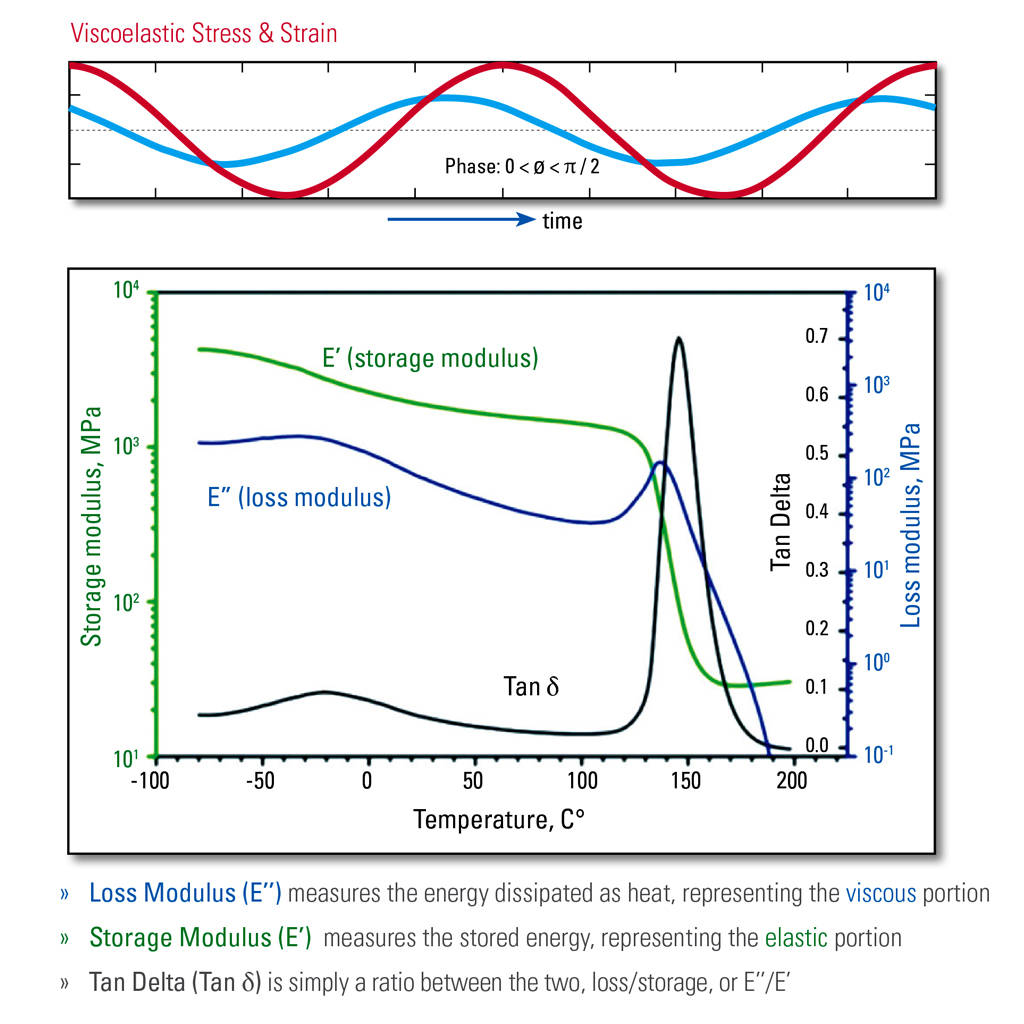
Welche sind die wichtigsten Überlegungen bei der Auswahl eines Prüfsystems für die dynamisch-mechanische Analyse?
1. KEINE MECHANISCHEN RESONANZEN
Die dynamisch-mechanische Analyse (DMA) bezeichnet die Untersuchung des dynamischen Verhaltens eines Materials oder einer Komponente. Meistens werden die DMA-Einstufungen als Funktion einer variierten Geschwindigkeit bei einer festen Verschiebungsamplitude untersucht, also als Funktion einer variierten Frequenz. Wird die Anregungsfrequenz erhöht, kann die dynamische Messgenauigkeit des Wandlers beeinträchtigt werden. Eine hochfrequente Anregung kann innerhalb der Rahmenstruktur unbeabsichtigt mechanische Resonanzmoden erzeugen, die oft die Messgenauigkeit von Weg- und Kraftwandlern verfälschen.
Typische blockreferenzierte Wegwandlermessungen (entweder LVDT oder Encoder) können durch fehlerhafte Bewegungen an der Referenzbasis des Aufnehmers aufgrund von Resonanzschwingungen verfälscht werden. Die Messungen von Kraftwandlern können durch hohe Beschleunigungen verfälscht werden, die aufgrund von Resonanzschwingungen auf einen Wandler einwirken. Diese Beschleunigung kann zu erheblichen Trägheitsfehlern bei der Kraftmessung führen. Es gibt Techniken, die helfen können die Empfindlichkeit eines Schallwandlers gegenüber diesen unerwünschten Schwingungen zu reduzieren, aber diese Techniken erfordern auch einige Kompromisse. Ein effektiverer Ansatz ist die Beseitigung aller blockmechanischen Resonanzen, die im Betriebsbereich des Systems vorhanden sein können. Mit einem dynamischen Kalibrierungsstandard kann eine dynamische Verifizierung bestätigen, dass die DMA-Messungen nicht durch mechanische Resonanzen verfälscht werden. Ein gutes DMA-System weist keine schädlichen mechanischen Resonanzmodi in der Messachse auf.
2. AMPLITUDEN ÜBER EXTREME DYNAMIKBEREICHE MESSEN
DMA-Prüfanforderungen stoßen oft an die Grenzen der dynamischen Bereichsamplitude von Kraft- und Bewegungswandlern. Für einige Elastomer- und Thermoplastmaterialien sind oft Messungen sowohl oberhalb als auch unterhalb der Glasübergangstemperatur innerhalb desselben Testaufbaus erforderlich. Der Elastizitätsmodul (und die Steifigkeit) des Materials kann sich um den Faktor 1000 ändern, wenn von Temperaturen unterhalb des Glasübergangs, bei denen das Material hart wie Glas ist, zu Temperaturen oberhalb der Glasübergangstemperatur, bei denen das Material gummiartig und relativ weich ist, gewechselt wird.
Dies bedeutet, dass die Materialverschiebungen im glasartigen Bereich relativ klein sein können, wenn eine konstante sinusförmige Kraft über den gesamten Prüfaufbau aufgebracht würde. Aber dieselbe sinusförmige Kraftamplitude, die oberhalb des Glasübergangs angewendet wird, wenn sich die Steifigkeit um den Faktor von 1000 ändern kann, bedeutet, dass sich die Verschiebung oberhalb des Glasübergangs ebenfalls um den Faktor von 1000 ändern würde. Dies bedeutet umgekehrt, dass die Materialkräfte im gummiartigen Bereich relativ klein sein können, wenn eine konstante sinusförmige Verschiebung über den gesamten Prüfaufbau aufgebracht würde. Aber die konstante Verschiebungsamplitude, die oberhalb des Glasübergangs angewendet wird, wenn sich die Steifigkeit um den Faktor von 1000 ändern kann, bedeutet, dass sich die Kraftamplitude ebenfalls um den Faktor von 1000 ändern würde. Beide Szenarien erfordern ein Prüfsystem mit der Fähigkeit, über extreme Dynamikbereiche Amplituden zu messen.
3. ÜBERLEGENE STEUERUNG DER DYNAMISCHEN AMPLITUDE
Die meisten Elastomere und Thermoplaste weisen eine signifikante Amplituden-Nichtlinearität auf, was bedeutet, dass der gemessene Elastizitätsmodul (oder die Steifigkeit) des Materials von der Amplitude der aufgebrachten Anregung abhängig ist. Unterschiedliche Eingangsamplituden (Weg oder Kraft) führen zu unterschiedlichen gemessenen Steifigkeiten oder Modulen. In der Tat ist der Zweck einiger Prüfprogramme, diese Amplitudenabhängigkeit zu messen. Für diese Tests wird ein Amplitudensweep mit einer festen Frequenz und Temperatur angewandt und der daraus resultierende gemessene Modul berichtet. Bei vielen Tests sind die variierten Parameter die Anregungsfrequenz und die Materialtemperatur. Da aber der Materialmodul und die Reaktion der Materialien so amplitudenabhängig sind, ist es äußerst wichtig, dass die Amplitude der Testeingangserregung genau bekannt ist und kontrolliert wird. Diese Amplitudenkontrolle wird bei höheren Testfrequenzen noch schwieriger.
Die Steuerung der gewünschten dynamischen Amplitude wird am effektivsten durch Echtzeit-Servo-Regelkreise und oft durch zusätzliche Kompensatoren in der äußeren Schleife erreicht. Es ist wichtig, dass diese Regelgesetze eine hohe Bandbreite haben und robust stabil sind. Regelkreise mit geringer Bandbreite oder träge äußere Regelkreiskompensatoren können dem Prüfkörper zusätzliche „Lernzyklen“ oder „Konvergenzzyklen“ auferlegen und eine interne Prüfkörpererwärmung verursachen, was zu irreführenden Materialkenndaten führt. Ein Mangel an extrem stabilen Regelgesetzen kann auch zu einer Instabilität des Regelkreises führen, was den Prüfkörper oft beschädigt. Zusammenfassend lässt sich sagen, dass eine überragende Kontrolle der dynamischen Amplitude ein entscheidendes Attribut des DMA-Prüfsystems ist.