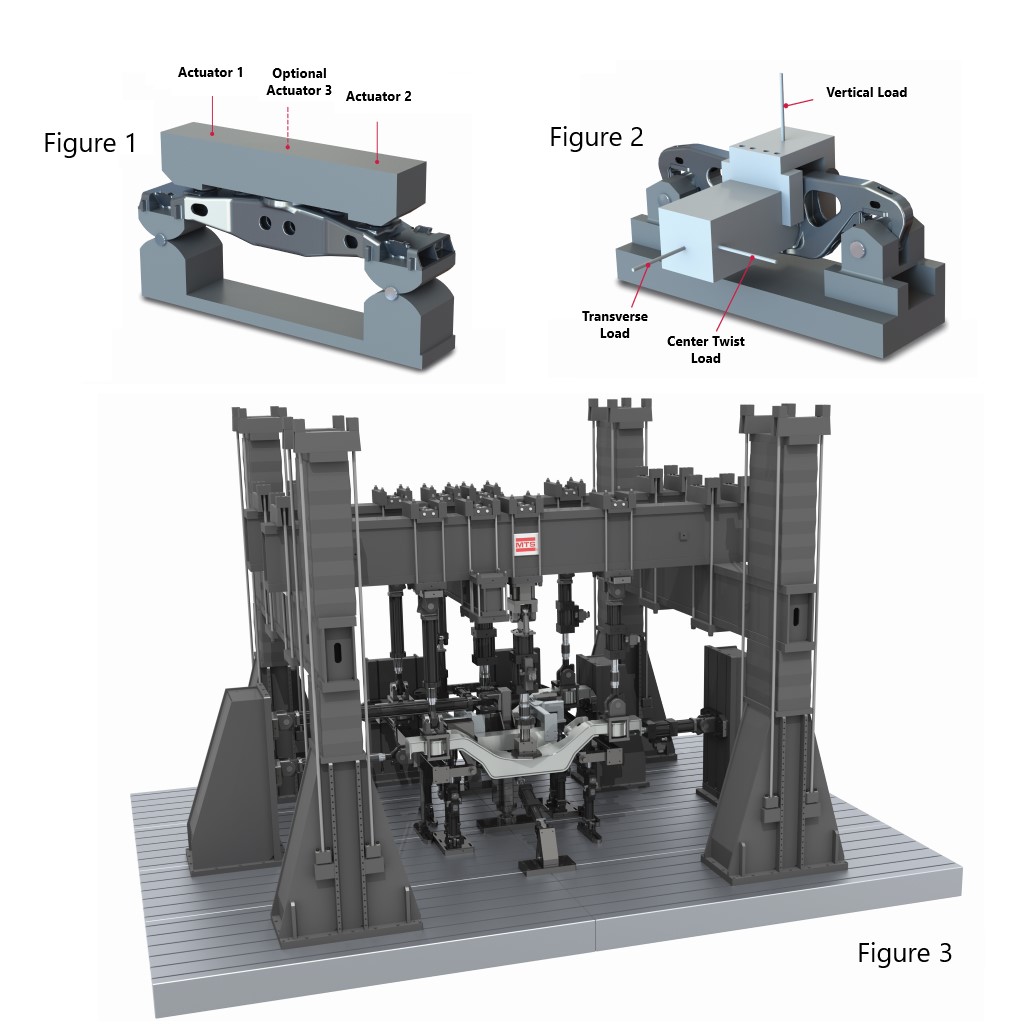
車両システムとその周囲環境を構成するすべての構成部品と部分組立品を考えるとき、レールの先端に沿って想像上の線を引くのに役立ちます。この線は、システムを大きく 2 つのグループに分けます。線上に位置する最初のグループは、台車フレーム(または 2 つのサイドフレームとボルスターの組み合わせ)と、一次および二次サスペンションと鉄道車両に代表される「車両」です。線の下に位置する第 2 のグループは、レール、ファスナー、枕木、バラストなどの構成部品に代表される「道」です。この 2 つのグループ間のインターフェイスは、ホイールセットを持つ車軸です。
このシステムの単純な要素の多くは、基本的な部品試験によって対処することができますが、鉄道車両内の構成部品や部分組立品を評価するには、次の 3 つの同様に重要な要素を考慮する必要があります。疲労、性能、および快適性。
疲労寿命は、乗客が乗車中に評価する(あるいは考える)ものではないかもしれませんが、鉄道車両の設計とサービスにおいて非常に重要な部分を占めています。前世紀の間に、鉄道業界は、鉄道部品の設計および製造における疲労試験の重要性を理解し、認識するようになりました。一貫した疲労寿命と乗客の安全性を確保するために、多くの認証基準が策定されています。
認証基準を満たす
鉄道部品やサブシステムのメーカーは、ボルスターの M-202-97、サイドフレームの M-203-05、台車の UIC615 などの国際規格を含む、適切な認証基準を満たすように構成部品やサブシステムを試験しなければなりません。これらの基準は、新しい部品の疲労寿命や耐久性を確立するために使用される試験を定義するのに役立ち、乗客、貨物、路面電車の安全で長期的な運用を確保するために不可欠なものです。
台車、ボルスター、サイドフレームの認証試験では、メーカーが特定の構成の台車構造や構成部品で安全性と信頼性の試験を行うことが求められます。静的および動的負荷をかけて、性能、強度、耐久性を評価します。試験結果には、降伏荷重、極限破壊荷重のレベル、および疲労寿命のデータが含まれています。
ボルスターを正しく試験するには、3 つの荷重が必要です。ロック荷重、センターバウンス、エッジバウンス(図 1 参照)。これらの荷重は、ボルスターが実際に使用される環境で受ける力を表しています。サイドフレームについても、3 つの荷重が必要です。縦方向、横方向、センターツイスト(図 2 参照)。これらの別々の力のベクトルはすべて、試料に適切な荷重と応力分布を与え、適切な疲労寿命を確保するために重要です。
ボルスターやサイドフレームの試験には、適切な評価を受けた床置きの負荷フレームが理想的で、固定も比較的簡単です。しかし、台車フレームの疲労試験は、より高度で複雑です。台車の認証試験は、国際規格や地域の規格で定められており、より多くのチャネル数とより複雑な治具が必要となります。試験の荷重構成は、台車の構成に基づいています。台車 1 台あたりの軸数、鉄道車両 1 台あたりの台車数、台車と鉄道車両の合計重量などが、試験に必要な荷重を決定するパラメータとなります。認証試験では、多チャネルの高荷重システムが必要で、通常は数百万回のサイクルを実行します。試験中、ひずみやその他の信号を収集し、分析することで、設計者がサービス環境の荷重力学を理解し、高応力の領域を特定し、それに応じて設計を改善するのに役立ちます。有限要素解析(FEA)モデルとひずみ応答を比較することで、エンジニアはモデルを検証し、将来の設計を改善することができます。
高度な疲労試験
認証基準は数百万回の負荷サイクルを伴う厳しいものですが、十分な疲労寿命と安全率を検証するために必要な最小限の負荷(縦方向、横方向、反り)にのみ焦点を当てています。これらの負荷は、通常の運転時に想定される負荷よりもかなり高いものです。負荷履歴は、あらゆる使用方法の組み合わせで故障率が限りなくゼロに近づくよう、あえて保守的に作成されています。この方法は、一般的な貨物用の台車に適していることが証明されており、世界中で(何らかの形で)採用されています。
しかし、現代の旅客用鉄道車両では、台車、サスペンション、車両のインターフェイスが貨物用に比べてはるかに複雑になっています。高速旅客機の台車は、複雑な溶接構造になっています。ダンパー、サスペンションリンク、補助機器(コンプレッサー、ブレーキキャリパー)などのアイテムは、すべて台車に負荷をかけます。これらの負荷は、多くの場合認証基準に記載されているものとは全く異なる負荷ベクトルと位置で構成されています。これらの負荷の位置、大きさ、ベクトル、位相は、実際の台車の動作環境を可能な限りリアルに再現したいと考えている試験エンジニアにとって重要な考慮事項です。
このような状況では、複雑さがすぐに問題になります。認証試験では通常 10 チャネル以下(ほとんどの場合 6 チャネル以下)しか使用しませんが、より高度な開発試験では 20 以上(場合によっては 30 チャネル以上)の制御チャネルが必要になることもあります。認証基準で定められた負荷に追加の負荷を組み合わせることは、治具の面で大きな課題となります。
この複雑さに対処することは不可欠です。この 10〜15 年の間に、エンドユーザーの間では、より高い信頼性、より優れた性能、より快適な乗り心地を備えた鉄道車両の需要が大きく高まっています。このようなニーズに応えるために、メーカーは、認証基準が確立された当初にはなかった材料や製造方法を開発しています。鉄道システムを構成するほぼすべての構成部品の設計および製造に使用されている新素材、特に新しい軽量化手法は、従来の認証試験の範囲を超えた新しい開発試験手順を必要としています。
このような大規模な構造のアプリケーションでは、カスタムアクチュエータ構成の 2 柱または 4 柱のポータルフレームが必要となります(図 3 参照)。台車にかかる力は大きいものが多いため、その負荷を再現するためのアクチュエータも大きくなります。アクチュエータを荷重点に直接適用すると、複数のアクチュエータが同時に同じ物理的空間を占有する必要がある場合があります。この問題を解決するには、治具や運動学的機構に関する相当な専門知識が必要です。アクチュエータ、レバー、ストラット(耐荷重柱)、軸受などを組み合わせて、負荷ベクトルを正しい位置に適用します。負荷センサは、アクチュエータ、荷重ストラット、リアクション治具に取り付けることができます。ストラットとアクチュエータの両端の自在軸受で、側面荷重や曲げ荷重を排除します。場合によっては、荷重点へのアクセスを良くするために、試料を反転させることもあります。
クロスカップリングとは、あるアクチュエータの動作が別のアクチュエータに影響を与える際に、解決しなければならない制御上の重大な問題のことです。デジタルコントローラとソフトウェアが連携して、影響を受けるチャネルの振幅と位相を調整し、干渉のリスクを取り除き、正確な負荷を確保する必要があります。一般的には、高度な制御技術が必要です。試料、フレーム、アクチュエータのサブシステムを含むシステム全体には、いくつかの自然な非線形性が含まれている可能性があります。このような非線形性を考慮すると、試料に望ましい負荷履歴を実現するために駆動信号を変更する必要がある場合があります。
調整は通常、MTS リモートパラメータ制御(RPC®)などの高度な信号処理ソフトウェアを使用し、システム全体の周波数応答関数(FRF)マトリクスに基づいて行われます。このソフトウェアは、コントローラのコマンドを測定し、それを目的の周波数範囲における試料の応答の振幅および位相と比較します。コマンドと応答の間のすべてのクロスカップリングおよびその他の線形差分を含むクロスカップリングマトリクスが生成されます。この FRF を反転させ、目的の応答を乗算します。その結果が、クロスカップリングや関連する問題を補正するアクチュエータのドライブファイルです。非線形的寄与の補正は、誤差を計算して対応する補正ファイルを作成し、その補正を前のドライブファイルに適用することで行われます。この繰り返しのプロセスは、目標精度が得られるまで繰り返されます。このような制御補正技術を適用することで、はるかに高い周波数で正確に試験を実行することができ、試験時間の短縮と試験品質の向上につながります。
その間、エンジニアは大量のデータを収集し管理できなければなりません。試験システムは、設計の潜在的な脆弱性を見つけるために、例えば最大 250 個のひずみゲージと変位チャネルを収容する必要があります。これらのデータの一部は、制御システムで使用するためにリアルタイムで収集する必要がありますが、一方で、オフラインでの分析や CAE(コンピューター援用エンジニアリング)モデルとの比較のために、さらに大量のデータを収集する必要があります。
これらの課題をすべて克服することは困難ですが、投資する価値はあります。その結果、部品メーカーは設計を最適化し、新製品を差別化し、新しい部品の品質と信頼性に対して顧客が必要とする確信を提供することができます。
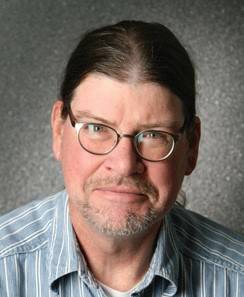