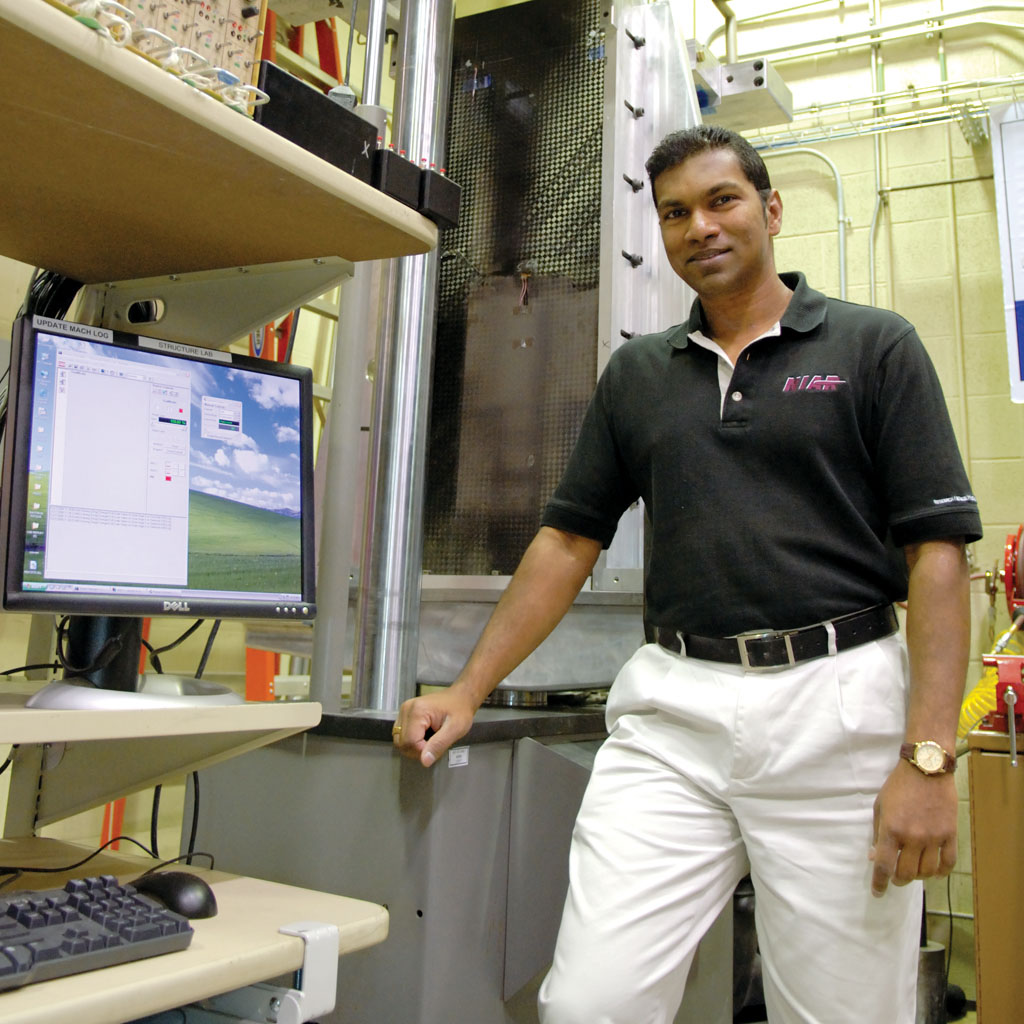
DÉFI DU CLIENT
Depuis 1985, le National Institute for Aviation Research (NIAR) de la Wichita State University répond aux besoins de l’industrie en matière de recherche, de conception, d’essais et de certification en fournissant des solutions compétitives et innovantes qui répondent à des normes technologiques élevées. Situé à Wichita, au Kansas, le NIAR rassemble les universités, les gouvernements et l’industrie afin de faire progresser les technologies pour l’aviation et les industries connexes. Les locaux de 120 000 pieds carrés du NIAR abritent 15 laboratoires, qui mènent des recherches, entre autres, sur l’assemblage avancé, l’aérodynamique, le vieillissement des aéronefs, la dynamique des accidents, les matériaux composites et avancés, les composants structurels, la réalité virtuelle et la mécanique informatique.
Le laboratoire de structures du NIAR offre des capacités de recherche et d’essai pour des éléments à l’essai pouvant aller d’échantillons de matériaux à de grandes structures d’aéronefs. Les recherches menées par le laboratoire de structures permettent aux organisations commerciales, d’aviation générale et militaires de mieux comprendre comment réduire les coûts de fabrication tout en augmentant l’efficacité opérationnelle. Les projets de recherche liés à la tolérance aux dommages, aux effets des défauts et aux essais d’éléments pour la conception et la certification des aéronefs et des véhicules aériens sans pilote permettent au laboratoire de structures du NIAR de figurer parmi les installations les plus sollicitées et les plus recherchées de sa catégorie.
Le laboratoire répond aux besoins d’essais du Center of Excellence for Composites and Advanced Materials (CECAM) de la Federal Aviation Administration (FAA) et du NASA National Center for Advanced Materials Performance (NCAMP), qui ont tous deux leur siège social au NIAR. Grâce à ces organisations, le NIAR conçoit des méthodes rentables de qualification des matériaux composites en partageant des bases de données centrales de qualification des matériaux. Par la suite, ces bases de données partagées aideront un fabricant à sélectionner un système de matériaux composites approuvé pour fabriquer des pièces et à effectuer un plus petit sous-ensemble d’essais (par rapport aux essais de matériaux déjà effectués par le NCAMP) pour une application spécifique.
« Pour que les matériaux soient acceptés dans nos bases de données partagées, les matières premières doivent être fabriquées conformément aux spécifications des matériaux, qui imposent un contrôle strict des principales propriétés physiques, chimiques et mécaniques », a indiqué Waruna Seneviratne, responsable du laboratoire de structures. « Nous sommes capables de mener cette recherche et d’atteindre nos objectifs d’essais, en grande partie grâce à l’utilisation d’équipements d’essais de matériaux avancés de MTS Systems. »
SOLUTIONS MTS
Le laboratoire de structures est équipé d’une grande variété de dispositifs d’essais et d’extensomètres MTS standard et personnalisés, notamment un extensomètre laser et des extensomètres de type KGR pour les tests d’adhérence. Le laboratoire utilise également des chambres climatiques MTS, qui lui permettent d’effectuer des essais de fatigue statique et spectrale à des températures allant de -200 °F à 2 500 °F, ainsi que dans des environnements à humidité contrôlée et à brouillard salin. Les solutions d’essais de MTS sont équipées du logiciel FlexTest avancé, d’une technologie de contrôle de pointe et de capacités d’acquisition de données multicanaux, ce qui offre au laboratoire la flexibilité dont elle a besoin pour effectuer pratiquement toutes les recherches nécessaires sur les essais de matériaux.
AVANTAGE POUR LE CLIENT
En coordination avec la FAA et le NCAMP, le laboratoire a mené à bien plusieurs programmes de recherche et d’essais importants au cours de l’année écoulée en utilisant ses solutions MTS sophistiquées. Une grande partie de la recherche était destinée à accélérer le développement de structures avancées d’aéronefs, telles que le Boeing 787 et l’Airbus A380, et contribuera au développement d’aéronefs au cours de la prochaine décennie, alors que de nouvelles technologies émergentes sont appliquées à la conception et mises en production dans toute l’industrie aéronautique.
Avec les équipements de MTS, le laboratoire effectue des essais de caractérisation de l’adhérence et des essais d’éléments sur les joints collés fatigués et endommagés. Le laboratoire identifie les réponses caractéristiques des structures collées aux défauts de fabrication et de réparation observés en situation réelle. Les recherches portent notamment sur les effets des défauts de fabrication, de la foudre et des impacts à faible vitesse sur la résistance résiduelle des joints collés. Ces travaux permettront d’établir des lignes directrices pour les contrôles de l’adhérence et de processus pour les structures collées.
L’équipe étudie également la complexité associée à l’utilisation de matériaux composites avancés non conventionnels dans les structures d’aéronefs au moyen d’une analyse par éléments finis et d’essais de sous-composants. Le laboratoire s’est servi de ses résultats pour mettre au point une méthodologie simplifiée de calcul des propriétés mécaniques des matériaux composites tressés non orthogonaux pour les structures coniques en utilisant une base de données de matériaux existante.
« Nous connaissons très bien les équipements de MTS, car le NIAR utilise beaucoup la technologie de l’entreprise dans ses nombreux laboratoires pour mener des recherches avancées », a précisé Waruna Seneviratne. « Il n’y a encore rien que les logiciels et les équipements de MTS ne puissent pas faire. »