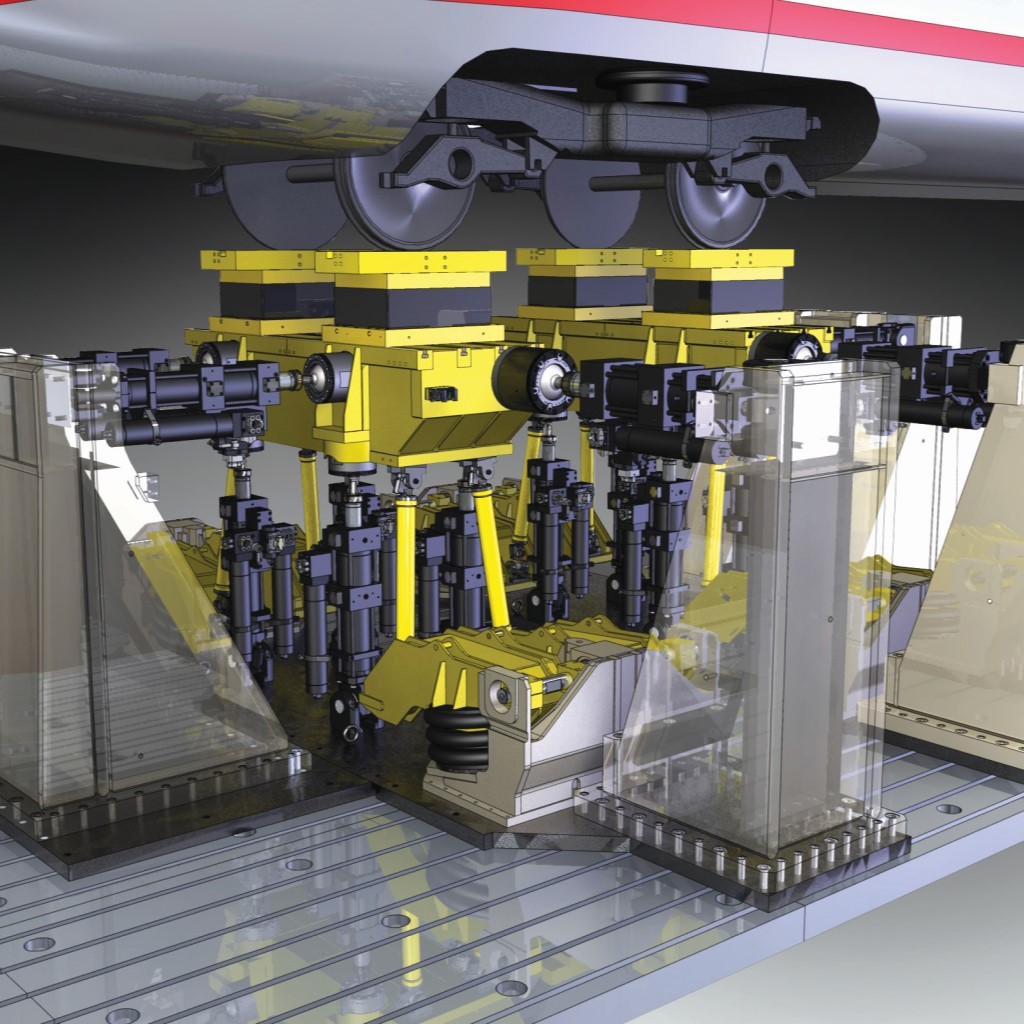
鉄道旅行の世界的増加に伴い、新しい鉄道車両に対する需要が高まっていることは世界中のメーカーにとって喜ばしいことです。同時に、これらの新型車両はより高い期待に応えなければなりません。最新の旅客鉄道車両は、高速走行、快適な乗り心地、エネルギー効率の最大化、そしてもちろん規制準拠への完全対応が求められます。
これらのニーズに同時に対応するには、設計上の難しい課題があります。重量を取り除くことで効率性は向上しますが、安定性に影響を与えることはできません。高速になると安定性が低くなりますが、現在、世界最速の鉄道車両は時速 350km で走行しています。また、高速走行時には乗り心地が悪くなります。
これらの要素は関連しているため、メーカーはトレードオフを効果的に管理するために新設計を最適化する能力が求められます。例えば、ボギーを硬くすると安定性は向上しますが、乗り心地は悪くなります。ロールバーの剛性を変えればハンドリングや乗客の快適性を向上させることができますが、その両方を同時に実現することはできません。
製品開発チームは市場の高い需要によって厳しい時間的制約にさらされていて、設計者は迅速な作業を求められます。このような場合、機械試験が特に有効です。
ラボでの挑戦
試験ラボでは、部品設計者は高度に制御された再現性のある方法で、新設計の多くのイタレーションを比較的早く検討できます。試験結果からは、部品やサブシステムのバーチャルモデルにフィードバックして精度を向上させるための係数などが得られます。これにより、新設計の分析と改善のプロセスを迅速に実施できます。
ラボにはには各々の課題があります。関連試験のリストは長く、それぞれの試験には通常、独自のセットアップを備えた違う種類の試験システムが必要です。新しい台車の設計を最適化するために必要なシステムを取得するには費用がかかります。複数のシステムを使用している場合、試験の構成や実行が非効率になる場合があります。
中でも最大の課題は、構成部品だけでなくメカニズム全体の試験が必要である点です。直感的には理解できないかもしれませんが、高度な設計技術者は、個々の部品を試験しても、台車全体を試験するのと同じ精度や洞察を得られないことを理解しています。
部品単体での試験は管理が簡単で迅速に実行できますが、システムとしての全部品試験と同じ精度は得られません。部本の相互作用は摩擦や軸外運動によって予期せぬ動作を引き起こします。このような相互作用は、各部品を個別に評価しても再現できません。技術者は以前からそのようなことを疑っていましたが、この10年間でそれが明らかになりました。バーチャルモデルの精度は向上していますが、個々の部品の特性に基づいてレール上のシステム性能を正確に予測することはできませんでした。
最近、完全なボギー台車機構の運動特性とコンプライアンス測定に使用できる画期的な鉄道車両試験システムが実用化されました。MTS Systems が提供するこのシステムでは、特性評価、基本的な耐久性や振動の試験をひとつのシステムで実施できます。
軸バネおよび枕バネ試験
現在、アジアの高速鉄道車両メーカーに設置されているこの新しい台車計測システムは、鉄道車両だけでなく台車の積載に必要なサイズと力を備えています。この試験システムには、これらの複雑なメカニズムを高精度で測定するために設計された多くの機器が組み込まれています。
メカニズムの複雑さは、試験データが様々な形で歪んでしまう点にあります。正確な結果を得るために、試験システムは以下のすべての現象を防ぐ(または補償する)必要があります。ラッシュや減衰による位相のずれ、システムや試料の共振による信号の歪みやノイズ、クロストーク、トランスデューサの温度補償、治具や試料の熱伸縮、キャリブレーションエラー、スリップ、ドリフト、トランスデュサーやマウント、ケーブル、コンディショナーのダメージなどから生じる力の測定誤差の全現象を防ぐ(または補償する)必要があります。多くの場合、目的の結果を算出するために複数の信号が組み合わされ、トータルでの誤差が大きくなります。
このシステムが行う最も重要な試験の中には、ボギーと軸の間にあるすべての構成部品(バネ、コイルスプリング、トーションバー、ラバービスケットなど)を含む、軸バネの試験が含まれます。軸バネはステアリング、ハンドリング、そして乗客の快適性にある程度影響を与えますが、エンジニアは新設計を最適化するために、ホイールセットのマウントとサスペンションシステム全体を詳細に把握する必要があります。軸バネの剛性は、ボギーフレームの剛性と同じ範囲にあり、両者の相互作用がボギー全体のハンドリング応答を決定します。そのため、この新しい試験システムは、個々の構成部品の貢献度や、統合されたシステムとしての完全なアセンブリの特性を測定するために独自設計をされています。
軸バネの剛性試験では、枕バネを固定し、車軸軸受ハウジングとボギーの応答点にリニア可変差動トランス(LVDT)を取り付け、目的の自由度(DOF)ごとにプログラムされた力または変位を加えます。有用な結果を得るためには、エンジニアはロードセルと LVDT の精度と分解能を確保し、ラボの温度を一定に保ち、減衰特性を評価するために異なる速度で測定を行う必要があります。安定性は、垂直方向だけでなく多軸の変位を組み合わせた機能であるため、台車の剛性を垂直方向だけでなく各方向で測定することが重要です。例えばコーナリング時には、ボギーがワープ(ヨー軸方向に変形)しますが、安定したステアリングを行うためにはワープの剛性が重要になります。
この同じセットアップを使って、軸バネの減衰試験を行い、スプリングの剛性との関係で減衰を評価することができます。軸バネの試験データは、モデルの生成と検証のためのボギーのバーチャルモデルへのフィードバックに非常に役立ちます。
また、台車の上部と車両の下部の間にある枕バネの一連の試験も重要です。この試験では軸バネは固定され、枕バネ(通常は一対のエアバッグ)は多軸ロードセルに取り付けられます。シミュレーションされた鉄道車両の治具は、3DOF で拘束され、残りの 3DOF で制御され、枕バネに実際に使用されるのと同じ負荷と変形を与えます。これにより、剛性や減衰特性を評価できます。エアバッグの「ハット」の形状が斜めになっているため、横方向とロール方向の剛性を予測することは特に困難です。エラストマー素材は予測不可能な変形をするため、その動きが乗り心地に大きく影響します。
追加性能試験
また、このシステムでは鉄道車両の下で台車を回転させ剛性を測定する操舵抵抗トルク測定も可能です。この試験では、各車軸に等しく反対の横方向の負荷または変位をかけます。引張/圧縮および縦方向の力はゼロに設定され、垂直方向のアクチュエータは、所望の力またはホイールでの固定された平面的動作を維持するように指令されます。
さらに、試験システムは直線または曲線のトラックのサスペンション係数を試験するように構成できます。この試験ではテーブル、台車、車体に角度測定用ジャイロを搭載した実物(または模擬)の鉄道車両を試料とします。試験には、台車の片側の車輪を任意の重力補正角まで持ち上げることと、テーブルの角度に対する台車と車の角度の測定が含まれます。サスペンション全体において多くの要素があるため、これらの関係を予測することは困難です。メーカーは、同様の試験により、乗り心地や安全性を確保するために不可欠な転倒係数を把握できます。
完成した鉄道車両の評価も可能です。エンジニアが係数試験のために動的応答を把握したい場合には、広帯域のバンド状のノイズや正弦波などの特定の波形のノイズをシステムに指令できます。鉄道車両の車体応答を測定し、試験ソフトを用いて得られたデータから固有振動数を推定できます。
また別の試験で、システムは重心位置や慣性モーメントの測定、路線上の運行データのリアルタイム再生なども可能です。
確かに多目的性能試験システムはラボにとって多額の設備投資ですが、試験スケジュールの迅速化、コストの削減、試験データや試料の特性評価の精度向上を実現することで、同様に大きな投資効果が得られます。最終的にこれらの機能により、鉄道車両や台車のメーカーはモデルの精度を向上させ、イノベーションを迅速に実現し、高品質な車両を製造し、持続的な競争優位性を築くことができます。
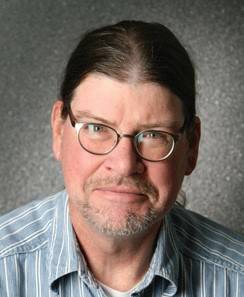