Die Pilotergebnisse zeigten eine hervorragende Korrelation der Testdaten mit den tatsächlichen Streckentests zur Analyse von Fahrkomfort und Handling. Durch den Einsatz des MTS-Vier-Ecken-Dämpfertestsystems konnte Nissan eine 40-prozentige Reduzierung der rückläufigen Änderungen an seinen in der Entwicklung befindlichen Fahrzeugen feststellen.
KUNDENVORTEILE
Mit dem MTS-Vier-Ecken-Dämpfertestsystem mit mHIL-Technologie kann Nissan Probleme, die durch unerwartetes Verhalten von Subsystemen entstehen, bereits in einem frühen Stadium der Fahrzeugentwicklung erkennen und lösen. Die Technologie spart Nissan viel Zeit und Geld, da unerwartete Phänomene aufgedeckt werden, die bisher erst auftraten, wenn ein Prototyp auf einer Teststrecke gefahren wurde.
„Mit der mHIL-Technologie von MTS können wir unbekannte Punkte der Qualitätsfunktionsentwicklung (QFD) bereits in der Vorbereitungsphase aufdecken und lösen, wodurch sich unsere Fahrzeugtestzeit um mindestens einen Monat verkürzt“, so Yoichi Sakai, leitender Vertreter für die experimentelle Systementwicklung bei Nissan. „In einer Zeit, in der viele Hersteller ihre Entwicklung von Versuchsfahrzeugen reduzieren, bietet uns die mHIL-Technologie eine schnelle, genaue und kostengünstige Möglichkeit, diese Initiativen weiter zu verfolgen.
„Darüber hinaus können wir dank der durch die mHIL-Technologie erreichte Effizienz den Verbrauchern höherwertige Fahrzeuge zu einem günstigeren Preis anbieten“, fügte Herr Sakai hinzu.
Im Jahr 2008 erhielten MTS und Nissan Motor Co., Ltd. den Development Tool of the Year Award des Vehicle Dynamics International Magazine für ihre gemeinsame Arbeit bei der Entwicklung des Vier-Ecken-Dämpfungssystems mit mHIL-Technologie.
„Die mHIL-Technologie stellt eine echte Revolution in der Geschwindigkeit und Kosteneffizienz der Fahrzeugentwicklung dar“, sagte Herr Sakai. „Es war für Nissan extrem vorteilhaft, und es wird sicherlich für die Zulieferer ebenso vorteilhaft sein.“