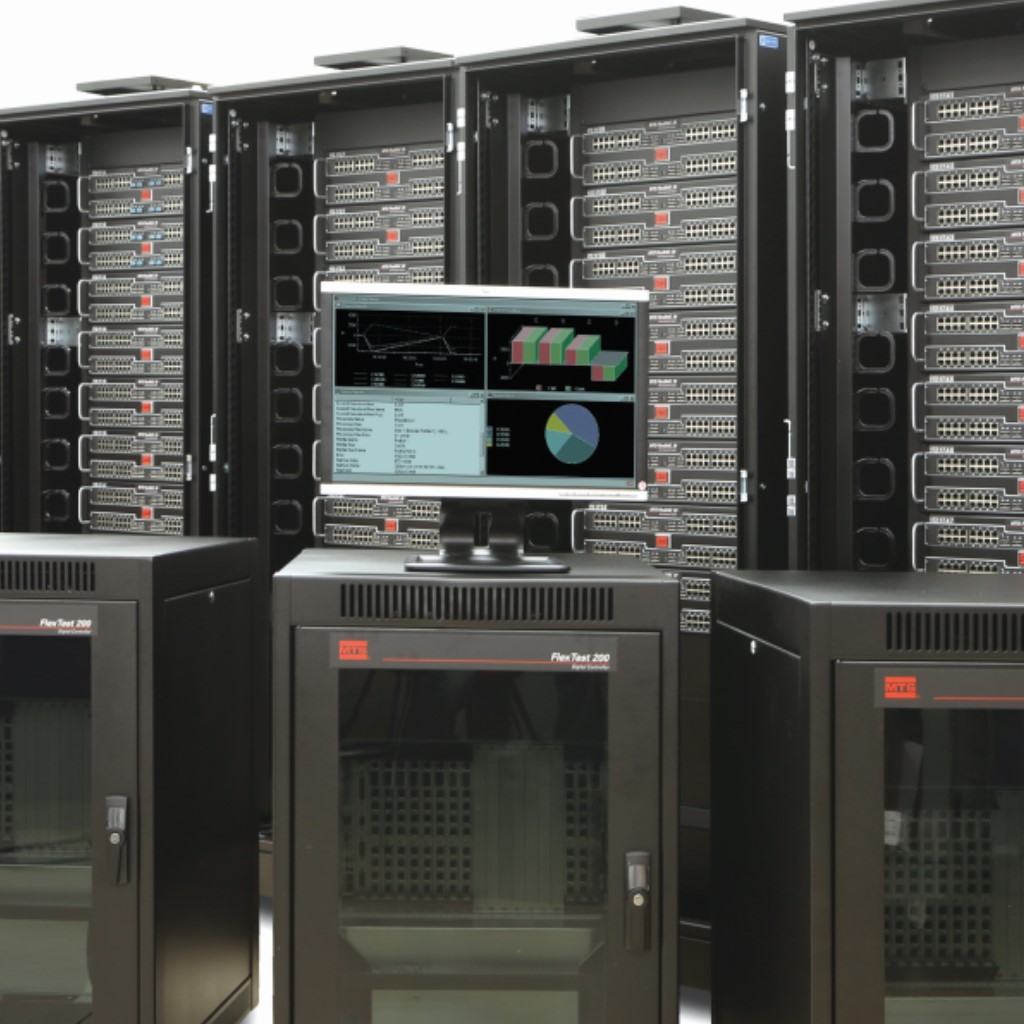
Q : Comment l’acquisition de données a-t-elle évolué au cours de la dernière décennie ?
R : Nous avons constaté une progression continue du nombre de canaux alors que les équipes d’essais structurels essaient d’obtenir autant de jauges que possible sur l’échantillon pour mieux comprendre les chemins de charge et les corréler avec les modèles. Il y a eu une accélération considérable dans ce domaine au cours des dernières années. Aujourd’hui, les équipes d’essai placent jusqu’à 10,000 jauges sur un avion plein cadre, et ce nombre ne fera qu’augmenter. Dans le même temps, la pression exercée pour mettre de nouveaux avions sur le marché plus rapidement impose d’accélérer les programmes d’essais. Mais il faut plus de temps pour configurer plus de jauges, il est donc important que les équipes d’essai comprennent la valeur que ces jauges supplémentaires apportent, et le processus doit être terminé aussi efficacement que possible.
Q : De quelles manières les laboratoires d’essai peuvent-ils optimiser l’efficacité des essais ?
R : Quelques idées me viennent à l’esprit. Vous avez besoin d’un logiciel d’essai conçu pour accélérer le processus de configuration. Et vous avez besoin d’une flexibilité maximale en ce qui concerne la façon dont les canaux d’acquisition de données sont répartis entre les essais. Avec certains systèmes, dès que vous dédiez un canal du boîtier DAC à un essai précis, vous sacrifiez tout le boîtier. Pour les laboratoires exécutant plusieurs essais avec moins de canaux pour chacun d’entre eux, ce n’est pas idéal. Si vous pouvez diviser les canaux, vous n’avez pas à gérer de boîtier séparé pour chaque essai, ce qui est très efficace. C’est pourquoi les systèmes MTS FlexDAC 20 sont conçus pour distribuer les canaux, quelle que soit la proportion, sur huit stations d’essai maximum en même temps. MTS propose le seul système DAC capable de faire cela.
Q : Les laboratoires doivent-ils remplacer les systèmes DAC existants pour bénéficier de cette flexibilité ?
R : Non, ce ne serait pas très rentable. Les systèmes MTS FlexDAC 20 peuvent fonctionner avec les unités DAC d’autres fournisseurs sur le même essai et le laboratoire peut tous les gérer avec le logiciel MTS AeroPro. Cette intégration vous permet d’ajouter un nombre de canaux avec les systèmes MTS DAC tout en protégeant l’investissement du laboratoire dans les systèmes actuels. Pour encore plus de flexibilité, les laboratoires peuvent mélanger et assortir les deux types de châssis FlexDAC, l’A32 et le B24, dans n’importe quelle combinaison, en fonction des besoins du laboratoire. Au sein d’AeroPro, il est très facile de distinguer les différentes plateformes. Les données des systèmes DAC non MTS sont combinées, tandis que les données acquises via FlexDAC offrent une synchronisation d’horloge unique dans l’industrie et basée sur le matériel avec les contrôleurs FlexTest.
Q : Pourquoi la synchronisation d’horloge basée sur le matériel est-elle importante ?
R : Il est essentiel de savoir quel niveau de charge produit une valeur de déformation donnée. S’il y a un décalage entre le contrôleur et le système d’acquisition de données, cela soulève des questions troublantes sur la charge réellement appliquée pour produire la contrainte. Nous évitons cela avec une synchronisation du matériel, entre les systèmes FlexDAC 20 et les contrôleurs FlexTest via le logiciel AeroPro. Plus précisément, les unités FlexDAC 20 utilisent la même horloge interne que les contrôleurs FlexTest, de sorte que vous obtenez une analyse des données exactement au même rythme d’horloge. Il génère des flux de commande et d’acquisition de données véritablement synchronisés. Sans cela, vous devez transférer les données par la suite à partir de deux applications logicielles distinctes et les assembler, mais ce n’est pas parfait. Notre approche ne présente aucun décalage entre la force et l’acquisition de données.
Q : Y a-t-il d’autres avantages à utiliser le DAC avec des contrôleurs et des logiciels intégrés ?
R : Le véritable avantage est que vous pouvez tout gérer avec une seule application logicielle, contrairement à l’utilisation d’outils séparés pour exécuter le contrôleur et l’acquisition de données, ce qui, encore une fois, implique un certain niveau d’intégration de données back-end. C’est pourquoi les systèmes FlexDAC 20 sont conçus dès le premier jour pour être entièrement compatibles avec AeroPro. Sur une base pratique, cela signifie que les ingénieurs d’essai peuvent afficher des tracés, des graphiques et des valeurs, et consulter les valeurs limites pour tous les canaux d’acquisition de données avec une seule application, quel que soit le fabricant du DAC. Vous pouvez effectuer un étalonnage shunt, une validation shunt et de nombreuses autres opérations sur des centaines de milliers de canaux simultanément. Les assistants de configuration accélèrent tout, de sorte que les opérateurs passent moins de temps sur la configuration et plus de temps sur l’essai. Vous pouvez même préparer les affectations de capteurs et de matériel hors ligne et les importer dans AeroPro. Et vous n’avez qu’une seule interface utilisateur, ce qui permet de faire face à la complexité croissante des essais.
Q : Existe-t-il d’autres moyens pour les laboratoires d’améliorer leur efficacité ?
R : L’étalonnage automatique peut y aider en grande partie. MTS a créé une méthode d’étalonnage automatisée qui prend environ dix minutes pour vérifier et documenter que chaque châssis FlexDAC 20 fonctionne selon nos spécifications. Cela implique plus de 1 200 mesures et calculs électriques distincts. Vous pouvez même procéder à l’étalonnage sans perturber la configuration de l’essai. Il n’est pas nécessaire de retirer les câbles des boîtiers, ce qui permet de gagner du temps et de réduire les risques d’erreurs. Bien entendu, les données des jauges de contrainte sont fournies aux organismes de réglementation, il est donc essentiel de pouvoir vérifier les performances des conditionneurs du système DAC.
R : Nous avons constaté une progression continue du nombre de canaux alors que les équipes d’essais structurels essaient d’obtenir autant de jauges que possible sur l’échantillon pour mieux comprendre les chemins de charge et les corréler avec les modèles. Il y a eu une accélération considérable dans ce domaine au cours des dernières années. Aujourd’hui, les équipes d’essai placent jusqu’à 10,000 jauges sur un avion plein cadre, et ce nombre ne fera qu’augmenter. Dans le même temps, la pression exercée pour mettre de nouveaux avions sur le marché plus rapidement impose d’accélérer les programmes d’essais. Mais il faut plus de temps pour configurer plus de jauges, il est donc important que les équipes d’essai comprennent la valeur que ces jauges supplémentaires apportent, et le processus doit être terminé aussi efficacement que possible.
Q : De quelles manières les laboratoires d’essai peuvent-ils optimiser l’efficacité des essais ?
R : Quelques idées me viennent à l’esprit. Vous avez besoin d’un logiciel d’essai conçu pour accélérer le processus de configuration. Et vous avez besoin d’une flexibilité maximale en ce qui concerne la façon dont les canaux d’acquisition de données sont répartis entre les essais. Avec certains systèmes, dès que vous dédiez un canal du boîtier DAC à un essai précis, vous sacrifiez tout le boîtier. Pour les laboratoires exécutant plusieurs essais avec moins de canaux pour chacun d’entre eux, ce n’est pas idéal. Si vous pouvez diviser les canaux, vous n’avez pas à gérer de boîtier séparé pour chaque essai, ce qui est très efficace. C’est pourquoi les systèmes MTS FlexDAC 20 sont conçus pour distribuer les canaux, quelle que soit la proportion, sur huit stations d’essai maximum en même temps. MTS propose le seul système DAC capable de faire cela.
Q : Les laboratoires doivent-ils remplacer les systèmes DAC existants pour bénéficier de cette flexibilité ?
R : Non, ce ne serait pas très rentable. Les systèmes MTS FlexDAC 20 peuvent fonctionner avec les unités DAC d’autres fournisseurs sur le même essai et le laboratoire peut tous les gérer avec le logiciel MTS AeroPro. Cette intégration vous permet d’ajouter un nombre de canaux avec les systèmes MTS DAC tout en protégeant l’investissement du laboratoire dans les systèmes actuels. Pour encore plus de flexibilité, les laboratoires peuvent mélanger et assortir les deux types de châssis FlexDAC, l’A32 et le B24, dans n’importe quelle combinaison, en fonction des besoins du laboratoire. Au sein d’AeroPro, il est très facile de distinguer les différentes plateformes. Les données des systèmes DAC non MTS sont combinées, tandis que les données acquises via FlexDAC offrent une synchronisation d’horloge unique dans l’industrie et basée sur le matériel avec les contrôleurs FlexTest.
Q : Pourquoi la synchronisation d’horloge basée sur le matériel est-elle importante ?
R : Il est essentiel de savoir quel niveau de charge produit une valeur de déformation donnée. S’il y a un décalage entre le contrôleur et le système d’acquisition de données, cela soulève des questions troublantes sur la charge réellement appliquée pour produire la contrainte. Nous évitons cela avec une synchronisation du matériel, entre les systèmes FlexDAC 20 et les contrôleurs FlexTest via le logiciel AeroPro. Plus précisément, les unités FlexDAC 20 utilisent la même horloge interne que les contrôleurs FlexTest, de sorte que vous obtenez une analyse des données exactement au même rythme d’horloge. Il génère des flux de commande et d’acquisition de données véritablement synchronisés. Sans cela, vous devez transférer les données par la suite à partir de deux applications logicielles distinctes et les assembler, mais ce n’est pas parfait. Notre approche ne présente aucun décalage entre la force et l’acquisition de données.
Q : Y a-t-il d’autres avantages à utiliser le DAC avec des contrôleurs et des logiciels intégrés ?
R : Le véritable avantage est que vous pouvez tout gérer avec une seule application logicielle, contrairement à l’utilisation d’outils séparés pour exécuter le contrôleur et l’acquisition de données, ce qui, encore une fois, implique un certain niveau d’intégration de données back-end. C’est pourquoi les systèmes FlexDAC 20 sont conçus dès le premier jour pour être entièrement compatibles avec AeroPro. Sur une base pratique, cela signifie que les ingénieurs d’essai peuvent afficher des tracés, des graphiques et des valeurs, et consulter les valeurs limites pour tous les canaux d’acquisition de données avec une seule application, quel que soit le fabricant du DAC. Vous pouvez effectuer un étalonnage shunt, une validation shunt et de nombreuses autres opérations sur des centaines de milliers de canaux simultanément. Les assistants de configuration accélèrent tout, de sorte que les opérateurs passent moins de temps sur la configuration et plus de temps sur l’essai. Vous pouvez même préparer les affectations de capteurs et de matériel hors ligne et les importer dans AeroPro. Et vous n’avez qu’une seule interface utilisateur, ce qui permet de faire face à la complexité croissante des essais.
Q : Existe-t-il d’autres moyens pour les laboratoires d’améliorer leur efficacité ?
R : L’étalonnage automatique peut y aider en grande partie. MTS a créé une méthode d’étalonnage automatisée qui prend environ dix minutes pour vérifier et documenter que chaque châssis FlexDAC 20 fonctionne selon nos spécifications. Cela implique plus de 1 200 mesures et calculs électriques distincts. Vous pouvez même procéder à l’étalonnage sans perturber la configuration de l’essai. Il n’est pas nécessaire de retirer les câbles des boîtiers, ce qui permet de gagner du temps et de réduire les risques d’erreurs. Bien entendu, les données des jauges de contrainte sont fournies aux organismes de réglementation, il est donc essentiel de pouvoir vérifier les performances des conditionneurs du système DAC.