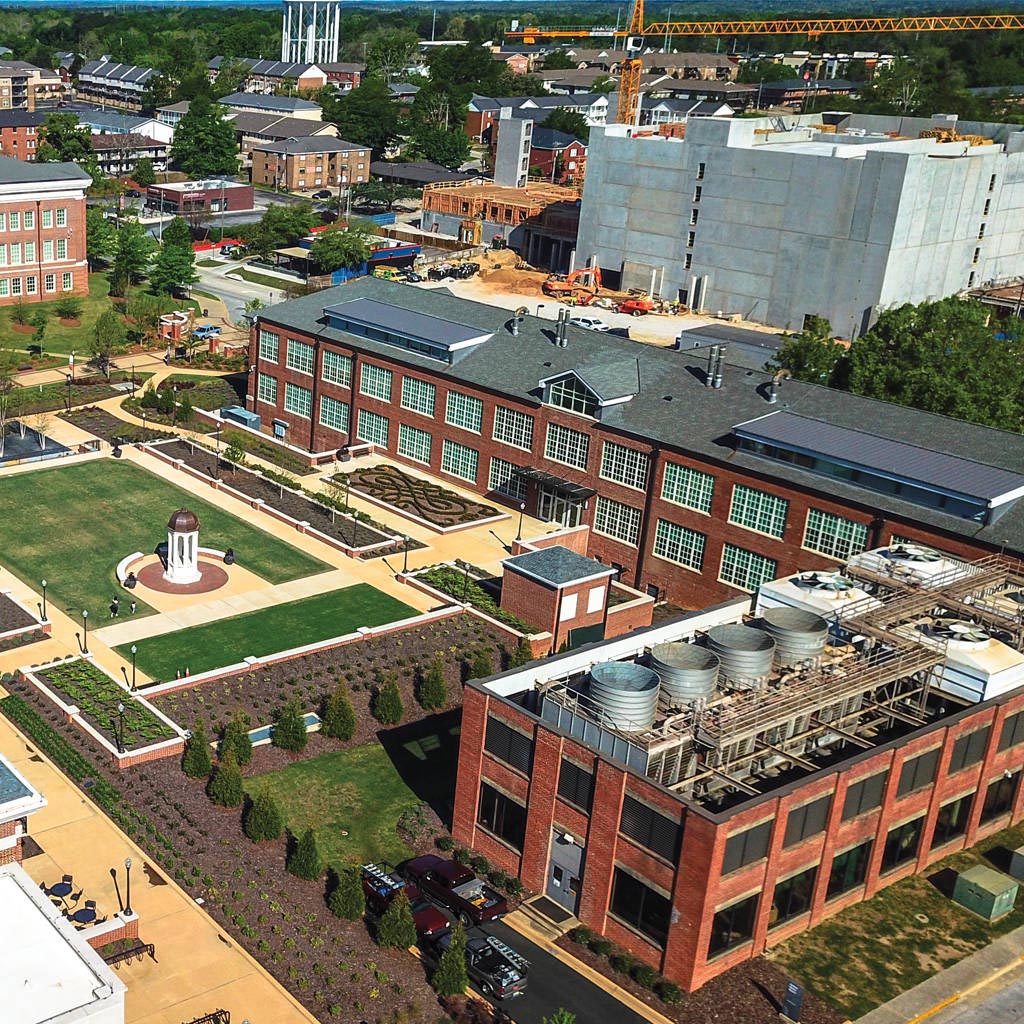
Ermüdung ist immer noch die Ursache für die Mehrzahl der mechanischen Ausfälle in vielen strukturellen Anwendungen, und ein typischer Ermüdungsausfall hat mindestens 3 Stufen: Rissinitiierung, Rissausbreitung und endgültiger Bruch. Es ist bekannt, dass Oberflächendefekte (z. B. Oberflächenrauhigkeit), volumetrische Defekte (z. B. Poren, fehlende Schmelze) und die Mikrostruktur Einfluss auf das Ermüdungsverhalten von metallischen Werkstoffen haben. Es ist auch erwähnenswert, dass Risse oft aus verschiedenen Gründen wie leichtere unelastische Verformung, höhere Spannungen/Dehnungen aus externen Belastungen und Spannungskonzentrationseffekte von/nahe der Oberfläche ausgehen.
Das stark zunehmende Interesse an den schichtweisen Fertigungsverfahren, auch generative Fertigung (additive manufacturing bzw. AM) genannt, hat viele Branchen dazu veranlasst, die Übernahme dieser Technologien in Betracht zu ziehen. Obwohl die AM-Prozesse einfach zu sein scheinen (schichtweise Fertigung), gibt es viele physikalische und metallurgische Komplexitäten, die mit dem wiederholten Schmelzen/schnellen Erstarren während der Herstellung verbunden sind. Die komplizierte thermische Geschichte (d. h. thermischer Gradient, Abkühlraten usw.), die das Bauteil während der Herstellung erfährt, beeinflusst die Mikrostruktur, die kristallografische Textur, die Eigenspannungen, die Oberflächenrauheit und die Bildung volumetrischer Defekte (z. B. Poren mit Gaseinschlüssen und fehlende Verschmelzungen), die folglich die mechanischen Eigenschaften, insbesondere unter zyklischer Belastung, beeinflussen [1, 2]. In diesem Zusammenhang gibt es mehrere Studien, die den Einfluss von volumetrischen Defekten, Oberflächenrauhigkeit und Mikrostruktur auf das Ermüdungsverhalten von generativ gefertigten (AM) metallischen Werkstoffen untersucht haben [3].
Die meisten Studien berichten von einer schlechteren Ermüdungsbeständigkeit für AM-Metallwerkstoffe, selbst im bearbeiteten Oberflächenzustand, im Vergleich zu ihren ausgearbeiteten Gegenstücken, was auf die nachteiligen Auswirkungen von volumetrischen Defekten zurückzuführen ist, die den AM-Prozessen eigen sind [4]. In diesem Zusammenhang wurden viele Anstrengungen unternommen, um die Größe und Anzahl dieser Defekte durch Anpassung der Prozessparameter zu reduzieren. Doch selbst bei Verwendung der optimalsten Fertigungsprozessparameter gibt es immer noch einige prozessbedingte Defekte, z. B. Gaseinschlüsse in den AM-Bauteilen, die deren Ermüdungsleistung verschlechtern können. Nach der Herstellung sind Oberflächen- und thermische Prozesse oft unerlässlich, um das Ermüdungsverhalten von AM-Werkstoffen zu verbessern. In Abbildung 1 ist zum Beispiel zu sehen, dass die Beseitigung der Oberflächenrauheit durch Bearbeitung die Ermüdungsleistung von laserstrahlgeschmolzenem (LB-PBF) 17-4 PH SS deutlich verbessern kann [1]. Ähnliche Auswirkungen der Oberflächenrauhigkeit auf das Ermüdungsverhalten wurden auch für andere Materialsysteme berichtet [5].
Abbildung 1
Vergleich der Spannungs-Lebensdauer-Ermüdung von LB-PBF 17-4 PH SS, das einer CA-H900-Wärmebehandlung unterzogen wurde, mit den Bedingungen der eingebauten und bearbeiteten Oberfläche [1]
Thermische Prozesse nach der Fertigung (z. B. heißisostatisches Pressen (HIP) oder Wärmebehandlung) können das Ermüdungsverhalten von AM-Metallwerkstoffen in Verbindung mit Veränderungen der Mikrostruktur (z. B. Porengröße und -verteilung, Korngröße und -morphologie, Ausscheidungsverhalten usw.) beeinflussen [2,4]. Zum Beispiel verbessern Wärmebehandlungsprozesse nach der Fertigung, einschließlich der Lösungsglühung (bekannt als Bedingung A (CA) für 17-4 PH SS), die Ermüdungsbeständigkeit von LB-PBF 17-4 PH SS (Abbildung 2). Dies wird auf das homogenere und feinere Gefüge zurückgeführt, das nach dem CA-Schritt im Vergleich zu dem Gefüge nach Wärmebehandlungsverfahren ohne diesen Schritt entsteht [1].
Abbildung 2
Spannungs-Ermüdungsdaten von LB-PBF 17-4 PH SS, im eingebauten Zustand der Oberfläche, die verschiedenen Wärmebehandlungsverfahren unterzogen wurde [1]. Beachten Sie, dass die hohlen Markierungen die Wärmebehandlungsverfahren ohne CA-Schritt zeigen, während die gefüllten Markierungen die Wärme Behandlungsbedingungen einschließlich CA-Schritt darstellen.
Interessanterweise zeigen generativ gefertigte metallische Werkstoffe meist ein ähnliches Ermüdungsrisswachstumsverhalten (fatigue crack growth bzw. FCG) wie das des ausgefertigten Gegenstücks im Paris-Regime (d. h. im Bereich des stabilen Risswachstums). Abbildung 3 ist ein Beispiel, das zeigt, dass LB-PBF 17-4 PH SS ein identisches FCG-Verhalten im Vergleich zum ausgefertigten Werkstoff aufweist [6]. Das LB-PBF 17-4 PH SS zeigt jedoch eine höhere FCG-Rate (d. h. einen geringeren FCG-Widerstand) im instabilen FCG-Bereich (d. h. im hohen ÄK-Bereich) im Vergleich zum ausgefertigten Werkstoff. Dies kann auf die Unterschiede in der Mikrostruktur sowie auf das Vorhandensein von volumetrischen Defekten in LB-PBF 17-4 PH SS zurückzuführen sein, die zu einer geringeren zyklischen Bruchzähigkeit führen als die des ausgefertigten Werkstoffs. Solche Defekte können auch die FCG-Rate von LB-PBF 17-4 PH SS im schwellennahen Bereich erhöhen.
Abbildung 3
Ermüdungsrisswachstum (FCG) von LBPBF 17-4 PH SS, das einer CA-H900-Wärmebehandlung unterzogen wurde, im Vergleich zu dem des gefertigten Werkstoffs mit derselben Wärmebehandlungsbedingung [6]
Referenzen
1. Nezhadfar PD, Shrestha R, Phan N, Shamsaei N. Int J Fatigue. 2019;124:188-204.
2. Pegues J.W., Shao S., Shamsaei N., Sanaei N., Fatemi A., Warner D.H., Li P., Phan N., Int J Fatigue, 2020: 132, p.105358.
3. Fatemi A, Molaei R, Simsiriwong J, Sanaei N, Pegues J, Torries B, Phan N, Shamsaei N., Fatigue & Fracture of Eng. Mater. & Struc. 2019: 991-1009.
4. Molaei R., Fatemi A., Sanaei N., Pegues J., Shamsaei N., Shao S., Li P., Warner D.H., Phan N., Int J Fatigue, 2020: 132, p.105363.
5. Pegues J., Roach M., Williamson R. S., Shamsaei N. Int J Fatigue, 116, 2018: 543-552.
6. Nezhadfar PD, Burford E, Anderson-wedge K, Zhang B, Daniewicz SR, Shamsaei N., Int J Fatigue. 2019.
Das National Center for Additive Manufacturing Excellence (NCAME) an der Auburn University wurde 2017 durch eine Zusammenarbeit mit dem NASA Marshall Space Flight Center gegründet.