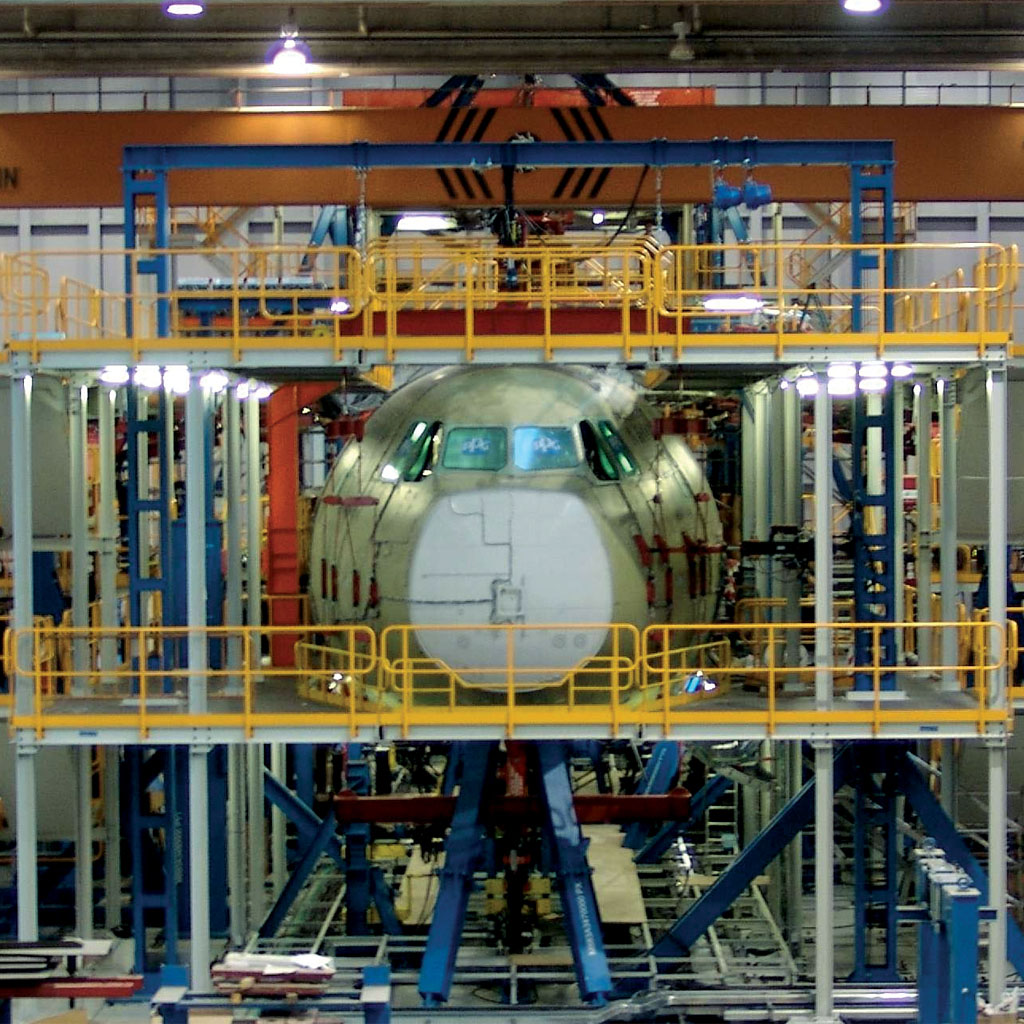
DÉFI DU CLIENT
Basé à Getafe, en Espagne, Airbus Military (anciennement EADS CASA-MTAD) était responsable de la conception, de la production et des essais d’avions militaires célèbres au cours des dernières décennies. Après l’approbation du programme en 2003, Airbus a commencé à travailler sur le prochain projet de grande envergure : le développement de l’avion de transport militaire Airbus A400M de poids intermédiaire.
L’avion à quatre turbopropulseurs est unique par sa taille relativement grande et sa capacité à être ravitaillé en vol. Des commandes de 180 A400M sont déjà programmées pour l’Allemagne, la France, l’Espagne, le Royaume-Uni, la Turquie, la Belgique, le Luxembourg et la Malaisie. Au cours du processus de développement, le premier article d’essai à grande échelle a été assemblé à Getafe, tandis que le banc d’essai était en cours de développement autour et à l’intérieur de l’avion. L’objectif était de mettre en place l’essai complet en six mois après l’arrivée de l’aile à Getafe en provenance de Séville.
« Le calendrier de cet avion ne nous a laissé aucune marge pour des retards », déclare Angel Gago, responsable du laboratoire d’essais structurels d’Airbus Military « Pendant les essais, notre défi est d’atteindre les plus hauts niveaux d’efficacité tout en préservant l’intégrité structurelle de l’article d’essai tout au long du processus. »
Les essais structurels de l’Airbus A400M nécessitent 120 canaux de commande et plus de 9,000 jauges de contrainte, avec la capacité de lire 6,000 jauges à la fois. Des charges massives doivent également être appliquées aux articles d’essai pour simuler les conditions d’exploitation réelles de l’avion. Angel Gago savait qu’avec une configuration impliquant une complexité et des forces aussi élevées, maintenir l’intégrité de l’article d’essai nécessiterait la capacité de charger et de décharger le système d’essai avec une précision absolue.
« Un dysfonctionnement du système pourrait nous faire perdre des mois précieux d’ingénierie si l’article d’essai subissait des dommages », explique-t-il. « De tels échecs sont rares, mais c’était un risque que nous ne pouvions pas prendre. Il était essentiel pour nous de pouvoir retirer immédiatement et uniformément de l’énergie du banc d’essai à tout moment et de manière contrôlée. »
SOLUTIONS MTS
La relation entre Airbus Military et MTS a commencé il y a plus de 20 ans. « Nous avons commencé à travailler avec MTS en 1978, et cinq ans plus tard, MTS nous a aidés à déplacer avec succès nos essais dans une boucle d’asservissement fermée pour la première fois », raconte Angel Gago. « Nous utilisons maintenant le logiciel AeroPro™ pour tous nos essais d’avions et, grâce aux capacités de commande etd’acquisition de données intégrées, il est facile pour nous de gérer l’ensemble de nos activités d’essai en temps réel.
Nous avons été ravis de découvrir que MTS offre non seulement une technologie de pointe dans ce domaine, mais que la technologie peut être gérée à partir de la même interface logicielle AeroPro que nous utilisions déjà », ajoute-t-il. « La capacité de MTS à fournir la solution d’essai complète, y compris tous les vérins, commandes et logiciels, nous a permis d’avancer plus rapidement. »
MTS a aidé Airbus Military à ajouter des systèmes ALA (Active Load Abort) à chacun de ses bancs d’essai destinés à être utilisés pour l’avion Airbus A400M. La technologie ALA aide à protéger les articles d’essai en offrant un contrôle précis du déchargement du système d’essai structurel en cas de panne de courant ou de verrouillage du système.
Lors d’un tel événement, le système ALA utilise des mesures, tant au niveau logiciel que matériel, pour réduire toutes les charges du vérin à un état neutre exactement en même temps, quelles que soient les pressions et les positions individuelles variables des vérins. Un système de commande séparé fonctionne parallèlement au système de commande de charge, prenant en compte l’état de l’ensemble de l’essai lors du retrait de la pression hydraulique sur l’article d’essai. Le système détecte une défaillance du côté de la commande, puis s’efforce de retirer instantanément et uniformément la charge de l’ensemble de l’article d’essai.
« MTS a travaillé en étroite collaboration avec nous à chaque étape du processus jusqu’à ce que notre système ALA soit pleinement intégré et opérationnel », indique Angel Gago. « Maintenant, ce système fonctionne de manière homogène dans l’ensemble de notre laboratoire d’essai, que nous gérons parallèlement à notre servocommande et à l’acquisition de données dans l’environnement AeroPro. »
AVANTAGES CLIENTS
Angel Gago affirme que le principal avantage de la technologie MTS ALA réside dans le fait qu’elle a permis à Airbus Military d’apporter une nouvelle façon de penser sur la manière de protéger les articles d’essai utilisés lors des essais structurels contre tout dysfonctionnement ou comportements inattendus du système.
« Nous sommes maintenant confiants de savoir que nos articles d’essai sont bien protégés contre les dommages pendant les essais », dit-il. « Nos ingénieurs d’essai peuvent se concentrer sur l’essai en lui-même, sans avoir à se soucier de la façon dont une défaillance inattendue sur le banc d’essai pourrait anéantir leur dur labeur. »
Selon Jesus Posada, responsable des essais structurels chez Airbus Military, MTS interviendra également lorsque le laboratoire d’essai entrera dans la prochaine phase des essais de fatigue. « Nous prévoyons bientôt d’améliorer la vitesse de nos essais de fatigue et de nous appuyer sur l’expertise de MTS en la matière pour nous aider à améliorer ce type d’essais », déclare Jesus Posada. « Nous avons beaucoup entendu parler des outils logiciels AeroPro pour accélérer les essais dynamiques et nous sommes impatients d’en tirer pleinement parti dans un avenir proche. »
C