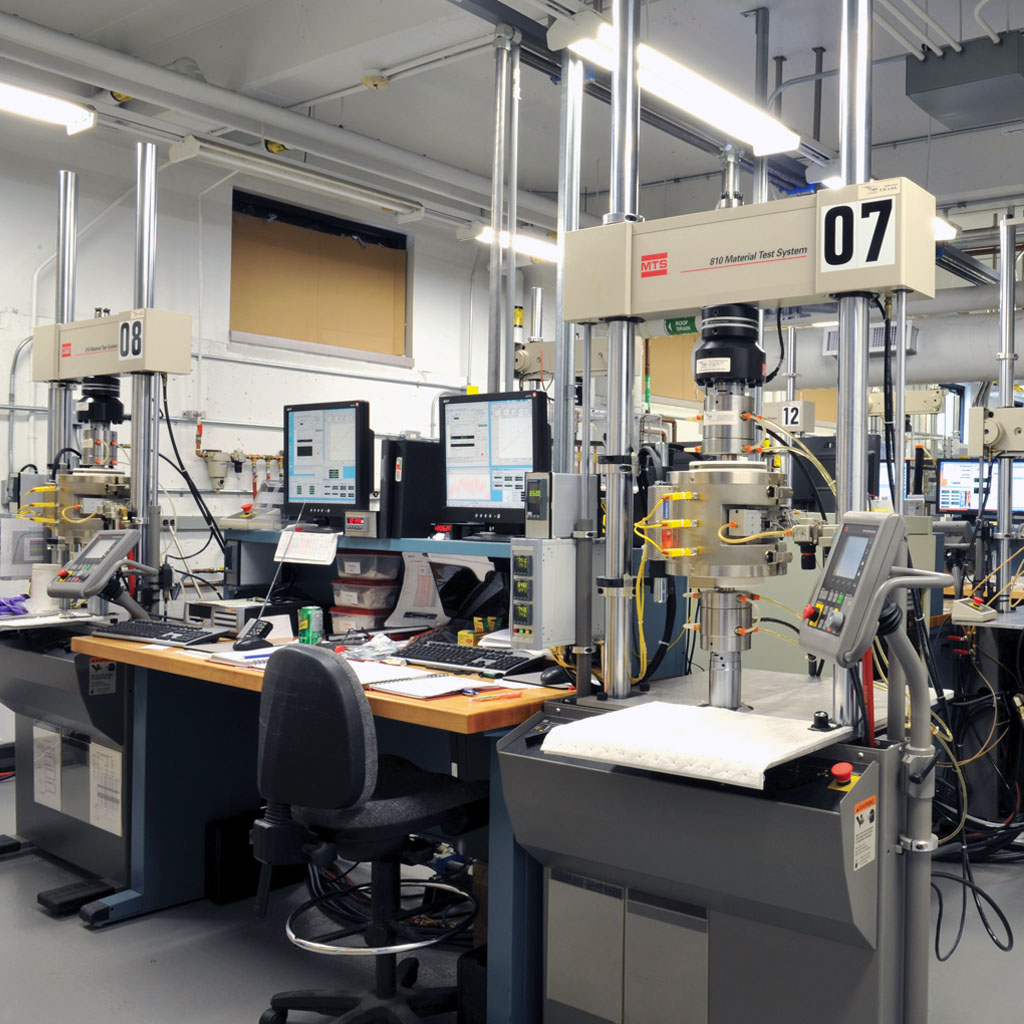
お客様の挑戦
極限温度かつ長時間使用可能な高温材料の開発は、燃料効率の期待を一新する次世代のジェットエンジンやガスタービンの開発につながるものです。この分野の最先端の研究は、オンタリオ州オタワにあるカナダ国立研究評議会の航空宇宙研究所内にある構造材料性能研究室で行われています。
ここでは、15人の研究者からなる材料・コンポーネント技術グループが、高温合金やセラミックマトリックス複合材などの新しいガスタービン材料の設計、開発、試験を専門に行っています。グループ内での研究はもちろん、Pratt & Whitney、Rolls-Royce、General Electric といった民生エンジンメーカーおよび ATI Allvac や Carpenter Technologies などの素材ベンダーとの協業も進めています。高温にさらされた新素材の性能や寿命を正確に把握するためには、さまざまな精密機械試験を行う必要があります。
「当社は、引張試験、クリープ試験、破壊靱性試験から、フレッティング疲労、熱機械疲労、疲労亀裂成長、クリープ亀裂成長率などのより専門的な試験まで、あらゆる試験を行っています」と語るのは、このグループの高温疲労/破壊力学施設のマネージャーである Kearsey 博士です。「当社は、材料を開発して試験を行い、材料の特性を評価するための標準的な試験方法を開発しています。これには、試験片の形状を把握することや、エンジンの使用環境を実験室で再現することなどが含まれます」
今、カーシー博士の最大の課題はシンプルで、それは熱です。過去数十年の間、ステンレス鋼、チタン、アルミニウム合金の試験温度は比較的緩やかなものでした。現在の最先端の素材の試験には、25%も高い温度が求められます。
「温度が非常に高いので、材料のテストはより複雑な問題になります」と彼は言います。「標準作業では定格 800℃ の機器を使っているのに、どうやって 1000℃ で材料を測定しますか?クラック成長率を測定するために、適切な計測器をどのように追加しますか?それは不可能ではありませんが、非常に複雑です。当社の結果は重要なエンジン部品の製造に使用されるため、温度と負荷が100%トレーサブルであることの絶対的な確認が必要です」
MTS のソリューション
材料/コンポーネント技術グループでは、高温試験用に 18 種類の MTS ソリューションを導入しており、そのラインナップは、従来の MTS 810 負荷フレームから最先端の MTS Landmark® 油圧サーボ試験システムまで多岐にわたっています。
「当社が MTS の負荷フレームしか使わない理由は、安定性です」と Kearsey 博士は述べました。「4 台または 5 台のフレームを並べて実行すると、研究所が揺れるんです。MTS のフレームは非常に安定しており、試験片の位置を狂わせるようなねじれや捻れはありません」
施設内の試験装置としては、2 台の MTS の油圧式パワーユニット、FlexTest® デジタル制御装置、多目的 TestWare® ソフトウェアがあります。また、この研究所では、グリップや固定具、伸縮計やひずみゲージ、炉や誘導加熱装置など、MTS の試験アクセサリをフル活用していますが、これらはすべて、特定の高温試験に必要な複雑な構成に簡単に組み合わせ、統合することができる必要があります。
「ハードウェアは、さまざまな試験温度や条件でも適切に動作する必要があります」と Kearsey 博士は語ります。「MTS の炉は、どのような負荷フレームにも取り付けられるのが良いですね。特に再現性を高めるためには、互換性が重要です。同じような形状のテストを 100 回行わなければならないとき、いちいち較正をやり直すのに時間をかけたくありません」
お客様のメリット
Kearsey 博士は、テストのハードウェアとソフトウェアの信頼性を最も重視しています。信頼性は、結果の正確さ、研究所の生産性、外部顧客の満足度のために不可欠です。
「MTS の機器を購入しているのは、ほとんど故障しないからです」と彼は言います。「交換する必要はありません。信頼でき、追跡も可能です。研究所として、トレーサビリティーは重要な要件です。あるシステムで調整を行ったら、次の試験でもその通りになることを確認しなければなりません。それは、最先端の単結晶合金をテストする場合でも、50 年前の合金を寿命予測モデリングのために評価する場合でも同じです。MTS の試験装置を使うことで、自信を持って決断を下すために必要なデータを生成することができます」
伸縮計の信頼性は、高温材料の試験において、特に 10 Hz までの周波数や、測定された反射が小さくなるような硬い材料では特に重要です。Kearsey 博士は、ソフトウェアの信頼性も重要な要素として挙げています。
「例えば、熱機械疲労試験を行う場合、試験は 3 ヶ月に及ぶこともあります」と博士は述べました。「それはお客様にとって非常に高価なものです。テスト中にソフトウェアが故障したので、結果が無効になってしまいましたなどとは、絶対に言いたくありませんね。その点、MTS のソフトは、そのような頭痛の種を与えない点において非常に重要です。信頼性が高く、多くのモジュールが低サイクル疲労、熱機械疲労などのテスト用にあらかじめプログラムされています」
現在、Kearsey 博士は、1000℃ でのテストに伴う課題の克服に取り組んでおり、上限値を上げることを期待しています。実際、博士は MTS と協力して、はるかに高い温度で動作する試験システムを設計しているところです。
「新しい合金がセラミックマトリックス複合材に置き換わると、1300℃ や 1400℃ までのテストを行う必要が出てきます」と彼は言います。「MTSとはすでに実現に向けて話し合っています。どのくらいの大きさの炉が必要になるか?ホットゾーンはどうなるのか?どのような伸縮計が必要なのか?MTS は、いつも適切なタイミングで当社に協力してくれます。このようなサポートがあるからこそ、当社は MTS に戻ってくるのです」