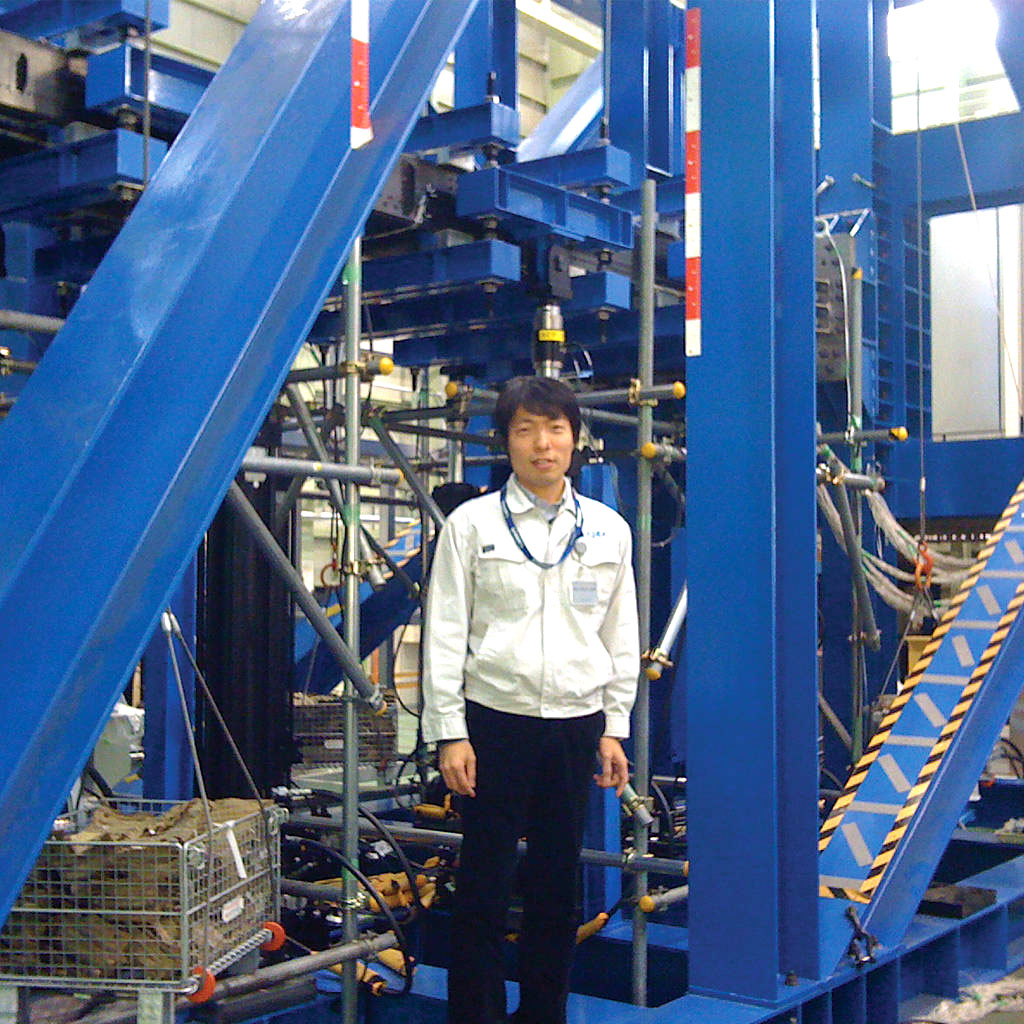
DÉFI DU CLIENT
Dans le cadre de sa mission de faire progresser la recherche aérospatiale, l’Agence d’exploration aérospatiale japonaise (JAXA) met au point des technologies et des méthodes d’évaluation innovantes pour améliorer la qualité et réduire le coût des matériaux, des composants et des structures des aéronefs. Pour les avions de ligne, qualité rime avec sécurité. L’équipe chargée du transport civil de la JAXA, le Groupe du programme aéronautique, doit donc être absolument certaine que toutes les méthodes de production qu’elle met en place réduisent non seulement les coûts, mais permettent également d’obtenir des produits qui répondent aux normes les plus élevées en matière de durabilité, de résistance et de fiabilité.
L’augmentation des coûts du carburant et la priorité accordée aux économies d’énergie dans le monde entier ont généré une forte demande d’avions plus légers, consommant moins de carburant. Cependant, les composants et les structures composites utilisés pour atteindre cet objectif coûtent généralement plus cher à produire que leurs équivalents conventionnels en aluminium. Yuichiri Aioki et son groupe chargé des matériaux composites avancés ont entrepris de résoudre ce dilemme. L’équipe s’est intéressée en particulier à la nouvelle technologie VaRTM (fabrication de moulage par transfert de résine sous vide) afin d’explorer son potentiel de production de composants et de structures composites à faible coût. Ils ont découvert que ce procédé innovant par infusion de résine pouvait produire des pièces composites qui pesaient non seulement 20 % de moins, mais coûtaient également 20 % de moins que les produits fabriqués à l’aide de méthodes conventionnelles. Le procédé VaRTM a permis de réduire le coût et le poids des pièces par rapport aux procédés classiques de préimprégnation en autoclave en utilisant un moulage simple face plus rationalisé, sans autoclave, afin de former des structures composites plus grandes et plus complexes avec moins de pièces.
Après avoir prouvé l’efficacité du procédé VaRTM en tant que procédé de production à faible coût, Yuichiri Aioki et son équipe ont ensuite dû prouver que les pièces produites par le procédé VaRTM pouvaient résister aux charges complexes subies par les aéronefs en vol. Les essais mécaniques étaient un élément clé de cette mission. Les solutions d’essais mécaniques sélectionnées par la JAXA devaient être suffisamment flexibles pour gérer les exigences des essais requis et capables de fournir les niveaux élevés de contrôle nécessaires pour répondre aux exigences multiaxiales de la simulation en conditions réelles.
La JAXA a finalement choisi de travailler avec MTS et selon Yuichiri Aioki, c’était un choix facile. « MTS est un leader technologique qui a fait ses preuves en matière de solutions d’essais de composants d’aéronefs », a-t-il affirmé. « L’entreprise possède également l’expertise nécessaire pour nous aider à répondre avec précision et en toute confiance à nos besoins uniques. »
SOLUTIONS MTS
L’objectif du programme d’essais mécaniques de la JAXA était de soumettre les pièces composites générées par le procédé VaRTM aux conditions exigeantes d’un vol réel, y compris les changements brusques d’altitude. Le programme comprenait des essais de fatigue des sous-composants, ainsi que des essais statiques d’une aile à l’échelle 1:1. MTS a aidé la JAXA à atteindre cet objectif en lui proposant des contrôles numériques de précision, des bâtis de charge et des vérins robustes, des logiciels d’application avancés, ainsi que des services de maintenance et d’assistance d’experts.
Pour les essais de fatigue des sous-composants, MTS a fourni un bâti de charge servohydraulique modèle 311.41 (2 500 kN) équipé de mors hydrauliques à force élevée modèle 647.200 pour les éprouvettes à panneaux larges. Le système utilise un contrôleur numérique polyvalent FlexTest® 40 et un PC équipé du logiciel Multi-Purpose TestWare®.
L’équipement pour les essais statiques de l’aile à l’échelle 1:1 comprenait quatre vérins servohydrauliques MTS compacts entraînés par un contrôleur numérique FlexTest 200 haute capacité et un PC client équipé du logiciel de contrôle et d’acquisition de données AeroPro™.
Outre le matériel et les logiciels haute performance, Yuichiri Aioki a également reconnu que les services d’étalonnage et la formation sur site de MTS étaient essentiels au succès de son équipe. « Le service d’étalonnage de MTS était important pour nous permettre de suivre les données de l’expérience. Lors des essais d’aéronefs, la traçabilité des données d’essai est strictement réglementée ; les données qui ne sont pas traçables ne seront pas approuvées. » En ce qui concerne l’assistance MTS, il a ajouté que « lorsque nous avions des questions, les experts de MTS nous ont rapidement apporté les réponses et les conseils dont nous avions besoin pour respecter le calendrier de nos essais ».
AVANTAGES CLIENTS
Les solutions de MTS ont aidé la JAXA à confirmer rapidement et en toute confiance que les pièces composites produites à l’aide du nouveau procédé pouvaient résister aux forces réelles subies par les aéronefs en vol. « Nous pouvons désormais prouver que les matériaux composites fabriqués par le procédé VaRTM ont été soumis à des évaluations de performances rigoureuses et ont démontré leur aptitude à être utilisés dans les ailes d’avion », a déclaré Yuichiri Aioki. « La grande expérience de MTS en matière d’essais de composants structurels à l’échelle 1:1 était évidente, l’entreprise avait clairement les connaissances requises pour mettre au point les solutions d’essais exactes dont nous avions besoin. »
Outre l’expertise interne de MTS, Yuichiri Aioki a indiqué avoir apprécié les forums d’utilisateurs et les séminaires parrainés par MTS. « Le fait de pouvoir échanger des idées et des meilleures pratiques à grande échelle avec d’autres utilisateurs d’appareils MTS est essentiel au succès continu de nos recherches. »
« Grâce à MTS, nous allons bientôt commencer les essais de certification des avions de ligne conçus par des entreprises japonaises », a conclu Yuichiri Aioki. « Le monde disposera bientôt d’un nouveau moyen sûr et rentable de fabriquer des avions commerciaux plus légers et économes en carburant sans compromettre la sécurité des passagers. La fiabilité des équipements d’essais et les conseils des experts de MTS ont été indispensables à cette réalisation. »