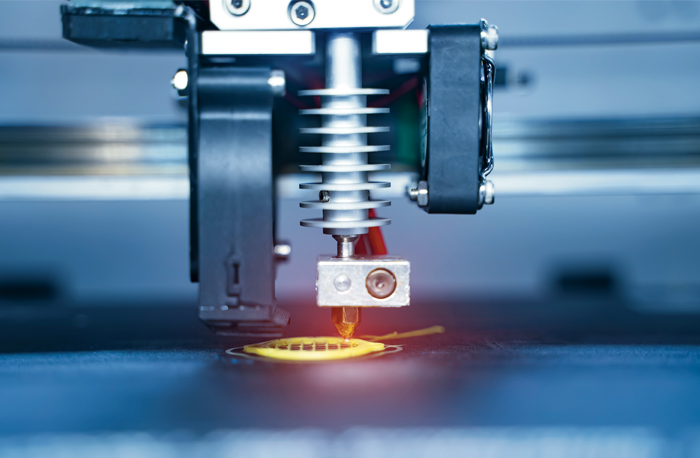
Il semblerait que toute l’industrie des essais de matériaux parle de la fabrication additive, mais qu’est-ce que cela implique pour les essais de matériaux ? Rejoignez les experts de MTS, Mike Shepard, titulaire d’un doctorat, et Mark Menzuber, titulaire d’une maîtrise en administration des affaires, pour découvrir les bases de la fabrication additive, les différences avec l’impression 3D et son impact sur l’avenir des essais de matériaux.
Qu’est-ce que la fabrication additive (FA) ? Quels sont ses avantages ?
M. Shepard : je ne saurais expliquer cette technologie par une réponse courte, mais la fabrication additive est en train de révolutionner la conception et la fabrication. Cette technologie nous permet de créer directement des pièces à partir d’un dessin solide, en utilisant toute une série de méthodes de fabrication additive, toujours plus nombreuses. Au mieux, les propriétés peuvent se comparer de manière favorable à celles des procédés de fabrication conventionnels. Les différentes techniques peuvent s’appliquer aux métaux, aux polymères, voire aux matériaux composites et aux céramiques. D’une manière générale, vous construisez la pièce directement, couche par couche. Il se peut que les pièces qui présentent des tolérances strictes ou qui supportent des charges doivent passer par des étapes d’usinage de finition ou un traitement thermique, mais dans certains cas, les pièces peuvent être utilisées dès qu’elles ressortent du système de fabrication additive.
Les avantages de cette technologie sont nombreux. Tout d’abord, vous pouvez concevoir des formes et des structures de manière incroyablement libre. Les concepteurs peuvent optimiser le poids, le transfert de chaleur, l’espace et d’autres propriétés. Ensuite, en termes d’utilisation des matériaux, elle peut être très efficace puisque vous n’avez pas à transformer un gros bloc de métal en morceaux pour créer une petite pièce compliquée. C’est pourquoi la fabrication additive est décrite comme ayant un excellent « ratio buy-to-fly ». Autrement dit, la majeure partie du matériau que vous achetez est effectivement utilisée dans le composant, au lieu d’être transformée en morceaux ou en déchets. La chaîne d’approvisionnement peut également être considérablement réduite. Au lieu d’avoir plusieurs étapes de fabrication et plusieurs fournisseurs, vous pouvez potentiellement utiliser un seul procédé de fabrication, certes complexe, mais qui se déroule en un seul endroit. Les avantages logistiques en termes de délais plus courts et de chaînes logistiques consolidées sont évidents.
Quelles tendances du secteur sont à l’origine du besoin de FA ? Quels sont les secteurs qui l’utilisent le plus ?
M. Menzuber : la plupart des entreprises qui s’intéressent à la fabrication additive sont vraiment attirées par la possibilité de réduire le poids et d’améliorer les performances de différentes manières. La possibilité de simplifier leur chaîne d’approvisionnement et de réduire les délais en utilisant la fabrication additive sur site au lieu de plusieurs étapes de production, éventuellement sur d’autres sites, présente également un grand intérêt. Enfin, la fabrication additive apporte de nouveaux gains d’efficacité pour les petites et moyennes séries de production, ce qui peut permettre d’adapter les produits de manière plus économique et raccourcir les délais de développement de produits.
Les technologies de fabrication additive, à mesure qu’elles se développent, risquent de créer des bouleversements. Tout le monde songe à utiliser la fabrication additive, mais les applications aérospatiales et biomédicales sont celles qui mobilisent le plus d’énergie et d’investissements. Ces secteurs ont des applications à très forte valeur ajoutée, avec des volumes faibles à modérés. Dans ces secteurs, les applications ont tendance à être fortement optimisées et testées de manière approfondie. Les procédés de fabrication émergents, comme la fabrication additive, peuvent donc y être intégrés, car leur proposition de valeur est évidente. Les applications automobiles sont également en plein essor, mais la sensibilité aux coûts est plus forte dans ce secteur.
Quelle est la différence entre l’impression 3D et la FA ?
M. Shepard : ces termes sont encore couramment utilisés comme synonymes, notamment dans les médias grand public et sur le marché de consommation. A mon sens, les pièces fabriquées de manière additive sont généralement utilisées dans des applications finales. Etant donné que la pièce sera utilisée dans un produit, le procédé de fabrication additive doit être robuste, adapté à un environnement de production et doit pouvoir être réalisé de manière raisonnablement efficace.
Dans une application de prototypage rapide, les pièces ne sont généralement pas utilisées de manière significative. Il se peut que la résistance ne soit pas trop élevée et que les propriétés ne soient pas uniformes. Mieux vaut être prudent en utilisant ces pièces dans une application pratique, en particulier lorsqu’une charge est impliquée. Le processus d’impression lui-même peut être assez lent. Cela étant dit, un prototype physique rapidement disponible peut vraiment aider les ingénieurs-concepteurs à comprendre comment une pièce va fonctionner et interagir avec d’autres pièces. Ces prototypes imprimés sont également extrêmement utiles pour prouver leur compatibilité et leur fonctionnement aux collaborateurs et aux clients. Pour moi, ces prototypes imprimés en 3D sont la prochaine étape en ce qui concerne les visualisations que vous pourriez créer avec un logiciel de CAO en 3D.
L’entreprise MTS utilise-t-elle la fabrication additive ?
M. Shepard : oh oui. Il se trouve que MTS a une longue expérience de la fabrication additive, depuis le milieu des années 1990. Nous étions un peu en avance sur notre temps par rapport au marché, mais en travaillant avec un certain nombre de partenaires, nous avons pu perfectionner notre procédé de fabrication additive laser au point de pouvoir produire avec succès des pièces Ti-6Al-4V de qualité aérospatiale. Certaines de ces pièces se trouvent peut-être encore sur des F-15. Cette expérience nous a permis de mieux comprendre ce qu’il faut faire pour qualifier un procédé de fabrication additive et les pièces qui en sont issues, notamment en ce qui concerne les essais mécaniques.
Plus récemment, les possibilités de conception et l’efficacité de la fabrication additive ont éveillé notre intérêt tout comme celui de nos clients pour cette technologie. Nous disposons d’un système de fabrication additive interne que nous utilisons pour le prototypage rapide et certaines pièces de production. Lorsque nous concevons des systèmes personnalisés, nous utilisons le prototypage rapide dans le cadre de notre processus de recherche et de développement. La CAO en 3D est un outil formidable et nous l’utilisons beaucoup, mais rien ne vaut le fait de pouvoir tenir les pièces dans les mains et de voir comment elles s’emboîtent et fonctionnent. Nos clients aussi apprécient. Lorsque nous concevons un nouveau système unique pour eux, il est vraiment utile de disposer d’un modèle à taille réelle ou réduite qui leur permettra de voir directement la conception mécanique du fonctionnement.
Nous utilisons également la fabrication additive pour certaines pièces de faible volume, très complexes et ne supportant pas de charge. Pour ces pièces, la FA nous permet d’obtenir des coûts compétitifs et de réduire les délais, ce qui est très intéressant d’un point de vue logistique. Auparavant, ces pièces devaient être fabriquées en plusieurs étapes, parfois en faisant appel à des fournisseurs extérieurs à notre usine. Désormais, il nous suffit de télécharger le modèle solide du composant, d’appliquer les pratiques standard relatives aux paramètres de notre procédé de FA et de revenir plus tard lorsque la pièce est terminée. Le composant fabriqué de manière additive peut parfois être intégré directement dans la construction, sans aucune étape de fabrication secondaire.
Comment la FA affecte-t-elle les essais de matériaux ?
M. Menzuber : il y a un certain nombre d’éléments importants. Tout d’abord, il peut être difficile d’obtenir des éprouvettes standard usinées à partir de composants fabriqués de manière additive, il faudra donc peut-être utiliser des éprouvettes à échelle réduite ou un type d’essai différent. Nous savons plutôt bien comment gérer ces variables. Nous disposons d’une large gamme de bâtis de charge et de dispositifs de fixation qui vous permettront d’appliquer le bon niveau de force à une éprouvette correctement configurée afin que vous puissiez évaluer les propriétés qui vous intéressent. Nous sommes également conscients du fait que différents clients seront intéressés par différents types d’essais et auront besoin de solutions à des capacités et à des prix différents.
Il faut également garder à l’esprit la nature des procédés de fabrication additive et leur influence sur l’uniformité des propriétés des matériaux dans une pièce. D’une manière générale, la principale caractéristique de la fabrication additive est qu’elle permet d’obtenir directement des pièces finies ou presque finies, couche par couche. Il ne s’agit pas de fabriquer un gros bloc de matériau relativement uniforme pour ensuite usiner une pièce à partir de ce bloc. La nature couche par couche de la fabrication additive peut donner lieu à des propriétés matérielles qui ne sont pas nécessairement isotropes, c’est-à-dire qu’elles ne sont pas uniformes selon la direction de la pièce. Les propriétés perpendiculaires aux couches additives, généralement appelées direction Z, sont notamment des plus intéressantes. Il faut prévoir des essais supplémentaires pour s’assurer de l’uniformité du matériau dans les pièces. Qui plus est, selon le degré de maturité du procédé de fabrication additive, il peut être nécessaire d’effectuer des essais pour comprendre l’impact des différents paramètres de traitement sur les propriétés mécaniques afin de déterminer la zone de traitement sûre pour la production. Ces procédés peuvent être extrêmement complexes et contenir énormément de variables.
Tester des éprouvettes témoins est particulièrement utile dans le cadre d’un procédé de fabrication additive. Vous pouvez créer une petite éprouvette avant et après une fabrication complexe pour vous assurer que le système fonctionne comme prévu dans l’ensemble. Nous disposons d’une gamme de systèmes plus petits et à des prix raisonnables qui sont parfaits pour cela. Ils sont faciles à utiliser et peuvent être placés juste à côté du système de fabrication additive si vous le souhaitez. Ces systèmes vous permettent de savoir immédiatement si le système produit ou non un bon matériau du point de vue des propriétés mécaniques. Les éprouvettes prélevées directement sur les composants peuvent donner une indication plus directe de la stabilité du processus et de la qualité des composants.
Que faut-il prendre en considération lors du choix de l’équipement d’essais pour les éprouvettes de FA ?
M. Shepard : logiquement, la communauté des testeurs essaie d’utiliser autant que possible les équipements existants et les méthodes d’essais standardisées. Malheureusement, le matériau d’un élément fabriqué de manière additive peut ne pas avoir des propriétés uniformes. Dans de nombreux cas, il est tout simplement impossible d’obtenir des éprouvettes standard à partir de ces composants fabriqués. Pour nous, c’est un défi amusant. Nos gammes complètes de technologies de bâtis de charge (servohydrauliques, électromécaniques, électrodynamiques) et de dispositifs de fixation (mors, flexion trois points, manilles,…) nous permettent de traiter sans difficulté excessive des éprouvettes à échelle réduite et inhabituelles. Nous avons également des bâtis de charge bien dimensionnés pour des essais à plus petite échelle, si cela est nécessaire.
Selon les types d’essais nécessaires, vous pouvez opter pour différents types de systèmes. En haut de gamme, pour bénéficier du plus haut niveau de performance et de flexibilité, vous aurez probablement besoin d’un système servohydraulique. Ces systèmes conviennent particulièrement bien aux essais dynamiques, comme les essais de fatigue et de rupture et peuvent facilement effectuer des essais de routine, comme les essais de traction. Certains clients peuvent avoir des exigences plus simples et avoir simplement besoin d’effectuer des essais de traction. Dans ce cas, un système électromécanique leur conviendrait mieux. Les systèmes électromécaniques peuvent être assez abordables et sont parfaits pour tester les éprouvettes témoins dans le cadre d’un processus de production.
Depuis quelques années, il existe une autre option. Les systèmes électrodynamiques offrent de nombreuses performances dynamiques et ne nécessitent pas de pompe hydraulique. Ces systèmes sont particulièrement intéressants si vous devez travailler dans un environnement particulièrement propre ou si vous débutez dans les essais et que vous avez besoin d’une certaine capacité dynamique, mais que vous préférez éviter la complexité et les dépenses d’une installation hydraulique.
Comment MTS contribue-t-elle à la communauté de la fabrication additive ?
M. Menzuber : premièrement, nous utilisons cette technologie et nous avons une longue expérience dans ce domaine. Nous avons donc une connaissance de première main des avantages et des défis associés aux méthodes de fabrication additive. Deuxièmement, nous entretenons des relations très étroites avec nos clients. Ils ont chacun leurs propres façons d’intégrer de nouveaux matériaux et processus dans leurs produits et nous travaillons en étroite collaboration avec eux pour les soutenir. Nous pouvons, par exemple, les aider à développer des données de conception, à générer des paramètres pour leurs modèles de matériaux, à tester des éprouvettes témoins, et même à tester des composants et des systèmes à l’échelle 1:1. Troisièmement, nous collaborons avec les organismes de normalisation qui élaborent des normes d’essai pour la fabrication additive, en particulier ASTM et ISO. Il est important pour MTS de participer à ces organismes afin de pouvoir soutenir la communauté technique avec notre expertise en matière d’essais et de faire valoir les besoins et les expériences de nos clients.
Qu’est-ce que la fabrication additive (FA) ? Quels sont ses avantages ?
M. Shepard : je ne saurais expliquer cette technologie par une réponse courte, mais la fabrication additive est en train de révolutionner la conception et la fabrication. Cette technologie nous permet de créer directement des pièces à partir d’un dessin solide, en utilisant toute une série de méthodes de fabrication additive, toujours plus nombreuses. Au mieux, les propriétés peuvent se comparer de manière favorable à celles des procédés de fabrication conventionnels. Les différentes techniques peuvent s’appliquer aux métaux, aux polymères, voire aux matériaux composites et aux céramiques. D’une manière générale, vous construisez la pièce directement, couche par couche. Il se peut que les pièces qui présentent des tolérances strictes ou qui supportent des charges doivent passer par des étapes d’usinage de finition ou un traitement thermique, mais dans certains cas, les pièces peuvent être utilisées dès qu’elles ressortent du système de fabrication additive.
Les avantages de cette technologie sont nombreux. Tout d’abord, vous pouvez concevoir des formes et des structures de manière incroyablement libre. Les concepteurs peuvent optimiser le poids, le transfert de chaleur, l’espace et d’autres propriétés. Ensuite, en termes d’utilisation des matériaux, elle peut être très efficace puisque vous n’avez pas à transformer un gros bloc de métal en morceaux pour créer une petite pièce compliquée. C’est pourquoi la fabrication additive est décrite comme ayant un excellent « ratio buy-to-fly ». Autrement dit, la majeure partie du matériau que vous achetez est effectivement utilisée dans le composant, au lieu d’être transformée en morceaux ou en déchets. La chaîne d’approvisionnement peut également être considérablement réduite. Au lieu d’avoir plusieurs étapes de fabrication et plusieurs fournisseurs, vous pouvez potentiellement utiliser un seul procédé de fabrication, certes complexe, mais qui se déroule en un seul endroit. Les avantages logistiques en termes de délais plus courts et de chaînes logistiques consolidées sont évidents.
Quelles tendances du secteur sont à l’origine du besoin de FA ? Quels sont les secteurs qui l’utilisent le plus ?
M. Menzuber : la plupart des entreprises qui s’intéressent à la fabrication additive sont vraiment attirées par la possibilité de réduire le poids et d’améliorer les performances de différentes manières. La possibilité de simplifier leur chaîne d’approvisionnement et de réduire les délais en utilisant la fabrication additive sur site au lieu de plusieurs étapes de production, éventuellement sur d’autres sites, présente également un grand intérêt. Enfin, la fabrication additive apporte de nouveaux gains d’efficacité pour les petites et moyennes séries de production, ce qui peut permettre d’adapter les produits de manière plus économique et raccourcir les délais de développement de produits.
Les technologies de fabrication additive, à mesure qu’elles se développent, risquent de créer des bouleversements. Tout le monde songe à utiliser la fabrication additive, mais les applications aérospatiales et biomédicales sont celles qui mobilisent le plus d’énergie et d’investissements. Ces secteurs ont des applications à très forte valeur ajoutée, avec des volumes faibles à modérés. Dans ces secteurs, les applications ont tendance à être fortement optimisées et testées de manière approfondie. Les procédés de fabrication émergents, comme la fabrication additive, peuvent donc y être intégrés, car leur proposition de valeur est évidente. Les applications automobiles sont également en plein essor, mais la sensibilité aux coûts est plus forte dans ce secteur.
Quelle est la différence entre l’impression 3D et la FA ?
M. Shepard : ces termes sont encore couramment utilisés comme synonymes, notamment dans les médias grand public et sur le marché de consommation. A mon sens, les pièces fabriquées de manière additive sont généralement utilisées dans des applications finales. Etant donné que la pièce sera utilisée dans un produit, le procédé de fabrication additive doit être robuste, adapté à un environnement de production et doit pouvoir être réalisé de manière raisonnablement efficace.
Dans une application de prototypage rapide, les pièces ne sont généralement pas utilisées de manière significative. Il se peut que la résistance ne soit pas trop élevée et que les propriétés ne soient pas uniformes. Mieux vaut être prudent en utilisant ces pièces dans une application pratique, en particulier lorsqu’une charge est impliquée. Le processus d’impression lui-même peut être assez lent. Cela étant dit, un prototype physique rapidement disponible peut vraiment aider les ingénieurs-concepteurs à comprendre comment une pièce va fonctionner et interagir avec d’autres pièces. Ces prototypes imprimés sont également extrêmement utiles pour prouver leur compatibilité et leur fonctionnement aux collaborateurs et aux clients. Pour moi, ces prototypes imprimés en 3D sont la prochaine étape en ce qui concerne les visualisations que vous pourriez créer avec un logiciel de CAO en 3D.
L’entreprise MTS utilise-t-elle la fabrication additive ?
M. Shepard : oh oui. Il se trouve que MTS a une longue expérience de la fabrication additive, depuis le milieu des années 1990. Nous étions un peu en avance sur notre temps par rapport au marché, mais en travaillant avec un certain nombre de partenaires, nous avons pu perfectionner notre procédé de fabrication additive laser au point de pouvoir produire avec succès des pièces Ti-6Al-4V de qualité aérospatiale. Certaines de ces pièces se trouvent peut-être encore sur des F-15. Cette expérience nous a permis de mieux comprendre ce qu’il faut faire pour qualifier un procédé de fabrication additive et les pièces qui en sont issues, notamment en ce qui concerne les essais mécaniques.
Plus récemment, les possibilités de conception et l’efficacité de la fabrication additive ont éveillé notre intérêt tout comme celui de nos clients pour cette technologie. Nous disposons d’un système de fabrication additive interne que nous utilisons pour le prototypage rapide et certaines pièces de production. Lorsque nous concevons des systèmes personnalisés, nous utilisons le prototypage rapide dans le cadre de notre processus de recherche et de développement. La CAO en 3D est un outil formidable et nous l’utilisons beaucoup, mais rien ne vaut le fait de pouvoir tenir les pièces dans les mains et de voir comment elles s’emboîtent et fonctionnent. Nos clients aussi apprécient. Lorsque nous concevons un nouveau système unique pour eux, il est vraiment utile de disposer d’un modèle à taille réelle ou réduite qui leur permettra de voir directement la conception mécanique du fonctionnement.
Nous utilisons également la fabrication additive pour certaines pièces de faible volume, très complexes et ne supportant pas de charge. Pour ces pièces, la FA nous permet d’obtenir des coûts compétitifs et de réduire les délais, ce qui est très intéressant d’un point de vue logistique. Auparavant, ces pièces devaient être fabriquées en plusieurs étapes, parfois en faisant appel à des fournisseurs extérieurs à notre usine. Désormais, il nous suffit de télécharger le modèle solide du composant, d’appliquer les pratiques standard relatives aux paramètres de notre procédé de FA et de revenir plus tard lorsque la pièce est terminée. Le composant fabriqué de manière additive peut parfois être intégré directement dans la construction, sans aucune étape de fabrication secondaire.
Comment la FA affecte-t-elle les essais de matériaux ?
M. Menzuber : il y a un certain nombre d’éléments importants. Tout d’abord, il peut être difficile d’obtenir des éprouvettes standard usinées à partir de composants fabriqués de manière additive, il faudra donc peut-être utiliser des éprouvettes à échelle réduite ou un type d’essai différent. Nous savons plutôt bien comment gérer ces variables. Nous disposons d’une large gamme de bâtis de charge et de dispositifs de fixation qui vous permettront d’appliquer le bon niveau de force à une éprouvette correctement configurée afin que vous puissiez évaluer les propriétés qui vous intéressent. Nous sommes également conscients du fait que différents clients seront intéressés par différents types d’essais et auront besoin de solutions à des capacités et à des prix différents.
Il faut également garder à l’esprit la nature des procédés de fabrication additive et leur influence sur l’uniformité des propriétés des matériaux dans une pièce. D’une manière générale, la principale caractéristique de la fabrication additive est qu’elle permet d’obtenir directement des pièces finies ou presque finies, couche par couche. Il ne s’agit pas de fabriquer un gros bloc de matériau relativement uniforme pour ensuite usiner une pièce à partir de ce bloc. La nature couche par couche de la fabrication additive peut donner lieu à des propriétés matérielles qui ne sont pas nécessairement isotropes, c’est-à-dire qu’elles ne sont pas uniformes selon la direction de la pièce. Les propriétés perpendiculaires aux couches additives, généralement appelées direction Z, sont notamment des plus intéressantes. Il faut prévoir des essais supplémentaires pour s’assurer de l’uniformité du matériau dans les pièces. Qui plus est, selon le degré de maturité du procédé de fabrication additive, il peut être nécessaire d’effectuer des essais pour comprendre l’impact des différents paramètres de traitement sur les propriétés mécaniques afin de déterminer la zone de traitement sûre pour la production. Ces procédés peuvent être extrêmement complexes et contenir énormément de variables.
Tester des éprouvettes témoins est particulièrement utile dans le cadre d’un procédé de fabrication additive. Vous pouvez créer une petite éprouvette avant et après une fabrication complexe pour vous assurer que le système fonctionne comme prévu dans l’ensemble. Nous disposons d’une gamme de systèmes plus petits et à des prix raisonnables qui sont parfaits pour cela. Ils sont faciles à utiliser et peuvent être placés juste à côté du système de fabrication additive si vous le souhaitez. Ces systèmes vous permettent de savoir immédiatement si le système produit ou non un bon matériau du point de vue des propriétés mécaniques. Les éprouvettes prélevées directement sur les composants peuvent donner une indication plus directe de la stabilité du processus et de la qualité des composants.
Que faut-il prendre en considération lors du choix de l’équipement d’essais pour les éprouvettes de FA ?
M. Shepard : logiquement, la communauté des testeurs essaie d’utiliser autant que possible les équipements existants et les méthodes d’essais standardisées. Malheureusement, le matériau d’un élément fabriqué de manière additive peut ne pas avoir des propriétés uniformes. Dans de nombreux cas, il est tout simplement impossible d’obtenir des éprouvettes standard à partir de ces composants fabriqués. Pour nous, c’est un défi amusant. Nos gammes complètes de technologies de bâtis de charge (servohydrauliques, électromécaniques, électrodynamiques) et de dispositifs de fixation (mors, flexion trois points, manilles,…) nous permettent de traiter sans difficulté excessive des éprouvettes à échelle réduite et inhabituelles. Nous avons également des bâtis de charge bien dimensionnés pour des essais à plus petite échelle, si cela est nécessaire.
Selon les types d’essais nécessaires, vous pouvez opter pour différents types de systèmes. En haut de gamme, pour bénéficier du plus haut niveau de performance et de flexibilité, vous aurez probablement besoin d’un système servohydraulique. Ces systèmes conviennent particulièrement bien aux essais dynamiques, comme les essais de fatigue et de rupture et peuvent facilement effectuer des essais de routine, comme les essais de traction. Certains clients peuvent avoir des exigences plus simples et avoir simplement besoin d’effectuer des essais de traction. Dans ce cas, un système électromécanique leur conviendrait mieux. Les systèmes électromécaniques peuvent être assez abordables et sont parfaits pour tester les éprouvettes témoins dans le cadre d’un processus de production.
Depuis quelques années, il existe une autre option. Les systèmes électrodynamiques offrent de nombreuses performances dynamiques et ne nécessitent pas de pompe hydraulique. Ces systèmes sont particulièrement intéressants si vous devez travailler dans un environnement particulièrement propre ou si vous débutez dans les essais et que vous avez besoin d’une certaine capacité dynamique, mais que vous préférez éviter la complexité et les dépenses d’une installation hydraulique.
Comment MTS contribue-t-elle à la communauté de la fabrication additive ?
M. Menzuber : premièrement, nous utilisons cette technologie et nous avons une longue expérience dans ce domaine. Nous avons donc une connaissance de première main des avantages et des défis associés aux méthodes de fabrication additive. Deuxièmement, nous entretenons des relations très étroites avec nos clients. Ils ont chacun leurs propres façons d’intégrer de nouveaux matériaux et processus dans leurs produits et nous travaillons en étroite collaboration avec eux pour les soutenir. Nous pouvons, par exemple, les aider à développer des données de conception, à générer des paramètres pour leurs modèles de matériaux, à tester des éprouvettes témoins, et même à tester des composants et des systèmes à l’échelle 1:1. Troisièmement, nous collaborons avec les organismes de normalisation qui élaborent des normes d’essai pour la fabrication additive, en particulier ASTM et ISO. Il est important pour MTS de participer à ces organismes afin de pouvoir soutenir la communauté technique avec notre expertise en matière d’essais et de faire valoir les besoins et les expériences de nos clients.