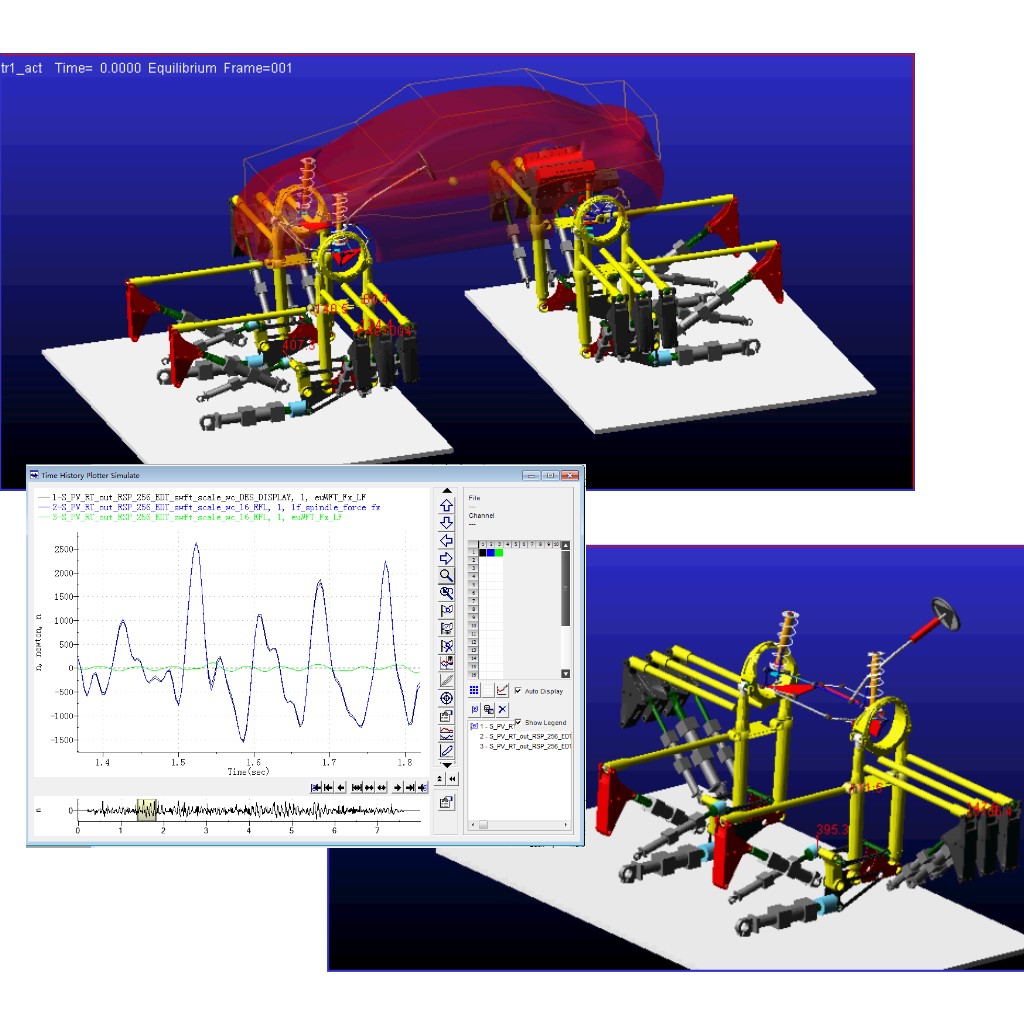
Soumis à une pression constante pour raccourcir les cycles de développement et réduire les coûts, les constructeurs automobiles cherchent de plus en plus à utiliser des outils d’analyse pour effectuer des évaluations virtuelles significatives des conceptions de véhicules dès le début, bien avant que les prototypes physiques ne soient disponibles. La capacité à obtenir des charges précises prédites (ou calculées) de cette manière augmente l’efficacité des essais physiques des composants, permet d’identifier et d’éliminer au plus tôt des défauts de conception, réduit la nécessité de retravailler et de s’appuyer sur des prototypes et rationalise la validation de la conception.
Diverses approches de simulation ont été conçues pour obtenir des charges calculées précises plus tôt dans le processus de développement des véhicules. Une méthode, celle du terrain d’essai virtuel, consiste à « conduire » un modèle de véhicule sur une route numérisée. Bien qu’elle ait l’avantage de s’appuyer entièrement sur des modèles virtuels, cette approche génère des charges inexactes difficiles à valider par des essais physiques. Une méthode semi-analytique, en revanche, utilise des charges de moyeu acquises à partir d’un véhicule existant pour stimuler le modèle de véhicule. Cette méthode donne de meilleurs résultats que le terrain d’essai virtuel, mais établit des conditions limites qui ne sont pas tout à fait appropriées au modèle de véhicule, si bien que les charges calculées sont toujours incorrectes et difficiles à valider. Une troisième méthode, les essais virtuels, résout ces problèmes en intégrant un modèle d’un système d’essais physiques réels dans la simulation pour stimuler le modèle de véhicule.
Les essais virtuels correspondent à la simulation d’un essai physique, à l’aide d’outils d’analyse par éléments finis, d’outils d’analyse dynamique multicorps et de techniques d’itération de RPC pour obtenir des informations précises sur les charges, les mouvements et les dommages d’un système de véhicule très tôt dans le processus de développement. Les avantages de cette approche sont nombreux. Premièrement, dans la mesure où il est plus facile de modéliser les contraintes d’un système d’essais physiques que de tester des surfaces de sol ou des pneus, les essais virtuels établissent des conditions limites bien plus efficaces que les autres méthodes. Deuxièmement, les essais virtuels utilisent un ensemble d’outils et de techniques d’essais physiques éprouvés et bien établis, qui ont démontré leur utilité dans le domaine de l’analyse. Et troisièmement, intégrer un système d’essais physiques modélisés rationalise considérablement la validation des résultats grâce à des essais physiques ultérieurs et permet d’améliorer les configurations des essais physiques et la conception des dispositifs de fixation. Les essais virtuels, qui englobent les disciplines de l’analyse et des essais physiques, nécessitent d’avoir une connaissance avancée des outils d’IAO et des essais physiques, de développer un processus pour relier le logiciel RPC Pro et les modèles d’analyse et d’avoir, de préférence, un certain degré d’exposition et d’expérience en matière d’essais virtuels.
Pendant des années, l’entreprise MTS s’est attachée à perfectionner l’approche des essais virtuels, en menant divers projets de démonstration avec des clients clés comme Hyundai Motor Company (HMC) et Thermo King pour évaluer différentes méthodologies. Ces projets comprenaient des essais virtuels de véhicules complets et de sous-systèmes, qui ont tous abouti à une corrélation satisfaisante avec les données de charge sur route (RLD) mesurées ou les essais physiques réels. La méthodologie de base tirée de ces expériences comprend les étapes suivantes : 1) Connexion des modèles de banc d’essai avec les modèles d’éprouvettes ; 2) Couplage des modèles avec RPC Pro ; 3) Reproduction des données de charge sur route sur le banc d’essai virtuel ; 4) Extraction des charges calculées ; 5) Création de l’essai physique du composant/sous-système.
Un récent projet de démonstration réalisé avec State Automotive Institute of China (SAIC) illustre parfaitement la mise en pratique de cette méthodologie :
- Connexion des modèles de banc d’essai avec les modèles d’éprouvettes
Au début du projet, MTS a construit une série de modèles de bancs d’essai dans des formats ADAMS, Simulink et de cosimulation ADAMS/Simulink. Les bancs d’essai de MTS qui ont été modélisés comprenaient divers simulateurs de route couplés au moyeu modèle 329, un système MAST (Table de simulation multiaxiale) modèle 353.20 et un système d’essais de composants TestLine. Certains composants du banc d’essai ont également été modélisés, notamment un contrôleur numérique FlexTest, des vérins et des servovalves MTS, ainsi qu’un transformateur de vérins qui convertit le déplacement, l’accélération et la force des vérins en déplacement, accélération et force DOF. Etant donné les contraintes de temps du projet et les vitesses de simulation relativement lentes des modèles de cosimulation les plus complexes, le modèle ADAMS/Car 329 a été couplé à des modèles SAIC de véhicule complet, de suspension avant et de suspension arrière et a finalement été utilisé pour la majeure partie des essais virtuels.
- Couplage des modèles avec RPC Pro
Un serveur d’essais virtuels a été développé pour connecter le logiciel RPC Pro et le modèle ADAMS/Car 329. Pendant les essais, RPC Pro utilise ce serveur virtuel pour envoyer des fichiers de commande au modèle ADAMS, lancer la simulation ADAMS et copier le fichier de réponse du dossier ADAMS vers le répertoire de travail de RPC Pro. En outre, un outil d’interface Matlab déjà présent dans RPC Pro a été utilisé pour coupler RPC Pro avec les modèles de cosimulation.
- Reproduction des données de charge sur route sur le banc d’essai virtuel
La technique d’itération de RPC a ensuite été utilisée pour reproduire les données de charge sur route (force du moyeu) recueillies sur le terrain d’essai lors de divers événements et manœuvres sélectionnés. Curieusement, les itérations initiales de RPC sur les bancs 329 virtuels n’ont montré aucune convergence, ce qui suggère des défauts dans le modèle de véhicule SAIC. L’analyse ultérieure du modèle a en effet révélé des lacunes, qui ont été corrigées rapidement. Grâce à l’amélioration du modèle, les itérations de RPC ont finalement convergé, montrant une excellente corrélation entre les signaux souhaités et obtenus et de faibles erreurs RMS sur tous les canaux pour les simulations virtuelles de véhicules complets et partiels.
- Extraction des charges calculées
Lors de la convergence des itérations de RPC, il est possible d’obtenir facilement, à partir du modèle de véhicule, les charges calculées pour n’importe quel composant ou sous-système mécanique, en fonction du temps.
- Création de l’essai physique
Les historiques des temps de charge extraits du modèle de véhicule ont ensuite été utilisés pour définir les essais physiques ultérieurs des composants. Une fois qu’il a été déterminé si une pièce est soumise à un chargement à un ou plusieurs axes, l’ensemble des méthodes et des outils d’essais RPC Pro peut être utilisé pour définir des essais de composants considérablement accélérés. Pour les composants soumis à un chargement à axe unique, la méthode du cycle de blocs ou les méthodes PSD (Densité spectrale de puissance) peuvent être utilisées. Pour les composants soumis à un chargement à plusieurs axes, la méthode de fractionnement de pic/creux peut être utilisée. Pour les situations où la fréquence de chargement d’un composant doit être préservée, la méthode de reproduction de l’historique temporel est la plus appropriée ; pour ces types d’essais, RPC Pro dispose d’une fonction d’édition sensible à la fatigue qui peut accélérer les essais de durabilité de 2 à 10 fois. Une fois que les signaux de chargement sont déterminés pour chaque composant, le même système d’essais physiques sur lequel étaient basés les bancs d’essai virtuels peut être utilisé pour effectuer l’essai des composants. En outre, diverses techniques de compensation présentes dans RPC Pro, telles que la compensation pic/creux, la compensation inverse adaptative et l’itération de RPC, peuvent être utilisées pour garantir que les conditions de chargement souhaitées sont obtenues avec précision lors des essais physiques.
Les recherches continues de MTS sur les essais virtuels montrent qu’il s’agit d’un moyen efficace de prédire avec précision les charges des composants avant le développement de pièces physiques ou de prototypes. Une fois ces charges calculées, les mêmes outils et techniques RPC Pro utilisés pour les obtenir peuvent ensuite servir à créer et à effectuer les essais physiques nécessaires pour valider leur précision, ainsi que celle du modèle de véhicule. Les impacts potentiels d’un essai virtuel efficace sur le développement des véhicules sont considérables. La disponibilité de charges prédites précises et les essais physiques ultérieurs plus précoces minimiseront les remaniements des composants et des sous-systèmes, réduiront le besoin de plusieurs prototypes et accéléreront la validation de la conception. Aussi, le rôle des essais physiques évoluera également : si les essais resteront nécessaires pour valider définitivement la conception d’un véhicule, ils seront de plus en plus adaptés pour valider la précision du modèle de véhicule. Enfin, les essais virtuels favoriseront l’intégration des disciplines et des cultures de l’analyse et des essais physiques, ce qui entraînera des gains d’efficacité grâce au partage d’outils, de processus et d’expériences.
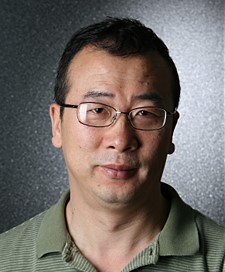