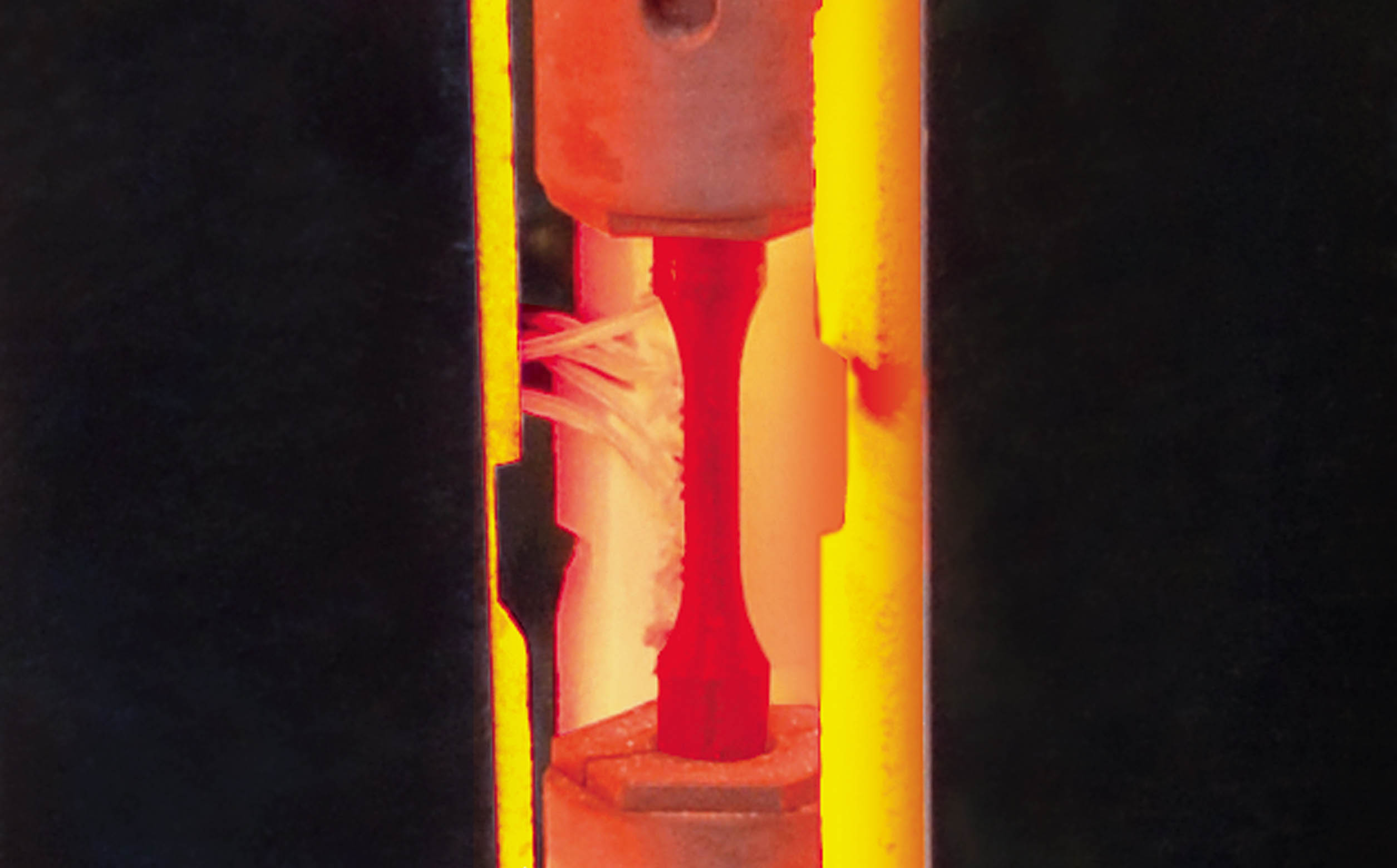
Der MTS F&E-Ingenieur und Wissenschaftler Erik Schwarzkopf verfügt über einen Doktortitel in der mechanischen Metallurgie und bringt mehrere Jahrzehnte an Erfahrung in der Hochtemperaturprüfung mit. In diesem Beitrag spricht er über die Herausforderungen, die mit der Aufrechterhaltung und präzisen Steuerung von Prüftemperaturen einhergehen.
F: Warum ist die Temperatur bei der Materialprüfung so wichtig, insbesondere bei isothermischen LCF- oder HCF-Prüfungen?
A: Ingenieure müssen wissen, wie sich die Materialeigenschaften bei unterschiedlichen Temperaturen verändern. Nur so können sie Produkte und Komponenten entwerfen, die bei den Temperaturen, wie sie in realen Betriebsumgebungen vorherrschen, eine zuverlässige Leistung liefern. LCF- und HCF-Prüfungen (Low-Cycle Fatigue und High-Cycle Fatigue), also Ermüdungstests bei niedriger und hoher Lastspielzahl, dauern mehrere Stunden. Die Temperaturstabilität ist daher ein kritischer Faktor. Kommt es im Verlauf der Prüfung zu Schwankungen von fünf oder zehn Grad, kann sich dies erheblich auf die Zuverlässigkeit der Ergebnisse auswirken.
F: Wie wird die Temperatur in einer typischen Testkonfiguration gemessen?
A: Die gängigste Methode ist die Verwendung eines Thermoelements, das über zwei Metalleiter (Drähte) verfügt. Der Stromfluss durch die Verbindungsstelle der Drähte ist proportional zur Temperatur an der Verbindungsstelle. Die Drähte werden in der Regel am Prüfkörper befestigt, sodass die Temperatur an der Verbindungsstelle der Temperatur des Prüfkörpers entspricht. Für Hochtemperaturprüfungen verwenden Ingenieure Thermoelemente vom Typ R mit Platin-/Rhodium-Drähten, obwohl Thermoelemente vom Typ K mit Chromel-/Alumel-Drähten die günstigere Wahl wären. Für Niedrigtemperaturanwendungen mit hoher Empfindlichkeit sind Thermoelemente vom Typ J mit Eisen-/Konstantan-Drähten erforderlich.
F: Wie wird die Temperatur während einer Prüfung gesteuert?
A: Für die Energiezufuhr des Erhitzungssystems, das den Prüfkörper umgibt, kann die Ausgabe einer PID-Steuerung (Proportional Integral Derivative) verwendet werden. Innerhalb der Kammer oder des Ofens können ein oder mehrere Controller verwendet werden, um die unterschiedlichen Zonen im Innenraum zu steuern. Das Ziel besteht darin, die Temperatur so zu steuern, dass sie innerhalb des Prüfkörpers einheitlich ist, selbst wenn an anderen Stellen Bereiche mit variabler Temperatur vorhanden sind.
F: Ist die Temperatur innerhalb des Ofens tatsächlich so unterschiedlich?
A:Ja. Wenn die Temperatursteuerung dieselben Anweisungen an drei Heizelemente im Ofen sendet, wird der Temperaturgradient innerhalb des Prüfkörpers so groß, dass die Qualität der Prüfergebnisse fraglich ist. Das ist natürlich nicht akzeptabel. Und unnötig ist es auch. Die Temperatur lässt sich nämlich effektiv steuern, Sie müssen allerdings die thermodynamischen Mechanismen bei der Arbeit verstehen. Gradienten entstehen, wenn der Laststrang aus dem Ofen herausragt und Lastzelle und Aktuator tangiert, die Umgebungstemperatur haben. Die Hitze im Ofen wird über Konduktion an die Bereiche mit Umgebungstemperatur übertragen, während die Heizelemente weiterhin Hitze erzeugen, jedoch finden diese Aktionen nicht mit derselben Geschwindigkeit statt. Mithilfe einer Steuerung für mehrere Zonen lassen sich „Puffer“ erzeugen, die die größeren Gradienten von der Messlänge des Prüfkörpers wegschieben, hin zu den Schäften oder sogar bis zu den Druckstangen. Auf diese Weise bleibt der Gradient im reduzierten Abschnitt des Prüfkörpers in einem akzeptablen niedrigeren Bereich.
F: Wie klein sollte der Gradient im Prüfkörper sein?
A: Das ist je nach Standard unterschiedlich. Die verschiedenen nationalen und internationalen Spezifikationen für LCF- und HCF-Prüfungen stimmen darin nicht überein. Im Allgemeinen sollte der maximale Gradient in der Messlänge einige Prozent der nominalen Prüftemperatur betragen. Beträgt die nominale Prüftemperatur also 500 °C, dann sollte der Gradient im reduzierten Abschnitt maximal 5 °C bis 10 °C betragen, also 1 % bis 2 %. Bei einem gut geplanten Prüfsystem kann der Gradient im reduzierten Bereich innerhalb von 1 % der gewünschten Temperatur gehalten werden. Der Dreizonenofen von MTS vom Modell 653.04 beispielsweise kann den Gradienten über eine Messlänge von 25 mm und bei einer nominalen Prüftemperatur von 800 °C auf ±2 °C halten. Dies erfüllt bei Weitem Fall die Spezifikationen nach ASTM und ISO.
F: Wie lange dauert es, bis die gewünschte Prüftemperatur erreicht ist?
A: Es kann bis zu einer Stunde dauern, bis die Temperatur hochgefahren ist, den Prüfkörper durchdrungen hat und eine gleichmäßige Verteilung innerhalb des Prüfkörpers und Laststrangs erreicht ist. Wenn Sie zu schnell hochfahren, kann es zu Überschwingung und Beschädigung des Prüfkörpers kommen, und Sie müssen das System erst wieder kühlen und erneut aufheizen. Viele Labors haben im Laufe der Jahre versucht, die Hochfahrzeit aus Produktivitätsgründen zu minimieren. Bei einigen Zugprüfungen lassen sich Prüfkörper und Laststränge in Ersatzöfen vorheizen, um sie zu gegebener Zeit im Prüfsystem zu installieren. Andere Labors haben mit variablen Heizraten in den einzelnen Ofenzonen experimentiert, um die Durchwärmzeit zu reduzieren. Die Hochtemperatur-LCF- und HCF-Vorlagen für die MTS TestSuite™ MP Elite-Software setzen auf komplexe Profile, um die äußeren Zonen schnell zu erhitzen und anschließend die innere Zone mit dem Prüfkörper allmählich hochzufahren. In vielen Fällen wird die Durchwärmzeit jedoch von der Prüfspezifikation vorgegeben.
F: Ist der größere, leistungsstärkere Ofen immer die richtige Wahl?
A: Das kommt darauf an, wie Sie „größer“ und „leistungsstärker“ definieren. Ein Ofen kann über eine höhere Maximaltemperatur, mehr Isolierung, einen größeren Innenraum, länger beheizte Zonen oder mehrere Steuerungszonen verfügen. Die Frage ist, welche Nachteile damit verbunden sind. Mehr Steuerungszonen ermöglichen kleinere Gradienten im Prüfkörper, sind aber teurer. Länger beheizte Zonen können Gradienten ebenfalls reduzieren, erfordern jedoch Hochtemperatur-Druckstangen. Mehr Isolierung verbessert die Stabilität, bei Überschwingen ist es jedoch schwieriger, die Temperatur wieder zu korrigieren. Die Verwendung eines 1.000-°C-Ofens für eine 150-°C-Prüfung geht zu Lasten der Temperatursteuerung. So hat jede Eigenschaft ihre Auswirkungen.
F: Was ist sonst noch für eine präzise Temperatursteuerung relevant?
A: Bevor Sie sich an die Auswahl des Zubehörs machen – wie Ofen oder Spannzeuge –, sollten Sie die Anwendung ganzheitlich betrachten: Wie hoch ist die gewünschte Prüftemperatur und wie gestalten sich Geometrie des Prüfkörpers, Gradient und Prüfdauer? Überlegen Sie außerdem, wie Sie den Prüfkörper erhitzen und die Temperatur während der Prüfung aufrecht erhalten möchten. Die gängigste Methode bei einer isothermischen Prüfung ist die Verwendung eines Widerstandsofens mit Thermoelementen, die den Prüfkörper berühren. Die Thermoelemente sind mit Schweißpunkten an den Schäften des Prüfkörpers und nicht am reduzierten Abschnitt befestigt, um das Risiko von Rissbildung zu vermeiden. Am Wichtigsten ist es, dass Forscher das mittlerweile aufgebaute Wissen über Hochtemperaturprüfungen vollständig nutzen. Vor nicht allzu langer Zeit war „Versuch und Irrtum“ die übliche Herangehensweise. Heute stehen intelligentere Wege zur Verfügung, die genauere Ergebnisse liefern.