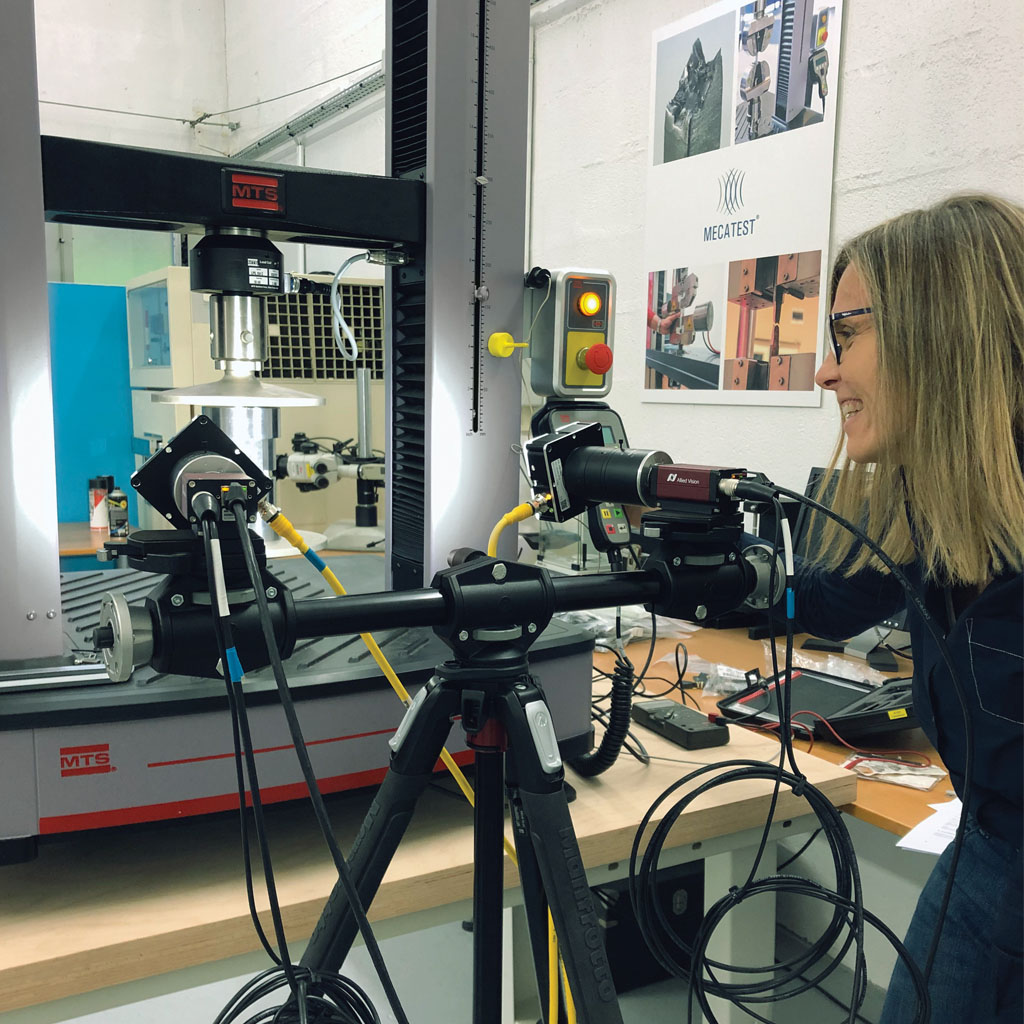
Mecatest, un fournisseur de services d’essais mécaniques, peut fournir à ses clients un large éventail de données sur la caractérisation des matériaux. Les essais, qui portent le plus souvent sur des polymères et des matériaux composites, sont généralement effectués en compression, en flexion ou en tension. Mais quel que soit le matériau ou le type d’essai, l’élément commun à la plupart de ces essais est l’utilisation de la corrélation d’images numériques (communément appelée DIC). En synchronisant ses données de déformation DIC avec les données de force et de déplacement de son système d’essais universel (UTM), Mecatest peut facilement produire des corrélations précises entre les données des essais physiques et la simulation modélisée de ses clients.
L’intégration des communications entre le système d’essais et les caméras DIC a été réalisée via des signaux TTL (interface matérielle standard). Cette communication en boucle fermée a été créée pour que le logiciel système de l’UTM puisse déclencher, capturer et stocker les images appropriées. Ainsi, toutes les données nécessaires (temps, force, déplacement, sortie numérique) sont conservées par l’UTM. Les données du système d’essais correspondant aux images (temps, force, déplacement) peuvent également être filtrées et envoyées au logiciel DIC pour analyse.
Le logiciel DIC collecte des images 3D de la structure mécanique pour mesurer les déplacements et les déformations directement sur le maillage d’éléments finis qui a été transféré à partir de la simulation numérique. Ainsi, une continuité de formatage simple mais essentielle est assurée entre la simulation et l’essai. Une telle méthodologie permet d’effectuer automatiquement des comparaisons entre les champs mesurés et simulés et facilite ainsi la validation rapide de la simulation numérique. Une fois le processus terminé, les données peuvent être exportées et utilisées par l’ingénieur IAO pour améliorer le modèle précédent.
Le logiciel DIC peut également être utilisé pour automatiser l’identification des sources d’erreur et les corrections de modèle. En appliquant ce principe, les simulations peuvent être exécutées avec des conditions limites mesurées afin de fournir un résultat simulé plus réaliste. Enfin, le logiciel DIC peut également modifier la simulation en fonction de l’ensemble de données physique (déplacements, déformations, forces). En général, cette méthode permet d’accroître la prévisibilité du modèle pour obtenir de meilleures simulations et réduit souvent le besoin d’effectuer des essais supplémentaires.
Etant donné que la DIC peut fournir des mesures plein champ, plusieurs scénarios de contrainte peuvent être évalués simultanément. La forme unique d’une éprouvette, comme celle-ci avec des trous, permet de caractériser les concentrations de contraintes liées à l’application du matériau d’une manière qui ne serait pas possible avec les techniques de mesure de la déformation conventionnelles. Grâce à la DIC, les mesures du niveau de déformation peuvent être prédites avec précision en améliorant le modèle d’éléments finis. Ces données peuvent ensuite être utilisées pour comprendre d’autres formes géométriques complexes. En outre, les mesures hors plan disponibles avec la DIC 3D permettent de réaliser des évaluations plus localisées.