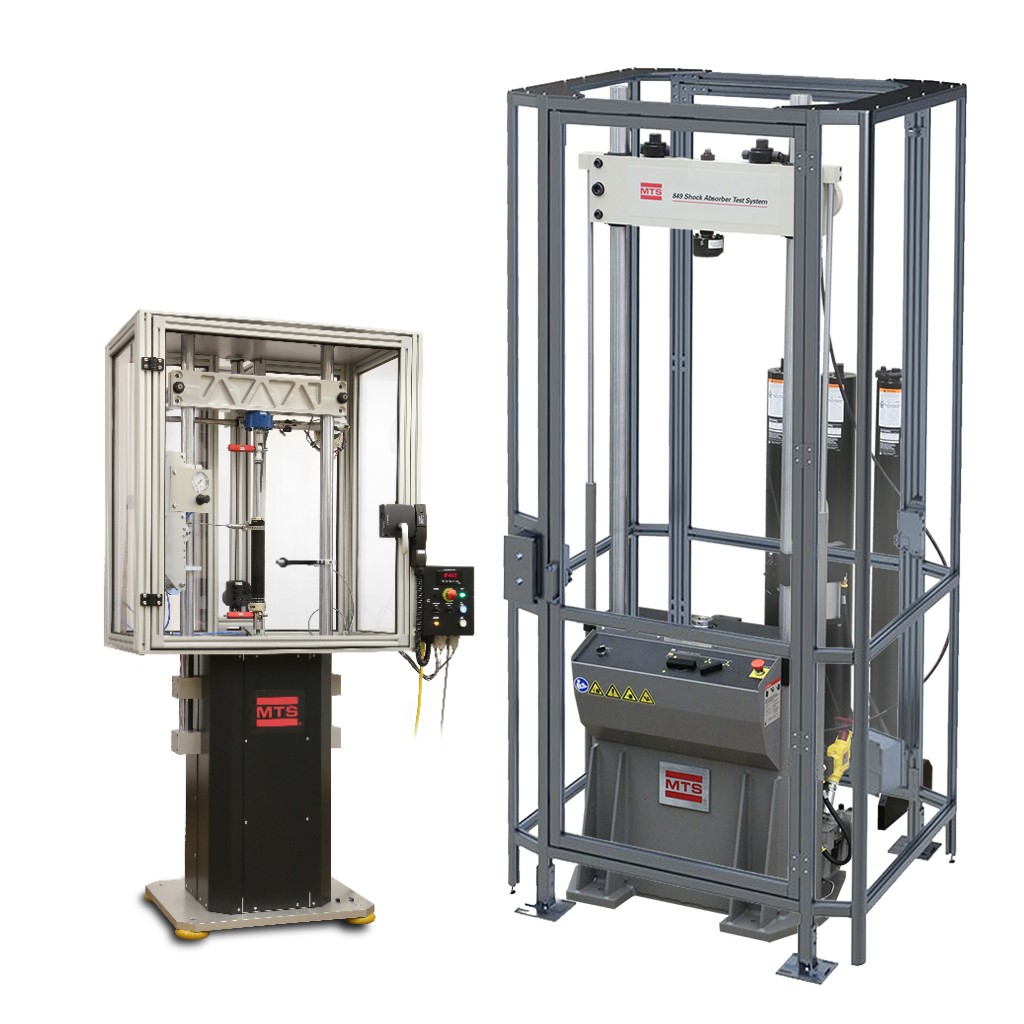
Q : Quels sont les grands principes à suivre pour choisir parmi les systèmes d’essais électriques et hydrauliques ?
S. Bieganek : le choix de la technologie à déployer dépend beaucoup de la situation et de nombreux facteurs, tels que les exigences fonctionnelles et de performance du système, le budget disponible, l’infrastructure existante,… C’est complexe. Il vaut mieux commencer par considérer le type d’environnement de l’essai (site/usine de production, laboratoire de recherche et de développement, terrain d’essai/piste de course) et partir de là. Les gammes de solutions d’essais d’amortisseurs et de simulation de route couplée à des pneus de MTS proposent un mélange complémentaire de systèmes électriques et hydrauliques. C’est notre travail que de faire profiter nos clients de notre expérience et de notre expertise pour les aider à trouver un système qui répond à leurs besoins actuels et futurs.
Q : Commençons par les essais d’amortisseurs dans un environnement de production. Quelles sont les principales applications ?
S. Bieganek : en général, les clients doivent effectuer des essais de caractérisation en ligne pour s’assurer que l’amortisseur a été assemblé correctement et qu’il fonctionne comme prévu. En d’autres termes, cela revient à faire un contrôle de la qualité. Ils vérifient généralement la force d’amortissement, la pression du gaz et les niveaux d’huile. L’essai peut être entièrement intégré à la ligne de production pour tester chaque amortisseur. Ou alors, il peut s’agir d’un audit de qualité, lors duquel le client prélève quelques échantillons toutes les heures et les teste hors ligne.
Q : Quelles sont les caractéristiques de performances qu’un système d’essais d’amortisseurs doit avoir dans un environnement de production ?
R. Simpson : la vitesse est essentielle. Le système d’essais ne doit pas retarder la ligne de production ou entraîner des blocages. Il se peut qu’il doive être intégré à la ligne pour améliorer la productivité ou être automatisé par la robotique existante de l’installation. Dans tous les cas, le système doit être facile à utiliser pour que les opérateurs puissent effectuer l’essai en toute efficacité et déterminer rapidement si un échantillon d’amortisseur est accepté. Le système doit généralement offrir une capacité de force comprise entre 2 000 et 6 000 livres.
Q : Quelles solutions d’essais l’entreprise MTS propose-t-elle pour une ligne de production d’amortisseurs ?
R. Simpson : les testeurs d’amortisseurs de ligne de production à vérin électromagnétique linéaire, ou LEMA, conviennent parfaitement aux environnements de production. Ils sont de bonne taille en termes de capacité de force, et leur facilité d’utilisation et leur réactivité garantissent le maintien de cadences élevées. Qui plus est, ils sont dotés d’une architecture ouverte qui permet une intégration totale ou partielle dans la ligne.
Q : Quels facteurs les clients doivent-ils prendre en compte pour les essais de production d’amortisseurs ?
S. Bieganek : l’impact sur les installations est un élément clé à prendre en compte lors de l’achat de systèmes d’essais. Toutes les usines de fabrication disposent d’une infrastructure électrique, ce qui fait qu’un système d’essais LEMA est idéal pour les essais de qualité de la production. La polyvalence entre aussi en ligne de compte. Les systèmes LEMA sont entièrement programmables, ce qui facilite et accélère le changement de ligne de production. Il y a aussi des facteurs pratiques, comme la facilité d’utilisation. Sur ces systèmes, un voyant lumineux indique l’état de réussite ou d’échec et l’interface numérique permet de placer les éprouvettes de manière robotique ou par intervention humaine à la fin de l’essai. L’efficacité opérationnelle est un autre facteur important. L’actionnement électrique consomme de l’énergie à la demande, il est donc plus efficace et moins coûteux que l’actionnement hydraulique dans ce cas. Enfin, les systèmes LEMA nécessitent peu de maintenance, ce qui garantit un temps de fonctionnement élevé et un fonctionnement efficace.
Q : En quoi les applications diffèrent-elles pour les essais d’amortisseurs en laboratoire ?
S. Bieganek : il existe deux applications principales : les essais de caractérisation d’une seule éprouvette et les essais de durabilité sur plusieurs éprouvettes. La caractérisation consiste à appliquer un déplacement ou une vitesse dans l’amortisseur et à mesurer la réponse de force. Les ingénieurs effectuent des essais de gaz pour éliminer le gaz de la partie analyse de la courbe force-vitesse. Les essais d’étanchéité les aident à comprendre les caractéristiques de broutage. Les essais de bruit, de vibration et de dureté déterminent les caractéristiques des bruits de sifflement et de chuintement. Il existe également des essais environnementaux pour connaître la réaction des amortisseurs aux changements de température ou d’humidité. Tout cela a pour but d’améliorer la conception du produit. Les essais de durabilité sont nécessaires pour déterminer la durée de vie attendue du produit dans des conditions réelles et nécessitent l’application d’entrées sinusoïdales, de blocs, cycliques, aléatoires ou de profil de route. Pour optimiser la productivité des essais, les essais de durabilité sont généralement effectués avec plusieurs éprouvettes, ce qui nécessite un système d’essais ayant une capacité de force supérieure à celle d’un système de caractérisation.
Q : Quelles solutions l’entreprise MTS propose-t-elle pour les essais d’amortisseurs dans un environnement de laboratoire ?
R. Simpson :MTS propose une large gamme d’options pour les essais d’amortisseurs en laboratoire. Les systèmes électriques SYD (dynamomètre à bielle manivelle ; souvent appelés dynamomètres à manivelle), sont un bon choix pour les laboratoires à budget limité qui n’ont besoin que d’entrées sinusoïdales. Les systèmes à vérin électromagnétique ou systèmes EMA 2K, 4K et 6K offrent des capacités de force de 9 à 53 kN et des entrées programmables plus complexes. Ces deux systèmes électriques sont silencieux, faciles à entretenir et rentables. Il existe ensuite une gamme complète de systèmes hydrauliques, dont les systèmes d’essais d’amortisseurs MTS 849, 850 et 852, qui sont suffisamment polyvalents pour traiter les données de charge sur route. Ils sont dotés de capacités de force plus élevées, de 15 à 150 N, et sont facilement extensibles pour fournir des forces plus élevées si les besoins du laboratoire évoluent.
Q : Comment les laboratoires peuvent-ils choisir la bonne solution en fonction de leur situation spécifique d’essai d’amortisseurs ?
Bieganek: il y a plusieurs facteurs à prendre en compte et ce n’est pas toujours évident. Le fait que le laboratoire dispose déjà ou non d’une infrastructure hydraulique est très important. S’il en a déjà une, un système hydraulique sera plus abordable que si le laboratoire doit ajouter cette infrastructure. Si le laboratoire se consacre à la caractérisation d’éprouvettes uniques, les systèmes EMA sont une bonne solution. Cependant, si le laboratoire a l’intention d’effectuer des essais de caractérisation et de durabilité avec le même système (ou de garder la possibilité de réaliser des essais de durabilité à l’avenir), il vaut mieux opter pour un système hydraulique. Il en va de même pour la capacité de force : les besoins resteront-ils les mêmes ou augmenteront-ils avec le temps ? Le laboratoire peut également avoir des priorités plus importantes qui influencent sa décision, comme l’investissement total en capital, une référence en matière d’efficacité énergétique, un engagement envers le respect de l’environnement ou une grande importance accordée à la facilité d’utilisation. MTS a travaillé avec des centaines de laboratoires et nous pouvons vous aider à trouver un système d’essais qui correspond à tous les besoins de votre laboratoire.
Q : Et pour les terrains d’essai ou les pistes de course ? Quelles applications d’essais d’amortisseurs sont importantes ici ?
R. Simpson : qu’il s’agisse d’un équipementier sur le terrain d’essai ou d’une équipe de course sur la piste, l’application correspond presque toujours à la caractérisation d’une seule éprouvette. Il est parfois nécessaire de faire un essai d’étanchéité ou de gaz, mais la plupart du temps, nos clients souhaitent vérifier la courbe force-vitesse d’un amortisseur, l’ajuster en conséquence, puis le tester dans un véhicule. Concrètement, les ingénieurs d’essais cherchent à identifier les vitesses présentant un intérêt et les impacts sur la piste, à effectuer un test sinusoïdal basé sur les données d’entrée de la route et à analyser la courbe de l’amortisseur à une vitesse spécifique. Les équipementiers mesurent les attributs dynamiques des véhicules, tandis que les équipes de course obtiennent des informations du pilote. Dans un cas comme dans l’autre, les contraintes de temps peuvent être très fortes, c’est pourquoi la rapidité et l’efficacité des essais sont très importantes. Il en va de même pour la régularité des essais, que ce soit lors des tours d’essais, des qualifications ou le jour de la course.
Q : Quelles exigences les systèmes d’essais d’amortisseurs doivent-ils remplir dans un environnement de piste ?
S. Bieganek : la portabilité et la taille du système d’essais sont essentielles dans un environnement de piste. Ces essais sont généralement effectués dans des fourgons ou des semi-remorques où l’espace est limité. Les systèmes d’essais doivent offrir le bon niveau de programmabilité et de performance ; ils doivent également être abordables, compte tenu de la diversité des clients et des niveaux d’investissement dans le monde des courses. Pour le pilote amateur, un système de la série SYD (dynamomètre à manivelle) est parfait. Les systèmes EMA sont petits, portables et légers, mais ils offrent les capacités avancées dont les équipes de course professionnelles ont besoin. Ils ne nécessitent pas d’infrastructure hydraulique et sont faciles à entretenir.
Q : Revenons sur la simulation de route couplée aux pneus. Quelles applications sont réalisées dans des environnements de production ?
S. Bieganek : les essais BSR (bourdonnement, grincement et cliquetis) sont la principale application de simulation de route pour un environnement de production. Comme pour les essais d’amortisseurs, ils peuvent être entièrement intégrés dans la ligne de production pour tester chaque véhicule. Ils peuvent aussi être réalisés hors ligne dans le cadre d’audit de qualité avec quelques échantillons de véhicules par heure. Les systèmes d’essais pour les BSR doivent fournir une capacité de force adéquate par rapport à la taille du véhicule, ainsi qu’un faible niveau de bruit (moins de 60 dB) afin de ne pas interférer avec l’essai.
Q : Quelles solutions l’entreprise MTS propose-t-elle pour les essais BSR dans un environnement de production ?
S. Bieganek : plusieurs systèmes d’essais sont disponibles, notamment les simulateurs de route couplés aux pneus ePost modèle 320, qui fonctionnent par commande électrique. La configuration 4K est adaptée aux voitures de petite et grande taille et la configuration 6K convient aux voitures de grande taille jusqu’aux véhicules utilitaires légers et aux SUV. Le fonctionnement de ces systèmes est plus silencieux. Comme les systèmes LEMA, ils sont électriques et s’adaptent donc mieux à l’infrastructure existante de l’environnement de production. Ils offrent des performances très efficaces et des avantages environnementaux uniques. Qui plus est, ils disposent d’une interface utilisateur optimisée au niveau de la conception pour des enquêtes BSR approfondies et efficaces, de sorte qu’un opérateur puisse effectuer l’essai depuis l’intérieur du véhicule. Pour les environnements de production disposant d’une infrastructure d’alimentation et de distribution hydraulique existante, le système hydraulique First Road modèle 320 peut également être utilisé.
Q : Les applications de simulation de route sont-elles différentes dans un environnement de laboratoire d’essais ?
R. Simpson : oui, le laboratoire d’essais s’intéresse aux enquêtes BSR, ainsi qu’aux enquêtes plus détaillées sur le bruit, les vibrations et la dureté (NVH). Il s’agit essentiellement d’essais BSR effectués dans une chambre climatique simulant la pluie/l’humidité, la température ou l’exposition au soleil pour tenir compte du vieillissement de l’éprouvette. Certains laboratoires ont des chambres anéchoïques pour créer un environnement d’essai encore plus silencieux. Par ailleurs, les laboratoires sont souvent chargés d’effectuer des essais de durabilité pour déterminer les caractéristiques relatives à la durée de vie des sous-systèmes et des véhicules complets.
Q : A quelles exigences les simulateurs de route doivent-ils répondre dans un environnement de laboratoire ?
S. Bieganek : cela dépend en grande partie de la taille du véhicule testé, s’il s’agit d’une petite voiture ou d’une pièce d’un équipement agricole. La capacité de force, la vitesse et l’accélération doivent toutes être adaptées au véhicule. Pour les essais BSR, il est très important d’avoir un faible niveau de bruit. La flexibilité des simulateurs est également importante pour pouvoir s’adapter à plusieurs types de véhicules et s’intégrer parfaitement à diverses chambres climatiques.
Q : Quelles solutions électriques l’entreprise MTS propose-t-elle pour la simulation de route couplée à des pneus en laboratoire ?
R. Simpson : les systèmes ePost modèle 320 fonctionnent par commande électrique et peuvent accueillir des véhicules de type moto, véhicule tout-terrain, voiture de grande taille ou véhicule utilitaire léger. Conçus spécialement pour les essais BSR, ils ont un faible impact sur les installations et ne nécessitent qu’un faible investissement en capital. Comme d’autres systèmes électriques, ils sont très faciles à utiliser, à entretenir et à configurer. Et ils peuvent s’adapter aux essais environnementaux.
Q : Quelles solutions hydrauliques l’entreprise MTS propose-t-elle pour la simulation de route couplée à des pneus en laboratoire ?
S. Bieganek : les simulateurs hydrauliques polyvalents modèle 320 sont conçus pour les essais de durabilité, mais ils peuvent être réglés pour les essais BSR. Ces systèmes offrent des performances éprouvées pour des applications nécessitant une force plus importante, ainsi qu’une vitesse et une accélération plus élevées. Ils peuvent accueillir de gros véhicules, y compris des poids lourds et des équipements de construction et agricoles. Là encore, tout dépend de l’infrastructure dont dispose le laboratoire et s’il souhaite avoir la possibilité d’ajouter des essais de durabilité à l’avenir.
Contactez MTS dès aujourd’hui et découvrez la diversité de notre offre de solutions d’essais d’amortisseurs électriques et hydrauliques et de simulation de route qui peuvent répondre à vos besoins spécifiques en matière de production, de laboratoire ou de terrain d’essai/piste.
S. Bieganek : le choix de la technologie à déployer dépend beaucoup de la situation et de nombreux facteurs, tels que les exigences fonctionnelles et de performance du système, le budget disponible, l’infrastructure existante,… C’est complexe. Il vaut mieux commencer par considérer le type d’environnement de l’essai (site/usine de production, laboratoire de recherche et de développement, terrain d’essai/piste de course) et partir de là. Les gammes de solutions d’essais d’amortisseurs et de simulation de route couplée à des pneus de MTS proposent un mélange complémentaire de systèmes électriques et hydrauliques. C’est notre travail que de faire profiter nos clients de notre expérience et de notre expertise pour les aider à trouver un système qui répond à leurs besoins actuels et futurs.
Q : Commençons par les essais d’amortisseurs dans un environnement de production. Quelles sont les principales applications ?
S. Bieganek : en général, les clients doivent effectuer des essais de caractérisation en ligne pour s’assurer que l’amortisseur a été assemblé correctement et qu’il fonctionne comme prévu. En d’autres termes, cela revient à faire un contrôle de la qualité. Ils vérifient généralement la force d’amortissement, la pression du gaz et les niveaux d’huile. L’essai peut être entièrement intégré à la ligne de production pour tester chaque amortisseur. Ou alors, il peut s’agir d’un audit de qualité, lors duquel le client prélève quelques échantillons toutes les heures et les teste hors ligne.
Q : Quelles sont les caractéristiques de performances qu’un système d’essais d’amortisseurs doit avoir dans un environnement de production ?
R. Simpson : la vitesse est essentielle. Le système d’essais ne doit pas retarder la ligne de production ou entraîner des blocages. Il se peut qu’il doive être intégré à la ligne pour améliorer la productivité ou être automatisé par la robotique existante de l’installation. Dans tous les cas, le système doit être facile à utiliser pour que les opérateurs puissent effectuer l’essai en toute efficacité et déterminer rapidement si un échantillon d’amortisseur est accepté. Le système doit généralement offrir une capacité de force comprise entre 2 000 et 6 000 livres.
Q : Quelles solutions d’essais l’entreprise MTS propose-t-elle pour une ligne de production d’amortisseurs ?
R. Simpson : les testeurs d’amortisseurs de ligne de production à vérin électromagnétique linéaire, ou LEMA, conviennent parfaitement aux environnements de production. Ils sont de bonne taille en termes de capacité de force, et leur facilité d’utilisation et leur réactivité garantissent le maintien de cadences élevées. Qui plus est, ils sont dotés d’une architecture ouverte qui permet une intégration totale ou partielle dans la ligne.
Q : Quels facteurs les clients doivent-ils prendre en compte pour les essais de production d’amortisseurs ?
S. Bieganek : l’impact sur les installations est un élément clé à prendre en compte lors de l’achat de systèmes d’essais. Toutes les usines de fabrication disposent d’une infrastructure électrique, ce qui fait qu’un système d’essais LEMA est idéal pour les essais de qualité de la production. La polyvalence entre aussi en ligne de compte. Les systèmes LEMA sont entièrement programmables, ce qui facilite et accélère le changement de ligne de production. Il y a aussi des facteurs pratiques, comme la facilité d’utilisation. Sur ces systèmes, un voyant lumineux indique l’état de réussite ou d’échec et l’interface numérique permet de placer les éprouvettes de manière robotique ou par intervention humaine à la fin de l’essai. L’efficacité opérationnelle est un autre facteur important. L’actionnement électrique consomme de l’énergie à la demande, il est donc plus efficace et moins coûteux que l’actionnement hydraulique dans ce cas. Enfin, les systèmes LEMA nécessitent peu de maintenance, ce qui garantit un temps de fonctionnement élevé et un fonctionnement efficace.
Q : En quoi les applications diffèrent-elles pour les essais d’amortisseurs en laboratoire ?
S. Bieganek : il existe deux applications principales : les essais de caractérisation d’une seule éprouvette et les essais de durabilité sur plusieurs éprouvettes. La caractérisation consiste à appliquer un déplacement ou une vitesse dans l’amortisseur et à mesurer la réponse de force. Les ingénieurs effectuent des essais de gaz pour éliminer le gaz de la partie analyse de la courbe force-vitesse. Les essais d’étanchéité les aident à comprendre les caractéristiques de broutage. Les essais de bruit, de vibration et de dureté déterminent les caractéristiques des bruits de sifflement et de chuintement. Il existe également des essais environnementaux pour connaître la réaction des amortisseurs aux changements de température ou d’humidité. Tout cela a pour but d’améliorer la conception du produit. Les essais de durabilité sont nécessaires pour déterminer la durée de vie attendue du produit dans des conditions réelles et nécessitent l’application d’entrées sinusoïdales, de blocs, cycliques, aléatoires ou de profil de route. Pour optimiser la productivité des essais, les essais de durabilité sont généralement effectués avec plusieurs éprouvettes, ce qui nécessite un système d’essais ayant une capacité de force supérieure à celle d’un système de caractérisation.
Q : Quelles solutions l’entreprise MTS propose-t-elle pour les essais d’amortisseurs dans un environnement de laboratoire ?
R. Simpson :MTS propose une large gamme d’options pour les essais d’amortisseurs en laboratoire. Les systèmes électriques SYD (dynamomètre à bielle manivelle ; souvent appelés dynamomètres à manivelle), sont un bon choix pour les laboratoires à budget limité qui n’ont besoin que d’entrées sinusoïdales. Les systèmes à vérin électromagnétique ou systèmes EMA 2K, 4K et 6K offrent des capacités de force de 9 à 53 kN et des entrées programmables plus complexes. Ces deux systèmes électriques sont silencieux, faciles à entretenir et rentables. Il existe ensuite une gamme complète de systèmes hydrauliques, dont les systèmes d’essais d’amortisseurs MTS 849, 850 et 852, qui sont suffisamment polyvalents pour traiter les données de charge sur route. Ils sont dotés de capacités de force plus élevées, de 15 à 150 N, et sont facilement extensibles pour fournir des forces plus élevées si les besoins du laboratoire évoluent.
Q : Comment les laboratoires peuvent-ils choisir la bonne solution en fonction de leur situation spécifique d’essai d’amortisseurs ?
Bieganek: il y a plusieurs facteurs à prendre en compte et ce n’est pas toujours évident. Le fait que le laboratoire dispose déjà ou non d’une infrastructure hydraulique est très important. S’il en a déjà une, un système hydraulique sera plus abordable que si le laboratoire doit ajouter cette infrastructure. Si le laboratoire se consacre à la caractérisation d’éprouvettes uniques, les systèmes EMA sont une bonne solution. Cependant, si le laboratoire a l’intention d’effectuer des essais de caractérisation et de durabilité avec le même système (ou de garder la possibilité de réaliser des essais de durabilité à l’avenir), il vaut mieux opter pour un système hydraulique. Il en va de même pour la capacité de force : les besoins resteront-ils les mêmes ou augmenteront-ils avec le temps ? Le laboratoire peut également avoir des priorités plus importantes qui influencent sa décision, comme l’investissement total en capital, une référence en matière d’efficacité énergétique, un engagement envers le respect de l’environnement ou une grande importance accordée à la facilité d’utilisation. MTS a travaillé avec des centaines de laboratoires et nous pouvons vous aider à trouver un système d’essais qui correspond à tous les besoins de votre laboratoire.
Q : Et pour les terrains d’essai ou les pistes de course ? Quelles applications d’essais d’amortisseurs sont importantes ici ?
R. Simpson : qu’il s’agisse d’un équipementier sur le terrain d’essai ou d’une équipe de course sur la piste, l’application correspond presque toujours à la caractérisation d’une seule éprouvette. Il est parfois nécessaire de faire un essai d’étanchéité ou de gaz, mais la plupart du temps, nos clients souhaitent vérifier la courbe force-vitesse d’un amortisseur, l’ajuster en conséquence, puis le tester dans un véhicule. Concrètement, les ingénieurs d’essais cherchent à identifier les vitesses présentant un intérêt et les impacts sur la piste, à effectuer un test sinusoïdal basé sur les données d’entrée de la route et à analyser la courbe de l’amortisseur à une vitesse spécifique. Les équipementiers mesurent les attributs dynamiques des véhicules, tandis que les équipes de course obtiennent des informations du pilote. Dans un cas comme dans l’autre, les contraintes de temps peuvent être très fortes, c’est pourquoi la rapidité et l’efficacité des essais sont très importantes. Il en va de même pour la régularité des essais, que ce soit lors des tours d’essais, des qualifications ou le jour de la course.
Q : Quelles exigences les systèmes d’essais d’amortisseurs doivent-ils remplir dans un environnement de piste ?
S. Bieganek : la portabilité et la taille du système d’essais sont essentielles dans un environnement de piste. Ces essais sont généralement effectués dans des fourgons ou des semi-remorques où l’espace est limité. Les systèmes d’essais doivent offrir le bon niveau de programmabilité et de performance ; ils doivent également être abordables, compte tenu de la diversité des clients et des niveaux d’investissement dans le monde des courses. Pour le pilote amateur, un système de la série SYD (dynamomètre à manivelle) est parfait. Les systèmes EMA sont petits, portables et légers, mais ils offrent les capacités avancées dont les équipes de course professionnelles ont besoin. Ils ne nécessitent pas d’infrastructure hydraulique et sont faciles à entretenir.
Q : Revenons sur la simulation de route couplée aux pneus. Quelles applications sont réalisées dans des environnements de production ?
S. Bieganek : les essais BSR (bourdonnement, grincement et cliquetis) sont la principale application de simulation de route pour un environnement de production. Comme pour les essais d’amortisseurs, ils peuvent être entièrement intégrés dans la ligne de production pour tester chaque véhicule. Ils peuvent aussi être réalisés hors ligne dans le cadre d’audit de qualité avec quelques échantillons de véhicules par heure. Les systèmes d’essais pour les BSR doivent fournir une capacité de force adéquate par rapport à la taille du véhicule, ainsi qu’un faible niveau de bruit (moins de 60 dB) afin de ne pas interférer avec l’essai.
Q : Quelles solutions l’entreprise MTS propose-t-elle pour les essais BSR dans un environnement de production ?
S. Bieganek : plusieurs systèmes d’essais sont disponibles, notamment les simulateurs de route couplés aux pneus ePost modèle 320, qui fonctionnent par commande électrique. La configuration 4K est adaptée aux voitures de petite et grande taille et la configuration 6K convient aux voitures de grande taille jusqu’aux véhicules utilitaires légers et aux SUV. Le fonctionnement de ces systèmes est plus silencieux. Comme les systèmes LEMA, ils sont électriques et s’adaptent donc mieux à l’infrastructure existante de l’environnement de production. Ils offrent des performances très efficaces et des avantages environnementaux uniques. Qui plus est, ils disposent d’une interface utilisateur optimisée au niveau de la conception pour des enquêtes BSR approfondies et efficaces, de sorte qu’un opérateur puisse effectuer l’essai depuis l’intérieur du véhicule. Pour les environnements de production disposant d’une infrastructure d’alimentation et de distribution hydraulique existante, le système hydraulique First Road modèle 320 peut également être utilisé.
Q : Les applications de simulation de route sont-elles différentes dans un environnement de laboratoire d’essais ?
R. Simpson : oui, le laboratoire d’essais s’intéresse aux enquêtes BSR, ainsi qu’aux enquêtes plus détaillées sur le bruit, les vibrations et la dureté (NVH). Il s’agit essentiellement d’essais BSR effectués dans une chambre climatique simulant la pluie/l’humidité, la température ou l’exposition au soleil pour tenir compte du vieillissement de l’éprouvette. Certains laboratoires ont des chambres anéchoïques pour créer un environnement d’essai encore plus silencieux. Par ailleurs, les laboratoires sont souvent chargés d’effectuer des essais de durabilité pour déterminer les caractéristiques relatives à la durée de vie des sous-systèmes et des véhicules complets.
Q : A quelles exigences les simulateurs de route doivent-ils répondre dans un environnement de laboratoire ?
S. Bieganek : cela dépend en grande partie de la taille du véhicule testé, s’il s’agit d’une petite voiture ou d’une pièce d’un équipement agricole. La capacité de force, la vitesse et l’accélération doivent toutes être adaptées au véhicule. Pour les essais BSR, il est très important d’avoir un faible niveau de bruit. La flexibilité des simulateurs est également importante pour pouvoir s’adapter à plusieurs types de véhicules et s’intégrer parfaitement à diverses chambres climatiques.
Q : Quelles solutions électriques l’entreprise MTS propose-t-elle pour la simulation de route couplée à des pneus en laboratoire ?
R. Simpson : les systèmes ePost modèle 320 fonctionnent par commande électrique et peuvent accueillir des véhicules de type moto, véhicule tout-terrain, voiture de grande taille ou véhicule utilitaire léger. Conçus spécialement pour les essais BSR, ils ont un faible impact sur les installations et ne nécessitent qu’un faible investissement en capital. Comme d’autres systèmes électriques, ils sont très faciles à utiliser, à entretenir et à configurer. Et ils peuvent s’adapter aux essais environnementaux.
Q : Quelles solutions hydrauliques l’entreprise MTS propose-t-elle pour la simulation de route couplée à des pneus en laboratoire ?
S. Bieganek : les simulateurs hydrauliques polyvalents modèle 320 sont conçus pour les essais de durabilité, mais ils peuvent être réglés pour les essais BSR. Ces systèmes offrent des performances éprouvées pour des applications nécessitant une force plus importante, ainsi qu’une vitesse et une accélération plus élevées. Ils peuvent accueillir de gros véhicules, y compris des poids lourds et des équipements de construction et agricoles. Là encore, tout dépend de l’infrastructure dont dispose le laboratoire et s’il souhaite avoir la possibilité d’ajouter des essais de durabilité à l’avenir.
Contactez MTS dès aujourd’hui et découvrez la diversité de notre offre de solutions d’essais d’amortisseurs électriques et hydrauliques et de simulation de route qui peuvent répondre à vos besoins spécifiques en matière de production, de laboratoire ou de terrain d’essai/piste.