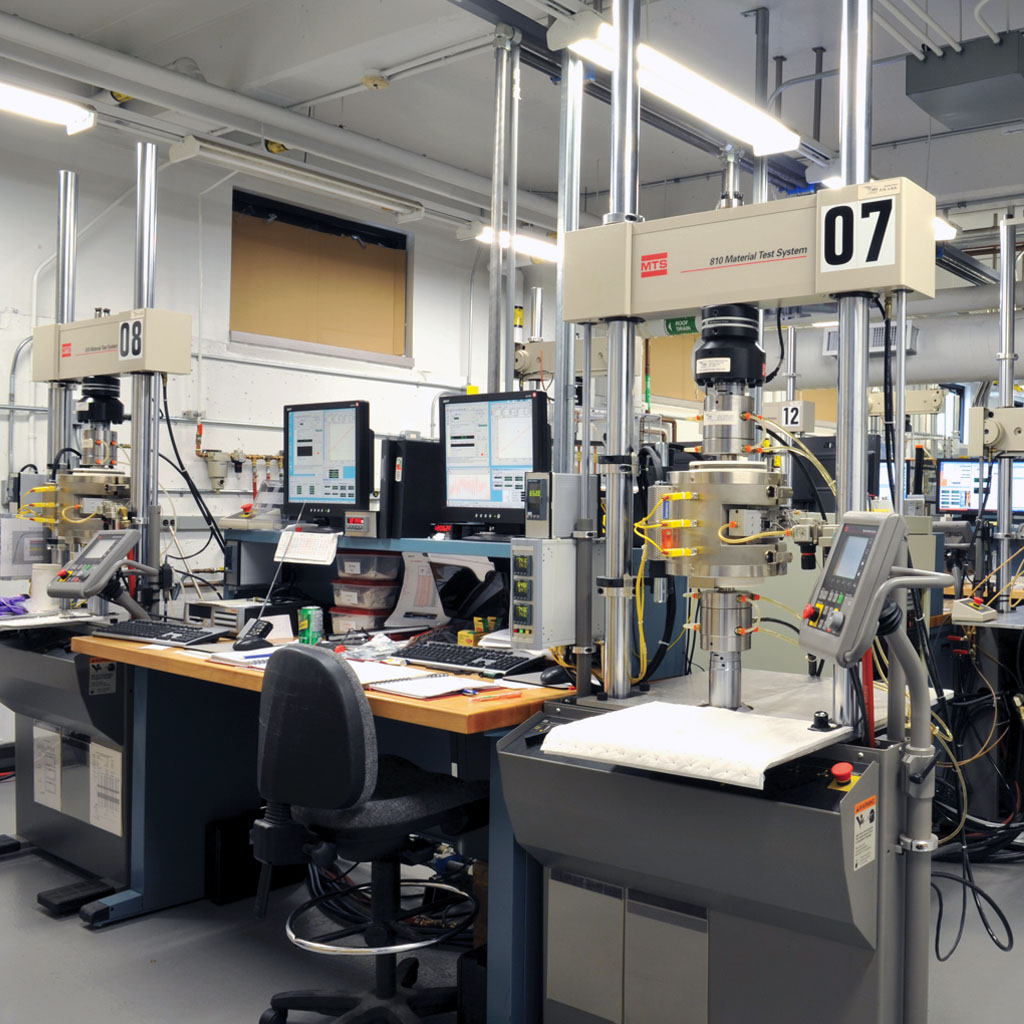
DÉFI DU CLIENT
La conception de matériaux à haute température (c’est-à-dire les matériaux qui peuvent fonctionner à des températures extrêmes pendant de longues périodes) ouvre la voie à la prochaine génération de moteurs à réaction et de turbines à gaz qui redéfiniront les attentes en matière d’efficacité énergétique. Certaines des recherches les plus avancées dans ce domaine sont menées au laboratoire de la performance des structures et matériaux, qui fait partie de l’Institut de recherche aérospatiale du Conseil national de recherches du Canada, situé à Ottawa, en Ontario.
Dans ce laboratoire, le groupe des technologies des matériaux et des composants, une équipe de 15 chercheurs, est spécialisé dans la conception, le développement et l’essai de nouveaux matériaux pour turbines à gaz, notamment des alliages haute température et des matériaux composites à matrice céramique. Le groupe mène des recherches en interne et collabore également avec des constructeurs de moteurs commerciaux, tels que Pratt & Whitney, Rolls-Royce et General Electric, ainsi qu’avec des fournisseurs de matériaux, tels que ATI Allvac et Carpenter Technologies. Pour déterminer exactement les caractéristiques des nouveaux matériaux, et leur durée de vie, lorsqu’ils sont exposés à des températures de plus en plus élevées, les chercheurs doivent procéder à un large éventail d’essais mécaniques de précision.
« Nous effectuons des essais de traction, de fluage et de résistance à la rupture, ainsi que des essais plus spécialisés, tels que la fatigue de contact, la fatigue thermomécanique, la vitesse de propagation des fissures de fatigue et la vitesse de propagation des fissures de fluage », a indiqué le Dr Kearsey, responsable de l’installation de fatigue à haute température et de mécanique des ruptures du groupe. « Nous développons les matériaux, nous les testons, puis nous élaborons des méthodes d’essai standard pour caractériser ces matériaux, ce qui inclut la définition de la géométrie de l’éprouvette, ainsi que la reproduction de l’environnement d’utilisation du moteur en laboratoire. »
A l’heure actuelle, le plus grand défi du Dr Kearsey est simple : la chaleur. Au cours des dernières décennies, les températures utilisées pour tester les alliages d’acier inoxydable, de titane et d’aluminium étaient relativement modérées. Pour tester les matériaux les plus avancés d’aujourd’hui, les températures doivent être jusqu’à 25 % plus élevées.
« Les températures sont tellement élevées que tester les matériaux devient un problème plus complexe », a-t-il déclaré. « Comment mesurer des matériaux à 1 000 °C alors que la pratique standard se base sur des équipements prévus pour 800 °C ? Comment ajouter une instrumentation appropriée pour mesurer la vitesse de propagation des fissures ? Ce n’est pas impossible, mais c’est très compliqué. Nous devons absolument nous assurer que les températures et les charges sont traçables à 100 %, car nos résultats sont utilisés pour fabriquer des composants de moteur essentiels. »
SOLUTIONS MTS
Le groupe des technologies des matériaux et des composants utilise 18 solutions MTS différentes pour les essais à haute température, qui incluent aussi bien des anciens bâtis de charge MTS 810 que des systèmes d’essais servohydrauliques MTS Landmark® de pointe.
« Si nous n’utilisons que des bâtis de charge MTS, c’est pour des raisons de stabilité », a expliqué le Dr Kearsey. « Lorsque nous avons quatre ou cinq bâtis côte à côte, le laboratoire tremble. Les bâtis MTS sont tellement stables qu’il n’y a pas de rotation ou de torsion qui pourrait désaligner l’éprouvette. »
L’équipement d’essais de l’installation comprend également deux groupes hydrauliques MTS, des commandes numériques FlexTest® et le logiciel Multipurpose TestWare®. Par ailleurs, le laboratoire utilise une gamme complète d’accessoires d’essais MTS, notamment des mors et des dispositifs de fixation, des extensomètres et des jauges de déformation, des fours et des appareils de chauffage par induction, qui doivent tous être faciles à combiner et à intégrer dans les configurations souvent complexes requises pour des essais spécifiques à haute température.
« Le matériel doit fonctionner correctement à différentes températures et conditions d’essai », a précisé le Dr Kearsey. « Ce qui nous plaît, c’est que pouvons prendre un four MTS et le greffer sur n’importe quel bâti de charge. L’interchangeabilité est importante, notamment pour la reproductibilité. Lorsque nous devons faire 100 essais sur une géométrie similaire, nous ne voulons pas perdre de temps à refaire l’étalonnage à chaque fois. »
AVANTAGES CLIENTS
Pour le Dr Kearsey, rien n’est plus important que la fiabilité du matériel et des logiciels d’essais. La fiabilité est essentielle pour l’exactitude des résultats, la productivité du laboratoire et la satisfaction des clients externes.
« Nous achetons des équipements MTS, car ils ne tombent presque jamais en panne », a-t-il ajouté. « Il n’y a pas besoin de les remplacer. Ils sont fiables et peuvent être tracés. En tant que laboratoire de recherche, la traçabilité est une exigence essentielle. Si nous effectuons un alignement sur un système, nous devons être sûrs que l’essai suivant se déroulera exactement de la même manière. Peu importe que nous testions un alliage monocristallin avancé ou que nous évaluions des alliages vieux de 50 ans pour établir des modèles de prédiction de la durée de vie. Avec les systèmes d’essais MTS, nous pouvons obtenir les données nécessaires pour prendre des décisions en toute confiance. »
La fiabilité des extensomètres est particulièrement importante dans les essais de matériaux à haute température, notamment à des fréquences pouvant atteindre 10 Hz ou avec des matériaux plus rigides où les réflexions mesurées sont plus petites. Le Dr Kearsey cite également la fiabilité du logiciel comme un facteur important.
« Lorsque vous effectuez des essais de fatigue thermomécanique, par exemple, ils peuvent durer trois mois », a-t-il souligné. « Cela coûte très cher à nos clients. Il ne faut jamais leur dire que le logiciel a planté pendant l’essai et que leurs résultats ne sont pas valables. Le logiciel MTS est essentiel à cet égard, car il nous évite ce casse-tête. Il est très fiable et de nombreux modules sont préprogrammés pour les essais de fatigue oligocyclique, les essais de fatigue thermomécanique et d’autres types d’essais. »
Aujourd’hui encore, alors que le Dr Kearsey s’efforce de relever les défis associés aux essais à 1 000 °C, il s’attend à ce que la limite supérieure augmente. En fait, il travaille avec MTS pour concevoir des systèmes d’essais capables de fonctionner à ces températures beaucoup plus élevées.
« Au fur et à mesure que les alliages les plus récents seront remplacés par des matériaux composites à matrice céramique, nous devrons effectuer des essais jusqu’à 1 300 °C ou 1 400 °C », a-t-il affirmé. « Nous sommes déjà en train de discuter avec MTS de la manière dont nous pourrons y parvenir. De quelle taille de four aurons-nous besoin ? Quelle sera la zone chaude ? De quelle extensométrie aurons-nous besoin ? MTS semble toujours intervenir au bon moment. C’est grâce à ce type d’assistance que nous continuons à faire appel à MTS. »