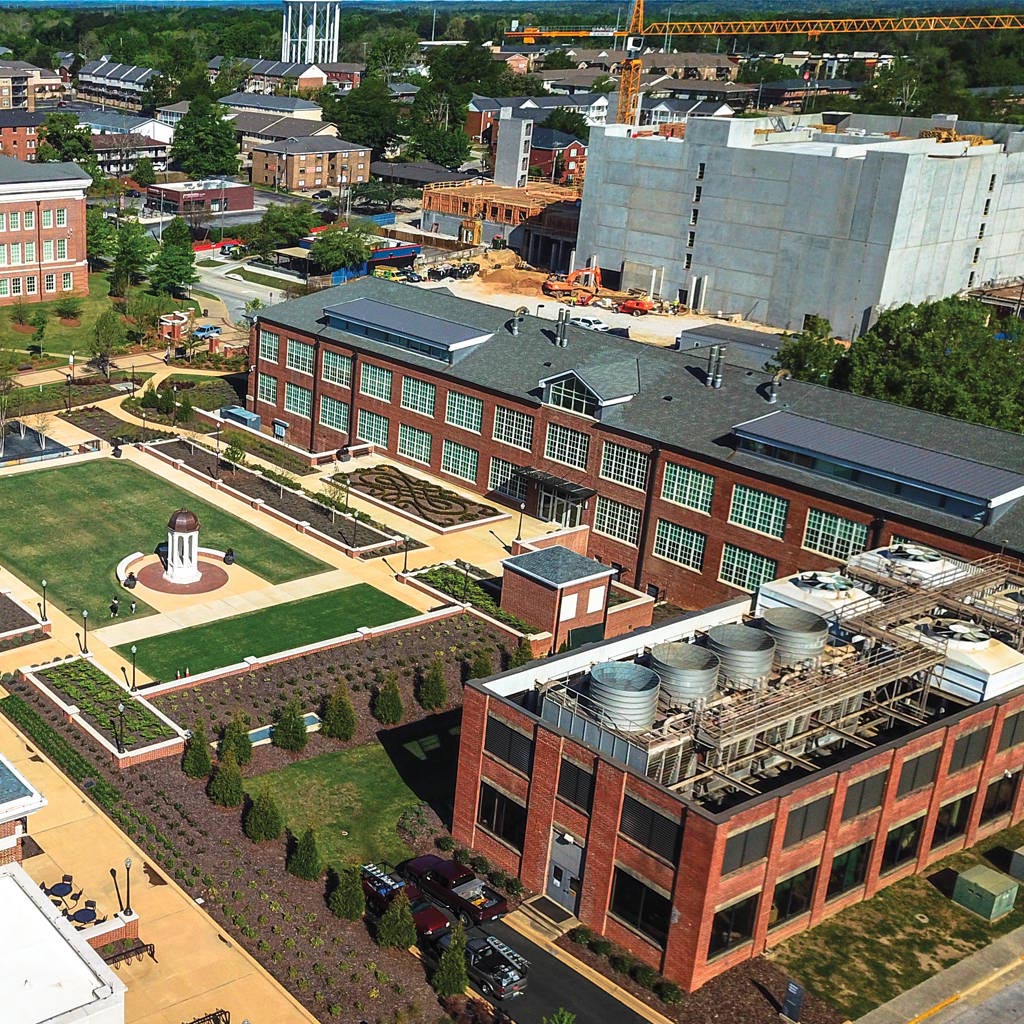
La fatigue est toujours à l’origine de la majorité des défaillances mécaniques dans de nombreuses applications structurelles et une défaillance par fatigue typique comporte au moins 3 étapes : l’amorçage des fissures, la propagation des fissures et la rupture finale. Il est bien établi que les défauts de surface (par exemple, la rugosité de surface), les défauts volumétriques (par exemple, les pores, l’absence de fusion) et la microstructure sont des facteurs influents sur la performance en fatigue des matériaux métalliques. Il convient également de noter que les fissures se forment souvent sur la surface ou à proximité de celle-ci pour plusieurs raisons, notamment une déformation inélastique plus facile, des contraintes/déformations plus élevées dues à des charges externes et des effets de concentration des contraintes.
L’intérêt croissant pour les procédés de fabrication par couches, également appelés fabrication additive (FA), a incité de nombreuses industries à envisager d’adopter ces technologies. Bien que les procédés de FA semblent simples (fabrication couche par couche), il existe de nombreuses complexités physiques et métallurgiques associées à la fusion répétée/solidification rapide lors de la fabrication. L’histoire thermique complexe (c’est-à-dire, le gradient thermique, les vitesses de refroidissement,…) subie par la pièce pendant la fabrication influence la microstructure, la texture cristallographique, les contraintes résiduelles, la rugosité de surface et la formation de défauts volumétriques (par exemple, les pores piégés par des gaz et l’absence de fusions), qui affectent par conséquent les propriétés mécaniques, notamment en cas de chargement cyclique [1, 2]. A cet égard, plusieurs études ont étudié l’effet des défauts volumétriques, de la rugosité de surface et de la microstructure sur le comportement en fatigue des matériaux métalliques fabriqués de manière additive (FA) [3].
La plupart des études ont révélé une résistance à la fatigue inférieure pour les matériaux métalliques obtenus par FA, même dans leur état de surface usiné, par rapport aux matériaux forgés, en raison des effets néfastes des défauts volumétriques inhérents aux procédés de FA [4]. De nombreux efforts ont donc été déployés pour réduire la taille et le nombre de ces défauts en ajustant les paramètres du procédé. Cependant, même en utilisant les paramètres du procédé de fabrication les plus optimisés, les pièces obtenues par FA présenteront toujours certains défauts induits par le procédé, tels que des pores piégés par des gaz, ce qui peut aggraver leurs performances en fatigue. Les processus de surface et thermiques après fabrication sont souvent essentiels pour améliorer les performances en fatigue des matériaux obtenues par FA. Par exemple, la figure 1 montre que supprimer la rugosité de surface par usinage peut améliorer considérablement les performances en fatigue de l’acier inoxydable 17-4 PH fusionné sur lit de poudre par faisceau laser (LB-PBF) [1]. Des effets similaires de rugosité de surface sur le comportement en fatigue ont également été observés pour d’autres systèmes de matériaux [5].
Figure 1
Comparaison de la fatigue en état de contrainte de l’acier inoxydable 17-4 PH LB-PBF ayant subi un traitement thermique CA-H900 avec des conditions de surface à l’état brut et usiné [1].
Les processus thermiques après fabrication (par exemple, le pressage isostatique à chaud [HIP] ou le traitement thermique) peuvent influencer les performances en fatigue des matériaux métalliques obtenus par FA en raison des modifications dans la microstructure (par exemple, la taille et la répartition des pores, la taille et la morphologie des grains, le comportement de précipitation,…) [2,4]. Par exemple, les processus de traitement thermique après fabrication, y compris le processus de traitement thermique de mise en solution (connu sous le nom de condition A [CA] pour l’acier inoxydable 17-4 PH) améliorent la résistance en fatigue de l’acier inoxydable 17-4 PH LB-PBF (figure 2). Ce résultat est dû à la microstructure plus homogénéisée et plus fine obtenue après l’étape CA par rapport à la microstructure produite après les procédures de traitement thermique sans cette étape [1].
Figure 2
Données sur la fatigue en état de contrainte de l’acier inoxydable 17-4 PH LB-PBF, dans l’état de surface tel qu’il a été construit, soumis à diverses procédures de traitement thermique [1]. Notez que les marqueurs sans remplissage correspondent aux procédures de traitement thermique sans étape CA, tandis que les marqueurs remplis représentent les conditions de traitement thermique incluant l’étape CA.
Il est intéressant de noter que les matériaux métalliques fabriqués de manière additive présentent pour la plupart un comportement de propagation des fissures de fatigue (FCG) similaire à celui des matériaux forgés dans la loi de Paris (c’est-à-dire, la zone de propagation stable des fissures). La figure 3 illustre le fait que l’acier inoxydable 17-4 PH LB-PBF présente un comportement FCG identique à celui du matériau forgé [6]. Cependant, l’acier inoxydable 17-4 PH LB-PBF montre une vitesse de FCG plus élevée (c’est-à-dire, une résistance FCG plus faible) dans la zone FCG instable (c’est-à-dire, une zone ÄK élevée) par rapport au matériau forgé. Cela peut être dû aux différences dans la microstructure, ainsi qu’à la présence de défauts volumétriques dans l’acier inoxydable 17-4 PH LB-PBF, entraînant une résistance à la rupture cyclique inférieure à celle du matériau forgé. De tels défauts peuvent également augmenter la vitesse de FCG de l’acier inoxydable 17-4 PH LB-PBF dans la zone proche du seuil.
Figure 3
Comportement de propagation des fissures de fatigue (FCG) de l’acier inoxydable 17-4 PH LB-PBF ayant subi un traitement thermique CA-H900 par rapport à celui des matériaux forgés dans les mêmes conditions de traitement thermique [6].
Références
1. Nezhadfar PD, Shrestha R, Phan N, Shamsaei N. Int J Fatigue. 2019;124:188-204.
2. Pegues J.W., Shao S., Shamsaei N., Sanaei N., Fatemi A., Warner D.H., Li P., Phan N., Int J Fatigue, 2020: 132, p.105358.
3. Fatemi A, Molaei R, Simsiriwong J, Sanaei N, Pegues J, Torries B, Phan N, Shamsaei N., Fatigue & Fracture of Eng. Mater. & Struc. 2019: 991-1009.
4. Molaei R., Fatemi A., Sanaei N., Pegues J., Shamsaei N., Shao S., Li P., Warner D.H., Phan N., Int J Fatigue, 2020: 132, p.105363.
5. Pegues J., Roach M., Williamson R. S., Shamsaei N. Int J Fatigue, 116, 2018: 543-552.
6. Nezhadfar PD, Burford E, Anderson-wedge K, Zhang B, Daniewicz SR, Shamsaei N., Int J Fatigue. 2019.
Le National Center for Additive Manufacturing Excellence (NCAME) de l’université d’Auburn a été créé en 2017 grâce à une collaboration avec le Centre de vol spatial Marshall de la NASA.