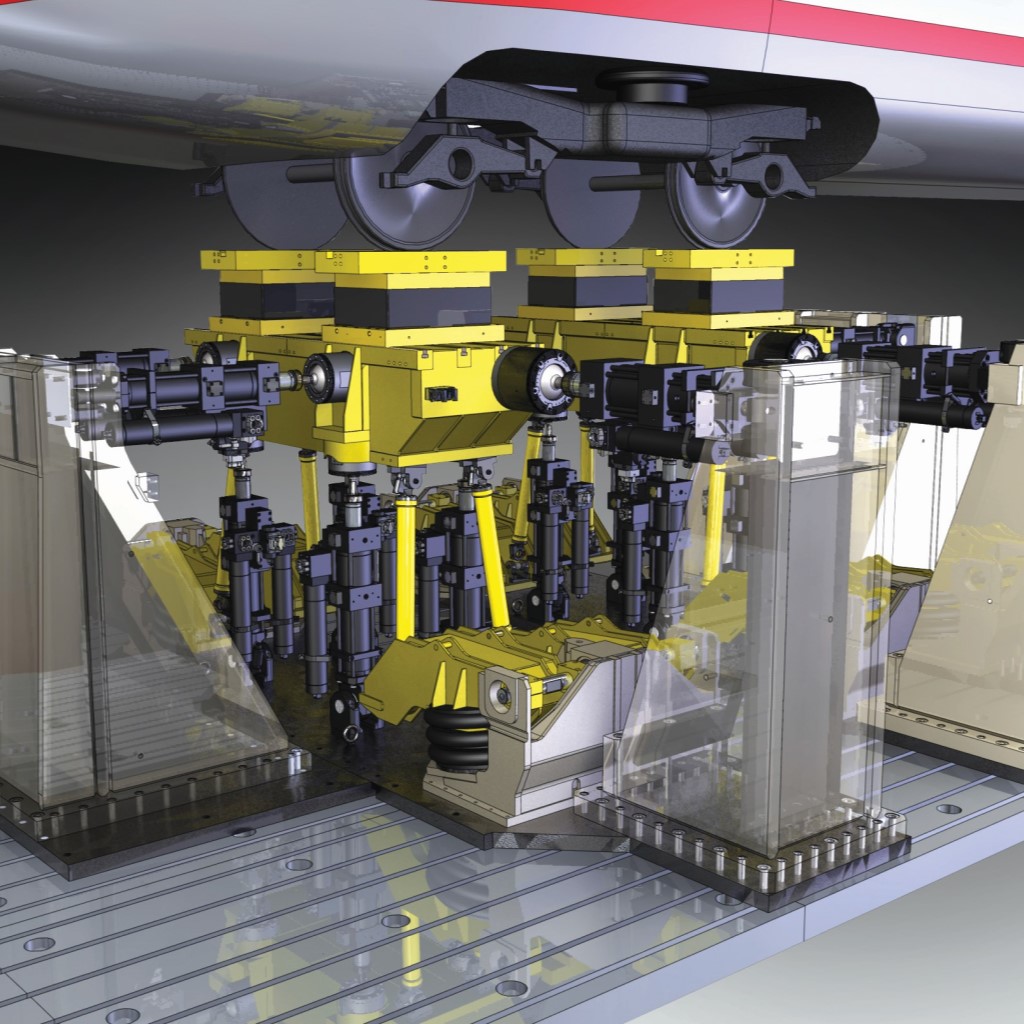
Das globale Wachstum des Zugverkehrs steigert die Nachfrage nach neuen Reisewaggons, was für Hersteller auf der ganzen Welt eine willkommene Nachricht ist. Gleichzeitig müssen diese neuen Schienenfahrzeuge höheren Ansprüchen genügen. Moderne Reisewaggons müssen mit höheren Geschwindigkeiten fahren, einen hohen Fahrkomfort bieten, die Energieeffizienz maximieren und natürlich alle gesetzlichen Vorschriften erfüllen.
Die gleichzeitige Erfüllung dieser Anforderungen stellt eine Reihe von Herausforderungen an das Design. Je weniger Gewicht, desto höher der Wirkungsgrad; weniger Gewicht darf aber keinen Einfluss auf die Stabilität haben. Bei hohen Geschwindigkeiten wird die Stabilität schwieriger, und die schnellsten Schienenfahrzeuge der Welt fahren inzwischen bis zu 350 Kilometer pro Stunde. Auch der Fahrkomfort ist bei hohen Geschwindigkeiten schwieriger zu erreichen.
Da diese Faktoren zusammenhängen, müssen Hersteller in der Lage sein, neue Designs zu optimieren, um die Kompromisse effektiv zu handhaben. Zum Beispiel kann ein steiferes Fahrwerk mehr Stabilität, aber weniger Fahrkomfort bieten. Die Steifigkeit des Überrollbügels kann verändert werden, um entweder ein besseres Fahrverhalten oder einen höheren Komfort für die Passagiere zu erreichen, aber nicht beides gleichzeitig.
Produktentwicklungsteams stehen aufgrund der hohen Marktnachfrage unter großem Zeitdruck, und die Designer müssen schnell arbeiten. An dieser Stelle wird die mechanische Prüfung sehr nützlich.
HERAUSFORDERUNGEN IM LABOR
Im Prüflabor können Komponentenkonstrukteure viele Iterationen eines neuen Designs relativ schnell in einer sehr kontrollierten und wiederholbaren Weise untersuchen. Aus den Testergebnissen lassen sich Koeffizienten und andere Faktoren ableiten, die in virtuelle Modelle von Komponenten und Teilsystemen zurückgeführt werden können, um diese genauer zu machen. Dies hilft, den Prozess der Analyse und Verbesserung neuer Designs zu beschleunigen.
Das Labor bietet seine eigenen Herausforderungen. Die Liste der relevanten Tests ist lang, und jeder erfordert typischerweise einen anderen Typ von Prüfsystem mit einem einzigartigen Aufbau. Die Anschaffung der Systeme, die zur Optimierung neuer Fahrwerkskonstruktionen erforderlich sind, kann teuer sein. Das Konfigurieren und Ausführen der Tests kann ineffizient werden, wenn mehrere Systeme im Einsatz sind.
Die größte Herausforderung von allen ist die Notwendigkeit, den gesamten Mechanismus zu testen und nicht nur eine einzelne Komponente. Dies mag kontraintuitiv erscheinen, aber Konstrukteure von heute wissen, dass das Testen einzelner Teile nicht die gleiche Genauigkeit oder den gleichen Einblick bietet wie das Testen eines kompletten Fahrwerks.
Obwohl diskrete Komponententests einfacher zu verwalten sind und schnell durchgeführt werden können, bieten sie nicht dieselbe Genauigkeit wie das Testen aller Komponenten als System. Die Interaktion der Komponenten führt zu unerwartetem Verhalten aufgrund von Reibung und dezentraler Bewegung. Diese Wechselwirkungen lassen sich nicht nachbilden, indem jede Komponente einzeln ausgewertet wird. Ingenieure haben dies schon lange vermutet, aber erst im letzten Jahrzehnt ist es offensichtlich geworden. Die virtuellen Modelle sind immer ausgefeilter geworden; dennoch waren die Ingenieure nicht in der Lage, die Systemleistung auf der Schiene auf der Grundlage der Eigenschaften einzelner Komponenten genau vorherzusagen.
Kürzlich wurde ein innovatives Schienenfahrzeug-Prüfsystem in Betrieb genommen, mit dem Kinematik und Nachgiebigkeit eines kompletten Fahrwerks gemessen werden kann. Das von MTS Systems Corp. gelieferte System kann auch für Einstufungs-, grundlegende Haltbarkeits- und Vibrationstests verwendet werden – alles in einem einzigen System.
PRÜFUNG DER PRIMÄREN UND SEKUNDÄREN AUFHÄNGUNG
Das neue Fahrwerkmesssystem, das derzeit bei einem Hersteller von Hochgeschwindigkeits-Reisewaggons in Asien installiert ist, liefert die Größe und Kraft, die für die Last eines kompletten Fahrwerks sowie eines kompletten Schienenfahrzeugs erforderlich ist. Das Prüfsystem verfügt über eine umfangreiche Instrumentierung, die für äußerst präzise Messungen dieser komplexen Mechanismen ausgelegt ist.
Die Komplexität ergibt sich aus den vielen Möglichkeiten, wie Testdaten verfälscht werden können. Um genaue Ergebnisse zu gewährleisten, müssen die Prüfsysteme in der Lage sein, alle folgenden Phänomene zu verhindern (oder zu kompensieren): Phasenverschiebung durch Spiel oder Dämpfung, Signalverzerrung und Rauschen durch System- und Prüfkörperresonanzen, und Kraftmessfehler, die durch Übersprechen, Temperaturkompensation der Wandler, thermische Ausdehnung und Kontraktion von Einspannungen und Prüfkörper, Kalibrierfehler, Schlupf, Drift oder Beschädigung von Wandlern, Halterungen, Kabeln oder Aufbereitern entstehen. In vielen Fällen werden mehrere Signale kombiniert, um das gewünschte Ergebnis zu berechnen, wodurch sich der Gesamtfehler vergrößert.
Zu den wichtigsten Prüfungen, die das System durchführt, gehören die Prüfung der primären Aufhängung, zu der alle Komponenten zwischen Fahrwerk und Achse gehören (Feder, Schraubenfeder, Drehstab, Gummizwischenstück usw.). Während die primäre Aufhängung die Lenkung, das Handling und bis zu einem gewissen Grad auch den Fahrkomfort beeinflusst, müssen die Ingenieure die komplette Radsatzbefestigung und das Aufhängungssystem bis ins Detail verstehen, um neue Designs zu optimieren. Die Steifigkeit der primären Aufhängung liegt im selben Bereich wie die Steifigkeit des Fahrwerkrahmens, und die Wechselwirkung zwischen beiden bestimmt das gesamte Fahrverhalten des Fahrwerks. Aus diesem Grund ist das neue Prüfsystem in einzigartiger Weise darauf ausgelegt, die einzelnen Komponentenbeiträge oder die komplette Baugruppeneigenschaft als integriertes System zu messen.
Der Steifigkeitstest der primären Aufhängung beinhaltet die Befestigung der Sekundäraufhängung, die Montage von linearen Differentialtransformatoren (Linear Variable Differential Transformer bzw. LVDTs) an den Ansprechpunkten des Achslagergehäuses und des Fahrwerks und das Aufbringen einer programmierten Kraft oder Verschiebung in jedem der gewünschten Freiheitsgrade (Degrees of Freedom bzw. DOF). Um ein brauchbares Ergebnis zu erzielen, müssen die Ingenieure die Genauigkeit und Auflösung von Kraftmessdosen und LVDTs sicherstellen, eine konstante Temperatur im Labor aufrechterhalten und Messungen bei verschiedenen Geschwindigkeiten durchführen, um die Dämpfungseigenschaften zu bewerten. Es ist wichtig, die Steifigkeit des Fahrwerks in jeder Richtung zu messen, nicht nur vertikal, da die Stabilität eine Funktion der kombinierten mehrachsigen Verschiebungen ist, eben nicht nur vertikal. Bei Kurvenfahrten z. B. verwindet sich das Fahrgestell (verformt sich in der Gierachse), und die Verwindungssteifigkeit ist entscheidend für eine stabile Lenkung.
Derselbe Aufbau kann verwendet werden, um einen Dämpfungstest der primären Aufhängung durchzuführen und die Dämpfung in Abhängigkeit von der Federsteifigkeit zu bewerten. Testdaten aus der Prüfung der primären Aufhängung sind sehr hilfreich für die Rückkopplung in virtuelle Modelle des Fahrwerks, sowohl für die Modellerstellung als auch für die Validierung.
Eine weitere wichtige Reihe von Prüfungen sind die an der sekundären Aufhängung, die sich zwischen der Oberseite des Fahrwerks und der Unterseite des Schienenfahrzeugs befindet. Für diese Tests ist die primäre Aufhängung fixiert und die sekundäre Aufhängung – typischerweise ein Paar Luftfederbälge – ist an mehrachsigen Kraftmessdosen montiert. Eine simulierte Schienenfahrzeughalterung wird in 3DOF eingeschränkt und in den verbleibenden 3DOF gesteuert, um die Sekundäraufhängung mit denselben Lasten und Verformungen zu präsentieren, die sie im Betrieb sieht. Dadurch können die Steifigkeits- und Dämpfungseigenschaften ausgewertet werden. Aufgrund der verkanteten Form des „Airbag-Huts“ ist die Vorhersage der Seiten- und Wanksteifigkeit besonders schwierig. Das elastomere Material verformt sich auf unvorhersehbare Weise, und diese Bewegungen beeinflussen den Fahrkomfort erheblich.
ZUSÄTZLICHE LEISTUNGSTESTS
Eine andere Art von Test, die dieses System durchführen kann, ist die Messung des Lenkwiderstandsmoments, bei der das Fahrwerk unter dem simulierten Schienenfahrzeug gedreht und seine Steifigkeit gemessen wird. Um diesen Test durchzuführen, werden auf jede Achse gleiche und entgegengesetzte seitliche Lasten oder Verschiebungen aufgebracht. Die Zug-/Druck- und Längskräfte werden auf Null gesetzt, und die vertikalen Aktuatoren werden so gesteuert, dass sie die gewünschte Kraft oder eine feste ebene Bewegung an den Rädern aufrechterhalten.
Außerdem kann das Prüfsystem so konfiguriert werden, dass der Aufhängungskoeffizient für gerade oder Kurvenstrecken getestet wird. Bei dieser Prüfung ist der Prüfkörper ein vollständiges (oder simuliertes) Schienenfahrzeug mit Winkelmesskreiseln an Auflageplatten, Fahrwerken und Karosserie. Bei der Prüfung werden die Räder auf einer Seite des Fahrwerks auf eine gewünschte Überhöhung angehoben, und der Winkel von Fahrwerk und Schienenfahrzeug relativ zum Auflageplattenwinkel gemessen. Diese Beziehungen können aufgrund der vielen Elemente in der kompletten Aufhängung schwer vorherzusagen sein. Hersteller können einen ähnlichen Test verwenden, um den Überschlagskoeffizienten zu verstehen, der für die Gewährleistung von Fahrkomfort und Sicherheit entscheidend ist.
Es können auch komplette Schienenfahrzeuge ausgewertet werden. Wenn Ingenieure das dynamische Verhalten für Koeffiziententests verstehen wollen, kann das System mit breitbandigem Rauschen oder bestimmten Wellenformen, z. B. einer Sinuswelle, angesteuert werden. Das Verhalten der Karosserie des Schienenfahrzeugs wird gemessen, und seine Eigenfrequenz kann aus den resultierenden Daten mit einer Prüfsoftware abgeschätzt werden.
Zu den weiteren Tests, die das System durchführen kann, gehören die Ermittlung des Schwerpunkts, die Prüfung des Trägheitsmoments und die Echtzeitwiedergabe von Betriebsdaten auf der Schiene.
Es stimmt zwar, dass ein Mehrzweck-Leistungsprüfsystem eine beträchtliche Kapitalinvestition für das Labor darstellt; aber durch seine Fähigkeit, den Prüfplan zu beschleunigen, die Kosten zu senken und die Genauigkeit der Prüfdaten und der Prüfkörpereinstufung zu verbessern, bietet es eine ebenso beträchtliche Kapitalrendite. Letztendlich ermöglichen diese Fähigkeiten den Herstellern von Schienenfahrzeugen und Fahrwerken, die Genauigkeit der Modelle zu verbessern, Innovationen schneller zu erreichen, qualitativ hochwertigere Fahrzeuge herzustellen und einen dauerhaften Wettbewerbsvorteil aufzubauen.
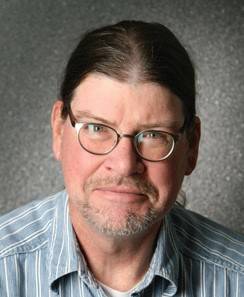