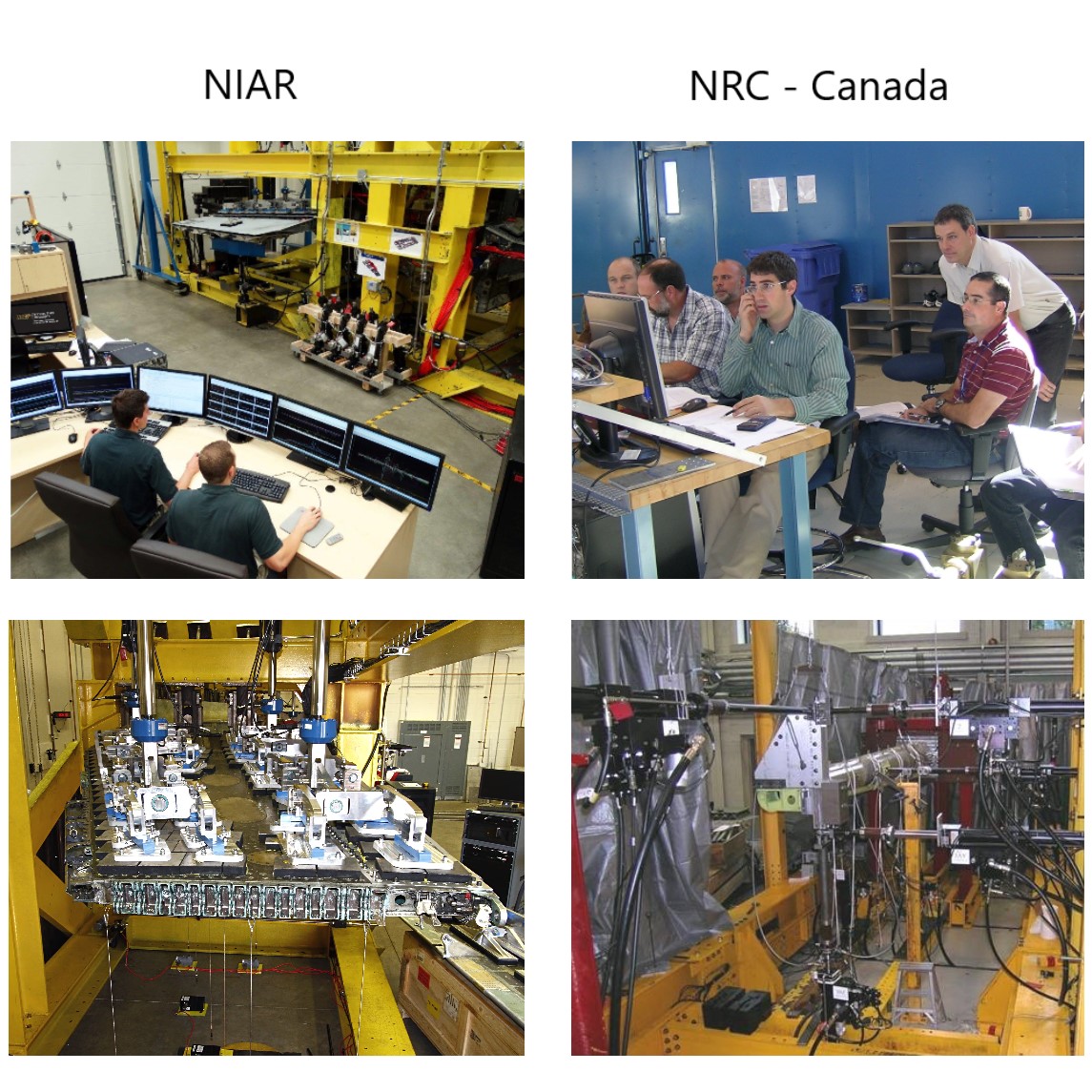
Les bancs d’essai structurels à grande échelle dotés de schémas d’actionnement hautement couplés présentent des défis uniques pour les ingénieurs en essais aérospatiaux. Dans ces configurations complexes, plusieurs actionneurs exercent simultanément des forces différentes sur la même partie d’un article d’essai, augmentant le potentiel d’erreurs qui peuvent compromettre les programmes d’essais et retarder les programmes de développement.
Un outil permet de réduire ces erreurs, tout en améliorant la vitesse et l’efficacité des essais : C3 Performance, un utilitaire du logiciel de contrôle et d’acquisition de données MTS AeroPro™. Également connu sous le nom de C-cubed, C3Performance permet aux équipes d’essais de gérer efficacement des schémas d’actionnement hautement couplés, sans avoir à prévoir du temps supplémentaire pour les programmes d’essais afin de résoudre de nombreux cas d’arrêts et de verrouillages récurrents.La technique de compensation de couplage croisé de
C 3 Performance a été élaborée conjointement par des experts du Conseil national de recherches du Canada (CNRC) et de MTS Systems Corporation. Aujourd’hui, il s’agit d’un composant fondamental du protocole d’essai au CNRC, le laboratoire d’essais structurels à grande échelle du Canada, où Andre Beltempo travaille comme ingénieur en essais structurels.
« En règle générale, nous utilisons C-cubed sur tous les essais », déclare M. Beltempo. « Les essais de fatigue à grande échelle impliquent une interaction très complexe entre les vérins. C’est exactement pourquoi nous en avons besoin. »
L’équipe de M. Beltempo a récemment utilisé C3 Performance lors d’une démonstration technologique pour un grand constructeur d’hélicoptères. Le programme d’essais de fatigue et statiques était axé sur une poutre de queue composite, produite à l’aide de techniques de fabrication de pointe. Les essais étaient identiques à ceux qui seraient utilisés pour certifier la pièce selon les exigences de durée de vie en sûreté de la FAA.
« Si vous regardez le raccord d’interface de la boîte de vitesses du rotor de queue, les deux vérins arrière se chargent tous les deux sur le même raccord », déclare M. Beltempo. « La compensation de couplage permet de minimiser les conflits [entre vérins]. »
L’essai impliquait six vérins et quatre millions de points finaux, fonctionnant pendant la nuit pendant environ 125 jours, avec une fréquence moyenne de 0,5 Hz. Cet essai de vitesse aurait été impossible sans C3 Performance, selon M. Beltempo.
« Nous n’aurions pas pu le faire aussi rapidement sans compensation de couplage croisé », affirme-t-il. « Pour un essai de nuit, nous aurions dû exécuter les niveaux finaux à la moitié de la vitesse pour ne pas avoir à nous soucier des arrêts sans surveillance. Notre approche standard pour tout essai de fatigue consiste à régler l’essai, à appliquer C-cubed et à le régler à nouveau immédiatement. Je n’ai jamais vu de hausse de vitesse inférieure à un facteur de deux pour un article rigide. »
Un autre aspect que M. Beltempo apprécie à propos de C3 Performance est sa facilité d’utilisation globale. Parce que les opérateurs d’essais peuvent le configurer eux-mêmes, C3 Performance permet aux laboratoires de gagner encore plus de temps.
« Le fait qu’il soit si ergonomique me donne la possibilité de me concentrer sur des tâches plus importantes », raconte M. Beltempo. « Si vous deviez vous asseoir et déterminer tous les coefficients par vous-même, ce serait différent. Mais il vous suffit de cliquer sur un bouton pour tout lancer. C’est une réelle amélioration de la productivité. »
L’organisation qui a contribué au développement de C3 Performance l’applique naturellement à chaque essai de fatigue dans le cadre de son protocole. Mais d’autres laboratoires découvrent également le potentiel de résolution de problèmes de ce puissant utilitaire.
Pour le Dr Waruna Seneviratne, directeur technique du laboratoire Composites and Advanced Materials de l’Institut national de recherche en aviation (NIAR) de l’Université d’État de Wichita, le problème était le manque de sommeil.
« Nous effectuions un essai de fatigue avec une combinaison très distinctive de fixation et de vérins personnalisés. Or, notre calendrier était très exigeant », confie M. Seneviratne. « Le test s’est déroulé en une journée et nous avons rencontré un grand nombre de déclencheurs de limites d’erreurs intempestives. Notre équipe a dû se rendre au laboratoire en pleine nuit pour voir ce qui causait les arrêts et redémarrer l’essai. Nous étions en retard. »
L’essai s’est concentré sur l’évaluation de la résistance à la fatigue des structures composites du F/A-18 Hornet, dont beaucoup approchent de la retraite. Étant donné que le remplacement de l’avion n’était pas prêt avant 2019, l’US Navy a du prolonger en toute sécurité la durée de vie des structures composites vieillissantes de l’avion.
Les recherches de M. Seneviratne ont réussi à déterminer que les joints collés composite-titane à l’emplanture de l’aile avaient une grande durée de vie. Le nouvel essai a élargi l’étude pour inclure l’ensemble de l’aile intérieure, qui a un revêtement composite. L’article d’essai comprend l’aile intérieure, le volet de bord de fuite et le canon central ainsi qu’un volet de bord d’attaque et une aile externe simulés. L’ équipe de recherche du NIAR a dû construire une plate-forme en acier haute résistance élaborée avec des fixations conçues sur mesure et appliquer des charges importantes pour reproduire des manœuvres agressives.
« Il y avait des différences significatives entre la course et les charges entre les vérins, ce qui constituait probablement une source d’erreurs », a-t-il déclaré. « Nous devions trouver un moyen de minimiser les faux arrêts, alors nous avons commencé à y réfléchir. »
L’ingénieur de recherche Travis Cravens, membre de l’équipe de M. Seneviratne, s’est occupé de l’installation et de la configuration de C3 Performance. Les ingénieurs en systèmes et applications MTS ont terminé l’installation et la formation en moins d’une journée, et le laboratoire a constaté les résultats presque immédiatement.
« Nous fonctionnions 20 % plus vite à la fin du premier jour sans aucune modification mécanique du banc d’essai », a déclaré Cravens. « C3 Performance a été très facile à apprendre et à mettre en place ; tout se passe dans le logiciel. Vous créez simplement une matrice de couplage croisé en appliquant une charge unitaire sur chaque canal de charge, ce qui ne représente qu’une étape supplémentaire pour chaque vérin.
Pour rationaliser la configuration des essais, C3 Performance élimine la tâche fastidieuse de saisie manuelle des données de couplage croisé en utilisant des cas de charge unitaires pour générer des coefficients de compensation de couplage croisé automatisés. M. Seneviratne a caractérisé ce processus à l’aide d’une analogie appropriée.
« C’est comme avoir une équipe de 20 personnes qui ne se connaissent et qui travaillent sur le même projet », a-t-il déclaré. « Les charges unitaires sont simplement un moyen de présenter toutes ces personnes les unes aux autres afin qu’elles puissent collaborer et travailler plus efficacement. »
Avec quelques réglages supplémentaires, Seneviratne et Cravens ont pu augmenter le taux d’esai de 24 % et réduire considérablement le nombre d’arrêts.
« Cela a considérablement amélioré les performances de notre essai », affirme Cravens. « Avec le suivi de charge amélioré, les petites perturbations de la rétroaction sont beaucoup moins susceptibles de déclencher des limites d’erreur, ce qui réduit le nombre d’arrêts. La réduction des erreurs nous a également permis d’exécuter davantage de segments par heure. »
Avant d’utiliser C3 Performance, le NIAR n’était capable d’atteindre qu’un maximum de 375 segments par heure, avec une moyenne de 97 arrêts et 55 verrouillages par bloc d’essai. Avec C3 Performance, cela est passé à 480 segments par heure avec une moyenne de 51 arrêts et 15 verrouillages.
« Le nombre d’arrêts était un tiers de ce qu’ils étaient, ce qui constituait un énorme gain pour nous », a déclaré M. Seneviratne. « Cela nous a permis de lancer des essais pendant la nuit, certains sans la moindre interruption. Cela pouvait représenter un gain de 10 heures d’essais supplémentaires, ce qui nous a énormément aidé du point de vue de notre calendrier. »
C3 Performance a permis de gagner des semaines, grâce auxquelles l’équipe de M. Seneviratne a pu produire les résultats à temps. De plus, la productivité du laboratoire a été améliorée : l’équipe a pu opérer selon un calendrier plus prévisible et avait plus de temps à consacrer à d’autres projets. Dans n’importe quel laboratoire aux ressources limitées, c’est un avantage important.
« Le fait de savoir que nous pouvions effectuer l’essai pendant la nuit et être sûrs de pouvoir effectuer des inspections et des réparations en journée nous a permis d’augmenter l’efficacité de nos procédures », a déclaré Seneviratne. « Nous avons pu mieux planifier et coordonner nos activités en sachant que l’essai se déroulait pendant la nuit, sans surveillance, avec un minimum d’interruptions. »
Un outil permet de réduire ces erreurs, tout en améliorant la vitesse et l’efficacité des essais : C3 Performance, un utilitaire du logiciel de contrôle et d’acquisition de données MTS AeroPro™. Également connu sous le nom de C-cubed, C3Performance permet aux équipes d’essais de gérer efficacement des schémas d’actionnement hautement couplés, sans avoir à prévoir du temps supplémentaire pour les programmes d’essais afin de résoudre de nombreux cas d’arrêts et de verrouillages récurrents.La technique de compensation de couplage croisé de
C 3 Performance a été élaborée conjointement par des experts du Conseil national de recherches du Canada (CNRC) et de MTS Systems Corporation. Aujourd’hui, il s’agit d’un composant fondamental du protocole d’essai au CNRC, le laboratoire d’essais structurels à grande échelle du Canada, où Andre Beltempo travaille comme ingénieur en essais structurels.
« En règle générale, nous utilisons C-cubed sur tous les essais », déclare M. Beltempo. « Les essais de fatigue à grande échelle impliquent une interaction très complexe entre les vérins. C’est exactement pourquoi nous en avons besoin. »
L’équipe de M. Beltempo a récemment utilisé C3 Performance lors d’une démonstration technologique pour un grand constructeur d’hélicoptères. Le programme d’essais de fatigue et statiques était axé sur une poutre de queue composite, produite à l’aide de techniques de fabrication de pointe. Les essais étaient identiques à ceux qui seraient utilisés pour certifier la pièce selon les exigences de durée de vie en sûreté de la FAA.
« Si vous regardez le raccord d’interface de la boîte de vitesses du rotor de queue, les deux vérins arrière se chargent tous les deux sur le même raccord », déclare M. Beltempo. « La compensation de couplage permet de minimiser les conflits [entre vérins]. »
L’essai impliquait six vérins et quatre millions de points finaux, fonctionnant pendant la nuit pendant environ 125 jours, avec une fréquence moyenne de 0,5 Hz. Cet essai de vitesse aurait été impossible sans C3 Performance, selon M. Beltempo.
« Nous n’aurions pas pu le faire aussi rapidement sans compensation de couplage croisé », affirme-t-il. « Pour un essai de nuit, nous aurions dû exécuter les niveaux finaux à la moitié de la vitesse pour ne pas avoir à nous soucier des arrêts sans surveillance. Notre approche standard pour tout essai de fatigue consiste à régler l’essai, à appliquer C-cubed et à le régler à nouveau immédiatement. Je n’ai jamais vu de hausse de vitesse inférieure à un facteur de deux pour un article rigide. »
Un autre aspect que M. Beltempo apprécie à propos de C3 Performance est sa facilité d’utilisation globale. Parce que les opérateurs d’essais peuvent le configurer eux-mêmes, C3 Performance permet aux laboratoires de gagner encore plus de temps.
« Le fait qu’il soit si ergonomique me donne la possibilité de me concentrer sur des tâches plus importantes », raconte M. Beltempo. « Si vous deviez vous asseoir et déterminer tous les coefficients par vous-même, ce serait différent. Mais il vous suffit de cliquer sur un bouton pour tout lancer. C’est une réelle amélioration de la productivité. »
L’organisation qui a contribué au développement de C3 Performance l’applique naturellement à chaque essai de fatigue dans le cadre de son protocole. Mais d’autres laboratoires découvrent également le potentiel de résolution de problèmes de ce puissant utilitaire.
Pour le Dr Waruna Seneviratne, directeur technique du laboratoire Composites and Advanced Materials de l’Institut national de recherche en aviation (NIAR) de l’Université d’État de Wichita, le problème était le manque de sommeil.
« Nous effectuions un essai de fatigue avec une combinaison très distinctive de fixation et de vérins personnalisés. Or, notre calendrier était très exigeant », confie M. Seneviratne. « Le test s’est déroulé en une journée et nous avons rencontré un grand nombre de déclencheurs de limites d’erreurs intempestives. Notre équipe a dû se rendre au laboratoire en pleine nuit pour voir ce qui causait les arrêts et redémarrer l’essai. Nous étions en retard. »
L’essai s’est concentré sur l’évaluation de la résistance à la fatigue des structures composites du F/A-18 Hornet, dont beaucoup approchent de la retraite. Étant donné que le remplacement de l’avion n’était pas prêt avant 2019, l’US Navy a du prolonger en toute sécurité la durée de vie des structures composites vieillissantes de l’avion.
Les recherches de M. Seneviratne ont réussi à déterminer que les joints collés composite-titane à l’emplanture de l’aile avaient une grande durée de vie. Le nouvel essai a élargi l’étude pour inclure l’ensemble de l’aile intérieure, qui a un revêtement composite. L’article d’essai comprend l’aile intérieure, le volet de bord de fuite et le canon central ainsi qu’un volet de bord d’attaque et une aile externe simulés. L’ équipe de recherche du NIAR a dû construire une plate-forme en acier haute résistance élaborée avec des fixations conçues sur mesure et appliquer des charges importantes pour reproduire des manœuvres agressives.
« Il y avait des différences significatives entre la course et les charges entre les vérins, ce qui constituait probablement une source d’erreurs », a-t-il déclaré. « Nous devions trouver un moyen de minimiser les faux arrêts, alors nous avons commencé à y réfléchir. »
L’ingénieur de recherche Travis Cravens, membre de l’équipe de M. Seneviratne, s’est occupé de l’installation et de la configuration de C3 Performance. Les ingénieurs en systèmes et applications MTS ont terminé l’installation et la formation en moins d’une journée, et le laboratoire a constaté les résultats presque immédiatement.
« Nous fonctionnions 20 % plus vite à la fin du premier jour sans aucune modification mécanique du banc d’essai », a déclaré Cravens. « C3 Performance a été très facile à apprendre et à mettre en place ; tout se passe dans le logiciel. Vous créez simplement une matrice de couplage croisé en appliquant une charge unitaire sur chaque canal de charge, ce qui ne représente qu’une étape supplémentaire pour chaque vérin.
Pour rationaliser la configuration des essais, C3 Performance élimine la tâche fastidieuse de saisie manuelle des données de couplage croisé en utilisant des cas de charge unitaires pour générer des coefficients de compensation de couplage croisé automatisés. M. Seneviratne a caractérisé ce processus à l’aide d’une analogie appropriée.
« C’est comme avoir une équipe de 20 personnes qui ne se connaissent et qui travaillent sur le même projet », a-t-il déclaré. « Les charges unitaires sont simplement un moyen de présenter toutes ces personnes les unes aux autres afin qu’elles puissent collaborer et travailler plus efficacement. »
Avec quelques réglages supplémentaires, Seneviratne et Cravens ont pu augmenter le taux d’esai de 24 % et réduire considérablement le nombre d’arrêts.
« Cela a considérablement amélioré les performances de notre essai », affirme Cravens. « Avec le suivi de charge amélioré, les petites perturbations de la rétroaction sont beaucoup moins susceptibles de déclencher des limites d’erreur, ce qui réduit le nombre d’arrêts. La réduction des erreurs nous a également permis d’exécuter davantage de segments par heure. »
Avant d’utiliser C3 Performance, le NIAR n’était capable d’atteindre qu’un maximum de 375 segments par heure, avec une moyenne de 97 arrêts et 55 verrouillages par bloc d’essai. Avec C3 Performance, cela est passé à 480 segments par heure avec une moyenne de 51 arrêts et 15 verrouillages.
« Le nombre d’arrêts était un tiers de ce qu’ils étaient, ce qui constituait un énorme gain pour nous », a déclaré M. Seneviratne. « Cela nous a permis de lancer des essais pendant la nuit, certains sans la moindre interruption. Cela pouvait représenter un gain de 10 heures d’essais supplémentaires, ce qui nous a énormément aidé du point de vue de notre calendrier. »
C3 Performance a permis de gagner des semaines, grâce auxquelles l’équipe de M. Seneviratne a pu produire les résultats à temps. De plus, la productivité du laboratoire a été améliorée : l’équipe a pu opérer selon un calendrier plus prévisible et avait plus de temps à consacrer à d’autres projets. Dans n’importe quel laboratoire aux ressources limitées, c’est un avantage important.
« Le fait de savoir que nous pouvions effectuer l’essai pendant la nuit et être sûrs de pouvoir effectuer des inspections et des réparations en journée nous a permis d’augmenter l’efficacité de nos procédures », a déclaré Seneviratne. « Nous avons pu mieux planifier et coordonner nos activités en sachant que l’essai se déroulait pendant la nuit, sans surveillance, avec un minimum d’interruptions. »