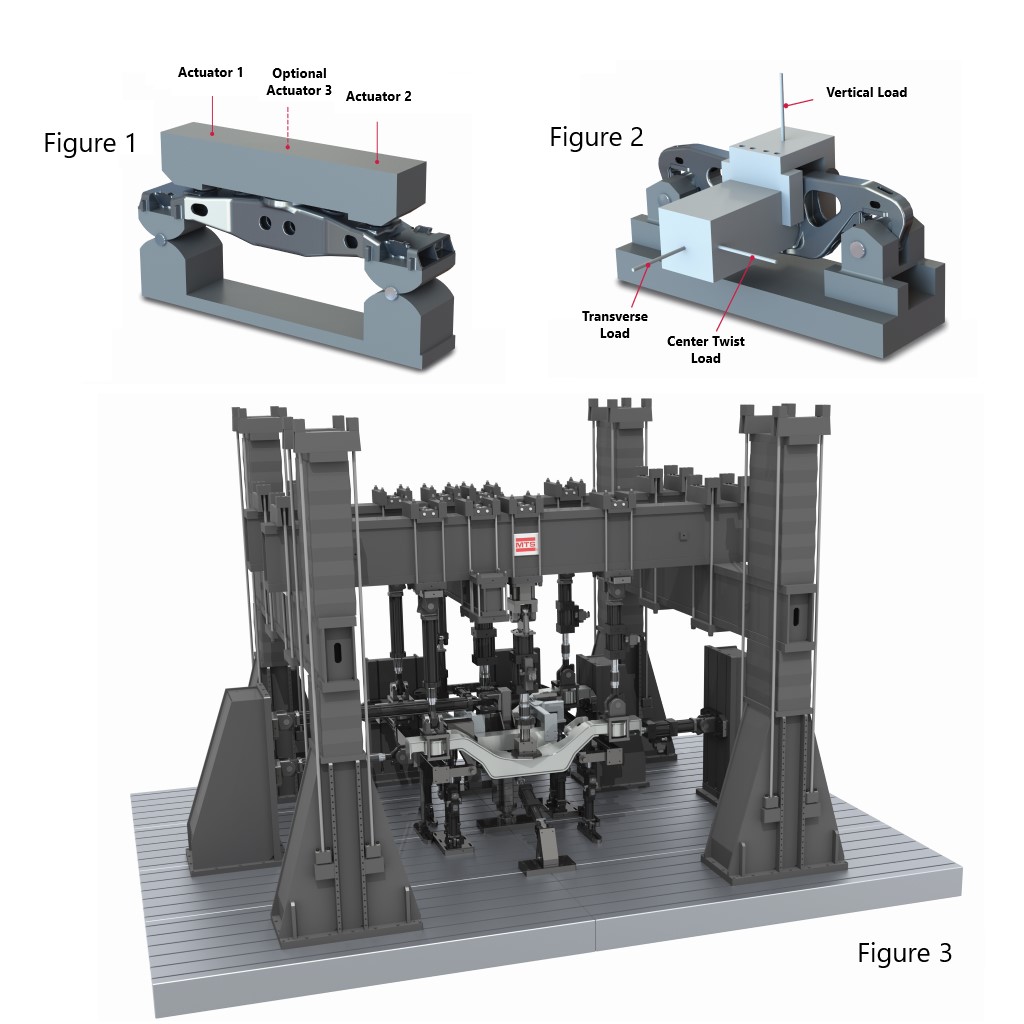
Bei der Betrachtung aller Komponenten und Baugruppen, aus denen ein Schienenfahrzeugsystem und seine Umgebung besteht, ist es hilfreich, eine imaginäre Linie entlang der Schienenoberkante zu ziehen. Diese Linie unterteilt das System in zwei große Gruppen. Die erste Gruppe, die sich oberhalb der Strecke befindet, ist das „Rollmaterial“, das durch einen Fahrwerksrahmen (oder eine Kombination aus zwei Seitenrahmen und einem Träger) zusammen mit der Primär- und Sekundäraufhängung und dem Schienenfahrzeug dargestellt wird. Die zweite Gruppe, die sich unterhalb der Linie befindet, ist „der Weg“, repräsentiert durch die Schienen, Befestigungen, Schwellen, Schotter und andere Komponenten. Die Schnittstelle zwischen den beiden Gruppen ist die Achse mit einem Radsatz.
Während viele der einfacheren Elemente in diesem System durch grundlegende Komponententests behandelt werden können, erfordert die Bewertung einer Komponente oder Teilbaugruppe innerhalb des Rollmaterials die Berücksichtigung von drei ebenso wichtigen Faktoren: Ermüdung, Leistung und Komfort.
Obwohl die Ermüdungslebensdauer vielleicht nicht das ist, was der Fahrgast während der Fahrt zu schätzen weiß (oder worüber er überhaupt nachdenkt), stellt sie dennoch einen sehr wichtigen Teil bei der Konstruktion und Wartung von Rollmaterial dar. Im Laufe des letzten Jahrhunderts hat die Bahnindustrie die Bedeutung von Ermüdungsprüfungen bei der Konstruktion und Herstellung von Schienenkomponenten verstanden und erkannt. Um eine gleichbleibende Lebensdauer und die Sicherheit der Fahrgäste zu gewährleisten, wurden viele Zertifizierungsstandards entwickelt.
ERFÜLLUNG DER ZERTIFIZIERUNGSSTANDARDS
Hersteller von Eisenbahnkomponenten und -teilsystemen müssen die Komponenten und Teilsysteme auf die Einhaltung der entsprechenden Zertifizierungsnormen prüfen, einschließlich internationaler Normen wie M-202-97 für Träger, M-203-05 für Seitenrahmen und UIC 615 für Fahrwerke. Diese Normen helfen dabei, die Tests zu definieren, mit denen die Ermüdungslebensdauer und Haltbarkeit neuer Komponenten ermittelt wird, und sie sind für den sicheren, langfristigen Betrieb von Personen-, Güter- und Stadtbahnlinien unerlässlich.
Die Zertifizierungsprüfungen für Fahrwerke, Träger und Seitenrahmen verlangen von den Herstellern die Durchführung von Sicherheits- und Zuverlässigkeitstests an Fahrwerksstrukturen und Komponenten in bestimmten Konfigurationen. Es werden statische und dynamische Lasten aufgebracht, um Leistung, Kraft und Ausdauer zu bewerten. Die Testergebnisse umfassen Fließ- und Bruchlastwerte sowie Ermüdungslebensdaten.
Drei Lasten sind erforderlich, um die Träger ordnungsgemäß zu testen: Rüttellast, Mittenaufprall und Kantenaufprall (siehe Abbildung 1). Diese Lasten repräsentieren die Kräfte, denen der Träger in seiner tatsächlichen Einsatzumgebung ausgesetzt ist. Für den Seitenrahmen werden ebenfalls drei Lasten benötigt: vertikal, quer und mittig verdreht (siehe Abbildung 2). Alle diese separaten Kraftvektoren sind wichtig, um die richtigen Lasten und die richtige Spannungsverteilung auf den Prüfkörper zu übertragen und eine angemessene Ermüdungslebensdauer zu gewährleisten.
Für die Prüfung von Trägern und Seitenrahmen ist ein entsprechend bemessener bodenstehender Lastrahmen ideal, der relativ einfach zu befestigen ist. Die Ermüdungstests für Fahrwerksrahmen sind jedoch anspruchsvoller und komplexer. Die Fahrwerk-Zertifizierungstests sind durch internationale und lokale Normen definiert und erfordern eine höhere Anzahl von Kanälen und eine viel kompliziertere Befestigung. Die Lastkonfigurationen für den Test basieren auf der Konfiguration des Fahrwerks. Die Anzahl der Achsen pro Fahrwerk, die Anzahl der Fahrwerke pro Schienenfahrzeug und das kombinierte Gewicht von Fahrwerk und Schienenfahrzeug sind einige der Parameter, welche die für den Test benötigten Lasten bestimmen. Die Zertifizierungstests erfordern ein Mehrkanal-Lastsystem mit hoher Kraft und laufen in der Regel über Millionen von Zyklen. Während eines Tests werden Dehnungs- und andere Signale gesammelt und analysiert, um den Konstrukteuren zu helfen, die Lastdynamik der Betriebsumgebung zu verstehen, Bereiche mit hoher Last zu identifizieren und die Konstruktionen entsprechend zu verbessern. Durch den Vergleich der Dehnungsreaktionen mit Finite-Elemente-Analysemodellen (Finite Element Analysis bzw. FEA) können Ingenieure die Modelle validieren, was zukünftige Konstruktionen verbessert.
ERWEITERTE ERMÜDUNGSPRÜFUNG
Die Zertifizierungsstandards sind streng und beinhalten Millionen von Belastungszyklen; aber sie konzentrieren sich ausschließlich auf die Mindestanzahl von Lasten (vertikal, quer und verwindend), die erforderlich sind, um eine angemessene Ermüdungslebensdauer und einen Sicherheitsfaktor zu verifizieren. Diese Lasten sind deutlich höher als die, die im Normalbetrieb zu erwarten sind. Die Lastverläufe sind bewusst konservativ gehalten, um eine Ausfallrate zu gewährleisten, die bei allen möglichen Einsatzkombinationen so nahe wie möglich bei Null liegt. Dieser Ansatz hat sich für gängige Güterfahrwerke bewährt und wurde (in der einen oder anderen Form) weltweit übernommen.
Bei modernen Fahrzeugen für den Personenverkehr sind jedoch die Fahrwerke, die Aufhängungen und die Schnittstelle zum Wagen wesentlich komplexer als im Güterverkehr. Hochgeschwindigkeitsfahrwerke für den Transport von Personen sind komplexe Schweißkonstruktionen. Dämpfer, Federlenker und Nebenaggregate (Kompressoren, Bremssättel) belasten das Fahrwerk zusätzlich. Diese Lasten setzen sich oft aus ganz anderen Lastvektoren und -orten zusammen als in der Zertifizierungsnorm beschrieben. Die Orte, Größen, Vektoren und Phasen dieser Lasten sind wichtig für Prüfingenieure, die daran interessiert sind, die tatsächliche Betriebsumgebung des Fahrwerks so realistisch wie möglich nachzubilden.
Die Komplexität wird unter diesen Umständen schnell zum Problem. Während Zertifizierungstests typischerweise weniger als 10 Kanäle (in den meisten Fällen weniger als sechs) verwenden, können fortgeschrittenere Entwicklungstests mehr als 20 (und in einigen Fällen mehr als 30) Steuerkanäle benötigen. Die Kombination von zusätzlichen Lasten mit den von den Zertifizierungsnormen vorgeschriebenen Lasten stellt eine große Herausforderung in Bezug auf die Befestigung dar.
Die Bewältigung dieser Komplexität ist unerlässlich. In den letzten 10 bis 15 Jahren ist die Nachfrage der Endnutzer nach Rollmaterial mit höherer Zuverlässigkeit, besserer Leistung und größerem Komfort erheblich gestiegen. Um diese Anforderungen zu erfüllen, entwickeln die Hersteller Werkstoffe und Fertigungsmethoden, die bei der Einführung der Zertifizierungsstandards noch nicht verfügbar waren. Neue Werkstoffe – und vor allem neue Methoden zur Gewichtsreduzierung – die bei der Konstruktion und Herstellung praktisch aller Komponenten des Eisenbahnsystems verwendet werden, haben einen Bedarf an neuen Entwicklungsprüfverfahren geschaffen, die außerhalb des Rahmens der traditionellen Zertifizierungsprüfung liegen.
Für diese größeren strukturellen Anwendungen werden zwei- oder viersäulige Portalrahmen mit kundenspezifischen Antriebskonfigurationen benötigt (siehe Abbildung 3). Da viele der Kräfte auf ein Fahrwerk hoch sind, sind die Aktuatoren die zur Nachbildung dieser Lasten verwendet werden, groß. Die direkte Anbringung von Aktuatoren an Lastpunkten kann erfordern, dass mehrere Aktuatoren gleichzeitig denselben physikalischen Raum belegen. Dies ist ein Problem, dessen Lösung erhebliches Fachwissen in Bezug auf Spannvorrichtungen und kinematische Mechanismen erfordert. Um die Lastvektoren an den richtigen Stellen aufzubringen, werden Kombinationen aus Aktuatoren, Hebeln, Streben (tragende Säulen) und Lagern verwendet. Lastsensoren können an Aktuatoren, Laststreben und/oder Reaktionsvorrichtungen installiert werden. Schwenklager an beiden Enden der Streben und Aktuatoren eliminieren Seiten- und Biegelasten. In einigen Fällen kann der Prüfkörper umgedreht werden, um einen besseren Zugang zu den Lastpunkten zu ermöglichen.
Kreuzkopplung – wenn die Aktion eines Aktuators einen anderen beeinflusst – stellt ernsthafte Steuerungsprobleme dar, die überwunden werden müssen. Der digitale Regler und die Software müssen zusammenarbeiten, um die Amplitude und die Phasenlage der betroffenen Kanäle zu koordinieren, das Risiko von Störungen zu beseitigen und eine genaue Last zu gewährleisten. Typischerweise handelt es sich um fortschrittliche Steuerungstechniken. Das gesamte System, einschließlich des Prüfkörpers, des Rahmens und des Aktuator-Teilsystems, kann einige natürliche Nichtlinearitäten enthalten. Die Berücksichtigung dieser Nichtlinearitäten kann eine Modifikation der Antriebssignale erfordern, um am Prüfkörper den gewünschten Lastverlauf zu erreichen.
Anpassungen werden typischerweise mit einer fortschrittlichen Signalverarbeitungssoftware wie der ferngesteuerten Parameterregelung ( Remote Parameter Control bzw. RPC®) von MTS vorgenommen, die auf der Übertragungsfunktionsmatrix (Frequency Response Function bzw. FRF) des gesamten Systems basiert. Die Software misst den Reglerbefehl und vergleicht ihn mit Amplitude und Phase der Prüfkörperantworten über den gewünschten Frequenzbereich. Es wird eine Kreuzkopplungsmatrix erzeugt, die alle Kreuzkopplungen und andere lineare Differenzen zwischen Befehl und Antwort enthält. Diese FRF wird dann invertiert und mit der gewünschten Reaktion multipliziert. Das Ergebnis ist eine Aktuator-Antriebsdatei, die Kreuzkopplungen und ähnliche Probleme kompensiert. Nichtlineare Beiträge werden korrigiert, indem der Fehler berechnet, eine entsprechende Korrekturdatei erstellt und dann die Korrektur auf die vorherige Antriebsdatei angewendet wird. Dieser iterative Prozess wird wiederholt, bis die gewünschte Genauigkeit erreicht ist. Durch die Anwendung solcher Regelkompensationstechniken kann der Test mit einer viel höheren Frequenz genau ablaufen, was die Testzeit reduziert und die Testqualität erhöht.
Während dies geschieht, müssen die Ingenieure in der Lage sein, große Datenmengen zu sammeln und zu verwalten. Das Prüfsystem muss z. B. bis zu 250 Dehnungsmessstreifen und Verschiebungskanäle aufnehmen, um mögliche Schwachstellen in der Konstruktion zu finden. Ein Teil dieser Daten muss in Echtzeit für die Verwendung im Steuerungssystem erfasst werden, während noch größere Datenmengen für die Offline-Analyse und den Vergleich mit Modellen aus der computergestützten Technik (Computer-Aided Engineering bzw. CAE) gesammelt werden müssen.
Die Bewältigung all dieser Herausforderungen ist schwierig, aber die Investition wert. Die Ergebnisse ermöglichen es den Komponentenherstellern, ihre Konstruktionen zu optimieren, neue Produktangebote zu differenzieren und den Kunden das nötige Vertrauen in die Qualität und Zuverlässigkeit der neuen Komponenten zu geben.
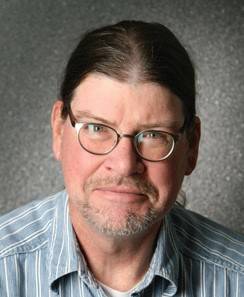