
La croissance mondiale des voyages en train fait augmenter la demande de nouveaux wagons pour le transport de passagers, ce qui est une bonne nouvelle pour les fabricants du monde entier. Parallèlement, ces nouvelles voitures doivent répondre à des attentes plus élevées. Les wagons modernes pour le transport de passagers doivent se déplacer à des vitesses plus élevées, offrir un voyage confortable, maximiser l’efficacité énergétique et, bien sûr, être entièrement conformes aux réglementations.
Répondre à ces besoins simultanément présente un ensemble de défis de conception difficiles à relever. L’efficacité dépend de la suppression du poids, mais cela ne peut pas affecter la stabilité. La stabilité devient plus difficile à grande vitesse, et les wagons les plus rapides du monde roulent désormais jusqu’à 350 kilomètres par heure. Le confort de conduite est également plus difficile à obtenir à grande vitesse.
Étant donné que ces facteurs sont liés, les fabricants doivent être en mesure d’optimiser les nouvelles conceptions afin de gérer efficacement les compromis. Par exemple, un bogie plus rigide peut offrir une plus grande stabilité, mais moins de confort pour le pilote. La rigidité de l’arceau de sécurité peut être modifiée pour offrir une meilleure maniabilité ou une expérience passager plus confortable, mais pas les deux à la fois.
Les équipes de développement de produits sont soumises à une pression temporelle intense en raison de la forte demande du marché, et les concepteurs doivent travailler rapidement. C’est là que les essais mécaniques deviennent très utiles.
LES DÉFIS EN LABORATOIRE
Dans le laboratoire d’essai, les concepteurs de composants peuvent examiner de nombreuses itérations d’une nouvelle conception de manière relativement rapide, très contrôlée et reproductible. Les résultats des essais révèlent des coefficients et d’autres facteurs qui peuvent être réinjectés dans des modèles virtuels de composants et de sous-systèmes pour les rendre plus précis. Cela permet d’accélérer le processus d’analyse et d’amélioration des nouvelles conceptions.
Le laboratoire propose ses propres défis. La liste des essais pertinents est longue et chacun nécessite généralement un type de système d’essai différent avec une configuration unique. L’acquisition des systèmes nécessaires pour optimiser les nouvelles conceptions de bogies peut être coûteuse. La configuration et l’exécution des essais peuvent devenir inefficaces lorsque plusieurs systèmes sont utilisés.
Le plus grand des défis est la nécessité de contrôler l’ensemble du mécanisme, et pas seulement un seul composant. Cela peut sembler contre-intuitif, mais les ingénieurs en conception avancés comprennent que le contrôle de pièces individuelles n’offre pas la même précision ou la même information que le contrôle d’un bogie complet.
Bien que les essais réalisés sur des composants distincts soient plus faciles à gérer et puissent être effectués rapidement, ils n’offrent pas la même précision que les essais réalisés sur tous les composants d’un système. Les interactions entre les composants produisent des comportements inattendus dus à la friction et au mouvement hors axe. Ces interactions ne peuvent pas être répliquées en évaluant chaque composant séparément. Les ingénieurs s’en doutent depuis longtemps, mais cela n’est devenu évident qu’au cours de la dernière décennie. Les modèles virtuels sont devenus plus sophistiqués, mais les ingénieurs ont été incapables de prédire avec précision les performances du système ferroviaire en fonction des caractéristiques des composants individuels.
Récemment, un système innovant d’essai de wagons a été mis en service. Il permet de mesurer la cinématique et la conformité d’un mécanisme de bogie complet. Le système, fourni par MTS Systems Corp., peut également être utilisé pour fournir une caractérisation, une durabilité de base et des essais de vibration, le tout dans un seul système.
ESSAI DE SUSPENSION PRIMAIRE ET SECONDAIRE
Actuellement installé chez un constructeur de wagons à grande vitesse en Asie, le nouveau système de mesure de bogie fournit la taille et la force nécessaires pour charger un bogie complet ainsi qu’un wagon complet. Le système d’essai intègre une instrumentation considérable conçue pour des mesures extrêmement précises de ces mécanismes complexes.
La complexité vient des nombreuses façons dont les données d’essai peuvent être déformées. Pour garantir des résultats précis, les systèmes d’essai doivent être capables d’empêcher (ou de compenser) tous les phénomènes suivants : le déphasage causé par le cil ou l’amortissement ; la distorsion du signal et bruit causés par les résonances du système et du spécimen ; et les erreurs de mesure de force résultant de la diaphonie, de la compensation de température des transducteurs, de la dilatation et de la contraction thermiques des montages et des spécimens, des erreurs d’étalonnage, du glissement, de la dérive ou des dommages aux transducteurs, supports, câbles ou conditionneurs. Dans de nombreux cas, plusieurs signaux sont combinés pour calculer le résultat souhaité, ce qui aggrave l’erreur totale.
Certains des essais les plus importants que le système effectue sont ceux de la suspension primaire, qui comprend tous les composants entre le bogie et l’essieu (ressort, ressort hélicoïdal, barre de torsion, biscuit en caoutchouc, etc.). Alors que la suspension principale affecte la direction, la maniabilité et, dans une certaine mesure, le confort du pilote, les ingénieurs doivent comprendre en détail le système complet de montage et de suspension de l’essieu pour optimiser les nouvelles conceptions. La rigidité de la suspension principale se situe dans la même plage que la rigidité du cadre de bogie, et l’interaction entre les deux détermine la réponse globale de tenue de route du bogie. Pour cette raison, le nouveau système d’essai est spécialement conçu pour mesurer les contributions des composants individuels ou les caractéristiques de l’ensemble complet en tant que système intégré.
L’essai de rigidité de la suspension primaire implique la fixation de la suspension secondaire, le montage de transformateurs différentiels variables linéaires (capteurs LVDT) aux points de réponse du boîtier de roulement d’essieu et du bogie, et l’application d’une force ou d’un déplacement programmé dans chacun des degrés de liberté (DDL) souhaités. Pour obtenir un résultat utile, les ingénieurs doivent garantir la précision et la résolution des cellules de charge et des capteurs LVDT, maintenir une température constante en laboratoire et prendre des mesures à différentes vitesses pour évaluer les caractéristiques d’amortissement. Il est important de mesurer la rigidité du bogie dans chaque direction, pas seulement verticale, car la stabilité est fonction des déplacements multiaxiaux combinés, pas seulement verticaux. Dans les virages, par exemple, le bogie se déforme (dans l’axe de lacet) et la rigidité de la chaîne est critique pour une direction stable.
Cette même configuration peut être utilisée pour effectuer un test d’amortissement de suspension primaire et évaluer l’amortissement par rapport à la rigidité du ressort. Les données des essais de la suspension primaire sont très utiles pour alimenter les modèles virtuels du bogie, tant pour la génération du modèle que pour sa validation.
Une autre série importante d’essais est celle de la suspension secondaire, qui se trouve entre le haut du bogie et le bas du wagon. Pour ces essais, la suspension primaire est fixe et la suspension secondaire (généralement une paire d’airbags) est montée sur des cellules de charge multiaxiales. Un wagon simulé est contraint en 3DOF et contrôlé dans les 3DOF restants afin de soumettre la suspension secondaire aux mêmes charges et déformations qu’en service. Cela permet d’évaluer les caractéristiques de rigidité et d’amortissement. En raison de la forme inclinée du "chapeau" du coussin gonflable, la prédiction de la rigidité latérale et du roulis est particulièrement difficile. Le matériau élastomère se déforme de manière imprévisible et ces mouvements affectent grandement le confort de conduite.
ESSAIS DE PERFORMANCES SUPPLÉMENTAIRES
Un autre type d’essai que ce système peut effectuer est la mesure du couple de résistance de direction, dans laquelle le bogie est tourné sous le wagon simulé et sa rigidité est mesurée. Pour effectuer cet essai, des charges ou des déplacements latéraux égaux et opposés sont appliqués à chaque essieu. Les forces de tension/compression et longitudinales sont mises à zéro et les actionneurs verticaux sont commandés pour maintenir la force désirée ou le mouvement plan fixe au niveau des roues.
De plus, le système d’essai peut être configuré pour contrôler le coefficient de suspension pour voie droite ou courbe. Dans cet essai, le spécimen est un wagon complet (ou simulé) avec des gyroscopes de mesure d’angle sur les tables, les bogies et la carrosserie. L’essai consiste à élever les roues d’un côté du bogie jusqu’à une surélévation souhaitée et à mesurer l’angle du bogie et de la cabine par rapport à l’angle de la table. Ces relations peuvent être difficiles à prévoir en raison des nombreux éléments de la suspension complète. Les fabricants peuvent utiliser un essai similaire pour comprendre le coefficient de renversement, ce qui est vital pour assurer le confort et la sécurité de conduite.
Des wagons complets peuvent également être évalués. Si les ingénieurs souhaitent comprendre la réponse dynamique pour les essais de coefficients, le système peut être commandé avec un bruit en forme de large bande ou des formes d’onde spécifiques, comme une onde sinusoïdale. La réponse de la carrosserie du wagon est mesurée et sa fréquence naturelle peut être estimée à partir des données résultantes à l’aide d’un logiciel d’essai.
Parmi les autres essais que le système peut effectuer, il y a la localisation du centre de gravité, un essai du moment d’inertie et la lecture en temps réel des données d’exploitation sur rail.
S’il est vrai qu’un système d’essai de performance polyvalent représente un investissement en capital important pour le laboratoire, il offre un retour sur investissement tout aussi important grâce à sa capacité à accélérer la programmation des tests, à réduire les coûts et à améliorer la précision des données d’essai et la caractérisation des spécimens. En fin de compte, ces capacités permettront aux fabricants de wagons et de bogies d’améliorer la précision des modèles, d’innover plus rapidement, de fabriquer des véhicules de meilleure qualité et de créer un avantage concurrentiel durable.
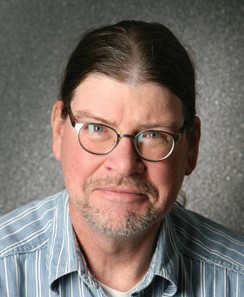