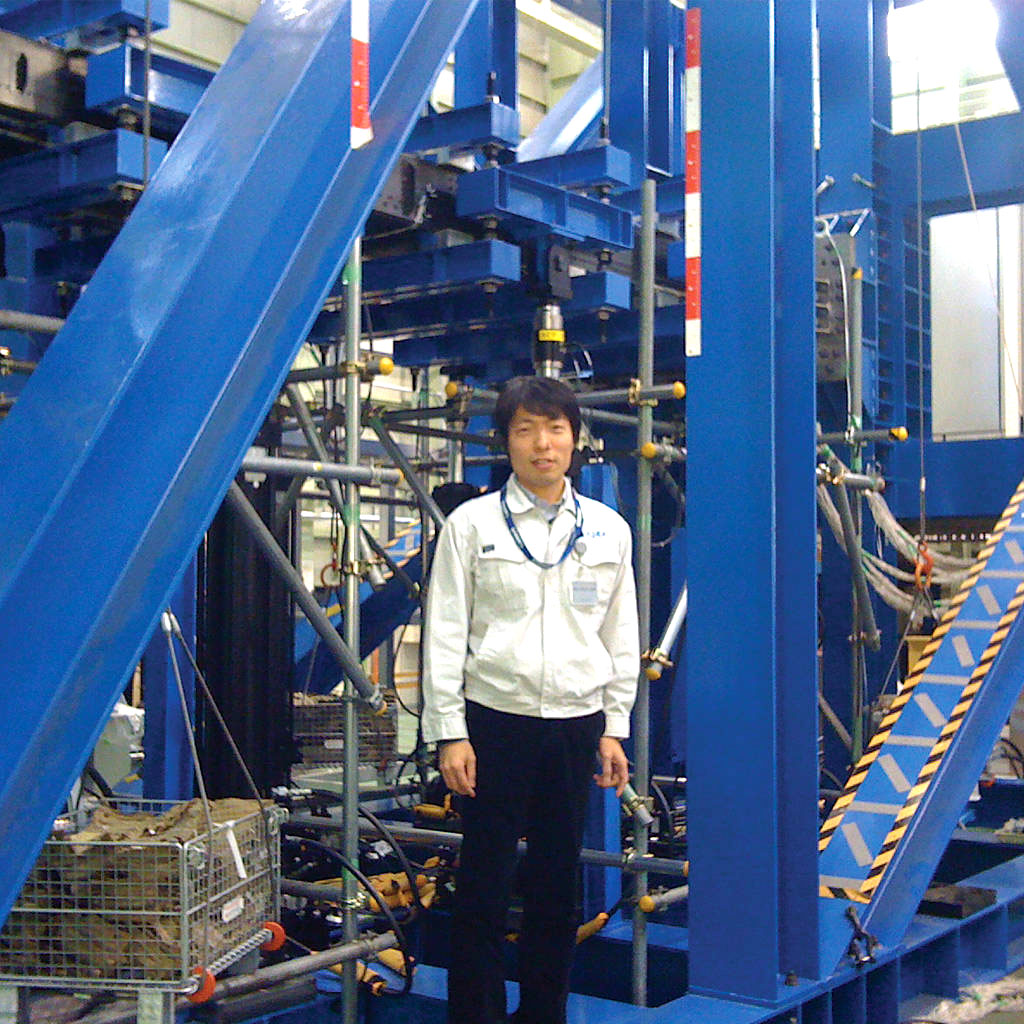
KUNDENHERAUSFORDERUNG
Im Rahmen ihrer Mission, die Forschung in der Luft- und Raumfahrt voranzutreiben, entwickelt die Japan Aerospace Exploration Agency (JAXA) innovative Technologien und Bewertungsmethoden zur Verbesserung der Qualität und zur Senkung der Kosten von Flugzeugmaterialien, Komponenten und Strukturen. Für Passagierflugzeuge bedeutet Qualität Sicherheit. Folglich muss das JAXA Civil Transport Team, Aviation Program Group, absolut sicher sein, dass alle von eingeführten Produktionsmethoden nicht nur die Kosten reduzieren, sondern auch Produkte hervorbringen, die den höchsten Anforderungen an Haltbarkeit, Festigkeit und Zuverlässigkeit entsprechen.
Steigende Treibstoffkosten und ein globaler Fokus auf Energieeinsparung haben zu einer starken Nachfrage nach leichteren Flugzeugen geführt, die weniger Treibstoff verbrauchen. Die zur Erreichung dieses Ziels eingesetzten Verbundwerkstoff-Komponenten und -Strukturen sind jedoch in der Regel teurer in der Herstellung als ihre konventionellen Gegenstücke aus Aluminium. Dr. Yuichiri Aioki und seine Advanced Composite Group haben sich vorgenommen, dieses Dilemma zu lösen. Insbesondere konzentrierte sich das Team auf die neue Fertigungstechnologie des vakuumgestützten Harzspritzspressens (VaRTM), um deren Potenzial für die kostengünstige Herstellung von Verbundwerkstoff-Komponenten und -Strukturen zu erforschen. Sie entdeckten, dass mit dem innovativen Harzspritzverfahren Verbundwerkstoffteile hergestellt werden können, die nicht nur 20 % weniger wiegen, sondern auch 20 % weniger kosten als Produkte, die mit herkömmlichen Methoden hergestellt werden. VaRTM reduzierte die Kosten und das Gewicht der Teile im Vergleich zu den typischen autoklavierten Prepreg-Prozessen, indem es ein stromlinienförmigeres, einseitiges Spritzgießen ohne Autoklav verwendet, um größere, komplexere Verbundstrukturen mit weniger Teilen zu formen.
Nachdem Dr. Aioki und sein Team die Effektivität von VaRTM als kostengünstiges Produktionsverfahren bewiesen hatten, mussten sie als nächstes beweisen, dass die mit dem VaRTM-Verfahren hergestellten Teile den komplexen Belastungen standhalten, denen Flugzeuge im Flug ausgesetzt sind. Ein wesentlicher Bestandteil dieser Aufgabe war die mechanische Prüfung. Die von JAXA ausgewählten mechanischen Testlösungen mussten flexibel genug sein, um die Anforderungen der geforderten Tests zu bewältigen, und sie mussten in der Lage sein, das hohe Maß an Kontrolle zu liefern, das erforderlich ist, um die multiaxialen Anforderungen der realen Simulation zu erfüllen.
JAXA entschied sich schließlich für die Zusammenarbeit mit MTS und laut Dr. Aioki fiel die Wahl leicht. „MTS ist ein Technologieführer mit einer nachgewiesenen Erfolgsbilanz bei Testlösungen für Flugzeugkomponenten“, sagte er. „Das Unternehmen verfügt außerdem über das nötige Fachwissen, um uns präzise und sicher bei der Erfüllung unserer einzigartigen Anforderungen zu unterstützen.“
MTS-LÖSUNG
Das Ziel des mechanischen Testprogramms der JAXA war es, die mit VaRTM erzeugten Verbundwerkstoffteile den anspruchsvollen Bedingungen des realen Fluges zu unterziehen, einschließlich steiler Höhenunterschiede. Das Programm umfasste sowohl Ermüdungstests an Teilkomponenten als auch statische Tests an einem Flügel in Originalgröße. MTS unterstützte JAXA bei der Erreichung dieses Ziels mit seinem Angebot an präzisen digitalen Steuerungen, robusten Lastrahmen und Aktuatoren, fortschrittlicher Anwendungssoftware und fachkundigem Service und Support.
Für die Ermüdungstests an den Unterkomponenten lieferte MTS einen servohydraulischen Lastrahmen des Modells 311.41 (2500 kN), der mit hydraulischen Spannzeugen des Modells 647.200 mit hoher Kraft für breite Plattenprüflinge ausgestattet war. Das System besteht aus einem vielseitigen digitalen Regler FlexTest® 40 und einem PC mit der Software Multi-Purpose TestWare®.
Die Ausrüstung für die statische Prüfung des maßstabsgetreuen Flügels umfasste vier kompakte servohydraulische MTS-Aktuatoren, die von einem leistungsstarken digitalen FlexTest 200-Regler und einem Client-PC mit AeroPro™ Regelungs- und Datenerfassungssoftware gesteuert wurden.
Neben der leistungsstarken Hard- und Software waren für Dr. Aioki auch die Kalibrierungsdienste von MTS und die Schulungen vor Ort entscheidend für den Erfolg seines Teams. „Der Kalibrierservice von MTS war wichtig, damit wir die Daten des Experiments nachvollziehen konnten. Bei Flugzeugtests ist die Rückverfolgbarkeit der Testdaten streng geregelt – Daten, die nicht rückverfolgbar sind, werden nicht zugelassen.“ In Bezug auf den MTS-Support fügte er hinzu: „Bei Fragen lieferten die Experten von MTS sofort die Antworten und Anleitungen, die wir brauchten, um unsere Tests im Zeitplan zu halten.“
KUNDENVORTEILE
Die Lösungen von MTS halfen der JAXA, schnell und sicher zu bestätigen, dass die mit dem neuen Verfahren hergestellten Verbundwerkstoffteile den realen Kräften standhalten, denen ein Flugzeug im Flug ausgesetzt ist. „Wir können jetzt nachweisen, dass die mit VaRTM hergestellten Verbundwerkstoffe strengen Leistungsbewertungen unterzogen wurden und ihre Eignung für den Einsatz in Flugzeugflügeln bewiesen haben“, sagte Aioki. „Die große Erfahrung von MTS mit dem Testen von Strukturkomponenten im großen Maßstab war offensichtlich, sie hatten eindeutig das nötige Wissen, um genau die Testlösungen zu formulieren, die wir benötigten.“
Neben dem MTS-eigenen Fachwissen schätzt Aioki auch die von MTS gesponserten Anwenderforen und Seminare. „Die Möglichkeit, sich mit anderen Anwendern von MTS-Geräten umfassend auszutauschen, ist für den weiteren Erfolg unserer Forschung von großer Bedeutung.“
„Dank MTS werden wir bald mit Zertifizierungstests von Passagierflugzeugen beginnen, die von japanischen Unternehmen entwickelt wurden“, so Aioki abschließend. „Die Welt wird bald eine sichere und kostengünstige neue Möglichkeit haben, leichtere und treibstoffeffizientere Verkehrsflugzeuge herzustellen, ohne die Sicherheit der Passagiere zu beeinträchtigen. Die Zuverlässigkeit der Prüfgeräte und die Anleitung der MTS-Experten waren für diesen Erfolg unabdingbar.“