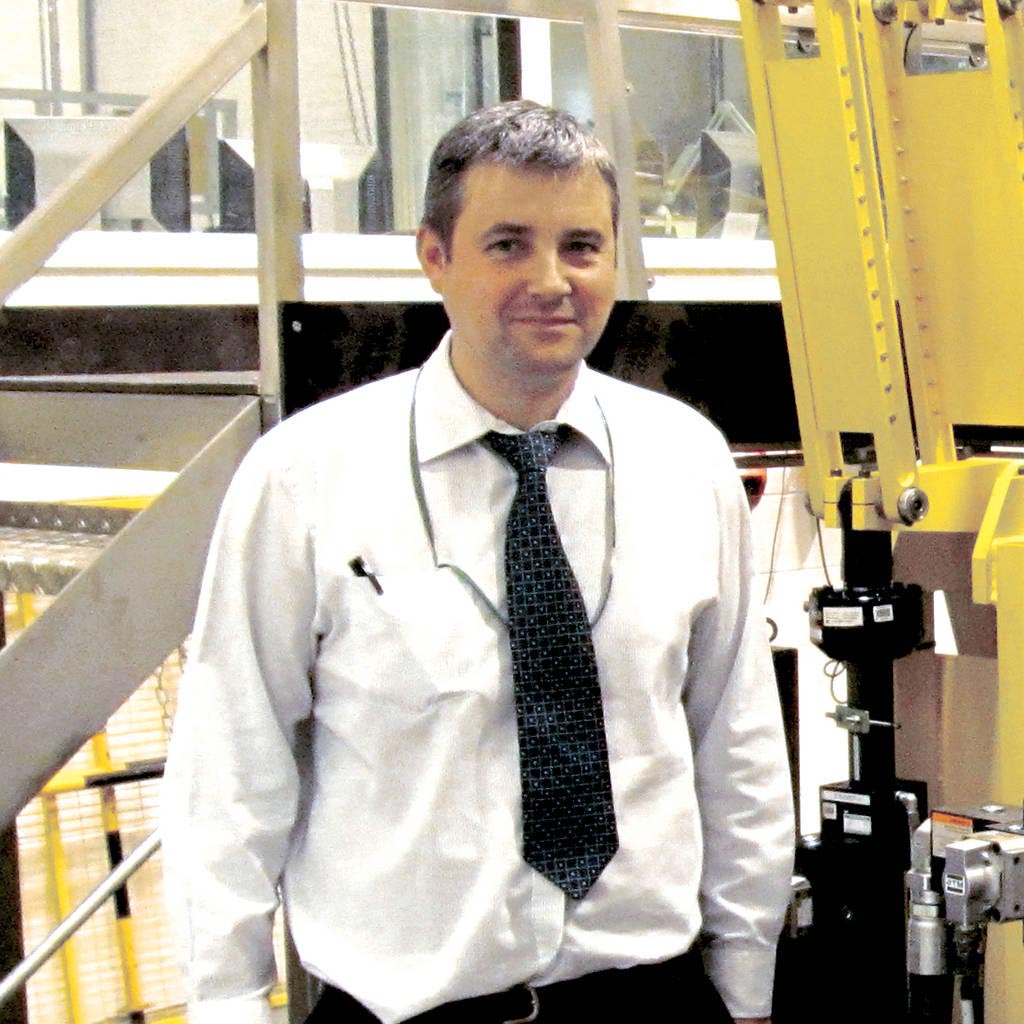
お客様の挑戦
ジャガー・ランドローバー(JLR)は、多様な車種を提供しており、世界的に有名な高級車や四輪駆動車を製造しています。こうした車種の開発を継続的に支援するために、英国内の 2 つの拠点では、構造試験エンジニアが多数の構成部品、サブシステム、車両プロトタイプのバッテリー耐久試験を常に実施しています。この取り組みをリードしてきたのは、製品解析・検証のグループリーダーである Ian Payne 氏です。Payne 氏のチームは、テストリグを使って構成部品のレベルから車両全体シミュレーションまで、あらゆるJLR製品の強度と耐久性の評価を担当しています。
「我々は、すべてのラボで単軸リグから最先端の車両全体のロードシミュレーターに至る範囲で、機器の設計、製造、操作を行っています」と Payne 氏は述べています。「私たちは車両耐久性検証の基盤を支えています。収集データは、ビジネス全体の製品開発を支援しています。」
Payne 氏が直面している最大の課題の一つは、新製品の市場投入までの時間を短縮して、より早くより良い結果を出さなければならないことで、常にプレッシャーを常に受けています。そのため、Payne 氏と彼のチームは、試験の精度と効率を向上させようとあらゆる機会を模索しています。彼らがこの問題に取り組んでいる一つの方法が、複数の個別テストを一つのデータ豊富なシミュレーションにまとめるという試験の統合です。
「試験時間を最適化することが我々の最優先事項です」と Payne 氏は述べています。「マイナス面は、試験がより複雑になっていることです。可変ダンピング、アクティブロール、アクティブディファレンシャルなど、我々の車両に搭載されているすべてのアクティブシステムをシミュレートし、その複雑な要素をすべてリアルタイムの試験でテストに組み込むことは非常に困難です」。
MTS のソリューション
今日、JLR は MTS の MAST(Multi-axial Simulation Table)システムを使ってこの課題を解決しています。Payne 氏のチームは、MAST システムを使用して、ボディ入力、エンジンマウントの構造負荷、トルク入力治具(TIF)によるリアルタイムのトルク負荷で、パワートレインやドライブトレインを含むエンジンマウントシステム一式の構造的耐久性を検証しています。
「私たちはリアルタイムでシミュレーションを実行し、相関性がある予測車両寿命により構造的耐久性を立証しています」と Payne 氏は述べています。「MTS の MAST システムでは、エンジンマウントシステム全体を一度に見ることができます。これによりボンネット下のパッケージングやワイヤーハーネスなど、車両のパッケージングにも目を向けることができます。我々にとって素晴らしいツールです。」
MTS MAST システムでは、直交型とヘキサポット型の両方の構成が利用でき、管理されたラボ環境で実際の使用環境の振動現象を正確に再現するよう設計されています。Payne 氏のチームが採用した直交システムは、 2 × 3 メートルの正方形で無共振テーブルを備え、6 自由度(6DOF)のシミュレーションが可能で、3 台の垂直アクチュエーターが垂直、ピッチ、ロールの動作を、3 台の水平アクチュエーターが横、偏揺れ、縦の動作を実施します。
「我々は、試験中にエンジンマウントに正しい平均負荷がかかるように、パワートレインに通常、縦および横、 必要に応じて垂直の直接制御負荷をかけています」と Payne 氏は述べています。「かなり大きなテーブルです。これにより、V8 エンジンで 4 x 4 のフロントパワートレインシステム全体を搭載することができます。私たちはテーブルは 30 Hz まで、ドライブのトルクは 20 Hz までの周波数で実行しています」。
お客様のメリット
Payne 氏によると、以前は別々に行われていた多くの試験を 1 つにまとめるためには MTS MAST システムが不可欠です。具体例として、MAST システムは設計が頑丈で高い最大積載量を持つため、Payne 氏のチームは試料の質量を最大限に増やすことができます。また、精密な 6DOF モーションコントロールには、あらゆるスペクトルのプロトタイプ検証に必要なすべての試験機能が用意されています。
「私たちはできる限り多くの試験を 1 つの物理的なプロトタイプにまとめようとしています」と Payne 氏は述べています。「より複雑ではありますが、実際には開発にかかる時間を大幅に短縮できています。また、システムの相互作用がすべて連動しているため試験はより安定しており、より現実的です。」
現実性が増すということは、単一の MAST 試験だけで、テストトラック上でプロトタイプに生じると JLR チームが予想する、実際に生じる不具合の多くを明らかにできることを意味しています。性能試験場に来る前にこれらの不具合を理解し対処すると、効率が上がり、市場に投入するまでの時間を短縮することができます。
「6DOF 試験では、実車全体の構造的耐久性について大きな洞察を得ることができます」と Payne 氏は述べています。「MAST システムはこの業務に最適です。より複雑な完全な車両のシミュレーションの作成および試験を組み合わせることについては、当面 MAST システムと 6DOF 試験に焦点を当てるつもりです。」
もちろん、試験システムは完全なソリューションの一部分に過ぎません。また、MTS は業界をリードするテストソフトウェアおよび専門家によるサービスとサポートを提供しており、Payne 氏のチームはこれにも信頼を寄せています。
「MTS から私たちは素晴らしいサポートを受けています」と Payne 氏は述べています。「私たちは、MTS チームの全員と強固な関係を築いており、現場サービスの技術者がもたらす専門知識に大きな敬意を払っています。彼らの技術的な知識は非常に高く評価されており、私たちが前進していく上で非常に貴重なものとなるでしょう。」