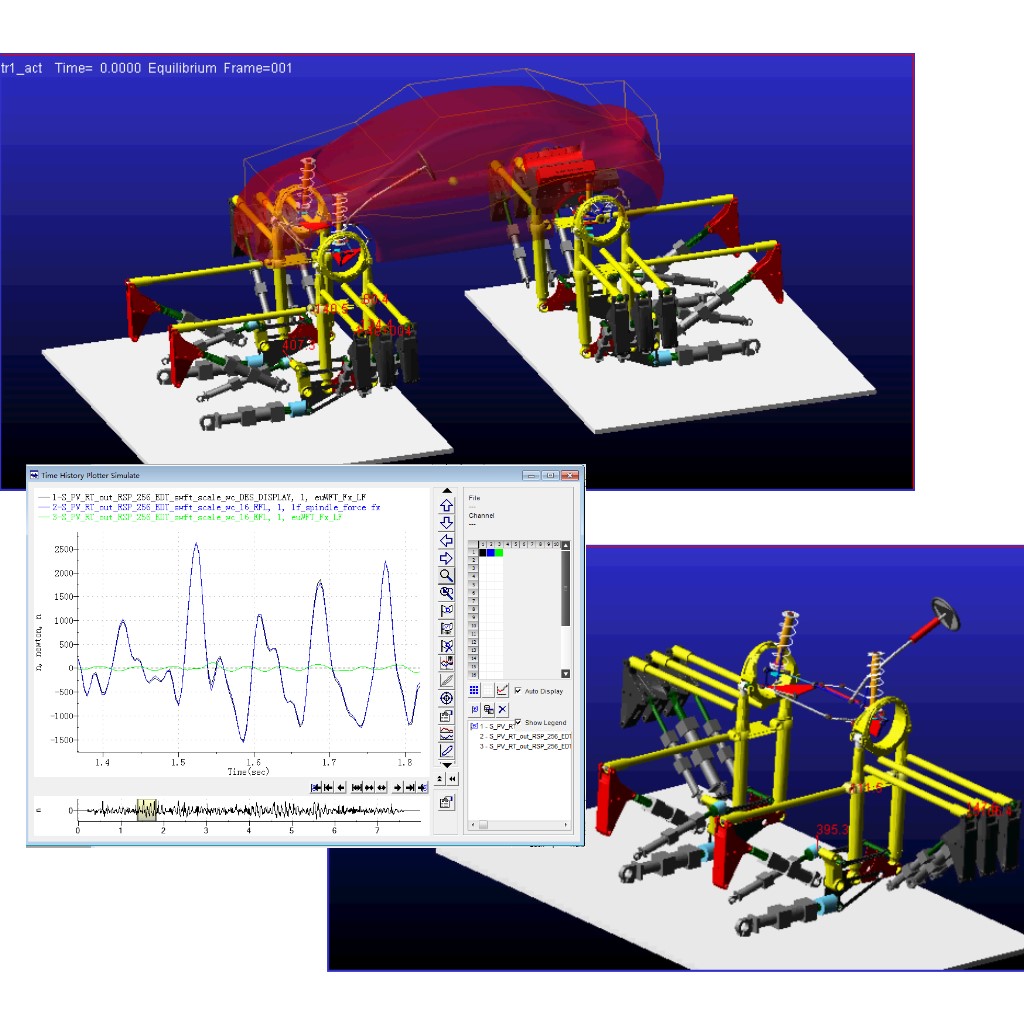
自動車メーカーは、開発期間の短縮とコスト削減のために、物理的なプロトタイプができるかなり前の段階で車両設計の意義ある仮想的評価を早期に実施するため、解析ツールを使う方法をますます模索するようになっています。このようにして正確な予測負荷(計算負荷)を得ることができれば、部品の物理試験の効果を高めることができ、 設計上の欠陥を早期に発見して取り除くことができ、手直しの必要性やプロトタイプへの依存を減らし、設計検証を効率化することができます。
車両開発の初期段階で正確な負荷計算を行うために、様々なシミュレーション手法が考案されています。シミュレーション手法の 1 つであるバーチャル性能試験場は、デジタル化された道路上で車両モデルを「運転」する方法です。この方法は、バーチャルモデルに全面的に依存するという利点がある一方で、物理的な試験で検証することが困難な不正確な負荷をもたらします。一方、半解析的手法は、既存の車両から得られるスピンドル負荷を用いて車両モデルを加振するものです。この方法では、バーチャルの性能試験場よりも良い結果が得られますが、車両モデルに完全には適していない境界条件が設定されるため、計算された負荷は依然として正しくなく、検証も困難です。第 3 の方法であるバーチャルテストは、実際の物理的な試験システムのモデルをシミュレーションに統合し、車両モデルを加振することで、これらの問題を克服します。
バーチャルテストとは、有限要素解析ツール、多体動力学解析ツール、RPC 反復技術を用いて、開発プロセスの非常に早い段階で車両システムの正確な愚化、動作、損傷情報を導き出す物理的な試験のシミュレーションです。このアプローチの利点は数多くあります。第一に、物理的な試験システムの制約条件をモデル化することは、性能試験場の路面やタイヤのモデル化よりも容易であるため、バーチャルテストは他の方法よりもはるかに効果的な境界条件を設定することができます。 第二に、バーチャルテストは、解析の領域で実用性が実証されている、定評のある物理的な試験ツールやテクニックを活用しています。そして3 つ目は、モデル化された物理試験システムを組み込むことで、その後の物理試験による結果の検証が大幅に効率化され、物理試験のセットアップや治具の設計を改善する機会が得られることです。解析と物理試験の分野にまたがるバーチャルテストでは、CAEツールと物理試験の両方に関する高度な知識、RPC Proソフトウェアと解析モデルをリンクさせるプロセスの開発、そしてできればある程度のバーチャルテストの経験が求められます。
長年にわたり、MTS はバーチャルテスト手法の改良に注力し、Hyundai Motor Company (HMC) や Thermo King などの主要顧客と様々な実証プロジェクトを実施し、様々な方法論を評価してきました。これらのプロジェクトでは、完全車両やサブシステムのバーチャルテストが行われ、いずれも路面負荷データ(RLD)の測定値や実際の物理的な試験と十分な相関関係が得られました。これらの経験から得られた基本的な方法論は、以下のステップで構成されています。1)テストリグモデルと試料モデルとの接続。2)RPC Pro でモデルをカップリングする。3) バーチャルテストリグでの路面負荷データの再現。4) 算出された負荷を抽出。5) 物理的な構成部品/サブシステムの試験の作成。
最近の中国国家汽車研究所(SAIC)との実証プロジェクトは、この方法論を実践した素晴らしい例です。
- テストリグモデルと試料モデルとの接続
MTS はプロジェクト開始時に、ADAMS、Simulink、そしてADAMS-Simulink の協調シミュレーション形式のテストリグモデルのコレクションを構築しました。モデル化された MTS のテストリグには、329 モデルスピンドルカップル式ロードシミュレータ、モデル 353.20 多軸シミュレーションテーブル(MAST)システム、TestLine 部品試験システムなどがあります。また、FlexTest のデジタルコントローラ、MTS のアクチュエータとサーボバルブ、アクチュエータの変位、加速度、力を DOF の変位、加速度、力に変換するアクチュエータトランスフォームなど、テストリグの構成部品もモデル化しました。プロジェクトの時間的制約と、より複雑な協調シミュレーションモデルのシミュレーション速度が比較的遅かったため、ADAMS/Car 329 モデルと SAIC の完全車両、フロントサスペンション、リアサスペンションモデルを結合し、最終的にバーチャルテストの大部分に使用しました。
- RPC Pro でモデルをカップリングする
RPC Pro ソフトウェアと ADAMS/Car 329 モデルを接続するバーチャルテストサーバーを開発しました。試験中、RPC Pro はこのバーチャルサーバーを使用して、ADAMS モデルへのドライブファイルの送信、ADAMS シミュレーションの開始、ADAMS フォルダから RPC Pro のワーキングディレクトリへの応答ファイルのコピーを行います。さらに、RPC Pro と強調シミュレーションモデルを連携させるために、RPC Pro にすでに搭載されている Matlab Interface Tool を使用しました。
- バーチャルテストリグでの路面負荷データの再現
そして、RPC の反復手法を用いて、さまざまなイベントやマヌーバで性能試験場から収集した路面負荷(スピンドルフォース)のデータを再現しました。興味深いことに、バーチャルの 329 リグに対する最初の RPC 反復処理では収束が見られず、SAIC の車両モデルに欠陥があることが示唆されました。その後、モデルの解析を行ったところ、確かに不備が見つかり、すぐに修正されました。モデルが改善されたことで、RPC の反復処理は最終的に収束し、完全車両および部分車両の両方のバーチャルシミュレーションにおいて、希望信号と達成信号の間に優れた相関関係が見られ、すべてのチャネルでRMS エラーは低いものでした。
- 算出された負荷を抽出
RPC の反復が収束すると、あらゆる機械構成部品やサブシステムの負荷計算が、時間の関数として車両モデルから容易に得られるようになります。
- 物理試験の作成
車両モデルから抽出された負荷時間履歴は、その後の物理的な部品試験を定義するために使用されました。部品が単軸または多軸のどちらの負荷にさらされるかが決定されると、RPC Pro の試験方法とツールを使用して、大幅に加速された部品試験を定義することができます。単軸負荷の部品には、ブロックサイクル法やスペクトル密度(PSD)法を用いることができます。多軸負荷がかかる部品には、ピークバレースライシング法を用いることができます。部品の負荷頻度を維持する必要がある場合には、時間履歴再現法が最も適しています。このようなタイプの試験のため、RPC Pro には、耐久性試験を 2~10 倍に加速する可能性のある Fatigue Sensitive Editing 機能が搭載されています。各部品の負荷信号が決定されると、バーチャルテストリグが基礎とする試験システムと同じ物理的な試験システムを使用して部品試験を実施することができます。さらに、「RPC Pro」に搭載されているピークバレー補正、アダプティブ・インバース補正、RPC 反復などの様々な補正技術を使用することで、物理試験時に希望の負荷条件が正確に実現されるようにすることができます。
MTS が継続的に行っているバーチャルテストは、物理的な部品やプロトタイプの開発に先立ち、部品への負荷を正確に予測するための有効な手段であることを示しています。これらの計算された負荷が得られれば、それを得るために使用されたのと同じ RPC Pro ツールと技術を使用して、その精度と車両モデルの精度を検証するために必要な物理的試験を作成し、実施することができます。効率的なバーチャルテストが車両開発に与える潜在的な影響は大きいものがあります。正確な予測負荷とそれに続く早期の物理試験が可能になることで、構成部品やサブシステムの手直しを最小限に抑え、いくつものプロトタイプの必要性を減らし、設計検証を迅速に行うことができます。また、物理試験の役割も進化していきます。試験は車両設計の最終的な検証のために必要であることに変わりはありませんが、車両モデルの精度を検証するために今後ますます行われるようになるでしょう。そして仮想試験は、最終的には解析と物理試験の分野や文化要素の統合を促し、ツール、プロセス、経験を共有することで新たな効率化を実現することでしょう。
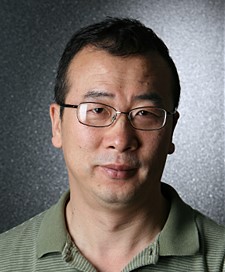