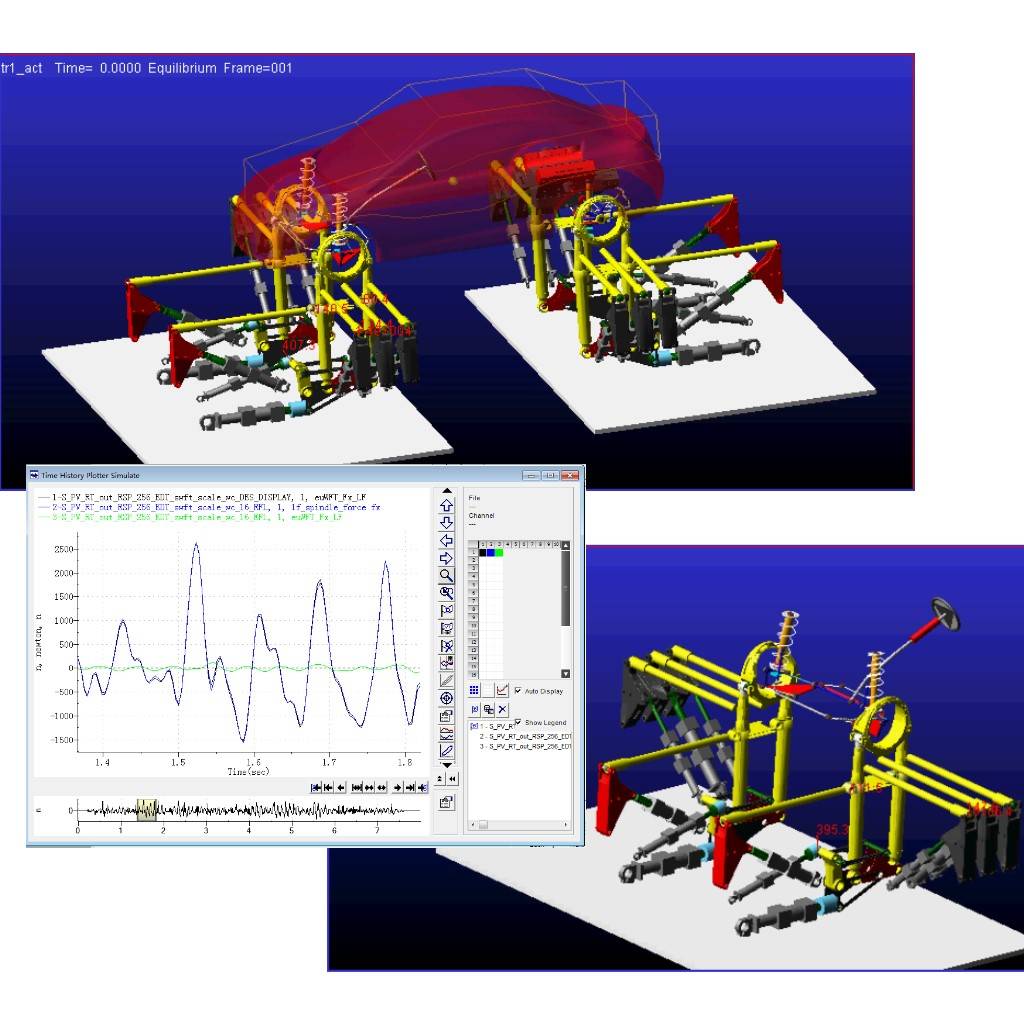
Unter dem ständigen Druck, die Entwicklungszyklen zu verkürzen und die Kosten zu senken, suchen Automobilhersteller zunehmend nach Möglichkeiten, mit Analysewerkzeugen aussagekräftige virtuelle Bewertungen von Fahrzeugdesigns frühzeitig durchzuführen, lange bevor physische Prototypen zur Verfügung stehen. Die Möglichkeit, auf diese Weise genaue vorhergesagte – oder berechnete – Lasten zu erhalten, erhöht die Effektivität der physikalischen Prüfung von Komponenten, ermöglicht eine frühzeitige Identifizierung und Beseitigung von Konstruktionsfehlern, reduziert den Bedarf an Nacharbeit und die Abhängigkeit von Prototypen und rationalisiert die Konstruktionsvalidierung.
Es wurden verschiedene Simulationsansätze entwickelt, um bereits zu einem früheren Zeitpunkt im Fahrzeugentwicklungsprozess genaue berechnete Lasten zu erhalten. Bei einer Methode, dem Virtual Proving Ground, wird ein Fahrzeugmodell über eine digitalisierte Straße „gefahren“. Dieser Ansatz hat zwar den Vorteil, dass er sich vollständig auf virtuelle Modelle stützt, führt aber zu ungenauen Lasten, die sich nur schwer durch physikalische Tests validieren lassen. Bei der semianalytischen Methode hingegen wird das Fahrzeugmodell mit Spindellasten angeregt, die von einem vorhandenen Fahrzeug erfasst werden. Dies liefert bessere Ergebnisse als die virtuelle Teststrecke, legt aber Randbedingungen fest, die für das Fahrzeugmodell nicht ganz angemessen sind, sodass die berechneten Lasten immer noch falsch und schwer zu validieren sind. Eine dritte Methode, das virtuelle Testen, überwindet diese Probleme, indem zur Anregung des Fahrzeugmodells ein Modell eines tatsächlichen physikalischen Testsystems in die Simulation integriert wird.
Virtuelles Testen ist die Simulation eines physikalischen Tests unter Verwendung von Finite-Elemente-Analysetools, Tools zur dynamischen Mehrkörperanalyse und RPC-Iterationstechniken, um sehr früh im Entwicklungsprozess genaue Lasten, Bewegungen und Schadensinformationen eines Fahrzeugsystems abzuleiten. Dieser Ansatz hat zahlreiche Vorteile. Erstens: Da es einfacher ist, die Randbedingungen eines physikalischen Testsystems zu modellieren als Bodenflächen oder Reifen zu testen, werden durch virtuelle Tests weitaus effektivere Randbedingungen geschaffen als bei den anderen Methoden. Zweitens bietet das virtuelle Testen lein ganzes Arsenal bewährter, gut etablierter physikalischer Testwerkzeuge und -techniken, die sich im Bereich der Analyse als nützlich erwiesen haben. Und drittens vereinfacht die Einbindung eines modellierten physikalischen Testsystems die Validierung der Ergebnisse durch anschließende physikalische Tests und verbessert physikalische Testaufbauten und Vorrichtungsdesigns. Das virtuelle Testen überspannt die analytischen und physikalischen Testdisziplinen und erfordert fortgeschrittene Kenntnisse sowohl der CAE-Tools als auch des physikalischen Testens, die Entwicklung eines Prozesses zur Verknüpfung von RPC Pro-Software und Analysemodellen und vorzugsweise ein gewisses Maß an Erfahrung im virtuellen Testen.
Seit Jahren konzentriert sich MTS auf die Verfeinerung des virtuellen Testansatzes und führt eine Vielzahl von Demonstrationsprojekten mit wichtigen Kunden wie Hyundai Motor Company (HMC) und Thermo King durch, um verschiedene Methoden zu evaluieren. Diese Projekte umfassten virtuelle Tests von kompletten Fahrzeugen und Subsystemen, die alle eine zufriedenstellende Korrelation mit gemessenen Straßenbelastungsdaten (RLD) oder tatsächlichen physischen Tests ergaben. Die grundlegende Methodik, die aus diesen Erfahrungen gewonnen wurde, umfasst die folgenden Schritte: 1) Verbinden der Prüfstandsmodelle mit Prüflingsmodellen 2) Koppeln der Modelle mit RPC Pro 3) Reproduzieren der Straßenbelastungsdaten auf dem virtuellen Prüfstand 4) Extrahieren der berechneten Lasten 5) Erstellen der physikalischen Komponenten-/Subsystemtest
Ein kürzlich durchgeführtes Demonstrationsprojekt mit dem State Automotive Institute of China (SAIC) ist ein hervorragendes Beispiel für diese Methodik in der Praxis:
- Verbinden der Prüfstandsmodelle mit Prüflingsmodellen
Zu Beginn des Projekts erstellte MTS eine Sammlung von Prüfstandsmodellen in den Formaten ADAMS, Simulink und ADAMS-Simulink Co-Simulation. Zu den MTS-Prüfständen, die modelliert wurden, gehörten verschiedene spindelgekoppelte Straßensimulatoren des Modells 329, ein mehrachsiges Simulationstischsystem (MAST) des Modells 353.20 und ein TestLine-Komponentenprüfsystem. Ausgewählte Prüfstandskomponenten wurden ebenfalls modelliert, darunter ein digitaler FlexTest-Regler, MTS-Aktuatoren und Servoventile sowie eine Aktuator-Transformation, die Aktuatorverschiebung, -beschleunigung und -kraft in DOF-Verschiebung, -Beschleunigung und -Kraft umwandelt. Aufgrund der zeitlichen Beschränkungen des Projekts und der relativ langsamen Simulationsgeschwindigkeiten der komplexeren Co-Simulationsmodelle wurde das ADAMS/Car 329-Modell mit den SAIC-Modellen für das Gesamtfahrzeug, die Vorderradaufhängung und die Hinterradaufhängung gekoppelt und schließlich für den Großteil der virtuellen Tests verwendet.
- Koppeln der Modelle mit RPC Pro
Ein virtueller Testserver wurde entwickelt, um die RPC Pro-Software und das ADAMS/Car 329-Modell zu verbinden. Während des Tests verwendet RPC Pro diesen virtuellen Server, um Drive-Dateien an das ADAMS-Modell zu senden, die ADAMS-Simulation zu initiieren und die Response-Datei aus dem ADAMS-Ordner in das RPC Pro-Arbeitsverzeichnis zu kopieren. Zusätzlich wurde ein bereits in RPC Pro vorhandenes Matlab Interface Tool verwendet, um RPC Pro mit den Co-Simulationsmodellen zu koppeln.
- Reproduzieren der Straßenbelastungsdaten auf dem virtuellen Prüfstand
Daraufhin wurden mit der RPC-Iterationstechnik Daten zur Straßenbelastung (Spindelkraft) reproduziert, die auf dem Testgelände für eine Vielzahl von ausgewählten Ereignissen und Manövern gesammelt wurden. Interessanterweise zeigten die ersten RPC-Iterationen auf den virtuellen 329-Prüfständen keine Konvergenz, was auf Fehler im SAIC-Fahrzeugmodell schließen lässt. Bei der anschließenden Analyse des Modells wurden tatsächlich Mängel festgestellt, die in kurzer Zeit behoben wurden. Mit dem verbesserten Modell konvergierten die RPC-Iterationen schließlich und zeigten eine ausgezeichnete Korrelation zwischen gewünschten und erreichten Signalen sowie niedrige RMS-Fehler über alle Kanäle hinweg, sowohl für die virtuellen Voll- als auch Teilfahrzeugsimulationen.
- Extrahieren der berechneten Lasten
Nach der Konvergenz der RPC-Iterationen können die berechneten Lasten für jede mechanische Komponente oder jedes Subsystem als Funktion der Zeit aus dem Fahrzeugmodell abgerufen werden.
- Physikalische Testerstellung
Die aus dem Fahrzeugmodell extrahierten Lastzeitverläufe wurden dann zur Definition der nachfolgenden physikalischen Komponententests verwendet. Sobald feststeht, ob ein Teil einer einachsigen oder mehrachsigen Belastung ausgesetzt ist, kann das RPC Pro-Arsenal an Prüfmethoden und Werkzeugen zur Definition deutlich beschleunigter Komponententests verwendet werden. Für einachsig belastete Komponenten können die Block Cycle-Methode oder die Power Spectrum Density (PSD)-Methode verwendet werden. Bei mehrachsig belasteten Bauteilen kann das Spitzenwerteabschnittverfahren angewendet werden. Für Situationen, in denen die Belastungshäufigkeit eines Bauteils beibehalten werden muss, ist die Methode der Zeitverlaufsreproduktion am besten geeignet; für diese Arten von Tests bietet RPC Pro die ermüdungsempfindliche Bearbeitung, die Dauerhaltbarkeitstests um einen Faktor von 2 bis 10 zu beschleunigen kann. Sobald die Belastungssignale für jede Komponente bestimmt sind, kann dasselbe physische Testsystem, auf dem die virtuellen Prüfstände basierten, zur Durchführung des Komponententests verwendet werden. Darüber hinaus kann eine Vielzahl von Kompensationstechniken in RPC Pro, wie z. B. die Spitzenwertkompensation, die adaptive invertierte Kompensation und die RPC-Iteration, verwendet werden, um sicherzustellen, dass die gewünschten Belastungsbedingungen während der physikalischen Prüfung genau erreicht werden.
Die fortlaufende Erforschung der virtuellen Tests durch MTS zeigt, dass sie ein effektives Mittel zur genauen Vorhersage von Bauteilbelastungen vor der Entwicklung von physischen Teilen oder Prototypen sind. Sobald diese berechneten Lasten ermittelt wurden, können dieselben RPC Pro-Tools und -Techniken, mit denen sie ermittelt wurden, zur Erstellung und Durchführung der physikalischen Tests verwendet werden, die zur Validierung ihrer Genauigkeit und der Genauigkeit des Fahrzeugmodells erforderlich sind. Die potenziellen Auswirkungen eines effektiven virtuellen Tests auf die Fahrzeugentwicklung sind erheblich. Die Verfügbarkeit von genauen Belastungsvorhersagen und anschließende frühere physikalische Tests minimieren die Nacharbeit an Komponenten und Subsystemen, reduzieren den Bedarf an mehreren Prototypen und beschleunigen die Designvalidierung. Auch die Rolle der physikalischen Prüfung wird sich weiterentwickeln: Während Tests weiterhin für die endgültige Validierung eines Fahrzeugdesigns notwendig sein werden, werden sie zunehmend auf die Validierung der Genauigkeit des Fahrzeugmodells zugeschnitten sein. Und schließlich wird das virtuelle Testen die Integration von Analyse- und physischen Testdisziplinen und -kulturen vorantreiben, was zu neuen Effizienzen durch die gemeinsame Nutzung von Werkzeugen, Prozessen und Erfahrungen führen wird.
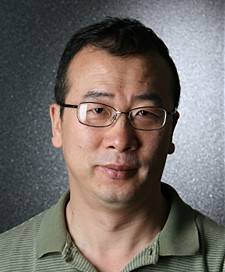