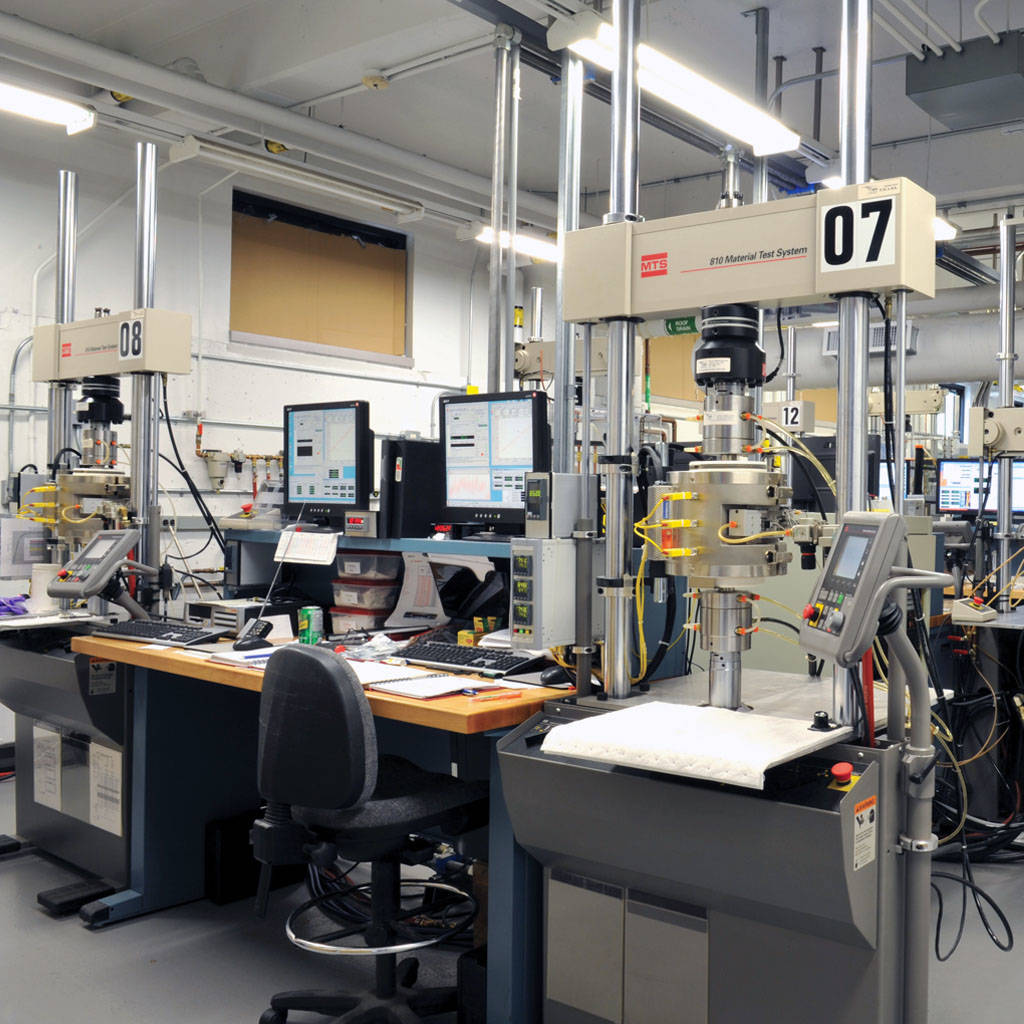
KUNDENHERAUSFORDERUNG
Die Entwicklung von Hochtemperaturwerkstoffen, die über einen längeren Zeitraum bei extremen Temperaturen arbeiten können, schafft die Voraussetzungen für die nächste Generation von Strahltriebwerken und Gasturbinen, die die Erwartungen an die Treibstoffeffizienz neu definieren werden. Einige der fortschrittlichsten Forschungen auf diesem Gebiet finden im Structures and Materials Performance Laboratory statt, das Teil des Instituts für Luft- und Raumfahrtforschung des National Research Council of Canada in Ottawa, Ontario, ist.
Hier ist die Materials and Component Technologies Group, ein Team von 15 Forschern, auf das Design, die Entwicklung und das Testen neuer Gasturbinenmaterialien spezialisiert, darunter Hochtemperaturlegierungen und Keramikmatrix-Verbundwerkstoffe. Die Gruppe betreibt eigene Forschung und arbeitet darüber hinaus mit zivilen Triebwerksherstellern wie Pratt & Whitney, Rolls-Royce und General Electric sowie mit Materialanbietern wie ATI Allvac und Carpenter Technologies zusammen. Um genau zu bestimmen, wie sich neue Materialien verhalten und wie lange sie bei immer höheren Temperaturen halten, müssen sie eine Vielzahl von feinmechanischen Tests durchlaufen.
„Wir machen alles, von Zug-, Kriech- und Bruchzähigkeitstests bis hin zu spezielleren Tests, wie z. B. Ermüdung durch Reibung, thermomechanische Ermüdung, Ermüdungsrisswachstum und Kriechrisswachstumsrate“, sagte Dr. Kearsey, Leiter der Hochtemperatur-Ermüdungs- und Bruchmechanik-Einrichtung der Gruppe. „Wir entwickeln die Materialien, testen sie und entwickeln dann Standardtestmethoden zur Charakterisierung dieser Materialien, was sowohl das Herausfinden der Geometrie des Probekörpers als auch die Nachbildung der Betriebsumgebung des Motors im Labor beinhaltet.“
Im Moment ist Dr. Kearseys größte Herausforderung einfach: Wärme. In früheren Jahrzehnten waren die Temperaturen für die Prüfung von Edelstahl-, Titan- und Aluminium-Legierungen relativ moderat. Das Testen der modernsten Materialien erfordert Temperaturen, die bis zu 25 Prozent heißer sind.
„Die Temperaturen sind so hoch, dass das Testen der Materialien zu einem komplexeren Problem wird“, sagte er. „Wie misst man Materialien bei 1000 °C, wenn die Standardpraxis sich auf Geräte stützt, die für 800 °C ausgelegt sind? Wie fügt man die richtige Instrumentierung zur Messung der Risswachstumsrate hinzu? Es ist nicht unmöglich, aber es ist sehr kompliziert. Wir müssen absolut sicher sein, dass die Temperaturen und Belastungen zu 100 Prozent nachvollziehbar sind, denn unsere Ergebnisse fließen in die Herstellung kritischer Motorkomponenten ein.“
MTS-LÖSUNG
Die Materials and Component Technologies Group setzt 18 verschiedene MTS-Lösungen für Hochtemperaturtests ein. Die Palette reicht von älteren MTS 810 Lastrahmen bis hin zu hochmodernen MTS Landmark® Servohydraulischen Testsystemen.
„Der Grund, warum wir nur MTS-Lastrahmen verwenden, ist die Stabilität“, sagte Dr. Kearsey. „Wenn wir vier oder fünf Rahmen nebeneinander laufen lassen, wackelt das Labor. Die MTS-Rahmen sind so stabil; es gibt keine Verwindung oder Torsion, die den Prüfling falsch ausrichten könnte.“
Zwei MTS-Hydraulikaggregate, die digitale Regelung FlexTest® und die Software Multipurpose TestWare® vervollständigen die Prüfausrüstung der Einrichtung. Das Labor verwendet auch ein komplettes Sortiment an MTS-Prüfzubehör, darunter Spannzeuge und Vorrichtungen, Dehnungsmessstreifen und Dehnungsaufnehmer, Öfen und Induktionsheizungen – die alle einfach zu kombinieren und in die oft komplexen Konfigurationen für spezifische Hochtemperaturtests zu integrieren sind.
„Die Hardware muss bei verschiedenen Testtemperaturen und -bedingungen richtig funktionieren“, so Dr. Kearsey. „Uns gefällt, dass wir einen MTS-Ofen nehmen und ihn auf jeden beliebigen Lastrahmen stecken können. Die Austauschbarkeit ist wichtig, insbesondere für die Wiederholbarkeit. Wenn wir 100 Tests an einer ähnlichen Geometrie durchführen müssen, wollen wir nicht die Zeit damit verbringen, die Kalibrierung für jeden einzelnen Test neu zu machen.“
KUNDENVORTEILE
Für Dr. Kearsey ist nichts wichtiger als die Zuverlässigkeit der Testhardware und -software. Zuverlässigkeit ist entscheidend für die Genauigkeit der Ergebnisse, die Produktivität des Labors und die Zufriedenheit externer Kunden.
„Wir kaufen MTS-Geräte, weil sie fast nie ausfallen“, sagte er. „Sie müssen nicht ersetzt werden. Sie sind zuverlässig und rückverfolgbar. Als Forschungslabor ist die Rückverfolgbarkeit eine wichtige Anforderung. Wenn wir einen Abgleich an einem System durchführen, müssen wir sicher sein, dass genau das auch beim nächsten Test passiert. Dabei spielt es keine Rolle, ob wir eine fortschrittliche einkristalline Legierung testen oder 50 Jahre alte Legierungen für die Lebensdauervorhersagemodellierung auswerten. Mit den Testsystemen von MTS können wir die nötigen Daten für fundierte Entscheidungen generieren.“
Die Zuverlässigkeit von Längenänderungsaufnehmern ist besonders kritisch bei der Prüfung von Hochtemperaturwerkstoffen, vor allem bei Frequenzen bis zu 10 Hz oder bei steiferen Werkstoffen, bei denen die gemessenen Reflexionen kleiner sind. Dr. Kearsey nennt auch die Zuverlässigkeit der Software als einen wichtigen Faktor.
„Wenn Sie zum Beispiel thermomechanische Ermüdungstests durchführen, können die Tests drei Monate dauern“, sagte er. „Es ist sehr teuer für unsere Kunden. Meldungen über abgestürzte Software und ungültige Ergebnisse sind völlig inakzeptabel. Die MTS-Software ist in dieser Hinsicht entscheidend, denn sie bereitet uns diese Probleme nicht. Es ist sehr zuverlässig und viele der Module sind für Low-Cycle-Fatigue, thermomechanische Ermüdung und andere Arten von Tests vorprogrammiert.“
Selbst jetzt, da Dr. Kearsey daran arbeitet, die Herausforderungen zu überwinden, die mit dem Testen bei 1000 °C verbunden sind, erwartet er, dass die Obergrenze steigen wird. In der Tat arbeitet er mit MTS zusammen, um Testsysteme zu entwickeln, die bei diesen viel heißeren Temperaturen arbeiten können.
„Wenn die neueren Legierungen durch Keramikmatrix-Verbundwerkstoffe ersetzt werden, müssen wir Tests bis zu 1300 °C oder 1400 °C durchführen“, sagte er. „Wir diskutieren bereits mit MTS darüber, wie wir dies umsetzen können. Welche Ofengröße benötigen wir? Was wird die heiße Zone sein? Welche Dehnungsmessung wird benötigt? MTS scheint immer zur richtigen Zeit zu uns zu kommen. Diese Art von Unterstützung ist der Grund, warum wir immer wieder auf MTS setzen.“